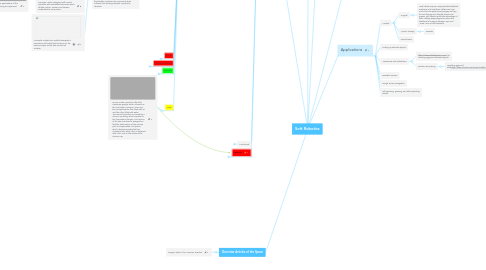
1. Based in SF, check on video on site http://www.pneubotics.com/
2. Think about an elephant’s trunk. Made of soft matter in the form of 150,000 muscles, it has the ability to tear down trees but also delicately manipulate objects the size of a peanut.
3. Actuators
3.1. Smart Materials
3.1.1. Coiled-thread Artificial Muscles (thermal expansion)
3.1.1.1. Thermal expansion of the thread in its coiled state results in linear extension or contraction, and can produce a force per weight superior to that of human muscle. Actuation is completed by applying a voltage across the muscle, where Joule heating in the thread provides the driving force for thermal expansion. Coiled muscles are embedded in the soft actuator.
3.1.1.1.1. Method developed by the Zhao Research Group at Colorado State University
3.1.1.1.2. Process available on the open source website soft robotics toolkit (you however must anneal the thread...)
3.1.2. Dielectric Elastomers
3.1.2.1. Working principle: a passive elastomer film is sandwiched between two compliant electrodes. When V is applied, electrostatic pressure (from Coulomb forces) acts between the electrodes, which squeezes the elastomer film.
3.1.2.1.1. Manta ray inspired soft robot: The robot is driven by dielectric elastomer assembly. Hydrogel is an ionically conductive electrode. The open water functions as the electric ground and the other electrode. When voltage is applied, (+) and (-) charges accumulate on either side of the DE, which deforms the DE membranes. The robot uses silicone thin film as fins, and a silicone frame as the elastomeric body. An electromagnet is embedded in the tail, which steers the fish.
3.1.2.1.2. University of California San Diego also used the open water as the other electrode
3.1.3. Thermo-responsive hydrogels
3.1.3.1. Reversible patterning and actuation of hydrogels by electrically assisted ionoprinting at the University of North Carolina
3.1.3.1.1. Press
3.1.3.2. Bio-Inspired Fast Actuation by Mechanical Instability of Thermoresponding Hydrogel Structures
3.1.3.2.1. (Study was conducted by the Tiefeng Li Group at the Zhejiang University)
3.1.4. Light-controlled hydrogels
3.1.4.1. UC Berkeley team was inspired by the way plants grow towards light: Elastic proteins were combined with graphene sheets (one-atom thick) which generate heat when exposed to near infrared light. The heat affects the synthetic proteins, which absorb water when cooled and release when hot. The gel shrinks when the light hits it and therefore bending can be controlled
3.1.4.1.1. Press
3.1.5. Shape Memory Alloys
3.1.5.1. Working Principles: an alloy that "remembers" its original state; after it is deformed, it can then be heated up which will return it to its original form.
3.1.5.1.1. One of the editions of this octopus inspired robot had tentacles are made up of coils, and by passing current through different combinations of coils, the tentacles can bend is the desired fashion. This is a research project funded by the European Commission
3.1.5.2. Cornell University developed a composite of two entangled foams: an elastomer and a low melting temperature metal, that exhibits dynamic shape morphing and shape memory actuation. By melting and freezing the metal foam, the composites can both self-heal and be assembled into larger, continuous structures from smaller sub-components.
3.1.6. Low-melting point metals
3.1.6.1. These metals are know as "Field's metal", and are fusible alloys (easily meltable at low temperatures) that becomes liquid at approximately 62 °C. This is an alloy of Bi, In and Sn.
3.1.6.1.1. Washington State University embedded Field's metal and power resistors in the middle of the silicon shape. When power is applied, the resistors dissipate heat into the surrounding silicone locally raising the temperature of the metal just above its melting point. Once a particular section of the metal bars reaches its molten state, the entire elastomer finger can be bent. The actuating force is applied by tendons lying just within the top layer of the elastomer. By varying which resistor is activated, the location of the joint within the finger can be varied, thus changing the geometry of its compliance.
3.2. Pneumatic
3.2.1. Oregon State University evaluated pneumatic energy sources for soft robots: Conclusions: Battery-powered microcompressors provide relatively high capacity, but maximum pressure and flow rates are low Cylinders of compressed fluid provide high pressures and flow rates, but their limited capacity leads to short operating times Methane and butane possess the highest net fuel energy densities however hey typically react at speeds and pressures too high for many soft robots and require extensive system-level development Hydrogen peroxide decomposition requires not only few additional parts (no pump or ignition system) but also considerable system-level development
3.2.1.1. Soft Barrier
3.2.1.1.1. This soft barrier has two components -one to control convection and one to control conduction. Compartments are inflated and deflated in order to control heat transfer.
3.2.1.2. Soft Wheel
3.2.1.2.1. Soft Wheel Robot This is a cylindrical soft sobot which is propelled in a rolling motion by pneumatically actuating different compartments.
3.2.1.3. PneuNets
3.2.1.3.1. PneuNets Pneumatic Networks are made up of a series of channels and chambers inside of an elastomers. Modifying the geometry of the shape will change its path of motion
3.2.1.4. Fiber-Reinforced Actuators
3.2.1.4.1. Fiber-Reinforced Actuators Consists of an elastomer bladder wrapped with inextensible reinforcements. Wrapping the bladder constrains its movement when inflated; thus tending towards a particular direction
3.2.1.5. Sleeve
3.2.1.5.1. This sleeve is actuated by air - there are tubes surrounding the heart that constrict and inflate, assisting the heart.
3.2.1.6. Hydrogen Peroxide
3.2.1.6.1. Uses a microfluidic circuit to direct fuel flow, where a reaction will convert Hydrogen Peroxide to gas, pneumatically actuating the octopus. This is the first completely soft robot.
3.2.1.7. Jamming
3.2.1.7.1. Working Principle:Granular material has this property called “jamming”. This is a reversible transition that the material undergoes which changes it from a rigid state to a malleable state. This transition is actuated by lowering the air pressure in a chamber with a granular material.
3.2.1.8. Water
3.2.1.8.1. FESTO made a product called the FlexShape gripper which is based on the chameleon's tongue. There are two compartments: one filled with air and the other filled with water. This second chamber is covered by a silicone moulding, which equates to the chameleon’s tongue. The volume of the two chambers is designed so that the deformation of the silicone part is compensated. The piston, which closely separates the two chambers from each other, is fastened with a thin rod on the inside of the silicone cap.
3.3. Mechanical
3.3.1. Cables
3.3.1.1. Pulling Cables Tension is applied to a cable and the compliant material deforms, causing the "finger" to bend.
3.3.1.1.1. This method is similar to that used in the inmoov finger.
3.3.1.1.2. SDM fingers: Used SDM to build multi-jointed fingers that are actuated by pulling a cable.
3.3.2. Servos
3.3.2.1. Worcester Polytechnic Institute designed a hexapod that utilizes origami techniques in order to avoid the use of fasteners. This robot uses servo motors to move the legs.
3.3.2.2. University of California, San Diego created a self-folding robot -the walking is actuated via motor, the self folding is actuated via shape-memory composites
3.3.2.3. Control Systems and Robotics Laboratory of the Technological Educational Institute of Crete created this undulatory propulsion robot exhibiting fluid fin-like motion with servos
3.3.2.3.1. http://lyle.smu.edu/propulsion/Pages/undulatory.htm
3.4. Hydraulic
3.4.1. The same body structure as PneuNets was used at MIT for hydrogel robots, actuated by hydraulics (pumping water in and out of the system)
3.4.1.1. The hydrogels used were developed over 5 years by the Soft Active Materials Laboratory at MIT
3.4.1.2. These robots are nearly transparent --since the hydrogels are nearly composed of all water
4. Manufacturing
4.1. Shape Deposition Manufacturing (SDM)
4.1.1. Shape Deposition Manufacturing is a rapid prototyping process in which mechanisms are simultaneously fabricated and assembled through alternating steps of subtractive (milling) and additive (casting) manufacturing.
4.1.1.1. Method is developed by the Biomimetics lab at Stanford
4.2. 3D Printing
4.2.1. University of California, San Diego printed their soft actuators using a multimaterial 3D printer (Object 350 Connex 3, Stratasys). This printer is capable of printing mixtures of a rubbery material (TangoBlackPlusand a rigid material (VeroClear) resulting in materials with a range of Shore hardness values from 30A-95A.
4.2.2. TU Delft is working on 3D printing air chambers in flexible material. (insufficient data on their website).
4.2.3. Oregon State University and Harvard University developed a custom-designed printhead composed of four cylindrical nozzles aligned coaxially in order to print capacitive soft strain sensors
4.3. complex
4.3.1. Stereolithography
4.3.1.1. Digital Mask Projection Stereolithography
4.3.1.1.1. Cornell University developed a custom system that uses an off-the-shelf projector to simultaneously control more than two million individual pixels of light. Nominal resolution of 35µm in XY plane. Layer heights of 25-50µm. Build speed of ~25mm/hr.
4.3.1.2. Fused deposition modeling and stereolithography
4.3.1.2.1. Washington State University used a technique involving printing hollow channels within 3D printed parts and then filling them with a low melting point liquid metal alloy that solidifies to form electrical traces
4.3.2. 3D Printed Hydraulics
4.3.2.1. MIT developed a 3D printing method which deposits liquids and photopolymers, allowing channels to be pre-filled with liquids
4.3.3. Liquid Metal Injection
4.3.3.1. Carnegie Mellon University is working on injecting liquid metals into channels for the soft artificial skin
4.4. mold making
4.4.1. trial and error to get right shape/form
4.4.1.1. replicable once mold is made
5. Overview Articles of the Space
5.1. Oregon State in the American Scientist
6. Challenge with dielectric elastomers: require a huge voltage (100s-1000s)
7. Applications
7.1. Locomotion and Exploration
7.1.1. Reasoning: - Adaptable to environments that may be difficult for rigid robots to navigate (ie underwater) - Soft materials can be tolerant to external shock - Inherently very compliant, can squeeze through tight spaces - Some can exhibit rapid agile maneuvers (escape maneuvers such as in fish)
7.1.1.1. GoQBot: Developed at Tufts University, this robot simulates a caterpillar and rolls for locomotion
7.1.1.2. Meshworm: developed at MIT, this robot exhibits peristaltic locomotion similar to that of an earthworm. The use of flexible mesh materials allows external shock absorption -ie hitting it with a hammer.
7.1.1.3. MIT developed a soft-robotic fish
7.2. Manipulation
7.2.1. Reasoning : Rigid robots have a natural limitation to the types of manipulation they can perform due to low DOF, complexity, and difficulty in calculation of grasping action - Soft robotic manipulators are more compliant and can manipulate fragile and unknown objects by a simple - Most soft-robots achieve manipulation by granular or tentacle-like techniques
7.2.1.1. Random Bin picking
7.2.1.2. On-orbit Serviving
7.3. Medical and Surgical Applications
7.3.1. Reasoning: Soft robots inherently have advantage of being compliant with the natural tissues of human and living organisms. - Some soft robots have controllable stiffness (granular)
7.3.1.1. Minimally Invasive Surgery: Soft robots overcome the obstacle of low DOF
7.3.1.2. Endoscopy: Navigation through the human body can be made safer through the use of soft robots
7.3.1.3. See info on the Sleeve for the heart
7.3.1.4. Colongscopy http://boingboing.net/tag/robotics
7.4. Rehabilitation and Wearable Robots
7.4.1. Reasoning: - Use of soft and elastic materials absorbs mechanical stress and minimizes the chance of injury to both the robot itself and the user.
7.4.1.1. Soft Robotic Gloves
7.4.1.2. Ankle Rehabilitation
7.4.1.3. Soft robotic exosuits
7.4.1.4. Stretchable sensors; a tremor neurobot is a form of sleeve which assesses and attenuates pathological tremors and can satisfy aesthetic appearance preferred by the patients
7.4.1.5. Soft oral rehabilitation robot for people with mandibular mobility disorders
8. Art
8.1. Wearables
8.1.1. Interactive Architecture Lab at the Bartlett and Helge Wurdemann from UCL Mechanical Engineering
8.1.2. Kari Love: started off as a costume designer, designed an inflatable spider man costume Now works at a start-up; recent projects trying to develop a spacesuit for NASA http://superreleaser.com/project-profiles/
8.1.3. "Archê is a wearable mediation of the surrounding air, which allows the aerial process caused by human respiration to emerge and dissolve."
8.2. Film
8.2.1. Disney is developing soft robots for theme parks-filing a patent for "soft, interactive huggable robots" (April 2017)
8.2.1.1. Disney researching soft skin
8.3. Installations
8.3.1. WonderBot: Uses a soft air muscle actuator to generate movements of the robot, experimented with different designs from tensegrity structure to biomorphic mechanism, the aim of the project is to create a modular system which is flexible to satisfy changing spatial requirements.
8.3.2. Furl: soft pneumatic pavillion
8.3.3. Robotic art display - basically lets a slithering robot move and distribute paint across a canvas https://robotart.org/archives/2017/team/anguis/ This was their entry in the competition
8.3.4. May 2017: Art display in Germany Headline: UC San Diego Artists, Sci-Fi Author Unveil Video Installation for Robot Exhibition in Germany
8.3.5. Exo-Biote
8.4. DIY
8.4.1. http://www.instructables.com/id/Aerobox-A-Soft-Robotics-Control-System/
8.5. Workshops
8.5.1. https://empathy.pixelache.ac/events/soft-robotics-workshop?locale=en
9. Complex=red Easy=green Moderate=yellow
10. Sensors
10.1. Soft Artificial Skin Sensors
10.1.1. Carnegie Mellon University recently developed soft artificial skin sensors that detect contact pressure and multi-axis strains and shear forces. They consist of stretchy silicone embedded with microchannels filled with conductive liquids (liquid metals and ionic liquids)
10.2. Dielectric Elastomer Sensors
10.2.1. Cornell University 3D printed soft capacitors on top of pneumatic actuators which can serve as touch sensors
10.2.2. Cornell University developed stretchable electroluminescent skin where it can undergo large deformations whilst emitting light and sensing this information. The center layer is a thin sheet of silicone with embedded ZnS phosphors that glow under a high electric field. Transparent, ionically conductive hydrogel electrodes sandwich the center dielectric layer.
10.2.3. Harvard and Oregon State developed capacitive soft strain sensors that detect elongation strains. Each fiber has four alternating concentric of a silicone elastomer (dielectric) and an ionically conductive fluid (conductor)
11. Modelling
11.1. Automatic design
11.1.1. Harvard Biodesign lab is working on using automatic design of fiber reinforced actuators to match trajectory.
11.2. Abaqus
11.2.1. This is an FEA software commonly used for soft robotics applications because it is well-known, widely available and particularly suitable for analyses involving large deformations.
11.2.1.1. Oregon State University wrote MATLAB and Abaqus scripts to form the three step process: "The proposed FE-based numerical tool consists of three steps. (A) The model is created using CAD software and then meshed. (B) The deformation of the sensor is determined by using non-linear FE analysis, in which the contours show the normalized Von Mises stress σvm. (C) The resistance at different levels of deformation is obtained by performing a steady-state linear electrical conductivity analysis. The contours show the potential across the channel."
12. Applications
12.1. Medical
12.1.1. Surgical
12.1.1.1. Hard robots require a sophisticated feedback mechanism to help them determine how much force to apply during surgery so they do not damage our delicate tissues and organs. Soft robots could take advantage of their rubbery appendages to reduce the likelihood of surgical damage, says Carl Vause, CEO of Soft Robotics.
12.1.2. Muscle Therapy
12.1.2.1. exosuits
12.1.3. Heart Sleeve
12.2. Picking up delicate objects
12.3. Warehouse and DIstribution
12.3.1. https://www.softroboticsinc.com/ for handling eggs and delicate objects
12.3.2. Random Bin picking
12.3.2.1. Handling eggs and stuffhttps://www.robotics.org/content-detail.cfm?content_id=6002
12.4. wearable sensors
12.5. Rough Terrain Navigation
12.6. self-repairing, growing, and self-replicating robots
13. Soft Lithography
13.1. Uses elastomeric materials -notably PDMS (Polydimethylsiloxane ie silicones)
13.2. Tools are commercially available
14. Idea: Coral Reef Art installation
14.1. undulating motion
14.2. How to progress: -Much like the Exo-Biote installation, the project can have separate pieces. The coral reef is a great habitat to draw inspiration from, since it is filled with soft bodied creatures. -This project is additive -make each part in series, and separately -Other interns and people can easily add to this installation -Thus, each component can be actuated by different means -ie one part can be pneumatic, another can use memory alloys etc. This allows to completely explore the space
14.3. Invertebrates
14.3.1. Echinoderms
14.3.2. sponges
14.3.3. molluscs
14.3.4. Crustaceans
14.3.5. Polychaetes
14.4. See: Cnidaria A phylum containing over species of animals found exclusively in aquatic (freshwater and marine) environments: they are predominantly marine species Their bodies consist of mesoglea, a non-living jelly-like substance,
14.4.1. Polyp (such as sea anemones): Polyps are approximately cylindrical in shape and elongated at the axis of the vase-shaped body.
14.4.2. Medusa: softbodied, free-swimming aquatic animals with a gelatinous umbrella-shaped bell and trailing tentacles.