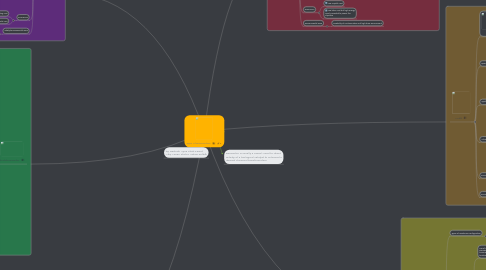
1. Packed Bed
1.1. Operation Principle
1.1.1. Packed bed bioreactor is a continuous reactor. The immobilized biocatalyst is packed in the column and the nutrient is fed to the column either from top or from bottom.
1.2. Application
1.2.1. Wastewater treatment
1.2.2. Mammalian cell culture
1.2.3. Ideal High Cell Density Replacement
1.3. Advantages/Disadvantages
1.3.1. Avantages
1.3.1.1. High conversion per unit mass of catalyst
1.3.1.2. Catalyst stay in the reactor
1.3.1.3. Effective at high temperatures and pressures
1.3.2. Disadvantages
1.3.2.1. Poor temperature control
1.3.2.2. Hard to clean
1.3.2.3. Difficult to replace the catalyst
1.4. Economics
1.4.1. Low operating cost
1.4.2. Low capital cost
1.5. Safety/Environmental issue
1.5.1. the catalyst need to be manage carefully when the process at high temperature
2. Fluidized Bed
2.1. Operation Principle
2.1.1. Continuous process. Fluidized bed reactors are heterogeneous catalytic reactors in which the mass of catalyst is fluidized. This allows for extensive mixing in all directions. A result of the mixing is excellent temperature stability and increased mass-transfer and reaction rates.
2.2. Application
2.2.1. Wastewater treatment
2.2.2. bulk anaerobic fermentations
2.3. Advantages/Disadvantages
2.3.1. Advantages
2.3.1.1. Uniform particle mixing
2.3.1.2. Uniform temperature gradient
2.3.1.3. Easy to replace catalyst
2.3.2. Disadvantages
2.3.2.1. Catalyst may be deactivated
2.3.2.2. Large pressure drop
2.3.2.3. Erosion of reactor walls may occur
2.4. Economics
2.4.1. Expensive to construct and maintain
2.4.2. Regeneration equipment for catalyst is expensive
2.5. Safety
2.5.1. As the catalyst in form of liquid, it is easier to come out from reactor through product pipe line, this should be prevent effectively,
3. Photobioreactor
3.1. Types
3.1.1. Open System
3.1.1.1. Open pond
3.1.2. Closed System
3.1.2.1. Tubular photobioreactor
3.1.2.2. Plate photobioreactor
3.1.2.3. Christmast tree photobioreactor
3.1.2.4. Horizontal photobioreactor
3.2. Operation Principle
3.2.1. used to promote biological growth by controlling environmental parameters such as lights
3.2.2. The tubes are made of acrylic and are designed to have light and dark intervals to enhance the growth rate.
3.2.3. Has a built-in cleaning system that internally cleans the tubes without need to stop the production.
3.3. Applications
3.3.1. To cultivate phototrophic microorganism
3.3.2. Popular in growing Algae
3.4. Advantages/Disadvantages
3.4.1. Advantages
3.4.1.1. Higher productivity
3.4.1.2. Large surface to volume ratio
3.4.1.3. Better control of gas transfer
3.4.1.4. More uniform temperature
3.4.1.5. Better protection from outside contamination.
3.4.2. Disadvantages
3.4.2.1. High costing
3.4.2.2. Technical dificulty in sterilzing
3.5. Economics
3.5.1. High capital cost
3.5.2. Low running cost
3.6. Environmental issue
3.6.1. Algae blooms in lakes and coastal waters can be prevented and minimized
3.6.2. Carbon dioxide released can be reduced since it can be supply back to the algae for photosynthesis process
4. by Nashrah Ayna Shah Fiesal, Afiq Aiman Shukri, Jailani Zulkifli
5. Bioreactor is usually a vessel, used to direct activity of a biological catalyst to achieved a desired chemical transformation.
6. Stirred-Tank
6.1. Operation Principles
6.1.1. Mode of Operation
6.1.1.1. Batch
6.1.1.1.1. Liquids and gas are usually charged via inlets in the top cover of the reactor. Vapours and gases also discharge through connections in the top. Usually liquids products are removed from the bottom.
6.1.1.2. Continuous
6.1.1.2.1. The substrate is continuously fed into the system and the product is continually drawn out and separated, with the producing organism recycled back into the tank for reuse.
6.1.2. Mechanically fitted with agitator system and sometimes sparger. Agitator system consist of agitator and baffles.
6.1.2.1. To provide good mixing
6.1.2.2. To prevent a whirlpool effect that could impede proper mixing
6.1.3. Sterile medium and inoculum are introduced into a sterilized tank, and the air supply typically enters at the bottom.
6.2. Applications
6.2.1. Aeration of liquid and heat exchange
6.2.2. Plant cell suspension
6.2.3. Dispersion of gas-liquid mixtures
6.3. Advantages/Disadvantages
6.3.1. Advantages
6.3.1.1. Suitable for low volume & high-value products
6.3.1.2. Suitable for reaction with good mass and heat transfer
6.3.1.3. Flexibility with varying products system
6.3.2. Disadvantages
6.3.2.1. The need for shaft seals and bearings
6.3.2.2. High power consumption and high shear forces
6.3.2.3. Size limitation by motor size, shaft length and weight
6.4. Economics
6.4.1. Low Capital Cost
6.4.2. Low labor cost but high energy input is needed to power the impellers
6.5. Environmental Issue
6.5.1. Possibility of contamination and high shear environment
7. Airlift
7.1. Types
7.1.1. Internal-Loop Split
7.1.2. Internal-Loop Concentric Loop
7.1.3. External-Loop
7.2. Operation Principles
7.2.1. Mode of Operation
7.2.1.1. Batch
7.2.1.2. Fed-Batch
7.2.2. Motionless and pnuematic bioreactor where the internal circulation and mixing achieved by bubbling air. The turbulence caused by the fluid flow ensures adequate mixing of the liquid
7.2.3. Air is typically fed through a sparger ring into the bottom of a central draught tube that controls the circulation of air and the medium. Air flows up the tube, forming bubbles, and exhaust gas disengages at the top of the column. The degassed liquid then flows downward and the product is drained from the tank.
7.2.4. The tube is designed to serve as an internal heat exchanger, or a heat exchanger can be added to an internal circulation loop.
7.3. Applications
7.3.1. Growth of microorganism, hear-sensitive mammalian and plant cells in culture
7.3.2. Waste water treatment
7.3.3. Used for both free and immobilized cells
7.4. Advantage/Disadvantage
7.4.1. Advantage
7.4.1.1. Simple design (no moving parts/agitator shafts)
7.4.1.2. Efficient gas-phase disengangement
7.4.1.3. Well-defined residence time for all phases
7.4.2. Disadvantage
7.4.2.1. Lower efficiency of gas compression
7.4.2.2. Inefficient gas/liquid separation when foaming occurs
7.4.2.3. Greater air throughput and high pressure required for large scale
7.5. Economics
7.5.1. Low operating cost
7.5.1.1. As no agitator used
7.5.1.2. Less maintenance
7.5.2. Lower power requirement
7.6. Environmental Issue
7.6.1. The use of airlift bioreactor extends to other chemical and allied industries, such as petroleum in which toxic SO2 and N2 are released causing environmental pollution.
8. Membrane Bioreactor (MBR)
8.1. Types of membrane configuration
8.1.1. Flat sheets (FS)
8.1.2. Hollow fiber (HF)
8.1.3. Multitube (MT)
8.2. Operation Principle
8.2.1. Use of membrane systems combined with biological processes to get superior clear water discharge and it is commonly used in industrial and household wastewater treatment
8.2.2. Systems are built with having two different compartments.
8.2.2.1. At screening stage, the waste water enters the unit. Heavy solids are first separated and go to another compartment which houses the membranes . This is important so that the larger molecules such as scum and grit materials will not trap on the surface of the membrane and led to fouling.
8.2.2.2. The biological process takes place in the second compartment. It has vigorous agitation coming from air bubbles generated from a blower system. This will clean the surface of the membrane to prevent build up of material on the surface and to provide sufficient oxygen concentration for biological action
8.2.3. Most unit equipped with a backflush system whereby discharged waste water will now move counter flow from the permeate side back again to the system to dislodge trapped material accumulating on the surface.
8.3. Applications
8.3.1. Waste water treatment
8.3.2. Removal of emerging trace organic compounds
8.4. Advantages/Disadvantages
8.4.1. Advantages
8.4.1.1. No settlement problems
8.4.1.2. No equalisation of hydraulic and organic loadings required
8.4.1.3. Small footprint
8.4.2. Disadvantages
8.4.2.1. Fouling of membrane surface
8.4.2.2. Membrane channel clogging
8.4.2.3. Process is kind of complex
8.5. Economics
8.5.1. High capital cost
8.5.2. High running costs
8.6. Safety
8.6.1. Monitoring and regular maintenance need to be done on membrane