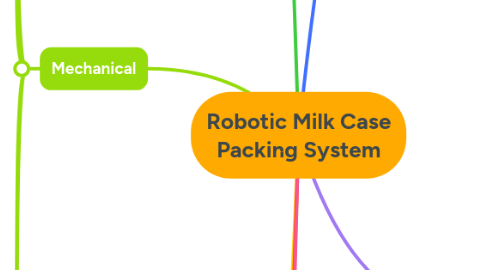
1. Overview
1.1. Motivation
1.1.1. Trend in robotics, reducing labor costs, high scalability and space utilization
1.1.2. Compare with traditional system
1.1.2.1. Traditional system
1.1.2.1.1. High speed
1.1.2.1.2. Lower initial cost
1.1.2.1.3. Require a larger space
1.1.2.1.4. Low flexibility
1.1.2.1.5. Complex maintenance
1.1.2.2. Robotic system
1.1.2.2.1. High flexibility
1.1.2.2.2. High scalability
1.1.2.2.3. More compact
1.1.2.2.4. High maintenance capability due to less mechanical parts
1.1.2.2.5. Higher initial cost
1.2. Current market review
1.2.1. Cobot https://www.youtube.com/watch?v=-CESiuu7CYs
1.2.2. Delta robot https://www.brentonengineering.com/products/rc1000-robotic-top-load-case-packer/
1.2.3. 6-axis robot https://www.edson.com/products/4000-tl-robotic-top-load-case-packer/
1.3. Requirements
2. Mechanical
2.1. Robot
2.1.1. Selection
2.1.1.1. Productivity
2.1.1.2. Load
2.1.1.3. Space
2.1.1.3.1. Base space
2.1.1.3.2. Operation space
2.1.1.4. Type
2.1.1.4.1. 6-axis robot
2.1.1.4.2. Delta robot
2.1.1.4.3. SCARA robot
2.1.2. Design the base for robot
2.2. Gripper
2.2.1. Drive design
2.2.1.1. Pneumatic
2.2.1.2. Electric
2.2.1.3. Hydraulic
2.2.2. Selection
2.2.2.1. Impactive
2.2.2.1.1. Non-penetrating
2.2.2.1.2. Penetrating
2.2.2.2. Ingressive
2.2.2.2.1. Non-penetrating
2.2.2.2.2. Penetrating
2.2.2.3. Contigutive
2.2.2.3.1. Non-penetrating
2.2.2.3.2. Penetrating
2.2.2.4. Astrictive
2.2.2.4.1. Non-penetrating
2.2.2.4.2. Penetrating
2.2.3. Calculation
2.2.3.1. Effects of the products
2.2.3.1.1. Product shape
2.2.3.1.2. Product size
2.2.3.1.3. Product mass
2.2.3.1.4. Product position
2.2.3.2. Technological requirements
2.2.3.2.1. Prehension time
2.2.3.2.2. Gripping path
2.2.4. Detail design
2.3. Conveyor
2.3.1. Selection
2.3.1.1. Belt conveyor
2.3.1.1.1. Least expensive
2.3.1.1.2. Utilize few power units
2.3.1.2. Roller conveyor
2.3.1.2.1. Belt driven
2.3.1.2.2. Chain driven
2.3.1.3. Slat conveyor
2.3.1.3.1. Loads are dirty, oily or wet
2.3.1.4. Line-shaft conveyor
2.3.1.4.1. Give more clearance when elevating
2.3.2. Drive design
2.3.2.1. Motor selection
2.3.2.1.1. Load
2.3.2.1.2. Speed
2.3.2.2. Drive selection
2.3.2.2.1. Gear
2.3.2.2.2. Belt
2.3.2.2.3. Chain
2.3.3. Detail design
2.3.4. Unit stopping and aligning
2.4. Drawings
3. Electrical
3.1. Sensors
3.1.1. Detection sensors
3.2. Electrical device
3.2.1. Relay
3.3. Controller
3.3.1. Calculate the number of I/O
3.4. Power supply
3.5. Safety control
3.6. Drawings
4. Control
4.1. Path planning for the robot
4.1.1. Optimized path
4.1.2. Avoid collision
4.2. PLC programming
5. Simulation
5.1. Build 3D models and their physics properties
5.2. Create I/O signals and connect to PLC program
5.3. Collision testing
5.4. Performance testing
5.4.1. Duration
5.4.2. Accuracy
5.5. Build an electrical cabinet
6. Testing and evaluation
6.1. Test the system with various scenarios
6.1.1. Different milk box sizes
6.1.2. Position of products on conveyors
6.2. Evaluate the efficiency, accuracy and stability of the system
7. Aim
7.1. Design and develop a robotic pick and place system for packing the milk into carton box.
7.2. Ensure the precision, accuracy and speed
7.3. Evaluate and optimize the efficiency, stability and safety by simulating the system using NX MCD
7.4. Flexibility
8. Outcomes
8.1. Excellent
8.1.1. Successfully design the gripper and conveyor
8.1.2. The whole system is able to meet the basic requirements in the virtual environment
8.1.3. The system can adapt to a large variation of products size
8.1.4. The system have great robustness
8.1.5. The system's accuracy and precision is 99%
8.1.6. Build an electrical cabinet to perform hardware in the loop
8.2. Good
8.2.1. Successfully design the gripper and conveyor
8.2.2. The whole system is able to meet the basic requirements in the virtual environment
8.2.3. The system can pick a certain type of milk box
8.2.4. The system have great robustness
8.2.5. The system's accuracy and precision is 99%
8.3. Average
8.3.1. Successfully design the gripper and conveyor
8.3.2. Design a robot station
8.3.3. The whole system is able to meet the basic requirements in the virtual environment