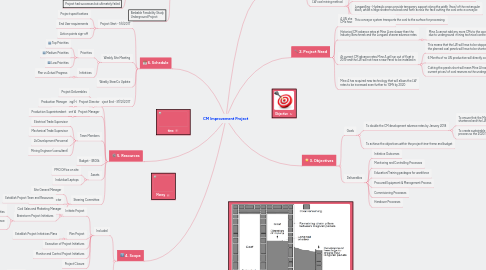
1. 6. Schedule
1.1. Project Start - 1/6/2017
1.1.1. Project specifications
1.1.2. End User requirements
1.1.3. Action points sign-off
1.2. Weekly Site Meeting
1.2.1. Priorities
1.2.1.1. Top Priorities
1.2.1.2. Medium Priorities
1.2.1.3. Low Priorities
1.2.2. Initiatives
1.2.2.1. Plan vs Actual Progress
1.3. Weekly SteerCo Update
1.4. Project End - 31/12/2017
1.4.1. Project Deliverables
1.4.2. Commisionning/Handover
1.4.3. Lessons Learnt Workshop
2. 5. Resources
2.1. Project Director
2.1.1. Production Manager
2.2. Project Manager
2.2.1. Production Superintendent
2.3. Team Members
2.3.1. Electrical Trade Supervisor
2.3.2. Mechanical Trade Supervisor
2.3.3. 2x Development Personnel
2.3.4. Mining Engineer (consultant)
2.4. Budget - $500k
2.5. Assets
2.5.1. PMO Office on site
2.5.2. Individual Laptops
2.6. Steering Committee
2.6.1. Site General Manager
2.6.2. Coal Managing Director
2.6.3. Coal Sales and Marketing Manager
3. 4. Scope
3.1. Included
3.1.1. Initiate Project
3.1.1.1. Establish Project Team and Resources
3.1.1.2. Brainstorm Project Initiatives
3.1.1.2.1. CM Development downstream & upstream Improvement Opportunities
3.1.1.2.2. CM Development Working Face Improvement Opportunities
3.1.2. Plan Project
3.1.2.1. Establish Project Initiatives Plans
3.1.3. Execution of Project Initiatives
3.1.4. Monitor and Control Project Initiatives
3.1.5. Project Closure
3.2. Excluded
3.2.1. Mining Technical Services Constraints
3.2.1.1. Ventilation
3.2.1.2. Gas
3.2.2. Large Equipment Procurement Costs
3.2.3. Reviewing LW shearer Rates
3.2.4. Cost Benefit Analysis of Cutting LWs Short
4. time
5. Money
6. Project Selection
6.1. Mine B Closure Planning
6.2. CM Improvement Project
6.2.1. The most structured of the three projects (PMO, progress reports, governance structure)
6.2.2. The most lessons to be learned
6.2.3. Project had successes but ultimately failed
6.3. Bankable Feasibility Study Underground Project
7. 2. Project Need
7.1. A LW shearer cannot be installed until the CMs have developed a full coal Panel
7.2. Historical CM advance rates at Mine A are slower than the Industry Benchmark and the Longwall shearer advance rates
7.2.1. Mine A cannot add any more CMs to the operation due to underground mining technical constraints
7.3. At current CM advance rates Mine A will run out of float in 2019 and the LW will not have a new Panel to be installed in
7.3.1. This means that the LW will have to be stopped for 6 months or the planned coal panels will have to be shortened
7.3.2. 6 Months of no LW production will directly cost the business $60M
7.3.3. Cutting the panels short will mean Mine A has to write-off 3.5Mt ($630M at current prices) of coal reserves as the underground area cannot be re-entered
7.4. Mine A has acquired new technology that will allows the LW rates to be increased even further to 10Mt by 2020
8. 1. Background
8.1. Mine A is an underground Longwall (LW) coal mine in Central Queensland Australia.
8.1.1. Mine A produces 6Mt of coking coal per annum and has specific/loyal customers that expect this quantity of coal
8.1.2. 10% of the Mine A Coal comes from Continuous Miner Development and 90% is produced from the Longwall Shearer
8.2. LW coal mining method
8.2.1. Continuous Miners (CMs) - machines with rotating drums on the front with picks - developing roadways to form a large rectangular shaped block of coal (415m wide by 3-9km long).
8.2.2. Once the block of coal (panel) has been fully developed the coal is extracted by, ‘longwalling’.
8.2.3. Longwalling - Hydraulic props provide temporary support along the width (face) of the rectangular block, whilst a large shearer runs back and forth across the face cutting the coal onto a conveyor.
8.2.4. This conveyor system transports the coal to the surface for processing.
9. 3. Objectives
9.1. Goals
9.1.1. To double the CM development advance rates by January 2018
9.1.1.1. To ensure that the Mine A LW panels do not have to be shortened and the LW shearers are not stopped in 2019
9.1.1.2. To create sustainable modification to the CM production process so the 2020 10Mt target can be achieved,
9.1.2. To achieve the objectives within the project time-frame and budget
9.2. Deliverables
9.2.1. Initiative Outcomes
9.2.2. Monitoring and Controlling Processes
9.2.3. Education/Training packages for workforce
9.2.4. Procured Equipment & Management Process
9.2.5. Commisioning Processes
9.2.6. Handover Processes