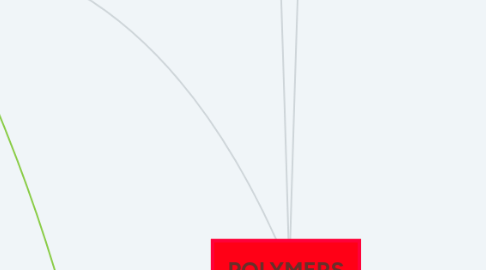
1. Crystallization, Melting, and Glass-Transition Phenomena in Polymers
1.1. Crystallization
1.1.1. The degree of crystallinity influences the mechanical and thermal properties of these materials.
1.1.2. The crystallization of a molten polymer occurs by nucleation and growth processes.
1.2. Melting
1.2.1. The melting of a polymer crystal corresponds to the transformation of a solid material, having an ordered structure of aligned molecular chains, into a viscous liquid in which the structure is highly random.
1.3. The Glass transition
1.3.1. The glass transition occurs in amorphous (or glassy) and semicrystalline polymers and is due to a reduction in motion of large segments of molecular chains with decreasing temperature.
1.3.2. The temperature at which the polymer experiences the transition from rubbery into rigid states is termed the glass transition temperature,
1.4. Melting and glass transition temperatures
1.4.1. Melting and glass transition temperatures are important parameters relative to inservice applications of polymers.
1.4.2. Melting and glass transition temperatures are important parameters relative to inservice applications of polymers.
1.5. Factors that influence melting and glass transition temperatures
1.5.1. Melting Temperature
1.5.1.1. During melting of a polymer there is a rearrangement of the molecules in the transformation from ordered to disordered molecular states
1.5.1.2. Chain stiffness, which is controlled by the ease of rotation about the chemical bonds along the chain, has a pronounced effect.
1.5.1.3. The melting temperature of a polymer also depends on molecular weight.
1.5.2. Glass transition Temperature
1.5.2.1. Upon heating through the glass transition temperature, the amorphous solid polymer transforms from a rigid into a rubbery state.
1.5.2.2. From the preceding discussion it is evident that essentially the same molecular characteristics raise and lower both melting and glass transition temperatures.
2. Mechanical Behaviour of Polymers
2.1. Stress strain behaviour
2.1.1. The mechanical characteristics of polymers, for the most part, are highly sensitive to the rate of deformation (strain rate), the temperature, and the chemical nature of the environment.
2.1.2. Three typically different types of stress–strain behavior are found for polymeric materials.
2.1.2.1. 1. The stress–strain character for a brittle polymer, which fractures while deforming elastically.
2.1.2.2. 2. The behavior for a plastic material is similar to that for many metallic materials; the initial deformation is elastic, which is followed by yielding and a region of plastic deformation
2.1.2.3. 3. Finally, the deformation is totally elastic; this rubber-like elasticity (large recoverable strains produced at low stress levels) is displayed by a class of polymers termed the elastomers.
2.1.3. The mechanical characteristics of polymers are much more sensitive to temperature changes near room temperature.
2.2. Macroscopic Deformation
2.2.1. At the upper yield point, a small neck forms within the gauge section of the specimen. Within this neck, the chains become oriented which leads to localized strengthening.
2.2.2. Consequently, there is a resistance to continued deformation at this point, and specimen elongation proceeds by the propagation of this neck region along the gauge length; the chain orientation phenomenon accompanies this neck extension. This tensile behavior may be contrasted to that found for ductile metals, in which once a neck has formed, all subsequent deformation is confined to within the neck region.
2.3. Viscoelastic deformation
2.3.1. An amorphous polymer may behave like a glass at low temperatures, a rubbery solid at intermediate temperatures, and a viscous liquid as the temperature is further raised.
2.3.2. Elastic deformation is instantaneous, which means that total deformation (or strain) occurs the instant the stress is applied or released.
2.3.3. Viscoelastic Relaxation Modulus
2.3.3.1. The viscoelastic behavior of polymeric materials is dependent on both time and temperature; several experimental techniques may be used to measure and quantify this behavior.
2.3.3.2. We may define a relaxation modulus Er(t), a time-dependent elastic modulus for viscoelastic polymers, as Er(t) =o(t) /E0 where o(t) is the measured time-dependent stress and E0 is the strain level, which is maintained constant.
2.3.3.3. The magnitude of the relaxation modulus is a function of temperature.
2.3.4. Viscoelastic creep
2.3.4.1. Many polymeric materials are susceptible to time-dependent deformation when the stress level is maintained constant; such deformation is termed viscoelastic creep.
2.3.4.2. Creep results are represented as a time-dependent creep modulus Ec(t), defined by: Ec(t) =o0/E(t) where o0 is the constant applied stress and E(t) is the time-dependent strain.
2.4. Fracture of polymers
2.4.1. The fracture strengths of polymeric materials are low relative to those of metals and ceramics. As a general rule, the mode of fracture in thermosetting polymers (heavily crosslinked networks) is brittle.
2.4.2. For thermoplastic polymers, both ductile and brittle modes are possible, and many of these materials are capable of experiencing a ductile-to-brittle transition.
2.5. Miscellaneous Mechanical Characteristics
2.5.1. Impact Strength
2.5.1.1. The degree of resistance of a polymeric material to impact loading may be of concern in some applications.
2.5.1.2. impact strength undergoes a gradual decrease at still higher temperatures as the polymer begins to soften.
2.5.2. Fatique
2.5.2.1. Polymers may experience fatigue failure under conditions of cyclic loading. As with metals, fatigue occurs at stress levels that are low relative to the yield strength.
2.5.2.2. The fatigue behavior of polymers is much more sensitive to loading frequency than for metals.
2.5.3. Tear Strength and Hardness
2.5.3.1. Other mechanical properties that are sometimes influential in the suitability of a polymer for some particular application include tear resistance and hardness.
2.5.3.2. Tear strength, the mechanical parameter measured, is the energy required to tear apart a cut specimen that has a standard geometry. The magnitude of tensile and tear strengths are related.
3. Polymers Types
3.1. Plastics
3.1.1. Possibly the largest number of different polymeric materials come under the plastic classification. Plastics are materials that have some structural rigidity under load and are used in general-purpose applications.
3.1.2. Polymers falling within this classification may have any degree of crystallinity, and all molecular structures and configurations are possible.
3.1.3. Plastic materials may be either thermoplastic or thermosetting in fact, this is the manner in which they are usually subclassified.
3.2. Elastomers
3.2.1. The most important synthetic elastomer is SBR, which is used predominantly in automobile tires, reinforced with carbon black. NBR, which is highly resistant to degradation and swelling, is another common synthetic elastomer.
3.3. Fibers
3.3.1. Fiber polymers are capable of being drawn into long filaments having at least a 100:1 length-to-diameter ratio.
3.3.2. To be useful as a textile material, a fiber polymer must have a host of rather restrictive physical and chemical properties.
3.3.3. Consequently, they must have a high tensile strength and a high modulus of elasticity, as well as abrasion resistance.
3.4. Miscellaneous applications
3.4.1. Coatings
3.4.1.1. Coatings are frequently applied to the surface of materials to serve one or more of the following functions: (1) to protect the item from the environment, which may produce corrosive or deteriorative reactions; (2) to improve the item’s appearance; and (3) to provide electrical insulation.
3.4.2. Adhesives
3.4.2.1. An adhesive is a substance used to bond together the surfaces of two solid materials (termed adherends). There are two types of bonding mechanisms: mechanical and chemical.
3.4.2.2. A special class of this group of materials is the pressure-sensitive adhesives
3.4.3. Films
3.4.3.1. Polymeric materials have found widespread use in the form of thin films. Films having thicknesses between 0.025 and 0.125 mm.
3.4.3.2. are fabricated and used extensively as bags for packaging food products and other merchandis
3.4.4. Foams
3.4.4.1. Foams are plastic materials that contain a relatively high volume percentage of small pores and trapped gas bubbles. Both thermoplastic and thermosetting materials are used as foams
3.5. Advanced polymeric materials
3.5.1. Ultra-High-Molecular-Weight Polyethylene
3.5.1.1. Ultra-high-molecular-weight polyethylene (UHMWPE) is a linear polyethylene that has an extremely high molecular weight.
3.5.2. Liquid Crystal Polymers
3.5.2.1. Liquid crystal polymers (LCPs) are a group of chemically complex and structurally distinct materials that have unique properties and are used in diverse applications
3.5.3. Thermoplastic Elastomers
3.5.3.1. Thermoplastic elastomers (TPEs or TEs) are a type of polymeric material that, at ambient conditions, exhibits elastomeric (or rubbery) behavior yet is thermoplastic.
4. Characteristics and Applications
5. Mechanisms of Deformation and for Strengthening of polymers
5.1. Deformation of semicrystalline polymers
5.1.1. Mechanisms of Elastic deformation
5.1.1.1. As with other material types, elastic deformation of polymers occurs at relatively low stress levels on the stress–strain curve
5.1.1.2. The elastic modulus may be taken as some combination of the moduli of crystalline and amorphous phases.
5.1.2. Mechanism of Plastic Deformation
5.1.2.1. Adjacent chains in the lamellae slide past one another: this results in tilting of the lamellae so that the chain folds become more aligned with the tensile axis.
5.1.2.2. During deformation, the spherulites experience shape changes for moderate levels of elongation.
5.2. Factors that influence the mechanical properties of semicrystalline polymers
5.2.1. Molecular Weight
5.2.1.1. The magnitude of the tensile modulus does not seem to be directly influenced by molecular weight, but for many polymers it has been observed that tensile strength increases with increasing molecular weight.
5.2.2. Degree of Crystallinity
5.2.2.1. The degree of crystallinity can have a significant influence on the mechanical properties because it affects the extent of the intermolecular secondary bonding.
5.2.2.2. Increasing the crystallinity of a polymer generally enhances its strength.
5.2.3. Predeformation by Drawing
5.2.3.1. One of the most important techniques used to improve mechanical strength and tensile modulus is to permanently deform the polymer in tension. This procedure is sometimes termed drawing.
5.2.4. Heat-Treating
5.2.4.1. Heat-treating (or annealing) of semicrystalline polymers can lead to an increase in the percent crystallinity and crystallite size and perfection, as well as to modifications of the spherulite structure.
5.3. Deformation of elastomers
5.3.1. Vulcanization
5.3.1.1. The crosslinking process in elastomers is called vulcanization, which is achieved by a nonreversible chemical reaction, typically carried out at an elevated temperature.
5.3.1.2. In most vulcanizing reactions, sulfur compounds are added to the heated elastomer.
6. Synthesis and Processing of Polymers
6.1. Polymerization
6.1.1. Addition polymerization
6.1.1.1. A process in which monometer units are attached one at a time in a chainlike fashion.
6.1.1.2. Three stages: initiation, propagation, termination.
6.1.2. Condensation Polymerization
6.1.2.1. The formation of polymers by stepwise intermolecular chemical reactions that may involve more than one monomer species.
6.1.2.2. Reaction times for condensation polymerization is usually longer than additional polymerization
6.2. Polymer Additives
6.2.1. Fillers
6.2.1.1. Improve tensile and compressive strengths, abrasion resistance, toughness, dimensional and thermal stability.
6.2.1.2. Polymers that contain fillers may be classified as composite materials.
6.2.2. Plasticizers
6.2.2.1. Flexibility, ductility and toughness of polymers is improved, but redustion in hardness and and stiffness.
6.2.2.2. Lowers the glass transition temperature.
6.2.3. Stabilizers
6.2.3.1. Deterioration results from exposure to light. Stabilizers counteract this.
6.2.3.2. Material reacts with bonds broken by the UV radiation.
6.2.3.3. Oxidation is another form of deterioration. stabilizers consume oxygen before it reaches the polymer.
6.2.4. Colorants
6.2.4.1. Imparts a specific colour, may be added as dyes or pigments
6.2.4.2. Dyes dissolve where pigments remains in seperate phase.
6.2.5. Flame Retardants
6.2.5.1. The flammability of polymers is a big concern, most polymers are flammable in their pure form.
6.2.5.2. Flame retardants interfere with the combustion process through the gas phase or initiation different combustion reactions and in result, decreasing the temperate, causing a slower burning.
6.3. Forming Techniques for plastics
6.3.1. Compression and Transfer Molding
6.3.1.1. For compression molding, the appropriate amounts of thoroughly mixed polymer and necessary additives are placed between male and female mold member
6.3.1.2. The mold is closed, and heat and pressure are applied, causing the plastic to become viscous and flow to conform to the mold shape.
6.3.1.3. In transfer molding—a variation of compression molding—the solid ingredients are first melted in a heated transfer chamber. As the molten material is injected into the mold chamber, the pressure is distributed more uniformly over all surfaces. This process is used with thermosetting polymers and for pieces having complex geometries
6.3.2. Injection molding
6.3.2.1. Most widely used technique for fabricating thermoplastic materials
6.3.2.2. The thermoplastic material melts to form a viscous liquid. Next, the molten plastic is impelled, again by ram motion, through a nozzle into the enclosed mold cavity; pressure is maintained until the molding has solidified. Finally, the mold is opened, the piece is ejected
6.3.2.3. Probably the most outstanding feature of this technique is the speed with which pieces may be produced.
6.3.3. Extrusion
6.3.3.1. The extrusion process is the molding of a viscous thermoplastic under pressure through an open-ended die.
6.3.3.2. Extrusion takes place as this molten mass is forced through a die orifice
6.3.3.3. The technique is especially adapted to producing continuous lengths having constant cross-sectional geometries—for example, rods, tubes, hose channels, sheets, and filaments
6.3.4. Blow molding
6.3.4.1. The blow-molding process for the fabrication of plastic containers is similar to that used for blowing glass bottles
6.3.4.2. The temperature and viscosity of the parison must be regulated carefully
6.3.5. Casting
6.3.5.1. Like metals, polymeric materials may be cast, as when a molten plastic material is poured into a mold and allowed to solidify.
6.3.5.2. Solidification occurs upon cooling from the molten state.
6.4. Fabrication of elastomers
6.4.1. Techniques used in the actual fabrication of rubber parts are essentially the same as those discussed for plastics as described previously—compression molding, extrusion, and so on.
6.5. Fabrication of fibers and films
6.5.1. Fibers
6.5.1.1. The process by which fibers are formed from bulk polymer material is termed spinning.
6.5.1.2. The material to be spun is first heated until it forms a relatively viscous liquid.
6.5.1.3. Next, it is pumped through a plate called a spinneret, which contains numerous small, typically round holes. As the molten material passes through each of these orifices, a single fiber is formed, which is rapidly solidified by cooling with air blowers or a water bath.
6.5.1.4. The crystallinity of a spun fiber depends on its rate of cooling during spinning. The strength of fibers is improved by a postforming process called drawing.
6.5.2. Films
6.5.2.1. Many films are simply extruded through a thin die slit; this may be followed by a rolling (calendering) or drawing operation that serves to reduce thickness and improve strength.