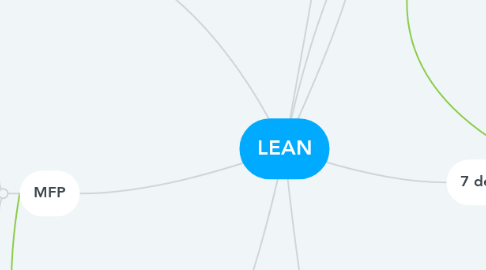
1. Autonomação
1.1. Mecanismo de controle das anomalias do processo e investigação imediata das falhas
1.2. Paradas automáticas
1.2.1. Equipamentos param quando detectam erro
1.2.2. Sistema poka yoke: ferramenta para evitar erros humanos
1.3. Andon
1.3.1. Auxilia na gestão visual da produção
1.4. Verificação de erros
1.4.1. Controle da qualidade no setor, para garantir que erros não avancem no processo e cheguem nos cliente
1.4.1.1. 5 porquês
1.4.1.1.1. Ferramenta que auxilia na investigação das falhas
2. Just in time
2.1. Busca fluxos produtivos enxutos
2.2. Fluxo contínuo
2.2.1. Sem variabilidade de demanda de produção
2.3. Sistema puxado
2.3.1. Etapas produtivas ocorrem conforme demanda
2.3.1.1. Kanban
2.3.1.1.1. Ferramenta que objetiva fazer com que os componentes se movam conforme quantidade previamente estabelecida
2.4. Troca rápida
2.4.1. Tempo perdido em setups - trocas, não pode ser elevado
2.5. Logística integrada
2.5.1. Todas as movimentações de materiais na cadeia produtiva seja síncrona.
3. STP
3.1. EUA x Japão
3.1.1. Após a segunda guerra mundial, a cooperação entre os dois países ajudou a entender as diferenças nas características gerenciais e no surgimento do sistema Toyota.
3.2. Comprometimento
3.2.1. Com a prática do "trabalho vitalício", a construção do STP foi facilitada, pois os colaboradores tinham mais comprometimento com a empresa e com as metas
3.3. Lean e STP
3.3.1. O termo Lean manufacturing foi desenvolvido para difundir de forma mais clara as praticas do STP no ocidente. Tratamos geralmente ambos como sendo a mesma coisa.
4. Pilares do STP
5. MFP
5.1. Operação
5.1.1. Trabalho realizado para efetivar a transformação da matéria prima em produto
5.2. Processo
5.2.1. Estágios pelos quais as matérias primas se movimentam até construir um produto acabado
5.3. Mecanismo da função produção
6. Reduzir perdas
6.1. Visão de perdas: Tudo aquilo que está nos processos e produtos e não agrega valor ao cliente
6.2. Até os estudos de Shigeo Shingo, desperdícios estavam relacionados apenas a perdas de MP
7. Valor
7.1. VA
7.1.1. Atividades que agregam valor: Causam transformação no produto ou geram vantagem competitiva
7.2. BNVA
7.2.1. Atividades do negócio que não agregam valor: Exigências da lei ou evitam perdas financeiras
7.3. NVA
7.3.1. Não agregam valor: Retrabalho, expedição, inspeção, setup...
7.4. Produto melhor com preço menor = maior valor para o cliente
8. 7 desperdícios
8.1. Superprodução
8.1.1. Superprodução antecipada ou quantitativa podem gerar, entre outras coisas, defeitos de qualidade, lead time elevado e aumento de custo do estoque
8.2. Espera no processo
8.2.1. Ocorre quando a MP ou o produto ficam parados esperando a próxima etapa do processo
8.3. Transporte
8.3.1. Dentre as principais causas estão o transporte desnecessário e os sistemas inadequados de transporte
8.4. Manuseio
8.4.1. Manuseios desnecessários geram fadiga dos operadores, aumento no ciclo produtivo e baixa produtividade
8.5. Processamento
8.5.1. Falta de treinamento, erro no projeto e falta de padronização
8.6. Estoque
8.6.1. Estoque elevado representam problema na gestão do estoque, necessidade de grande espaço físico para armazenagem e capital financeiro parado
8.7. Itens defeituosos
8.7.1. Principalmente causado por baixa qualificação e treinamento dos operadores, defeitos em máquinas e equipamentos ou alta variabilidade nos processos.