controlling
저자: Khairunnisa Dinda
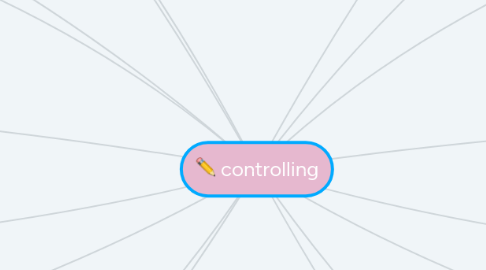
1. Reason why controlling is needed
1.1. To adapt to change & uncertainty
1.2. To discover irregularities & errors
1.3. To reduce costs, increase productivity, or add value
1.4. To detect opportunities
1.5. To deal with complexity
1.6. To decentralize decision making & facilitate teamwork
2. Steps in the Control Process
2.1. Establish standards
2.2. Measure performance
2.3. Compare performance to standards
2.4. Take corrective action if necessary
3. Levels of Control
3.1. Strategic control
3.2. Tactical control
3.3. Operational control
4. Six Areas of Control
4.1. Physical
4.2. Human Resources
4.3. informational
4.4. Financial
4.5. Structural
4.6. Cultural
5. Structural Area
5.1. Bureaucratic control
5.2. Decentralized control
6. The Balanced Scoreboard
6.1. Financial
6.2. Customer
6.3. Internal business
6.4. Innovation & learning
7. Why Measure-Managed Firms Succeed
7.1. Top executives agree on strategy
7.2. Communication is clear
7.3. There is better focus and alignment
7.4. The organizational culture emphasizes teamwork and allows risk taking
8. Barriers to Effective Measurement
8.1. Objectives are fuzzy
8.2. Managers put too much trust in informal feedback systems
8.3. Employees resist new measurement systems
8.4. Companies focus too much on measuring activities instead of results
9. The Visual Representation of a Balanced Scorecard
9.1. Strategy Map
10. Budgets
10.1. Incremental budgeting
10.2. Fixed versus Variable Budgets
10.3. Types
10.3.1. Cash or cashflow budget
10.3.2. capital expenditures budget
10.3.3. sales or revenue budget
10.3.4. financial budget
10.3.5. operating budget
10.3.6. nonmonetary budget
10.3.7. expense budget
10.4. Financial Statements
10.4.1. Balanced sheet
10.4.2. Income statement
10.5. Ratio Analysis
10.5.1. Liquidity ratios
10.5.2. Debt management ratios
10.5.3. Return ratios
10.6. Audit
10.6.1. External
10.6.2. Internal
11. The PDCA Cycle
11.1. Plan
11.2. Do
11.3. Check
11.4. Act
12. Total Quality Management
12.1. Applying TQM to Services
12.1.1. RATER scale
12.2. Some TQM Techniques
12.2.1. Outsourcing
12.2.2. Reduced cycle time
12.2.3. Statistical process control
12.2.4. Six sigma & Lean Six Sigma
12.2.5. ISO 9000 and 14000 Series
12.3. Two Core Principles of TQM
12.3.1. People orientation
12.3.2. Improvement orientation