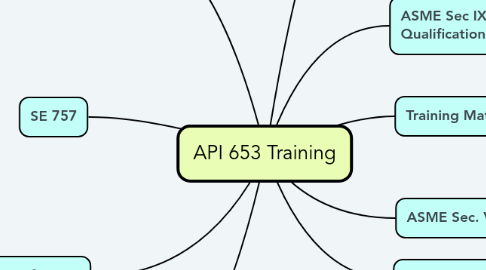
1. API 653
1.1. General Information
1.1.1. API 653 is referencing code/standard for In Service Tank
1.1.2. Normally revised 5 years
1.1.3. Become effective 6 months after date of publication
1.2. Arrangement of API 653 Section
1.2.1. 1. Scope
1.2.1.1. 1.1 API 653 can be used for Tank IN SERVICE, build to:
1.2.1.1.1. 1.1.1 This standard covers steel storage tanks built to API 650 and its predecessor API 12C. It provides minimum requirements for maintaining the integrity of such tanks after they have been placed in service and addresses inspection, repair, alteration, relocation, and reconstruction.
1.2.1.1.2. API 650
1.2.1.1.3. API 12C (Older version)
1.2.1.1.4. Any Tank Specification
1.2.1.1.5. 1.1.2 The scope is limited to the tank foundation, bottom, shell, structure, roof, attached appurtenances, and nozzles to the face of the first flange, first threaded joint, or first welding-end connection. Many of the design, welding, examination, and material requirements of API 650 can be applied in the maintenance inspection, rating, repair, and alteration of in-service tanks. In the case of apparent conflicts between the requirements of this standard and API 650 or its predecessor API 12C, this standard shall govern for tanks that have been placed in service.
1.2.1.1.6. 1.1.3 This standard employs the principles of API 650; however, storage tank owner/operators, based on consideration of specific construction and operating details, may apply this standard to any steel tank constructed in accordance with a tank specification.
1.2.1.2. 1.3 In Case of Conflict between
1.2.1.2.1. 1.3 Jurisdiction
1.2.1.2.2. API 653 and API 650
1.2.1.2.3. API 653 and regulation
1.2.1.3. API 653 recognizes following technical concepts
1.2.1.3.1. Risk Based Inspection
1.2.1.3.2. FFS- Fitness for Service
1.2.2. 3. Definition
1.2.2.1. 3.1 Alteration or repair
1.2.2.1.1. Alteration
1.2.2.1.2. Repair
1.2.2.2. 3.2 As Build Standard
1.2.2.2.1. The standard (such as API standard or UL 6 standard) used for the construction of the tank component in question. If this standard is not known, the as-built standard is the standard that was in effect at the date of the installation of the component. If the date of the installation of the component is unknown, then the current applicable standard shall be considered to be the as-built standard. See Annex A for a list of API welded storage tank standards. The standard used for repairs or alterations made after original construction is the as-built standard only for those repairs or alterations, so there may be more than one as-built standard for a tank.
1.2.2.3. 3.4 authorized inspector
1.2.2.3.1. An employee of an authorized inspection agency who is qualified and certified to perform inspections under this inspection standard. Whenever the term inspector is used in API 653, it refers to an authorized API Standard 653 inspector
1.2.2.3.2. Annex D Authorized Inspector Certification
1.2.2.4. 3.5 Break Over Point
1.2.2.5. 3.9 Corrosion Rate
1.2.2.5.1. Metal loss per unit time (year)
1.2.2.5.2. (mm/year, inch/year, mil/year(mpy)
1.2.2.6. 3.10 Critical Zone
1.2.2.6.1. The portion of the tank bottom or annular plate within 3 in. of the inside edge of the shell, measured radially inward.
1.2.2.6.2. Bottom or Annular Plate
1.2.2.7. 3.14 External Inspection
1.2.2.7.1. Inspection performed while Tank is In Service
1.2.3. 4. Suitability for Service
1.2.3.1. Damage Mechanism
1.2.3.1.1. Thinning (Corrosion)/(Metal Loss)
1.2.3.1.2. Crack (Stress Corrosion Crack/SCC) (Environment + Stress)
1.2.3.1.3. Mechanical (Over pressure, Cyclic Stress)
1.2.3.1.4. Metallurgical (Phase Transformation)
1.2.3.2. 4.1 General
1.2.3.2.1. 4.1.1 When the results of a tank inspection show that a change has occurred from the original physical condition of that tank, an evaluation shall be made to determine its suitability for continued use.
1.2.3.3. 4.2 Roof
1.2.3.3.1. 4.2.1.1 The structural integrity of the roof and roof support system shall be verified.
1.2.3.3.2. 4.2.1.2 Roof plates corroded to an average thickness of less than 0.09 in. (2.25mm) in any 100 in.2 area or
1.2.3.3.3. roof plates with any holes through the roof plate shall be repaired or replaced.
1.2.3.4. 4.3 Shell
1.2.3.4.1. 4.3.1 Corrosion
1.2.3.4.2. 4.3.2 Thickness Averaging Method for an Localized Thin Area (LTA)
1.2.3.4.3. 4.3.3 Minimum Thickness Calculation for Welded Tank Shell
1.2.3.4.4. 4.3.4 Minimum Thickness Calculation for Riveted Tank Shell
1.2.3.4.5. 4.3.6 Flaws Flaws such as cracks or laminations shall be thoroughly examined and evaluated to determine their nature and extent and need for repair. If a repair is needed, a repair procedure shall be developed and implemented. The requirement for repairing scars such as arc strikes, gouges, or tears from temporary attachment welds must be evaluated on a case-by-case basis. Cracks in the shell-to-bottom weld shall be removed.
1.2.3.5. 4.4 Tank Bottom Evaluation
1.2.3.5.1. Bottom Plate
1.2.3.5.2. Annular Bottom Plate
1.2.3.5.3. Critical Zone
1.2.3.6. Appendix B - Settlement
1.2.3.6.1. General
1.2.3.6.2. B.2.1 Settlement Measurements
1.2.3.6.3. B.3 Determination of Acceptable Settlement
1.2.4. 5. Brittle Fracture Considerations
1.2.4.1. 5.2 Basic Considerations
1.2.4.1.1. 5.2.1 A decision tree (see Figure 5.1) is used to present the assessment procedure for failure due to brittle fracture. The decision tree is based on the following principles.
1.2.4.2. Any change to severe service from existing tank requires evaluation of brittle fructure
1.2.4.2.1. Changin to higher specific gravity
1.2.4.2.2. Lowering temperature
1.2.4.3. Hydrostatic test shiws fitness for brittle fracture not to occur
1.2.4.4. A flow chart (fig 5.1) is used to take waiver from hydrotest if tank service is changed to more severe service
1.2.4.5. If all requirements of fig 5.1 are not met then for service change to more severe service will require :
1.2.4.5.1. Hydrotest, or
1.2.4.5.2. Rerating
1.2.5. 6. Inspection
1.2.5.1. 6.1 General
1.2.5.1.1. Periodic in-service inspection of tanks shall be performed as defined herein. The purpose of this inspection is to assure continued tank integrity. Inspections, other than those defined in 6.3 shall be directed by an authorized inspector.
1.2.5.2. Type of Inspection
1.2.5.2.1. 6.3 External Inspections
1.2.5.2.2. 6.4 Internal Inspection
1.2.5.2.3. API 575
1.2.5.2.4. Risk Based Inspection (RBI)
1.2.6. 7. Materials
1.2.6.1. 7.1 General This section provides general requirements for the selection of materials for the repair, alteration, and reconstruction of existing tanks. Specific requirements for repairs and alterations are covered in Section 9.
1.2.6.2. 7.2 New Materials All new materials used for repair, alterations, or reconstruction shall conform to the current applicable standard.
1.2.6.3. For reconstructed tank- shell plates and bottom plates welded to shell must be identified
1.2.6.3.1. Identified Material
1.2.6.3.2. Un identified material, perform :
1.2.7. 8. Design Consideration for Reconstructed Tanks
1.2.7.1. 8.2 New Weld Joints
1.2.7.2. 8.2.1 Weld joint details shall meet the welding requirements of the current applicable standard.
1.2.7.3. 8.2.2 All new shell joints shall be butt-welded joints with complete penetration and complete fusion.
1.2.7.4. 8.3 Existing Weld Joints Existing weld joints shall meet the requirements of the as-built standard.
1.2.7.5. 8.4 Shell Design
1.2.7.5.1. 8.4.1 Thickness to be used for each shell course when checking tank design shall be based on measurements taken within 180 days prior to relocation. (See 4.3.2 for measuring procedure, number, and locations of measured thicknesses.)
1.2.7.5.2. 8.4.2 The maximum design liquid level for product shall be determined by calculating the maximum design liquid level for each shell course based on the specific gravity of the product, the actual thickness measured for each shell course, the allowable stress for the material in each course, and the design method to be used.
1.2.7.5.3. 8.4.3 The maximum liquid level for hydrostatic test shall be determined by using the actual thickness measured for each shell course, the allowable stress for the material in each course, and the design method to be used.
1.2.7.5.4. 8.4.4 If a corrosion allowance is required for the reconstructed tank, the required corrosion allowance shall be deducted from the actual thickness before calculating the maximum liquid level. If the actual thickness is greater than that necessary to allow the liquid level required, the extra thickness can be considered as corrosion allowance.
1.2.7.6. 8.5 Shell Penetrations
1.2.7.6.1. 8.5.1 Replacement and new penetrations shall be designed, detailed, welded, and examined to meet the requirements of the current applicable standard.
1.2.7.6.2. 8.5.2 Existing penetrations shall be evaluated for compliance with the as-built standard
1.2.8. 9. Tank repair and Alteration
1.2.8.1. 9.1 General
1.2.8.1.1. 9.1.3 All repair work must be authorized by the authorized inspector or an engineer experienced in storage tank design, before commencement of the work by a repair organization. Authorization for alterations to storage tanks that comply with API 650 may not be given without prior consultation with, and approved by, an engineer experienced in storage tank design. The authorized inspector will designate inspection hold points required during the repair or alteration sequence and minimum documentation to be submitted upon job completion. The authorized inspector may give prior general authorization for limited or routine repairs as long as the authorized inspector is sure that the repairs will not require hydrostatic testing or do not require an engineering evaluation.
1.2.8.1.2. 9.1.4 All proposed design, work execution, materials, welding procedures, examination, and testing methods must be approved by the authorized inspector or by an engineer experienced in storage tank design. The authorized inspector or an engineer experienced in storage tank design shall approve all specified repair and alteration work at the designated hold points and after repairs and alterations have been completed in accordance with the requirements of this standard.
1.2.8.2. Type of Repair
1.2.8.2.1. Shell Repair (Permanent Repair)
1.2.8.2.2. 9.10 Bottom repair (Permanent Repair)
1.2.8.2.3. 9.14 Hot Taps
1.2.9. 10. Dismantling and Reconstruction
1.2.9.1. A. Reconstruction
1.2.9.1.1. Authorization
1.2.9.1.2. Approval
1.2.9.2. B. Compare dimensional Tolerance for Construction and Reconstruction
1.2.9.2.1. Tolerance
1.2.9.2.2. Plumbness
1.2.9.2.3. Roundness
1.2.9.2.4. Deviation
1.2.10. 11. Welding
1.2.10.1. 11.1 Welding Qualifications for repair/Alteration/Reconstruction per
1.2.10.1.1. ASME Sec IX
1.2.10.1.2. API 650 Sec. 9
1.2.10.1.3. API 653 Sec. 11
1.2.10.2. 11.2 Identification and records
1.2.10.2.1. API 650 Sec 9
1.2.10.3. 11.3 Alternatives to Post-weld Heat Treatment (PWHT)
1.2.10.3.1. Preheating
1.2.10.3.2. Controlled deposition welding
1.2.11. 12. Examination and Testing
1.2.11.1. 12.1 NDE
1.2.11.1.1. 12.1.1 General
1.2.11.1.2. 12.1.2 Shell Penetrations
1.2.11.1.3. 12.1.3 Examination of Repaired Weld Defects
1.2.11.1.4. 12.1.5 Shell Plate to Shell Plate Welds
1.2.11.2. 12.2 Radiographs
1.2.11.2.1. 12.2.1 Number and Location of Radiographs
1.2.11.3. 12.3 Hydrostatic Testing
1.2.11.3.1. 12.3.1 When Hydrostatic Testing is Required
1.2.11.3.2. 12.3.2 Hydrostatic Test Procedure
2. References
2.1. Code/ Standard
2.1.1. Shall be
2.1.2. May be
2.1.3. Has Legal Status
2.1.4. Standard developed by prime safety organization
2.1.5. Has Minimum Requirements to build an equipment
2.1.5.1. To Build = Construction
2.1.5.2. Right material
2.1.5.3. Right design
2.1.5.4. Right fabrication
2.1.5.5. Right Inspection, Examination and Testing
2.1.5.5.1. Inspection
2.1.5.5.2. Examination
2.1.5.5.3. Testing
2.2. Recommended Practice
2.2.1. Should be
2.2.2. Standard compliment
2.2.3. Good Engineering practices used in Industry
2.3. Specification
2.3.1. May be
2.3.2. Document addressing Specific Requirements, which may be over & above Code or standars
3. SE 757
4. Online Exam Certification
4.1. Method
4.1.1. Open Book
4.1.1.1. 3.45 Hours (60 Question)
4.1.1.1.1. After noon
4.1.2. Close Book
4.1.2.1. 2.45 Hours (110 Question)
4.1.2.1.1. Morning
4.1.3. Multiple Choice (170 Question)
4.1.3.1. In Person (Prometric Center)
4.1.3.2. Remote (at Home)
4.2. Document
4.2.1. API 653 (Standard)
4.2.1.1. 50%
4.2.2. API RP 575 (Recommended Practice)
4.2.2.1. 6-8%
4.2.3. API RP 571
4.2.3.1. 6-8%
4.2.4. API 650
4.2.4.1. 8-10%
4.2.5. API RP 651
4.2.5.1. 3-4%
4.2.6. API RP 652
4.2.6.1. 3-4%
4.2.7. API RP 576
4.2.7.1. 2-3%
4.2.8. API RP 577
4.2.8.1. 4-5%
4.2.9. ASME Sec. IX
4.2.9.1. 4-5%
4.2.10. ASME Sec. V
4.2.10.1. 4-5%
4.3. Grading
4.3.1. 170 Questions
4.3.1.1. 140 Questions Grade on Test
4.3.1.2. 30 Questions Pre Test
4.3.1.3. Question Type
4.3.1.3.1. Sngle Choice
4.3.1.3.2. Alternative Item
4.3.2. Passing Grade min. 80%
4.3.2.1. 112 Questions or more
5. API 650-Welded Tank for Oil Storage
5.1. 1. Referencing Code/Standard for Construction
5.2. 2. Normally Revised every 5 years
5.3. 3. Becomes effective (Mandatory) 6 months after date of Publication
5.4. 4. Arrangement of API 650 Section
5.4.1. 1. Scope
5.4.1.1. 1. Applies to Above Ground Storage Tank Which are:
5.4.1.1.1. a. Vertical
5.4.1.1.2. b. Cylindrical
5.4.1.1.3. c. Welded
5.4.1.1.4. d. Closed and Open Top
5.4.1.1.5. e. Fully supported bottom
5.4.1.1.6. f. Non refrigerated
5.4.1.2. 2. Applied to Atmospheric (Gage Pressure = 0 psi) or Use Annexure "F" for pressure
5.4.1.2.1. Permitted internal pressure is equal OR less than 2.5 psi
5.4.1.2.2. For greater than 2.5 psi to 15 psi, follow API 620
5.4.1.3. 3. Applied to temperature max. 93 degree CELCIUS or 200 FAHRENHAIT
5.4.1.3.1. Use Annex "M" if temperature design greater than 93C (200F) to 260 C (500F)
5.4.1.4. Limitation
5.4.1.4.1. 1.2 Limitations, The rules of this standard are not applicable beyond the following limits of piping connected internally or externally to the roof, shell, or bottom of tanks constructed according to this standard:
5.4.1.5. Notes
5.4.1.5.1. NOTE (•) A bullet, at the beginning of a paragraph indicates that there is an expressed decision or action required of the Purchaser. The Purchaser’s responsibility is not limited to these decisions or actions alone. When such decisions and actions are taken, they are to be specified in documents such as requisitions, change orders, data sheets, and drawings.
5.4.1.5.2. The designation “Normative” shall be understood to mean mandatory. The designation “informative” shall be understood to mean non-mandatory (i.e. informational data, recommendations, suggestions, commentary, samples, and examples).
5.4.2. 2. Normative References
5.4.2.1. The designation “Normative” shall be understood to mean mandatory. The designation “informative” shall be understood to mean non-mandatory (i.e. informational data, recommendations, suggestions, commentary, samples, and examples).
5.4.3. 3. Definitions
5.4.3.1. Bottom
5.4.3.1.1. Bottom Plate
5.4.3.1.2. Annular Bottom Plate
5.4.3.2. Center Line Stacked
5.4.3.2.1. 3.3 centerline-stacked The mid-thickness centerlines of plates in all shell courses coincide.
5.4.3.3. Thickness
5.4.3.3.1. Corroded Thickness
5.4.3.3.2. Design
5.4.3.3.3. Nominal (t Nom)
5.4.3.4. Welder
5.4.3.4.1. 3.31.20 welder One who performs manual or semiautomatic welding.
5.4.3.4.2. 3.31.21 welding operator One who operates automatic or machine welding equipment.
5.4.4. 4. Materials
5.4.4.1. 4.1.2 Materials used in the construction of tanks shall conform to the specifications listed in this section, subject to the modifications and limitations indicated in this standard. Material produced to specifications other than those listed in this section may be employed, provided that the material is certified to meet all of the requirements of an applicable material specification listed in this standard and the material’s use is approved by the Purchaser.
5.4.4.2. 4.1.2. Material approved by API 650 - Plate (Within Thickness Limitation)
5.4.4.2.1. 4.2.2. ASTM (American)
5.4.4.2.2. 4.2.3. CSA ( Canadian)
5.4.4.2.3. 4.2.4. ISO
5.4.4.2.4. 4.2.5. EN (European)
5.4.4.2.5. 4.2.6. National Standards
5.4.4.3. 4.2.1.4 Shell Plate Thickness
5.4.4.3.1. 4.2.1.4 Shell plates are limited to a maximum thickness of 45 mm (1.75 in.) unless a lesser thickness is stated in this standard or in the plate specification. Plates used as thickened inserts or flanges may be thicker than 45 mm (1.75 in.).
5.4.4.3.2. LESS than or EQUAL to 45mm (1.75")
5.4.4.4. 4.2.10.1 Plates
5.4.4.4.1. 4.2.1.2.3 Whether an edge-thickness or a weight basis is used, an underrun not more than 0.3 mm (0.01 in.) from the computed design thickness or the minimum permitted thickness is acceptable.
5.4.4.4.2. Plates, as designated in 4.2.10.1 and thicker than 40 mm (1.5 in.), shall be normalized or quench tempered, killed, made to fine-grain practice, and impact tested.
5.4.4.4.3. Plates MUST BE GREATER than or EQUAL to 40mm, and greater than or equal to 45mm (>/= 40mm </= 45mm) MUST BE:
5.4.4.4.4. Mill undertolerance </= 0.3mm (0.01") from design thickness
5.4.4.5. 4.2.9 Impact Test
5.4.4.5.1. Why required this?
5.4.4.5.2. Impact Test Excemption
5.4.4.5.3. Impact Test Requirements and Acceptence
5.4.4.6. 4.2.10 Toughness Requirements
5.4.5. 5. Design
5.4.6. 6. Fabrication
5.4.6.1. 6.1.3 Shaping of Shell Plates Figure 6.1 provides criteria for shaping of plates to the curvature of the tank prior to installation in the tank. Shaping of plates concurrently with installation in the tank shell is permitted if the tank diameter exceeds the limit in Figure 6.1 or if the Manufacturer’s alternate procedure for any diameter has been accepted by the Purchaser.
5.4.6.1.1. Figure 6.1 Tells us whether shaping of shell plates
5.4.6.2. 6.2.4.a The Manufacturer shall visually inspect all edges of shell and roof plates before installing the plates in the tank or before inserting a nozzle into the plate to determine if laminations are present. If a lamination is visually detected, the Manufacturer shall ultrasonically examine the area to determine the extent of the laminations and shall reject the plate or make repairs in accordance with 6.2.4b.
5.4.6.3. 6.2.4.b For laminations found not exceeding 75 mm (3 in.) in length or 25 mm (1 in.) in depth, repairs may be made by edge gouging and rewelding to seal the lamination.
5.4.7. 7. Erection and Assembly
5.4.7.1. 7.2 Detail of Welding
5.4.7.1.1. 7.2.1 General
5.4.7.1.2. 7.2.2 Bottoms
5.4.7.1.3. 7.2.3 Shells
5.4.7.1.4. 7.2.4 Bottom to Shell
5.4.7.2. 7.3 Examination, Inspection, and Repairs
5.4.7.2.1. Component
5.4.7.3. 7.5 Dimensional Tolerance
5.4.7.3.1. 7.5.2 Plumbness
5.4.7.3.2. 7.5.3 Out of Roundness
5.4.7.3.3. 7.5.4 Local Deviation
5.4.8. 8. Examination
5.4.8.1. Examination Method
5.4.8.1.1. Surface
5.4.8.1.2. Volumetric
5.4.8.1.3. Leak Test
5.4.8.1.4. 8.1.2 Number and Location of Radiographs
5.4.8.2. ASME Sec V Reference
5.4.8.2.1. Article 9
5.4.8.2.2. Article 6
5.4.8.2.3. Article 7
5.4.8.2.4. Article 2
5.4.8.2.5. Article 4, 5
5.4.8.2.6. Article
5.4.8.3. Close Book Exam
5.4.9. 9. Welding Qualifications
5.4.9.1. 9. Welding Qualification
5.4.9.2. 1. Welding qualification is responsibility of manufacturer, fabricator, erector
5.4.9.3. 2. Welding Qualifications are done as per ASME Sec IX
5.4.9.4. 3. All Tank Materials in API 650 are considered PNo1
5.4.9.4.1. Gr. No. 1
5.4.9.4.2. Gr. No. 2
5.4.9.4.3. Gr. No. 3
5.4.9.5. 4. Welding joints (Except roof) must have song form of identification. WHich is tracable, welder ID must be included
5.4.9.5.1. Weld Map, or
5.4.9.5.2. Hard stamping every 3 ft or 1m
5.4.10. 10. Marking (Name Plate)
6. Training Materials
6.1. Differences between design code & Inservice code
6.1.1. Construction Code/Standards
6.1.1.1. Fit for purposed
6.1.1.2. 1. Meant for new Equipment
6.1.1.3. 2. Equipment is designed for service requirement, but not actually exposed to service requirements
6.1.2. InService Code/Standard
6.1.2.1. In Service means
6.1.2.1.1. Type of Damage (What)
6.1.2.1.2. Installed and Commisioned
6.1.2.1.3. In Operation or not in Operation
6.1.2.2. Fit for Continued Use
6.1.2.3. 1. Meant for equipment placed In Service
6.1.2.4. 2. Equipment is exposed to actual service requirements
6.1.2.5. 3. InService code/standard address
6.1.2.5.1. Location of damage (Where)
6.1.2.5.2. Method to find damage (How)
6.1.2.5.3. Interval/frequency (When)
6.1.2.6. 4. "3R" Decision are taken based on Inspection/NDE
6.1.2.6.1. REPAIR and RUN for next inspection Interval
6.1.2.6.2. RERATE or RETIRE or REPLACE
7. ASME Sec IX Welding Qualifications
7.1. 1. References Code/Standard For welding Qualification
7.1.1. Procedure (Properties)
7.1.2. Performance (Skill)
7.2. 2. Revised every 2 years
7.3. 3. All Clause of welding start with QW
7.3.1. Q= Qualification
7.3.2. W= Welding
7.4. 4. Section Arrangement
7.4.1. Clause QW-1xx
7.4.1.1. Article I
7.4.1.1.1. General Requirements
7.4.2. Clause QW-2xx
7.4.2.1. Article II
7.4.2.1.1. WELDING PROCEDURE QUALIFICATIONS
7.4.3. Clause QW-3xx
7.4.3.1. Article III
7.4.3.1.1. Welding Qualification
7.4.4. Clause QW-4xx
7.4.4.1. Article IV
7.4.4.1.1. Welding Procedure Specification
7.4.5. Clause QW-5xx
7.4.5.1. Article V
7.4.5.1.1. Procedure Qualification Record
8. ASME Sec. V
8.1. Radiography Sensitivity
8.1.1. Contrast (Defective Surrounding)
8.1.1.1. FIlm Density
8.1.1.1.1. X-Ray
8.1.1.1.2. Gamma Ray
8.1.1.2. Densitometer measure density, Calibrate every 3 months
8.1.2. Definition (Sharpness of Image)
8.1.2.1. T-233.1 Image Quality Indicator (IQI)
8.1.2.2. Table T233.2 Wire Type
8.1.2.2.1. Set A= 1 to 6
8.1.2.2.2. Set B= 6 to 11
8.1.2.2.3. Set C= 11 to 16
8.1.2.2.4. Set D= 16 to 21
8.1.2.3. Selection of IQL - Follow T276 and Table T276
9. SE 797 Thickness Measurement
9.1. 1. Basic Principle - Pulse - Echo
9.1.1. Distance = Velocity x transit time (t)
9.1.2. 2T= V x t
9.1.3. T= V x (t/2)
9.2. 2. High Temperature Measurement
9.2.1. 9.5 Rule of Thumb,
9.2.1.1. For every 100F (55C) Rise, there is positive error of 1%