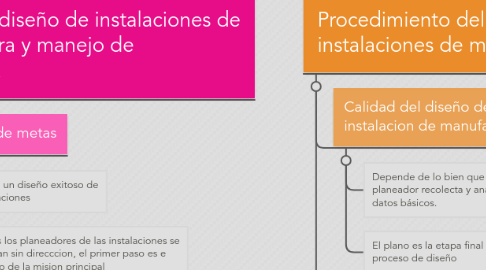
1. La importancia del diseño
1.1. Afecta a:
1.1.1. La productividad
1.1.2. El costo del producto
1.1.3. La calidad del producto
1.1.4. La rentabilidad
1.2. Se refiere a:
1.2.1. La organizacion de las instalaciones fisicas para:
1.2.2. Promover el uso eficiente de recursos, personal, equipo, materiales y energia.
1.3. Tambien incluye factores como:
1.3.1. Ubicacion de la planta
1.3.2. Manejo de materiales
1.3.3. Distribucion de la planta
1.3.4. Diseño del inmueble
1.3.4.1. El arreglo fisico de maquinas y equipos para la produccion
1.4. La importancia de una buena ubicación:
1.4.1. Proximidad de las fuentes de materia prima
1.4.2. Mercados y sistemas de transporte
1.5. La distribucion en una planta es:
1.5.1. Estaciones de trabajo
1.5.2. Ubicacion de materiales de todo tipo
1.5.3. Elaboracion y equipo de materiales
1.5.4. Personal
1.6. El manejo de materiales...
1.6.1. Basicamente, es mover la materia
1.6.2. Han tenido un efecto positivo sobre los trabajadores
1.6.3. Si se mejora el flujo del material, en forma automatica se reducen los costos de produccion. (Entre mas corto es el flujo a traves de la planta)
1.6.4. Ocasiona el 50% de los accidentes.
1.6.5. Ha eliminado los trabajos físicos pesados gracias a los equipos para el manejo de materiales. (el dinero para pagar dicho equipo deve provenir de las disminuciones en mano de obra, materiales o costos indirectos, y los gastos deben recuperarse en dos años o menos)
1.6.6. Formula de reducción de costos
1.6.6.1. Pregunta: ¿Por qué? ¿Quien? ¿Qué? ¿Dónde? ¿Cuando? ¿Cómo?
1.6.6.2. Para todo: Operación, transporte, insepcción, almacenamiento, retraso
1.6.6.3. Por tanto se puede: Eliminar, combinar, cambiar la secuencia, simplificar.
1.7. Cinco principios para reduccion de costos
1.7.1. Sacar solo lo necesario: Mantener el mínimo de lo que se requiere ahorrará espacio, inventario y dinero.
1.7.2. Acomodar: Un lugar para cada cosa y cada cosa en su lugar.
1.7.3. Limpiar y ordenar: Una planta segura es resultado de una buena planeacion de la distrubucion
1.7.4. Ser estrictos: Seguir procedimientos y métodos estandarizados hasta convertirlos en hábitos para que la planta opere de manera eficiente y segura.
1.8. Los cinco porqués
1.8.1. ¿Por qué?
1.8.2. La máquina se atascó. ¿Por qué?
1.8.3. La máquina no se limpió. ¿Por qué?
1.8.4. El operador no la limpió a intervalos regulares. ¿Por qué?
1.8.5. ¿Fue debido a la falta de capacitacion? ¿Por qué?
2. Pensamiento esbelto y manufactura esbelta
2.1. Muda (desperdicio)
2.1.1. Se define como: cualquier gasto que no ayuda a producir valor
2.1.2. Employee
2.2. Ocho clases de muda
2.2.1. Sobreproducción
2.2.2. Desperdicio
2.2.3. Transporte
2.2.4. Porcesamiento
2.2.5. Inventario
2.2.6. Movimiento
2.2.7. Repeticiones
2.2.8. Utilizacion deficiente del personal.
2.3. Kaizen
2.3.1. Se define como: Mejora constante o continua
2.3.2. Requiere de la participacion de todos los empleados
2.3.3. Se anima a cada persona de la compañía a buscar nuevas ideas y oportunidades para mejorar aún más la organización y sus procesos
2.4. Kanban
2.4.1. Difiere de los sistemas tradicionales como Just in time, o planeacion de requerimientos de materiales.
2.4.2. Consiste en un tablero de señales que comunica la necesidad de material e indica en forma visual al operador que produzca otra unidad o cantidad
2.5. Mapeo de la corriente de valor (MCV)
2.5.1. Se define como el proceso de evaluación de cada componente o etapa de la producción con fin de determinar el grado en que contribuye a la eficiencia operacional o a la calidad del producto.
2.5.2. Este proceso de mejora continua pasa por tres etapas representativas: Evaluación, análisis y ajuste.
3. Metas del diseño de instalaciones de manufactura y manejo de materiales.
3.1. Conjunto de metas
3.1.1. Garantiza un diseño exitoso de las instalaciones
3.1.2. Sin metas los planeadores de las instalaciones se encuentran sin direcccion, el primer paso es e enunciado de la mision principal
3.1.3. Un enunciado de mision bien pensado asegura que el inteniero o gerente de proyecto y la direccion de la empresa comparten las mismas visiones y objetivos
3.1.4. Abre lineas de comunicacion entre la direccion y el diseñador: la retroalimentacion
3.2. Enunciado de misión
3.2.1. Debe ser breve para que su esencia no se pierda y sea recordado con facilidad.
3.2.2. Define el proposito para el cual existe la empresa
3.2.3. Comunica las metas primarias y la cultura de la organización al planeador de las instalaciones.
3.3. Submetas para alcanzar metas especificas
3.3.1. Minimizar los costos unitarios y del proyecto.
3.3.2. Optimizar la calidad
3.3.2.1. Sin subir demasiado el costo del producto
3.3.3. Promover el uso eficaz de a) el personal, b) el equipo, c) el espacio, y d) la energía.
3.3.3.1. La ubicacion de servicios tales como sanitarios, casilleros, cafeterias, almacenes de herramientas y otros servcios.
3.3.4. Proporcionar a los empleados a) conveniencia, b) seguridad, y c) comodidad.
3.3.4.1. Los estacionamientos, entradas de empleados, sanitarios deben ser convenientes para todos los trabajadores
3.3.4.2. Las estadísticas de seguridad industrial indican que el 50 por ciento de todos los accidentes industriales ocurren mientras se manipulan los materiales
3.3.4.3. Si los trabajadores se encuentran en un receso, es deseable proporcionarles un ambiente agradable, de modo que puedan recuperarse y regresar al trabajo frescos y, por tanto, más productivos.
3.3.5. Controlar los costos del proyecto
3.3.5.1. Presupuestar y después funcionar con el presupuesto son dos cosas que los administradores e ingenieros exitosos aprenden a hacer en una fase temprana de sus carreras.
3.3.5.2. El costo del diseño de las instalaciones y proyecto del manejo de materiales debe determinarse antes de presentar el plan a la dirección para que lo apruebe
3.3.6. Alcanzar la fecha de inicio de la producción
3.3.6.1. Para productos de temporada, de hecho, si se pierde la estación, se pierde el año entero
3.3.6.2. El éxito del proyecto depende de que el producto entre a tiempo al mercado
3.3.7. Dar flexibilidad al plan
3.3.7.1. Es seguro que las cosas cambiarán y los diseñadores necesitan anticipar hacia dónde van a expandirse
3.3.8. Reducir o eliminar los inventarios excesivos
3.3.8.1. Los costos de llevar el inventario son aproximadamente 35% anual, y son:
3.3.8.1.1. a. Costo del espacio y su costo de apoyo. b. Costo del dinero inmovilizado en el inventario. c. Costo de los empleados que se requieren para mover y administrar el inventario. d. Pérdidas por daños, obsolescencia y otras mermas. e. Costo del equipo para manejar materiales.
3.3.9. Alcanzar varias metas
3.3.9.1. Todo lo que piense que es importante y quiera conseguir mediante su diseño de instalaciones nuevas debe establecerse como una meta. Las metas son para alcanzarse pero no siempre para lograrse a la perfección
4. Procedimiento del diseño de instalaciones de manufactura
4.1. Calidad del diseño de una instalacion de manufactura
4.1.1. Depende de lo bien que el planeador recolecta y analiza los datos básicos.
4.1.2. El plano es la etapa final del proceso de diseño
4.2. Procedimiento resumido
4.2.1. 1. Determinar lo que se producirá
4.2.2. 2. Calcular cuántos artículos se fabricarán por unidad de tiempo
4.2.3. 3. Definir qué partes se fabricarán o comprarán terminadas
4.2.4. 6. Establecer estándares de tiempo para cada operación
4.2.5. 8. Calcular el número de máquinas necesarias
4.2.6. 10. Estudiar los patrones de flujo del material para establecer cuál es el mejor
4.2.7. 12. Hacer la distribución de cada estación de trabajo.
4.2.8. 18. Desarrollar un plan gráfico y la forma de la construcción. ¿Cómo se ajusta la instalación al terreno?
4.2.9. 20. Buscar fallas y ajustar.
4.2.10. 22. Instalar la distribución
4.2.11. 23. Comenzar la producción.
4.2.12. 24. Ajuste lo que se requiera
5. Tipos y fuentes de los proyectos del diseño de instalaciones de manufactura
5.1. Instalacion nueva
5.1.1. En un proyecto nuevo hay pocas restricciones y limitantes
5.2. Producto nuevo
5.2.1. El producto nuevo debe incorporarse al flujo del resto de la planta
5.3. Cambios en el diseño
5.3.1. Se hacen para mejorar su costo y su calidad.
5.3.2. La distribución podría verse afectada por dichos cambios y el diseñador de instalaciones debe revisar cada modificación del diseño.
5.4. Reduccion del costo
5.4.1. El diseñador podría entronar una distribución mejor que produjera mas unidades con menos esfuerzo de los trabajadores.(y aceptar retroalimentacion de trabajadores)
5.5. Retroajuste
5.5.1. El procedimiento para el retroajuste es el mismo que para una planta nueva, pero con mas restricciones (por ejemplo, paredes que ya existen, techos bajos...)(renovación de una planta)
6. Las computadoras y la simulacion en el diseño de instalaciones de manufactura (software)
6.1. Ventajas de simulacion a computadora
6.1.1. Puede usarse para estudiar y optimizar la distribucion y la capacidad.
6.1.2. El software genera reportes y estadisticas detallados, con los cuales pueden evaluarse distribuciones fisica, seleccion de equipo, procedimientos de operacion...
6.1.3. Puede usarse para predecir el comportamiento de un sistema de manufactura
6.1.4. Son de valiosa ayuda en la toma de decisiones
6.1.5. Ya no requieren una formación solida en matemáticas o lenguajes de programacion
6.1.6. El software tiene una interfaz amigable para el usuario
6.2. ISO 9000
6.2.1. La revisión más reciente del estándar ISO 9000 pone énfasis en “el enfoque en el proceso”
6.2.2. Fue publicada en 1987
6.2.3. La compañía debe tener el compromiso de la alta dirección para producir un artículo de calidad
6.2.4. Debe haber mecanismos adecuados para asegurar el manejo, el almacenamiento, el empaque, la preservación y la entrega apropiados del producto.
6.2.5. También debe tomarse en cuenta el proceso de diseño y desarrollo. Desde las especificaciones del consumidor hasta las salidas de la instalación, todos los procedimientos y los procesos deben ligarse para lograr la satisfacción del cliente.
6.2.6. El ambiente de trabajo requiere ser apropiado para lograr la conformidad con el producto y alcanzar los requerimientos del consumidor.
6.2.7. La compañía debe desarrollar, documentar, implantar y mantener un sistema eficaz de administración por calidad.
6.2.8. Los planeadores de las instalaciones tienen muchas oportunidades para incorporar estos procedimientos en las etapas iniciales del diseño de la planta.
6.2.9. La compañía debe asegurar que tiene recursos adecuados
6.2.9.1. Personal calificado, equipo adecuado y niveles suficientes de inventario.