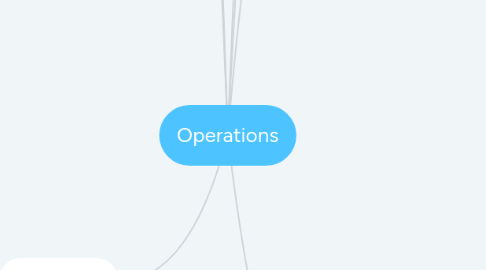
1. standarization
1.1. Standardization means producing maximum variety of products from the minimum variety of materials, parts, tools and processes.
2. service concept
2.1. The service concept outlines how a service provider can realize the value and desired outcomes of its services. The service concept can best be described as the way in which an organization would like to have its services perceived by its stakeholders
3. service blueprint
3.1. a service blueprint is a diagram that displays the entire process of service delivery, by listing all the activities that happen at each stage, performed by the different roles involved.
4. Improvement
4.1. Issue
4.1.1. management issue
4.1.1.1. Issues that often happen across the company, not just in one specific process Issues are dealt with on the strategic level, they need long term decisions Everything related to employee attitude, turnover, customer satisfaction
4.1.2. operational issue
4.1.2.1. In any kind of business, operational issues are any kind of problem that arises which can render a business less profitable.
4.2. Techniques
4.2.1. pareto chart
4.2.1.1. This is a basic tool that helps you identify the most frequent defects, complaints, or any other factor you can count and categorize. Mainly used to answer questions that focus on the 80%-20% percentage and you mainly focus on the 80%.
4.2.2. cause - effect diagram
4.2.2.1. This s a tool that helps identify, sort, and display possible causes of a specific problem or quality characteristic. It graphically illustrates the relationship between a given outcome and all the factors that influence the outcome. Categorize each issue on the right side of the diagram.
4.2.3. scatter diagram
4.2.3.1. This pairs of numerical data, with one variable on each axis, to look for a relationship between them. If the variables are correlated, the points will fall along a line or curve. The better the correlation, the tighter the points will hug the line.
4.2.4. why - why
4.2.4.1. The 5 Why Technique, a method to discover and analyze solutions of a problem and breaks down the solutions and is somewhat linked to the fishbone diagram whereas you break it down into smaller components. Most of the issues contain the same causes.
4.2.5. process map
4.2.5.1. This is a planning and management tool that visually describes the flow of work. A process map is also called a flowchart, process flowchart, process chart, functional process chart, functional flowchart, process model, workflow diagram, business flow diagram, or process flow diagram. You use this to help identify failures, improvement and it is similar to the flowchart, but it withholds a different function.
4.2.6. check list
4.2.6.1. This is a type of job aid used to reduce failure by compensating for potential limits of human memory and attention. It helps to ensure consistency and completeness in carrying out a task. Use then when you want to avoid failure and ensure consistency.
4.2.7. run chart
4.2.7.1. This is a line graph of data plotted over time. By collecting and charting data over time, you can find trends or patterns in the process. Since they do not use control limits, run charts cannot tell you if a process is stable. However, they can show you how the process is running.
4.3. approaches
4.3.1. six sigma
4.3.1.1. Is a statistical based, data driven approach & improvement methodology
4.3.1.2. For eliminating defects in a product/ service
4.3.1.3. Is defined as anything that falls out of a customer specification
4.3.1.4. Is a statistical measuring system
4.3.1.5. gradual Improvement
4.3.2. TGM
4.3.2.1. is the continual process of detecting, reducing or eliminating a problem
4.3.2.2. Continual improvement through internal practices
4.3.2.3. Aims to hold all parties involved in the process for the overall quality of the final product/ service
4.3.2.4. gradual improvement
4.3.3. Lean management
4.3.3.1. is a system that approach to the identification and elimination of problems through employee development and continious improvement of all services and products
4.3.3.2. Eliminating waste and creating value for customer
4.3.3.3. Increase revenue by providing better qualified service
4.3.3.4. gradual improvement
4.3.4. BPR
4.3.4.1. is to obtain a specific business outcome radically
4.3.4.2. Important goal is to analyze workflows within and between enterprises in order to optimize end-to-end processes and eliminate tasks that do not provide the customer with value
4.3.4.3. radical improvement
4.4. radical improvement
4.4.1. is a fast and fundamental improvement (in big steps)
4.5. gradual improvement
4.5.1. is proceeded step by step, slow, from one step to another (=slow improvement, no step for a long time
4.6. key elements of improvement process
4.6.1. Quality Improvement Safety Performance Asset Optimization Project Execution Supply Chain Process Improvement Shutdown Management Reliability Inventory Management Value Engineering
5. segmentation
5.1. Segmentation means to divide the marketplace into parts, or segments.
6. Quality
6.1. quality managemant systems
6.1.1. Internally
6.1.1.1. Internal audits act on behalf of the company rather than a certification body and are conducted on a set of processes to ensure they meet the organization’s internal requirements or standards.
6.1.2. externally
6.1.2.1. An external audit is what we call a certification audit and it is when a certification body outside the organization is hired to ensure the company complies with the Reference Standard. This process involves a greater level of detail and strictly follows international accreditation standards
6.2. quality in general
6.2.1. Quality in the tourism and hospitality industry involves consistent delivery of products and guest services according to expected standards.
6.3. quality in operations
6.3.1. Quality management is the act of overseeing all activities and tasks that must be accomplished to maintain a desired level of excellence. This includes the determination of a quality policy, creating and implementing quality planning and assurance and quality control and quality improvement.
7. Process design
7.1. layout types
7.1.1. process layouts
7.1.1.1. group similar resources together
7.1.2. product layouts
7.1.2.1. desinged to produce a specific product efficiently
7.1.3. Hybrid layouts
7.1.3.1. combine aspects of both process and product layouts
7.1.4. Fixed-postion layouts
7.1.4.1. product is to large to move (building)
8. Process management
8.1. Process
8.1.1. Input-output process
8.1.1.1. Operations management transforms inputs (labor, capital, equipment, land, buildings, materials and information) into outputs (goods and services) that provide added value to customers.
8.1.2. 4 v's dimension
8.1.2.1. volume
8.1.2.1.1. this refers to the how much of a specific product is required to satisfy its demand. Low volume operations tend to be less repetitive with staff performing more than one function (multitasking) whereas high volume translates into repeatable processes, which in turn can be standardized or automated. A high volume can easier satisfy a higher level of demand since the production process is faster due to automated activities.
8.1.2.2. variety
8.1.2.2.1. relates to the variety of goods/service to be produced and sold to customer. This V is all about diversity. High variety give more company’s the flexibility to produce goods and/or services to match the customer’s requirements. Variety and volume correlates, the higher the variety the lower the volume of the products or services.
8.1.2.3. variation
8.1.2.3.1. Variation: this refers to how much the level of demand changes over a time period due to external factors. However, a number of factors make it difficult to predict variation.
8.1.2.4. visibility
8.1.2.4.1. refers to how much of the company’s process does the customer actually experience. The service industries has a high level of visibility whereas the manufacturing industry has little to no visibility to its customers. There are some companies that have a mixture of both.
8.2. process design
8.2.1. performance objectives
8.2.1.1. quality
8.2.1.2. speed
8.2.1.3. dependability
8.2.1.4. flexibility
8.2.1.5. costs
8.2.2. layout types
8.2.2.1. process layouts
8.2.2.1.1. group similar resources together
8.2.2.2. product layouts
8.2.2.2.1. desinged to produce a specific product efficiently
8.2.2.3. Hybrid layouts
8.2.2.3.1. combine aspects of both process and product layouts
8.2.2.4. Fixed-postion layouts
8.2.2.4.1. product is to large to move (building)
8.3. process types
8.3.1. Repetitive Processing
8.3.1.1. Repetitive processing has dedicated production lines that produce the same or similar items consistently without change. It requires minimal setup or changeover, so it can be accelerated, slowed down, or another production line added.
8.3.2. Discrete Processing
8.3.2.1. Discrete processing is also an assembly or production line process, but it is highly diverse, with a wide variation of setups and changeover frequencies. The variation is based on whether the products being produced are alike or very disparate. If the latter is the case, setup and tear-down will require more time.
8.3.3. Job Shop Processing
8.3.3.1. Job shop processing has production areas, rather than production lines. One or a number of product versions are assembled in the areas. If demand deems necessary, the job shop operation is converted to a discrete processing environment with automated equipment.
8.3.4. Process Manufacturing
8.3.4.1. This type of operation is analogous to discrete and job shop processes. The process can run produce one batch or several, depending on requirements. Continuous batch processes are possible when the composition of raw materials can’t be made to a strict standard. Design considerations and disciplines are more diverse.