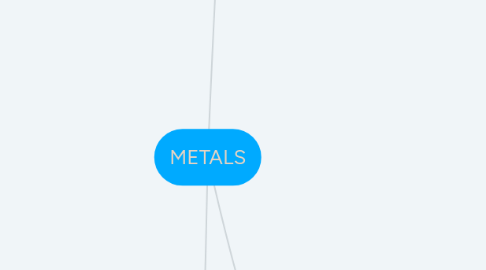
1. Fabrication of Metals
1.1. Casting
1.1.1. Sand Casting
1.1.1.1. Sand is used as the mold material
1.1.1.2. Sand-cast parts include automotive cylinder blocks, fire hydrants and large pipe fittings
1.1.2. Die Casting
1.1.2.1. The liquid metal is forced into the mold at a relatively high velocity and allowed to solidify with the pressure maintained
1.1.2.2. Only works for relatively small pieces and alloys having low melting temperatures
1.1.2.3. An inexpensive method
1.1.3. Investment Casting
1.1.3.1. The pattern is made from a wax having a low melting temperature
1.1.3.2. Fluid metal is poured around the pattern pattern and sets
1.1.3.3. The wax is then melted away
1.1.3.4. Method has high dimensional accuracy
1.1.4. Lost-Foam Casting
1.1.4.1. A variation of investment casting
1.1.4.2. The pattern is foam
1.1.4.3. Molten is placed in the mold, thus melting the foam
1.1.4.4. Complex geometries and tight tolerances are possible
1.1.4.5. Simpler, quicker and less expensive than sand casting
1.1.4.6. Used with cast irons and aluminum alloys
1.1.5. Continuous Casting
1.1.5.1. Many molten metals are solidified by casting into large ingot molds
1.1.5.2. The refined and molten metal is cast directly into a continuous strand with either a rectangular or circle cross section
1.1.5.3. Highly automated and more efficient
1.2. Fabrication of Metals
1.2.1. Extrusion
1.2.1.1. A bar of metal is forced through a die orifice
1.2.1.2. The extruded piece has the desired shape
1.2.1.3. Products include rods, tubing and seamless tubing
1.2.2. Drawing
1.2.2.1. The pulling of a metal piece through a die having a tapered bore
1.2.2.2. Results in a reduction in the cross section, with an increase in length
1.2.2.3. Rod, wire, and tubing products are fabricated in this manner
1.2.3. Forging
1.2.3.1. Mechanically deforming a single piece of hot metal
1.2.3.2. Can be a closed or open die
1.2.3.3. For closed die, a force is brought to bear on two or more die halves having the finished shape
1.2.3.4. For open die, two dies having simple geometric shapes are employed
1.2.3.5. outstanding grain structures
1.2.4. Rolling
1.2.4.1. Most widely used deformation process
1.2.4.2. Passing a metal between two rolls causing a reduction in thickness
1.2.4.3. Cold rolling is used to produce sheet and foil
1.2.4.4. Grooved rolls fabricates circular shapes, I-beams and railroads
1.3. Miscellaneous Techniques
1.3.1. Powder Metallurgy
1.3.1.1. Compaction of powdered metal followed by a heat treatment
1.3.1.2. Suitable for metals having low ductilities
1.3.1.3. Economical to produce parts requiring close dimensional tolerances
1.3.2. Welding
1.3.2.1. Two or more metal parts are joined to form a single piece
1.3.2.2. Both similar and dissimilar metals may be welded
1.3.2.3. The joining bond is metallurgical rather than mechanical
1.3.2.4. Methods include :
1.3.2.4.1. arc
1.3.2.4.2. gas welding
1.3.2.4.3. brazing
1.3.2.4.4. soldering
2. Non-Ferrous Alloys
2.1. Copper and its Alloys
2.1.1. Unalloyed copper is highly resistant to corrosion
2.1.2. Brasses are the most common copper alloys
2.1.3. Bronzes are alloys of copper and several other elements
2.1.4. Bronzes are stronger than the brasses and have good tensile properties
2.2. Aluminum and its alloys
2.2.1. Characterized by a relatively low density, high conductivities, and a resistance to corrosion
2.2.2. Has a low melting temperature
2.2.3. Strength can be enhanced by cold work and alloying, but decreases resistance to corrosion
2.2.4. Used as engineering materials for transportation
2.3. Magnesium and its alloys
2.3.1. Lowest density of all structural materials
2.3.2. Difficult to deform at room temperature
2.3.3. Most fabrication by casting and/or hot-working
2.3.4. Susceptible to corrosion in marine environments but better in normal environment
2.4. Titanium and its alloys
2.4.1. Relatively low density with a high melting point
2.4.2. Extremely strong
2.4.3. Four categories
2.4.3.1. Alpha-alloys
2.4.3.1.1. Preferred for high temperature applications
2.4.3.2. Beta-alloys
2.4.3.2.1. Highly forgeable and has high fracture toughness
2.4.3.3. Alpha+Beta-alloys
2.4.3.3.1. Quite formable
2.4.3.4. Near-alpha alloys
2.4.3.4.1. Has a greater possibility for diversity of microstructures and properties
2.4.4. Chemical reactivity with other materials is a major limitation
2.5. Refractory metals
2.5.1. Extremely high melting temperatures
2.5.2. Some are alloyed with stainless steel to improve corrosion resistance
2.5.3. Molybdenum alloys are used for extrusion dies and structural parts in space vehicles
2.6. The superalloys
2.6.1. Most are used in aircraft turbine components
2.6.2. Must withstand exposure to severely oxidizing environments
2.7. Noble metals
2.7.1. They are expensive
2.7.2. Soft, ductile and oxidation resistant
2.7.3. Used in jewelry, as dental restoration equipment, and for chemical laboratory equipment
2.8. Miscellaneous
2.8.1. Nickel and is alloys are highly resistant to corrosion
2.8.2. Lead, tin and their alloys are used as engineering materials. They are soft and weak but quite resistant to corrosion
2.8.3. Unalloyed zinc is a relatively soft metal with a low melting temperature and is chemically reactive
2.8.4. Zirconium and its alloys are ductile and very resistant to corrosion
3. Ferrous Alloys
3.1. Steels
3.1.1. Low-Carbon Steels
3.1.1.1. Contains less than 0.25 wt% of carbon
3.1.1.2. Unresponsive to heat treatments
3.1.1.3. Soft and weak but very ductile and tough due to it consisting of ferrite and pearlite
3.1.1.4. Least expensive of the steels to produce
3.1.2. Medium-Carbon Steels
3.1.2.1. Contains between 0.25 and 0.60 wt% of carbon
3.1.2.2. May be heat treated to improve mechanical abilities
3.1.2.3. Has low hardenabilities
3.1.2.4. Adding chromium, nickel, and molybdenum improves the heat treating ability
3.1.2.5. Stronger than low-carbon steels but sacrifice ductility and toughness
3.1.3. High-Carbon Steels
3.1.3.1. Carbon contents between 0.60 and 1.4 wt%
3.1.3.2. Almost always in a hardened and tempered state
3.1.3.3. Wear resistant and can hold a sharp edge
3.1.4. Stainless Steel
3.1.4.1. Highly resistant to corrosion in a variety of environments
3.1.4.2. Corrosion resistance improved with nickel and molybdenum additions
3.1.4.3. Three classes
3.1.4.3.1. Martensitic
3.1.4.3.2. Austenitic
3.1.4.3.3. Ferritic
3.1.5. Iron -carbon alloys that may contain other alloying elements
3.2. Cast Irons
3.2.1. Gray Iron
3.2.1.1. Graphite exists as flakes
3.2.1.2. Weak and brittle in tension but strong and ductile in compression
3.2.1.3. Effective for damping vibrations
3.2.1.4. High resistance to wear
3.2.1.5. Least expensive metallic material
3.2.2. Nodular Iron
3.2.2.1. Graphite forms as nodules instead instead of flakes
3.2.2.2. Castings are stronger and more ductile than gray iron
3.2.3. White and Malleable Iron
3.2.3.1. For low-silicon cast irons, most of the carbon exists as cementite
3.2.3.2. Extremely hard but also very brittle
3.2.3.3. Use is limited to applications that need a very hard and wear-resistant surface without large ductility
3.2.3.4. White iron is used to produce malleable iron
3.2.4. Compacted Graphite Iron
3.2.4.1. Carbon exists as graphite, promoteed by silicon
3.2.4.2. Carbon concentration ranges between 3.1 and 4.0 wt%
3.2.4.3. Has a wormlike shape, microstructurally
3.2.4.4. Some graphite may exist as nodules
3.2.4.5. Sharp edges should be avoided
3.2.4.6. An increase in nodularity leads to enhancements of both strength and ductility