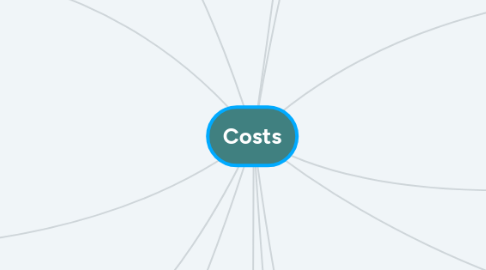
1. Indirect Costs
1.1. Indirect costs are those that can't be directly linked to the manufacture of a part, such as indirect labour, indirect materials costs and any other expenses that cant be attribute to the manufacture of a part.
1.1.1. Indirect materials costs
1.1.1.1. Materials used in a process that cant be directly traced to a cost object
1.1.2. Indirect labour
1.1.2.1. Labour costs that aren't directly linked with the manufacture of a part e.g. security officers and cleaners.
2. Overhead Costs
2.1. Any costs from the ongoing running of a business
2.2. Overhead costs include: research and development, office wages, rent, machinery costs, maintenance costs and any bills, such as heating and lighting. Any indirect costs of manufacturing a part are also considered as overhead costs
3. Non-Added Value
3.1. Non-added value costs are any additional costs that don't add to the value of a product.
3.1.1. Transportation would be classed as a non-added value cost as it doesn't enhance the product in any way but the cost of it needs to be factored in to the total cost.
3.1.2. Other examples are: storing raw materials and excess stock, reworking defective parts and returning damaged materials.
3.1.3. Non-added value costs can be reduced by trying to eliminate any activities that don't benefit the product, such as only producing the number of parts needed
4. Prime Costs
4.1. Prime costs is the sum of all direct costs incurred in the production of a part
4.2. Prime costs = Direct materials + Direct labour + Direct expanses
5. Unit Cost
5.1. The average cost per part of manufacturing a finished product.
5.1.1. Unit cost = Total cost/Number of Units
6. Break Even Point
6.1. The break even point is when the total expenditure is equal to the total revenue made
6.2. The break even point can be calculated by using the following formula: Break Even Quantity = Fixed costs / (Selling price- Variable costs)
6.3. The break even point can be used to calculate the number of parts that need to be sold to cover any costs incurred to the company, including fixed and variable costs.
6.4. Profit
6.4.1. Any revenue made after the break even point is made would be considered profit.
7. Fixed Costs
7.1. Fixed costs are expenses to a business that don't change with the productivity of a business.
7.1.1. They are usually costs that are paid monthly, such as rent for the building, phone line rental and a security system.
8. Material Costs
8.1. Direct material costs are the costs of materials which are directly linked to a product or its manufacture e.g. glass is a direct materials cost for a light bulb
8.2. Can be reduced using cheaper materials and modifying designs
8.3. Can be reduced DFMA (designed for manufacture and assembly) tools to streamline the process
8.4. Calculate materials costs: 1. Find the total amount to be produced. 2. Calculate the amount of raw materials needed 3. Multiply that amount by the cost of the raw materials. 4. Any waste or scrap materials should be added to the cost 5. If waste or scrap can be sold, this value should be subtracted from the costs in step 4.
9. Tooling Costs
9.1. The cost to a manufactured that is incurred by the acquirement of tooling needed to complete a job.
9.2. Tooling costs can be calculated by adding the cost of each tool tat will be used to produce a part together.
9.3. Tooling costs can be reduced by using simpler designs, subcontracting work out, changing the manufacturing method and using larger tolerances
10. Labour Costs
10.1. Labour costs is the sum of all wages paid to employees over the duration of a part being manufactured. These are worked out by multiplying an employees hourly rate by the amount of hours it will take them to complete a job. e.g. if someone is paid £10/h and the part will take 15 hours to produce then the cost of labour for that part will be £150
10.2. Labour costs can be reduced by reducing the amount of overtime worked, using shifts, using less skilled workers and by subcontracting work out.
11. Production Costs
11.1. The production cost is the total cost of the production of a part
11.2. Production costs = Prime costs + Production overheads
12. Direct Costs
12.1. Direct costs are those which are directly linked to the manufacture of a part, such as materials costs, direct labour costs any any other costs which can be associated with the parts.
12.1.1. Direct labour
12.1.1.1. Labour costs that can be directly linked to manufacture e.g. a machinist