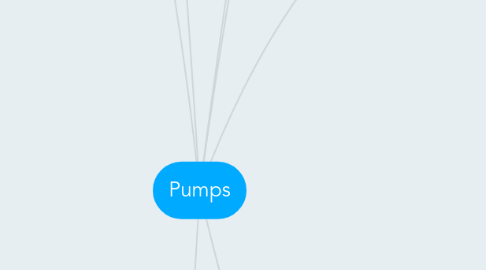
1. Classification
1.1. Positive Displacement Pumps
1.1.1. Definition
1.1.1.1. A positive displacement pump operates by alternating filling a cavity and then displacing a given volume of liquid.
1.1.1.2. A positive displacement pump delivers a constant volume of liquid for each cycle independent of discharge pressure or head.
1.1.2. The positive displacement pump can be classified as
1.1.2.1. Reciprocating pumps
1.1.2.1.1. Piston
1.1.2.1.2. Plunger
1.1.2.1.3. Diaphragm
1.1.2.2. Rotary pumps
1.1.2.2.1. Gear
1.1.2.2.2. Lobe
1.1.2.2.3. Screw
1.1.2.2.4. Vane
1.1.2.2.5. Regenerative (Peripheral)
1.1.2.2.6. Progressive Cavity
1.1.2.3. Steam pumps
1.1.2.4. Power pumps
1.1.3. Source Link : http://www.engineeringtoolbox.com/positive-displacement-pumps-d_414.html
1.2. Centrifugal or Roto-Dynamic
1.2.1. Definition
1.2.1.1. The centrifugal or roto-dynamic pump produce a head and a flow by increasing the velocity of the liquid through the machine with the help of the rotating vane impeller.
1.2.2. The Centrifugal or Roto-Dynamic pump can be classified as
1.2.2.1. Radial
1.2.2.2. Axial
1.2.2.3. Mixed Flow Units
1.2.2.4. End Suction Pumps
1.2.2.5. In-Line Pumps
1.2.2.6. Double Suction Pumps
1.2.2.7. Vertical Multistage Pumps
1.2.2.8. Horizontal Multistage Pumps
1.2.2.9. Submersible Pumps
1.2.2.10. Self-Priming Pumps
1.2.2.11. Axial-Flow Pumps
1.2.2.12. Regenerative Pumps
1.2.3. Source Link: http://www.engineeringtoolbox.com/positive-displacement-pumps-d_414.html
2. Symptoms
2.1. PUMP MOTOR FAILS TO START
2.1.1. Blown fuse or tripped breaker
2.1.2. Open thermal overload in motor starter
2.1.3. Low line current
2.1.4. Open circuit in limit switches, timers or other control devices in pump motor starter circuit
2.1.5. Motor damage
2.2. PUMP RUNS BUT FAILS TO DELIVER
2.2.1. Insufficient hydraulic oil
2.2.2. Check valve(s) lodged open by solids
2.2.3. Worn or dirty check valves
2.2.4. Suction or discharge line blocked
2.2.5. Isolation valve closed
2.2.6. Pump is not primed
2.2.7. Check valve(s) installed incorrectly
2.2.8. Solids buildup between diaphragm and contour plate, preventing diaphragm movement
2.3. PUMP FAILS TO DELIVER RATED CAPACITY
2.3.1. Incorrect capacity setting
2.3.2. Insufficient hydraulic oil
2.3.3. Starved suction
2.3.4. Internal or external relief valve set too low for system conditions and is relieving
2.3.5. Leaky suction piping
2.3.6. Excessive suction lift
2.3.7. Liquid close to boiling point
2.3.8. Liquid viscosity too high
2.3.9. Worn or dirty check valves
2.4. PUMP DELIVERS TOO MUCH CAPACITY
2.4.1. Insufficient discharge pressure
2.4.2. Too much suction pressure
2.5. NOISY OPERATION OF BALL CHECK VALVES
2.5.1. Excessive gear wear
2.5.2. End play in worm (motor) shaft
2.5.3. Improper lubrication
2.5.4. Worn bearings
2.6. MOTOR OVERHEATS
2.6.1. Motor overloaded due to operating in excess of pump discharge pressure rating
2.6.2. Improper wiring or low voltage
2.6.3. Hydraulic oil too viscous
2.6.4. High ambient temperature
2.7. PUMP LEAKING OIL
2.7.1. Oil plug loose
2.7.2. Pump overfilled with oil
2.7.3. Breather cap loose or missing
2.7.4. Diaphragm head bolts not tightened
2.8. Source Link : http://jaecofs.com/technical-info/troubleshooting-guide/
3. Working Operation
3.1. Positive Displacement Pump
3.1.1. A positive displacement pump makes a fluid move by trapping a fixed amount of the fluid and forcing (displacing) that trapped volume into a discharge pipe or discharge system.
3.1.2. Some positive displacement pumps use an expanding cavity on the suction side and a decreasing cavity on the discharge side. Liquid flows into the pump as the cavity on the suction side expands and the liquid flows out of the discharge as the cavity collapses. The volume remains constant through each cycle of pump operation.
3.1.3. Positive Displacement pumps do not use impellers, but rely on rotating or reciprocating parts to directly push the liquid in an enclosed cavity, until enough pressure is built up to move the liquid into the discharge system. The pump does not rely on raising the velocity of the fluid as the centrifugal pump does by moving the liquid through the impeller. Consequently, the fluid velocity inside a positive displacement pump is much lower than that of a centrifugal pump. This is often a desirable feature for certain applications, such as when needing to pump a media containing fragile solids.
3.1.4. Source Link: http://www.processindustryforum.com/article/different-types-pumps-positive-displacement-pumps http://www.engineeringtoolbox.com/positive-displacement-pumps-d_414.html
3.1.5. Video Link : https://www.youtube.com/watch?v=DXYrJq_fjbI
3.2. Centrifugal or Roto-Dynamic Pump
3.2.1. Similar to all other pumps, the centrifugal pump also converts one form of energy into another form to operate for pumping fluid.
3.2.2. It principally takes mechanical energy from the motor assembled with the pump, and converts it into either kinetic energy or the potential energy of the fluid movement.
3.2.3. It absolutely depends upon the fluid as to what energy mechanical energy convert into. For example, when the fluid is lifted above and against the force of gravity, the form of energy changes from mechanical to potential. Likewise if the fluid experiences change in its pressure, even then the form of energy changes, but this time it changes from mechanical to kinetic energy.
3.2.4. Modern centrifugal pumps, however, work on a slightly different mechanism. The impeller, as indicated earlier, is available in both straight and curved blades/vanes. These curved blades are used by the impeller to exert an outward force over the fluid. Impeller is actually a spinning component and plays the vital role in pushing the fluid outside.
3.2.5. In response to this outward force upon the fluid, the fluid also starts circular motion. The continuous rotation of the fluid creates a pressure within the impeller and this rise in pressure transfers some amount of energy to the discharge end too.
3.2.6. Eventually when the pressure of the discharge end increases, the fluid is forced to move out via the discharge end and thus one pumping cycle is completed.
3.2.7. Source Link : http://www.pumpsandspares.com.au/tutorials/how-does-a-centrifugal-pump-work/
3.2.8. Video Link : https://www.youtube.com/watch?v=0ycvbFxB87s
4. Definiton
4.1. It is a machine which converts mechanical energy into hydraulic energy to move liquid from one place to another place.
4.2. The basic function of a pump is to transfer fluid, liquid or gasses from a lower to a higher level.
4.3. Source Link : http://www.engineeringtoolbox.com/positive-displacement-pumps-d_414.html
5. Failure
5.1. Types Of Failure
5.1.1. 1. Seal Leakage
5.1.2. 2. Shaft Breakzge
5.1.3. 3. Casting Breakage
5.2. Possible Causes Of Failure
5.2.1. Seal Breakage
5.2.1.1. Cooling System Contamination
5.2.1.1.1. The abrasiveness of the particles found in a badly contaminated system will prematurely wear the water pump seal. Harmful contamination is common in systems that are not properly maintained. A system that is not properly pressurized will allow air to enter and promote the build-up of rust. If water with a high mineral content is added to the system and is heated, it will begin to form deposits that will accumulate and cause passage restrictions which may damage the seal.
5.2.1.2. Thermal Shock
5.2.1.2.1. The seal was more closely inspected after no signs of contamination were observed. This revealed that the seal damage had come from thermal shock, typically caused by adding cold coolant to an overheated engine. The damage appears as a diametrical crack across either the seal face or the mating ring. This can also occur following water pump replacement if the engine is started before adding coolant.
5.2.1.3. High Temperatures
5.2.1.3.1. Mechanical seal have spring-loaded assemblies to keep the carbon seals intact and rubber parts that may disintegrate if the engine runs hot or overheats. If a system overheats to the point of boiling out and the system is permitted to run dry, the polished sealing faces can wear and warp. A worn seal face allows fluids to escape and leak out the weep hole. Most pumps will leak catastrophically shortly after a boil-over.
5.2.2. Shaft Breakage
5.2.2.1. Bearing Overload
5.2.2.1.1. This bearing failed as the result of a sudden overload caused by vibration or imbalance. The lack of heat-related discoloration indicates that this was sudden rather than gradual, and was probably compounded by rapid engine acceleration. Blue discoloration of the shaft would indicate that there was excessive heat build-up for some period prior to shaft breakage. This heat build-up can be caused by the tremendous centrifugal forces created by imbalance. This overloads the bearing generating a great deal of heat. This load is amplified through rapid acceleration and high RPM operation.
5.2.3. Casting Breakage
5.2.3.1. Excessive Vibration
5.2.3.1.1. Casting failure is normally associated with heavy vibration or imbalance which can be caused by a badly worn fan clutch or bent fan.
5.2.4. Source Link : http://asc-ind.com/technical-assistance/technical-resources/helpful-articles-tips/water-pump-failures-and-causes/ https://www.flowkoolerwaterpumps.com/info/common_waterpump_failures.html
6. Performance
6.1. Terms
6.1.1. The pump characteristic is normally described graphically by the manufacturer as the pump performance curve. The pump performance curve describes the relation between the flowrate and the head for the actual pump. Other important information for a proper pump selection is also included - like efficiency curves, net positive suction head curve, pump curves for several impeller diameters and different speeds, and power consumption.
6.1.2. Increasing the impeller diameter or speed increases the head and flow rate capacity - and the pump curve moves upwards. The head capacity can be increased by connecting two or more pumps in series, or the flow rate capacity can be increased by connecting two or more pumps in parallel.
6.1.3. Source Link : http://www.engineeringtoolbox.com/pump-system-curves-d_635.html http://www.engineeringtoolbox.com/npsh-net-positive-suction-head-d_634.html
6.2. Pump Selection
6.2.1. 1. Process and design requirements
6.2.1.1. In some cases the pump selection is determined by some stringent requirements for a number of design or process parameters. Unlike piston-type pumps, centrifugal pumps can provide uniform delivery of pumped medium, whereas in order to meet uniformity condition on a piston-type pump its design has to be made noticeably complicated, by arranging on the crankshaft several pistons making reciprocating movements with certain delay from each other. At the same time, delivery of pumped medium in discrete portions of set volume can also be a process requirement. Example of definitive design requirements can be the use of submerged pumps in cases, when it is necessary and only possible to install the pump below level of the pumped fluid.
6.2.1.2. The pump process and design requirements are seldom definitive, and ranges of suitable types of pumps for various specific cases of application are known as a matter of experience accumulated by humanity, and there is no need to enumerate them in detail.
6.2.2. 2. Nature of pumped medium
6.2.2.1. Characteristics of the pumped medium often become a decisive factor in pumping equipment selection. Different types of pumps are suitable for pumping of various media differing in viscosity, toxicity, abrasiveness and many other parameters. So screw pumps can pump viscous media with different inclusions without damaging structure of the medium, and can successfully be used in food-processing industry for pumping of jams and pastes with various fillers. Corrosion properties of the pumped medium determine material design of the selected pump, and toxicity – degree of its air-tightness.
6.2.3. Key design parameters
6.2.3.1. Operational requirements specified by different industries can be satisfied by several types of pumps. In the situation like this preference is given to the type of pump which is most suitable under concrete values of key design parameters (capacity, head and power consumption)
6.2.4. Source link : http://www.ence-pumps.ru/eng/podbor_raschet_nasosov.php
7. Failure
7.1. Types Of failure
7.1.1. 1. Seal Leakage
7.1.2. 2. Shaft Breakage
7.1.3. 3. Casting Breakage
7.1.4. 4. Weep Hole Leakage
7.1.5. 5. Leakage of Mounting Surface
7.1.6. 6. Rust and Corrosion
7.1.7. 7. Deposit Build-Up
7.1.8. 8. Cavitation
7.2. Possible Causes
7.2.1. Seal Leakage
7.2.1.1. Clean System
7.2.1.1.1. The seal was more closely inspected after no signs of contamination were observed. This revealed that the seal damage had come from thermal shock, typically caused by adding cold coolant to an overheated engine. The damage appears as a diametrical crack across either the seal face or the mating ring. This can also occur following water pump replacement if the engine is started before adding coolant.
7.2.1.2. Dirty System
7.2.1.2.1. The abrasiveness of the particles found in a badly contaminated system will prematurely wear the water pump seal. Harmful contamination is common in systems that are not properly maintained. A system that is not properly pressurized will allow air to enter and promote the build-up of rust. If water with a high mineral content is added to the system and is heated, it will begin to form deposits that will accumulate and cause passage restrictions which may damage the seal.
7.2.2. Shaft Breakage
7.2.2.1. Bearing Overload
7.2.2.1.1. This bearing failed as the result of a sudden overload caused by vibration or imbalance. The lack of heat-related discoloration indicates that this was sudden rather than gradual, and was probably compounded by rapid engine acceleration. Blue discoloration of the shaft would indicate that there was excessive heat build-up for some period prior to shaft breakage. This heat build-up can be caused by the tremendous centrifugal forces created by imbalance. This overloads the bearing generating a great deal of heat. This load is amplified through rapid acceleration and high RPM operation.
7.2.3. Casting Breakage
7.2.3.1. Excessive Vibration
7.2.3.1.1. Casting failure is normally associated with heavy vibration or imbalance which can be caused by a badly worn fan clutch or bent fan.
7.2.4. Weep Hole Leakage
7.2.4.1. Contaminated coolant is the main cause of weep hole leakage.
7.2.5. Leakage of Mounting Surface
7.2.5.1. Improper water pump installation or improper use of seals/gaskets or sealant.
7.2.6. Rust and Corrosion
7.2.6.1. Contaminated coolant, non-compatible coolant or mixing coolants of different chemistries. Another possible cause may be a defective pressure cap causing air bubbles, accelerating the rust process.
7.2.7. Deposit Build-Up
7.2.7.1. Contaminated coolant, non-compatible coolant or mixing coolants of different chemistries.
7.2.8. Cavitation
7.2.8.1. The formation of bubbles at the coolant inlet of the pump. As the pressure increases in the system, the bubbles implode and cause harm.