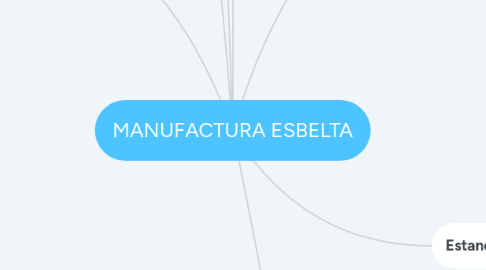
1. Que es?
1.1. Herramientas que ayudaran a eliminar las operaciones que no agregan valor
2. Tipos de valor
2.1. Valor agregado
2.2. Valor no agregado
2.3. Valor no agregado pero necesario
3. Diagnostico de un negocio
3.1. Cadena de Valor
3.1.1. Actividades primarias o de línea
3.1.1.1. Logística interior
3.1.1.2. Operaciones
3.1.1.3. Logística exterior
3.1.1.4. Mercadotecnia y ventas
3.1.1.5. Servicios
3.1.2. Actividades de apoyo o de soporte
3.1.2.1. Infraestructura de la empresa
3.1.2.2. Gestión de recursos humanos
3.1.2.3. Desarrollo de la tecnología
3.1.2.4. Aprovisionamiento
3.2. Tiempo de Respuesta
3.2.1. Tiempo para entregar el producto al cliente
3.3. Value Stream Map
3.3.1. Identificar el producto
3.3.2. Conocer los símbolos a utilizar
3.3.3. Definir el alcance
3.3.4. Agregar las actividades involucradas
3.3.5. Agregar el flujo de información
3.3.6. Incluir los datos especificos
3.3.7. Reflejar el inventario y la línea de tiempo
3.3.8. Determinar las posibles mejoras
3.3.9. Realizar el mapa Futuro
3.3.10. Generar indicadores
3.3.11. Implementación
4. Sistema de produccion TOYOTA
4.1. Antecedentes del Sistema
4.2. Conformación y reglas del sistema
4.2.1. JIT
4.2.2. JIDOKA
4.3. Estandarización de operación
4.4. Pokayoke
4.4.1. A prueba de errores
4.5. Control Visual
4.6. Kanban
4.6.1. Etiqueta de instrucción
4.6.2. Funciones
4.6.2.1. Control de la producción
4.6.2.2. Mejora de los procesos
4.6.2.3. Eliminación de la sobreproducción
4.6.2.4. Control de material
4.6.3. Tipos
4.6.3.1. Tarjeta Kanban
4.6.3.2. Kanban Contenedor
4.6.3.3. Kanban de ubicación
4.6.3.4. Kanban disparador
4.6.3.5. Kanban electrónico
4.7. SMED
4.7.1. Cambios Rapido
4.8. HEIJUNKA
4.8.1. Transformación a nivel plano
4.9. JIDOKA
4.9.1. Automatización con un toque humano
5. Ojetivos
5.1. Reducir desperdicios
5.1.1. Productos de alta calidad con precios competitivos y en el tiempo requerido.
5.2. Crear sistemas de producción más robustos.
5.3. Mejorar el flujo del proceso.
5.4. Mejorar el lay out de planta para aumentar la flexibilidad.
5.5. Reducir el inventario
5.5.1. 7 Desperdicios
5.5.1.1. Sobreproducción
5.5.1.2. Tiempo de espera
5.5.1.3. Transporte
5.5.1.4. Movimientos
5.5.1.5. Sobreporceso
5.5.1.6. Defectos
5.5.1.7. Inventario
6. KAIZEN
6.1. Mejor Continua
6.2. PDCA
6.2.1. Planear
6.2.2. Hacer
6.2.3. Verificar
6.2.4. Actuar
7. Estandarizacion de operaciones.
7.1. Tiempo ciclo
7.2. Secuencia de Pasos
7.3. Estándar de Trabajo en proceso
7.3.1. Hoja de trabajo estandar
7.3.1.1. Detalle del proceso
7.3.1.2. La secuencia del proceso definida en pasos.
7.3.1.3. Tiempos de cada elemento o paso.
7.3.1.4. Diagrama que muestra los movimientos en la operación.
7.3.1.5. Indica puntos de seguridad, calidad, en cada paso del proceso.
7.3.1.6. Firma de los responsables de seguir el estandar.