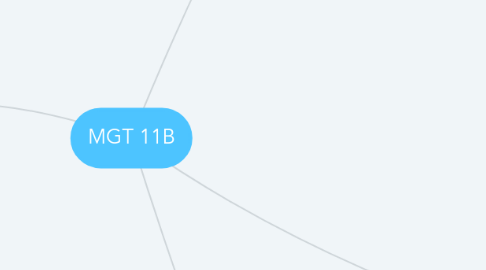
1. Chapter 4
1.1. 4.1 Compare between job-order and process costing
1.1.1. Similarities
1.1.1.1. 1. Both systems have the same basic purposes—to assign material, labor, and manufacturing overhead costs to products and to provide a mechanism for computing unit product costs. 2. Both systems use the same basic manufacturing accounts, including Manufacturing Overhead, Raw Materials, Work in Process, and Finished Goods. 3. The flow of costs through the manufacturing accounts is basically the same in both systems.
1.1.2. Differences
1.1.2.1. job-order
1.1.2.1.1. 1. Many different jobs are worked on during each period, with each job having unique production requirements. 2. Costs are accumulated by individual job. 3. Unit costs are computed by job on the job cost sheet.
1.1.2.2. process
1.1.2.2.1. 1. A single product is produced either on a continuous basis or for long periods of time. All units of product are identical. 2. Costs are accumulated by department. 3. Unit costs are computed by department.
1.2. 4.2 Cost flow in processing
1.2.1. Processing Departments
1.2.1.1. is an organizational unit where work is performed on a product and where materials, labor, or overhead costs are added to the product
1.2.1.2. Two essential features of all processing departments
1.2.1.2.1. 1. the activity in the processing department is performed uniformly on all of the units passing through it.
1.2.1.2.2. 2. the output of the processing department is homogeneous
1.2.2. Journal Entry
1.2.2.1. Manufacturing Overhead
1.2.2.1.1. debit: Work in Process--Department name credit: Manufacturing overhead
1.3. 4.3 Processing Cost Computation
1.3.1. Weighted-average Method
1.3.2. FIFO Method
1.3.3. Conversion Cost
1.3.3.1. direct labor + manufacturing overhead
1.3.4. Equivalent Units
1.3.4.1. Equivalent units=Number of partially completed units×Percentage completion
1.4. 4.4 Weighted-average Method: an Example
1.4.1. 1. Compute Equivalent Units of Production
1.4.1.1. = Number of completed units transferred + equivalent units in the department′s ending Work in Process Inventory(%completion * number of units in ending)
1.4.1.1.1. Eg: 4800 + 400 * 40% = 4960
1.4.2. 2. Compute Cost per Equivalent Unit
1.4.2.1. Cost of beginning work in process inventory+cost added during the period —————————————————————————————————— Equivalent Units of Production
1.4.3. 3. Assign Cost to units
1.4.3.1. Cost of Ending Inventory=Equivalent Units * Cost Per Equivalent Unit
2. Chapter 1 Cost classification
2.1. 1.1 Assigning costs to cost objects
2.1.1. Direct cost
2.1.1.1. Costs that can be easily and conveniently traced to a unit of product or other cost object Eg: direct material and direct labor
2.1.2. Indirect cost
2.1.2.1. Costs that cannot be easily and conveniently traced to a unit of product or other cost object Eg: manufacturing overhead and common costs
2.2. 1.2 Accounting for Costs in manufacturing companies
2.2.1. Manufacturing cost
2.2.1.1. Direct Material
2.2.1.1.1. Raw materials that become an integral part of the product Can be traced directly to the product Example: radio installed in automobile
2.2.1.2. Direct Labor
2.2.1.2.1. Labor costs that can be easily traced to individual units of product Example: wages paid to automobile assembly workers
2.2.1.3. Manufacturing overhead
2.2.1.3.1. Includes all manufacturing costs except direct material and direct labor. Includes indirect materials and indirect labor costs that cannot be easily traced to specific units of product Examples: depreciation of manufacturing equipment, utility costs
2.2.2. Non-manufacturing cost
2.2.2.1. Selling cost
2.2.2.1.1. Costs necessary to secure the order and deliver the product Can be direct or indirect costs Examples: advertising and sales commissions
2.2.2.2. Administrative Cost
2.2.2.2.1. Costs associated with the general management of an organization Can be direct or indirect costs All executive, organizational, and clerical costs
2.3. 1.3 Product costs and period costs
2.3.1. Product Cost
2.3.1.1. Costs that are involved in acquiring or making a product Attach to a unit of product as it is purchased or manufactured Stay attached to each unit of product as long as it remains in inventory awaiting sale
2.3.1.1.1. Raw material + direct labor + manufacturing overhead
2.3.2. Period Cost
2.3.2.1. Costs that are not product costs Selling and administrative expenses Expensed on the income statement in the period in which they occur
2.4. 1.4 Cost Classification for predicting cost behavior
2.4.1. Variable cost
2.4.1.1. - Cost that varies in direct proportion to changes in the level of activity - A variable cost per unit is constant
2.4.1.1.1. Activity base – a measure of what causes the incurrence of a variable cost Examples: units produced, labor hours
2.4.2. Fixed Cost
2.4.2.1. Cost that remains constant regardless of changes in the level of activity
2.4.2.1.1. Committed fixed costs – long-term costs that cannot be significantly reduced in the short term - Examples: equipment, salaries of management Discretionary costs – costs that may be altered in the short term - Examples: advertising, annual costs
2.4.3. Mixed Costs Contains both variable and fixed elements Y = a + bX
2.4.3.1. a = fixed cost b = variable cost X = level of activity base
2.5. 1.5 Cost used in making decisions
2.5.1. Differential Cost and Revenue
2.5.1.1. Difference in cost between two alternatives Only differences between alternatives are relevant in decisions Differential revenue – difference in revenue between two alternatives Differential cost – difference in cost between two alternatives
2.5.1.1.1. For example, one building is leased for $50 per square foot and another building is leased for $60 per square foot
2.5.2. Opportunity Cost
2.5.2.1. Potential benefit that is given up when one alternative is selected over another
2.5.2.1.1. For example, you decide to Uber to school instead of taking the bus. The Uber was $5 and the bus is $1. The opportunity cost is $4.
2.5.3. Sunk Cost (Ignored when making decisions)
2.5.3.1. Costs that have already been incurred and cannot be changed now or in the future
2.5.3.1.1. A company pays a new recruit $10,000 to join the organization. If the person proves to be unreliable, the $10,000 payment should be considered a sunk cost when deciding whether the individual's employment should be terminated.
2.6. Other stuffs
2.6.1. Contribution Margin = Sales - Variable expenses
3. Chapter 2 Job-Order Costing: Calculating Unit Product Costs
3.1. 2.1 Overview
3.1.1. Job-order costing systems
3.1.1.1. are used when many different products, each with individual and unique features, are produced each period
3.1.1.1.1. Examples Boeing – aircraft manufacturing Walt Disney Studios – movie production Service industries such as hospitals and law firms use the same basic concepts
3.1.1.2. Job:
3.1.1.2.1. A particular order might consist of 1,000 boot-cut men’s blue denim jeans, style number A312. This order of 1,000 jeans is called a job
3.1.2. Classification of Manufacturing Cost
3.1.2.1. direct material
3.1.2.2. direct labor
3.1.2.3. manufacturing overhead
3.2. 2.2 Sample and Calculation
3.2.1. Measuring direct material cost
3.2.1.1. Bill of materials
3.2.1.1.1. is a document that lists the quantity of each type of direct material needed to complete a unit of product
3.2.1.2. Materials requisition form
3.2.1.2.1. is a document that specifies the type and quantity of materials to be drawn from the storeroom and identifies the job that will be charged for the cost of the materials.
3.2.2. Job cost sheet
3.2.2.1. records the materials, labor, and manufacturing overhead costs charged to that job
3.2.2.2. generated after a production order has been issued
3.2.3. Measuring direct labor cost
3.2.3.1. time ticket
3.2.3.1.1. A completed time ticket is an hour-by-hour summary of the employee’s activities throughout the day
3.2.4. Measuring Manufacturing overhead cost
3.2.4.1. Predetermined Overhead Rate(POHR)
3.2.4.1.1. Estimate total fixed manufacturing overhead cost ——————————————— Estimated total amount of the allocation base
3.2.4.2. Total manufacturing Overhead Cost
3.2.4.2.1. = a + bX
3.2.5. Applying Manufacturing overhead cost
3.2.5.1. Overhead application
3.2.5.1.1. The process of assigning overhead cost to jobs is called overhead application
3.2.5.1.2. Overhead applied to a job = POHR * Amount of allocation base incurred by the job
3.2.5.1.3. This approach to overhead application is known as normal costing(normal cost system)
3.2.6. Single and Multiple Predetermined Overhead Rate
3.2.6.1. cost driver
3.2.6.1.1. is a factor, such as machine-hours, beds occupied, computer time, or flight-hours, that causes overhead costs.
3.2.6.2. plantwide overhead rate
3.2.6.2.1. single predetermined overhead rate to allocate all manufacturing overhead costs to jobs based on their usage of direct-labor hours
3.2.6.3. multiple predetermined overhead rates
3.2.6.3.1. uses more than one overhead rate to apply overhead costs to jobs
4. Chapter 3 Job-Order Costing: Cost Flows and External Reporting
4.1. 3.1 The Flow of Cost
4.1.1. Definitions:
4.1.1.1. Raw material
4.1.1.1.1. When raw materials are used in production as direct materials, their costs are transferred to Work in Process inventory
4.1.1.2. Work in process
4.1.1.2.1. consists of units of product that are only partially complete and will require further work before they are ready for sale to the customer
4.1.1.3. Finished Goods
4.1.1.3.1. consist of completed units of product that have not yet been sold to customers
4.1.1.4. Cost of Goods Manufactured
4.1.1.4.1. The amount transferred from Work in Process to Finished Goods
4.1.2. Journal Entry
4.1.2.1. Taking raw materials for production
4.1.2.1.1. Direct Material → Work in Process
4.1.2.1.2. Indirect Material → Manufacturing Overhead
4.1.2.2. Labor Cost
4.1.2.2.1. Direct Labor → Work in Process
4.1.2.2.2. Indirect Material → Manufacturing Overhead
4.1.2.3. Manufacturing Overhead Cost
4.1.2.3.1. indirect labor and material
4.1.2.3.2. utility, rent, miscellaneous
4.1.2.4. Applying Manufacturing Overhead Cost
4.1.2.4.1. quantity: debit: Work in Process applied manufac credit: Manufac overhead applied manufac
4.1.2.5. Non-manufacturing Cost
4.1.2.5.1. debit expenses credit: account payable/accumulated depreciation
4.2. 3.2 Schedules of Cost of Goods Manufactured and Cost of Goods Sold
4.2.1. Raw material used in production = (Beginning Raw material inventory + Raw material purchased)(= raw material available for use in production) - ending raw material inventory
4.2.2. Total manufacturing overhead cost = direct material + direct labor + manufacturing overhead applied to work in process
4.2.3. Cost of goods manufactured = total manufacturing cost + beginning work in process inventory - ending work in process inventory
4.2.4. Unadjusted cost of goods sold = beginning finished goods inventory + Cost of goods manufactured - ending finished goods inventory = cost of goods available for sale - ending finished goods inventory
4.3. 3.3 Underapplied and Overapplied Overhead
4.3.1. underapplied overhead
4.3.1.1. Underapplied – amount applied to jobs during the period using the predetermined overhead rate is less than the total amount of overhead actually incurred during the period
4.3.1.1.1. debit: Cost of goods sold credit: Manufacturing Overhead
4.3.2. overapplied overhead
4.3.2.1. amount applied to jobs during the period using the predetermined overhead rate is more than the total amount of overhead actually incurred during the period
4.3.2.1.1. debit: Manufacturing Overhead credit: Cost of goods sold
4.3.3. Underapplied (overapplied) manufacturing overhead = actual overhead costs of a period - Manufacturing overhead applied