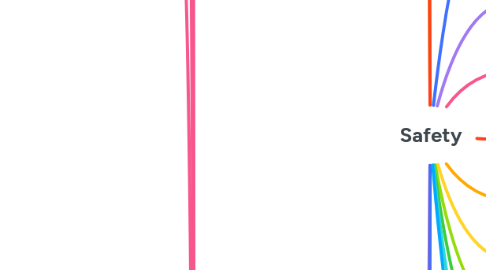
1. SHELL model
1.1. Liveware-Hardware
1.2. Liveware-Software
1.3. Liveware-Liveware
1.4. Liveware-Environment
2. Error & violations
2.1. slips & lapses
2.1.1. fail to execute vs fail to memorise
2.2. mistakes
2.2.1. fail to plan & act
2.3. safety strategies
2.3.1. reduction
2.3.2. capturing
2.3.3. tolerance
2.4. violations
2.4.1. situational
2.4.2. routine
2.4.3. organisationally induced
3. cultural components
3.1. organisational
3.2. national
3.3. professional
4. management dilemma
4.1. protection (safety)
4.1.1. safety management
4.2. production (efficiency)
4.2.1. financial management
5. What is SMS?
5.1. decision-making, processes, and risk
5.1.1. safety risk
5.1.2. hazard
5.2. processes
5.2.1. hazard identification
5.2.1.1. hazard vs consequence
5.2.1.1.1. hazard identification methods
5.2.2. safety reporting
5.2.3. risk management
5.2.4. performance measurement
5.2.5. safety assurance
5.3. QMS vs SMS
5.3.1. tools
5.3.1.1. KPIs
5.4. starting point
5.4.1. annex dedicated to safety management responsibilities and processes
5.5. ICAO
5.5.1. safety management function related to or in direct support of safe operation or aircraft
5.5.2. recommended SMS complying w/ SSP
5.6. SMS framework
5.6.1. safety policies
5.6.1.1. Management commitment & responsibility
5.6.1.1.1. safety policy & objectives.
5.6.1.1.2. Safety policy demonstrates senior management commitment.
5.6.1.1.3. Outlines safety goals and organizational structure.
5.6.1.1.4. Aims for effective safety management.
5.6.1.1.5. Management commitment and safety leadership is key to the implementation of an effective SMS.
5.6.1.2. safety accountibilities
5.6.1.3. appointment of key safety personnel
5.6.1.4. coordination of emergency response planning
5.6.1.5. SMS documentation
5.6.1.6. Safety policies
5.6.1.6.1. Demonstrates senior management's dedication to ongoing safety improvement
5.6.1.6.2. Commits to safety performance through SMS
5.6.1.6.3. Establishes transparent safety objectives and commitment
5.6.1.6.4. Specifies methods, processes, and organizational structure to attain safety goals
5.6.1.6.5. Ensures thorough documentation of policy and processes
5.6.1.6.6. Implements an employee reporting and resolution system
5.6.1.6.7. Enforces accountability for both management and employees
5.6.1.6.8. Enhances existing processes and procedures
5.6.1.6.9. Promotes cross-organizational communication and cooperation
5.6.2. safety risk management
5.6.2.1. hazard identification
5.6.2.2. safety risk assessment and mitigation
5.6.3. safety assurance
5.6.3.1. safety performance monitoring & measurement
5.6.3.2. Management of change
5.6.3.2.1. criticality of systems and activities
5.6.3.2.2. stability of systems & operational environment
5.6.3.2.3. past performance
5.6.3.3. continuous improvement of SMS & audit
5.6.4. safety promotion
5.6.4.1. training education
5.6.4.2. safety coomunication
5.6.5. All about safety decision-making throughout the organisation
5.7. failures to achieve SMS
5.7.1. poor reporting culture
5.7.1.1. safety culture
5.7.1.1.1. good safety policy
5.7.1.1.2. effective safety promotion
5.7.1.1.3. robust reporting systems
5.7.1.1.4. refers to organisation's shared values, beliefs, attitudes, practices related to safety
5.7.2. data-rich, information-poor
5.7.3. lack of measurable SPIs
5.7.3.1. SPI
5.7.3.1.1. quantifiable metrics to assess and measure safety performance
5.7.3.1.2. organisation can track safety performance over time
5.7.3.1.3. set clear improvement targets
5.7.3.1.4. make informed decisions about based data
5.8. SMS for airlines
5.8.1. safety risk mitigation is reduced if best thought-out allocation is appropriated
5.8.2. Performance & Compliance
5.8.2.1. quality & safety management systems
5.8.2.1.1. provides assurance across the industry
5.8.2.2. Compliance
5.8.2.2.1. Work as planned
5.8.2.3. Performance
5.8.2.3.1. work as executed
5.8.3. The realities
5.8.3.1. Commercial aviation is a highly regulated industry.
5.8.3.2. Operations often deviate from regulations.
5.8.3.3. Main challenge: Balancing and allocating resources effectively.
5.8.4. Value of SMS
5.8.4.1. Profitability is a key objective for all businesses.
5.8.4.2. SMS & safety actions should be approached like any other business decision.
5.8.4.3. Challenges
5.8.4.3.1. Traditional cost-benefit analysis
5.8.4.3.2. Cost-benefit analysis for SMS
5.8.4.4. Considerations regarding costs
5.8.4.4.1. Maximize use of current systems and processes to cut implementation costs
5.8.4.4.2. Utilize internal knowledge when selecting roles for SMS support
5.8.4.4.3. Include both direct and indirect SMS costs in organizational overhead for investment calculations
5.8.4.5. Considerations regarding benefits
5.8.4.5.1. Safety management investments offer direct and indirect advantages for organizational productivity
5.8.4.5.2. Investing in safety is a wise business decision, even without accidents.
5.8.4.5.3. QMS simplifies cost-benefit analysis
5.8.5. Safety policy
5.8.5.1. Commits
5.8.5.1.1. senior management to continual safety improvement.
5.8.5.2. Ensures
5.8.5.2.1. transparency, documentation, and employee involvement.
5.8.5.3. Defines
5.8.5.3.1. methods, processes, and structures for safety goals.
5.8.6. Safety Manager Role
5.8.6.1. Crucial for effective SMS implementation.
5.8.6.2. Focuses on function rather than individual title.
5.8.7. Development of SMS Manual
5.8.7.1. Essential documentation describing SMS policies and procedures
5.8.8. Emergency Response Plan (ERP)
5.8.8.1. Part of SMS for specific service providers.
5.8.8.2. Not explicitly mandated by Annex 19 but aids in ERP development.
5.8.9. Safety Risk Management
5.8.9.1. Basics
5.8.9.1.1. Balances evidence-based resource allocation.
5.8.9.1.2. Risk is about choice, not luck.
5.8.9.1.3. Involves direction, supervision, and control.
5.8.9.2. Importance
5.8.9.2.1. Ensures airline viability and contributes to enterprise risk management.
5.8.9.3. Under SMS
5.8.9.3.1. Involves setting targets, collecting data, and allocating resources.
5.8.9.3.2. Decisions involve technical evaluation and financial/administrative considerations.
5.8.9.4. SMS system
5.8.9.4.1. Input
5.8.9.4.2. Cycle
5.8.9.4.3. Output
5.8.9.4.4. Safety programs
5.8.9.5. Baseline Concepts
5.8.9.5.1. Defines
5.8.9.5.2. Identifies
5.8.10. Safety Assurance
5.8.10.1. Performance manangement
5.8.10.1.1. Safety programs maintain the loop between output and input.
5.8.10.1.2. Ensures states have their SSP manual.
5.8.10.2. Safety Performance Management (SPM)
5.8.10.2.1. Balances effectiveness and efficiency in safety interventions.
5.8.10.2.2. Defines
5.8.10.3. Identifying Action and Management of Change:
5.8.10.3.1. Evaluates safety risks before implementing operational changes.
5.8.10.3.2. Management of change principles apply to
5.8.11. Safety Promotion
5.8.11.1. Reporting
5.8.11.1.1. Encourages a reporting culture to mitigate practical drift.
5.8.11.1.2. Employee safety reporting feeds data into the SMS cycle.
5.8.11.2. Employee Safety Reporting Program Management
5.8.11.2.1. reporting
5.8.11.2.2. storage
5.8.11.2.3. AI-driven analysis
5.8.11.2.4. information exchange within the service provider ecosystem
6. Final MCQ
6.1. SMS IMPLEMENTATION PLANNING
6.1.1. Situation in Thailand
6.1.1.1. not clear
6.1.1.2. under process
6.1.1.3. CAAT
6.1.1.3.1. SMS implementation schedule & mandatory deadline
6.1.1.4. red flag
6.1.1.4.1. DCA owned the airport before
6.1.1.4.2. DCA owned 28 A/P
6.1.2. ICAO: International Civil Aviation Organization
6.1.2.1. sets international standards and regulations for aviation safety, security, efficiency, and regularity
6.1.2.1.1. Different states = different laws
6.1.2.2. Set up as United Nations (UN) specialized agency formed in 1947:
6.1.2.2.1. Represent aviation authorities of different countries in UN
6.1.3. IATA: International Air Transport Association
6.1.3.1. Represents the operator (airline)
6.1.3.2. 82% of total airline in the world
6.1.3.3. 1945
6.1.3.4. Presenting airline’s industry view on international convention
6.1.3.5. Ensure the simple and smooth cooperation's between airlines and national government (ICAO)
6.1.3.6. Core activities;
6.1.3.6.1. 1. Advocacy & Lobbying
6.1.3.6.2. 2. Standard setting & adoption for business simplicity
6.1.3.6.3. 3. Product & service
6.1.3.7. SSP
6.1.3.7.1. Must be AOC holder
6.1.3.7.2. Management system for
6.1.3.7.3. by state
6.1.3.7.4. Appropriate to the size & complexity of the state's civil aviation system
6.1.3.7.5. must have different document but same logic
6.1.3.7.6. As part of its SSP
6.2. Why different bodies approve implementation plan for different state and not ICAO
6.2.1. ICAO sets international standard and regulations
6.2.1.1. State Safety Program (SSP) is developed by each state to comply with the local law while also complying with ICAO SSP = ICAO + local law
6.2.1.1.1. Safety Management System must be developed under SSP
6.3. different operators = different safety policy = different SMS
6.3.1. no one-size-fit-all
6.3.2. not only self-operated
6.3.2.1. outsourced company is acceptable
6.3.2.1.1. as long as they qualified by the company SMS standard
6.4. Intro ABM
6.4.1. identifying the players: STAKEHOLDERS
6.4.1.1. Airport
6.4.1.1.1. AOT & DOA
6.4.1.2. Airlines
6.4.1.2.1. Passengers
6.4.1.2.2. Cargo
6.5. Australian Government: Civil Aviation Safety Authority
6.5.1. SMS implementation
6.5.1.1. historical events
6.5.1.1.1. 1988; the piper alpha disaster
6.5.1.1.2. 2010; deep water horizon oil spill
6.5.1.2. events of the incidents were similar
6.5.1.2.1. Coincidence of causation / failure of lessons learned
6.5.1.2.2. characterised by;
6.5.1.3. SMS is management system;
6.5.1.3.1. more process, not really product
6.5.1.3.2. SMS is a systematic approach to managing safety
6.6. Conclusion of wrap up
6.6.1. SMS implementation is not about product but process. ie. not about checking if pilot had enough sleep
6.6.1.1. about implementing management system to control why pilot did not have enough sleep, and still decided to fly
6.6.1.1.1. = afraid to report due to angry management
6.6.1.2. incident (risk) can be control & mitigate in the futute
6.6.2. Implementation = Embedding
6.6.2.1. embedding safety culture to AOC through 4 components
6.6.2.1.1. 1. Safety policy
6.6.2.1.2. 2. Safety risk management
6.6.2.1.3. 3. safety assurance
6.6.2.1.4. 4. safety promotion
6.6.2.2. CAAT approves after embedded safety culture into 4 components
6.7. Short version
6.7.1. Lifecycle
6.7.1.1. stages require you to
6.7.1.1.1. 1. identify where organisation is regarding the required SMS elements
6.7.1.1.2. 2. develop plan to meet SMS requirements
6.7.1.1.3. 3. lesson learned for
6.7.1.2. the starting point, will be different for all organisation
6.7.1.2.1. even if some level of safety management is already in place
6.7.2. in a picture
6.7.2.1. 1. implementation
6.7.2.1.1. gap analysis
6.7.2.1.2. implementation plan
6.7.2.2. 2. operating
6.7.2.2.1. evaluation (LSOE)
6.7.2.2.2. measuring performance
6.7.2.3. 3. continuous improvement
6.7.2.3.1. monitoring performance
6.7.2.3.2. lesson learned
6.7.3. Case study: airport in taiwan
6.7.3.1. safety management at international airport in taiwan w/ respect to ICAO's SMS standards
6.7.3.1.1. AKA gap analysis of Airport Safety using ICAO SMS perspective was born
6.7.3.2. taiwan is non-member of ICAO
6.7.3.2.1. UN considered taiwan to be apart of China
6.8. SMS guidebook example; embedding safety culture is key
6.8.1. Taiwan's
6.8.1.1. 1. Safety policy
6.8.1.1.1. 1. air traffic controller
6.8.1.1.2. 2. ground services company
6.8.1.1.3. management company places the responsibility of the SMS in; Flight operations department
6.8.1.2. 2. Safety Risk management
6.8.1.2.1. Airport
6.8.1.2.2. ATC
6.8.1.2.3. ground services operator
6.8.1.2.4. Reviewing reports & making decision
6.8.1.3. 3. Safety assurance
6.8.1.3.1. For ground services provider
6.8.1.3.2. For ATC (stakeholder)
6.8.1.3.3. For airport
6.8.1.4. 4. Safety promotion
6.8.1.4.1. promote safety to stakeholders, participants & employees
6.8.1.4.2. Ground services provider
6.8.1.4.3. ATC
6.8.1.4.4. Airport company's stakeholders
6.8.2. CAAT's
6.8.2.1. 1. Safety policy
6.8.2.1.1. the safety policy states the organisation's intentions, Management principles & commitment to continuous improvement in the aviation safety level
6.8.2.1.2. the safety policy should be appropriate to the size & complexity of the organisation
6.8.2.1.3. Safety accountability & key personnel
6.8.2.2. 2. Safety Risk management
6.8.2.2.1. heart of safety management is identifying hazards
6.8.2.2.2. process of hazard identification & risk assessment
6.8.2.3. 3. Safety assurance
6.8.2.3.1. how corrective action is recommended to prevent reoccurence
6.8.2.4. 4. Safety promotion
6.8.2.4.1. Promoting communication
6.8.2.4.2. CAAT checks whether SMS is embedded safety culture & announced or not
6.9. Case study 2
6.9.1. Emirates SMS
6.9.1.1. 1. safety policy
6.9.1.1.1. maintain a culture of safety at emirates
6.9.1.2. 2. safety management system
6.9.1.2.1. everyone is encouraged to identify hazards, intervene if appropriate & report
6.9.1.2.2. all our colleagues have access to the company online safety reporting system called SID
6.9.1.3. 3. Safety assurance (prevent reoccurance)
6.9.1.3.1. hazard identification
6.9.1.4. 4. Safety Promotion
6.9.1.4.1. company SMS manual is available on the company intranet, where all employees can access it
6.10. SMS Implementation: Long Version
6.10.1. 10 sequence / steps implementation by ICAO
6.10.1.1. Step 1: Planning preparation
6.10.1.1.1. conduct gap analysis
6.10.1.1.2. designate a safety manager
6.10.1.2. Step 2: Senior management's commitment to safety
6.10.1.2.1. endorses & support safety plans & program documents
6.10.1.2.2. if not endorsed = no resources to improve / support
6.10.1.2.3. senior management commitment by providing time / money / allocating appropriate resources
6.10.1.3. Step 3: Safety promotion
6.10.1.3.1. during SMS implementation
6.10.1.3.2. promoting safety
6.10.1.4. Step 4: Organisation
6.10.1.4.1. identify the stakeholders in safety roles
6.10.1.4.2. why? you need to develop an SMS organisational chart showing the reporting structure
6.10.1.5. Step 5: Hazard Identification
6.10.1.5.1. good safety culture
6.10.1.5.2. Errors & unsafe actions will remain hidden
6.10.1.5.3. Line Operations Safety Audits (LOSA)
6.10.1.5.4. Management must provide adequate resources to
6.10.1.6. Step 6: Safety risk management
6.10.1.6.1. if collecting data was effective, assessing risk & ranking will also be affective
6.10.1.6.2. focuses safety efforts on hazards posing greatest risks
6.10.1.6.3. assess all risks critically & rank them according to potential
6.10.1.7. Step 7: Safety investigation
6.10.1.7.1. create system that learns the safety investigation
6.10.1.7.2. safety lesson
6.10.1.7.3. key operational staff must be properly trained to conduct safety investigations
6.10.1.7.4. findings should be disseminated throughout organisation as safety lessons learned
6.10.1.8. Step 8: Safety analysis
6.10.1.8.1. analytical tools & up-to-date safety databases
6.10.1.8.2. Safety recommendations should be proposed to senior management
6.10.1.8.3. safety analysis system, safety database
6.10.1.9. Step 9: Safety information management
6.10.1.9.1. operating an SMS has potential to generate large amounts of data
6.10.1.9.2. appropriate technical support & equipment
6.10.1.9.3. Guarantee to regulator that data collected is protected
6.10.1.10. Step 10: Safety performance monitoring & measurement
6.10.1.10.1. feedback to help close the loop
6.10.1.10.2. feedback for continuous improvement of SMS
7. safety data collection & quality
7.1. validity
7.2. completeness
7.3. consistency
7.4. accessibility
7.5. timeliness
7.6. security
7.7. accuracy
8. safety data collection and analysis
8.1. management of safety information
8.1.1. data-driven
8.2. protection of safety data
9. what is safety?
9.1. controlled risks & error
9.2. reduced to, maintained at acceptable level through continuous process of hazard identification and risk management
9.3. SMS profiled frameworks for it to happen in a systematic way
10. evolution of thinking
10.1. technical
10.1.1. better technology
10.2. human
10.2.1. HF, CRM
10.3. organisational
10.3.1. quality assurance, QMS threat & error
10.4. system safety
10.4.1. SSP & SMS
11. safety indicators & performance monitoring
11.1. snapshot
12. safety risk
12.1. probability
12.2. risk severity
12.3. risk tolerability
13. Swiss-cheese
13.1. accidents involve successive breaches of multiple system defences
13.2. active failure
13.2.1. frontline personnel
13.3. latent conditions
13.3.1. exist before damaging outcome
13.3.2. perceived as harmful and will become evident once the system's defence is breached
14. organisational accidents
14.1. human/technical failure
14.1.1. stems from organisation
14.1.2. responsibility of management
14.2. individual > organisational
14.3. events occur due to more complex technology
14.3.1. products and innovations
14.3.1.1. radically altered relationship between human and automation
14.4. workplace conditions
14.4.1. efficiency of people
14.5. latent conditions
14.5.1. deficiencies of equipment
15. practical-drift
15.1. baseline-performance drifts away from its original design when the organisation processes and procedures cannot anticipate all situations that may arise in daily operations
15.1.1. a consequence of real life operations and changes in the operational and regulatory environment
15.1.2. the bigger the gap b/w the baseline performance & the operational performance = the bigger the risks to develop accidents
16. what is SSP?
16.1. Framework at national law and standards set by CAA of that country
16.2. compliance to guidelines of ICAO
16.3. SSP framework
16.3.1. safety policies & objectives
16.3.1.1. state safety legislative framework
16.3.1.2. state safety responsibilities & accountabilities
16.3.1.3. accidents & incidents
16.3.2. safety risk management
16.3.2.1. safety requirements for service provider's SMS
16.3.2.2. agreement on the service provider's safety performance
16.3.3. safety assurance
16.3.3.1. oversight
16.3.3.2. data collection, analysis, exchange
16.3.3.2.1. SPI
16.3.3.3. safety data-driven targeting of oversight of areas of greater concern or need
16.3.4. safety promotion
16.3.4.1. internal & external communication and dissemination of safety information
16.4. safety performance management
16.4.1. use of data and processes to mitigate risk and improve safety performance
16.5. gap analysis
16.5.1. identifies the difference b/w the current state of safety & the desired safety objectives
16.5.2. provides roadmap for achieving safety goals
16.5.3. allows for continuous improvement by addressing identified gaps & risk