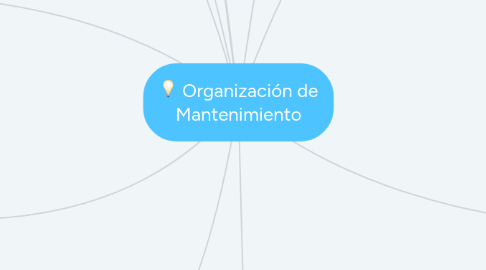
1. Definición de Mantenimiento
1.1. Definimos mantenimiento como el conjunto de técnicas destinado a conservar equipos e instalaciones en servicio durante el mayor tiempo posible (buscando la más alta disponibilidad) y con el máximo rendimiento.
2. Análisis de Equipos
2.1. Hoy en día con la evolución del mantenimiento industrial no se debe pensar que toda una planta debe estar sujeta a un tipo de mantenimiento (por ejemplo, correctivo, o preventivo, etc.). Cada equipo ocupa una posición distinta en el proceso industrial, y tiene unas características propias que lo hacen diferente del resto, incluso de otros equipos similares.
3. Lista de Equipos
3.1. Si queremos elaborar una lista de equipos realmente útil, debemos expresar esta lista en forma de estructura arbórea, en la que se indiquen las relaciones de dependencia de cada uno de los ítems con los restantes.
4. Codificación de Equipos
4.1. Una vez elaborada la lista de equipos es muy importante identificar cada uno de los equipos con un código único. Esto facilita su localización, su referencia en órdenes de trabajo, en planos, permite la elaboración de registros históricos de fallos e intervenciones, permite el cálculo de indicadores referidos a áreas, equipos, sistemas, elementos, etc., y permite el control de costes. Básicamente, existen dos posibilidades a la hora de codificar:
4.1.1. — Sistemas de codificación no significativos: son sistemas que asignan un número o un código correlativo a cada equipo, pero el número o código no aporta ninguna información adicional.
4.1.2. — Sistemas de codificación significativos o inteligentes, en el que el código asignado aporta información.
5. Analisis de Criticidad
5.1. Como los recursos de una empresa para mantener una planta son limitados, debemos destinar la mayor parte de los recursos a los equipos más importantes, dejando una pequeña porción del reparto a los equipos que menos pueden influir en los resultados de la empresa.
5.1.1. A) Equipos críticos. Son aquellos equipos cuya parada o mal funcionamiento afecta significativamente a los resultados de la empresa.
5.1.2. B) Equipos importantes. Son aquellos equipos cuya parada, avería o mal funcionamiento afecta a la empresa, pero las consecuencias son asumibles.
5.1.3. C) Equipos prescindibles. Son aquellos con una incidencia escasa en los resultados. Como mucho, supondrán una pequeña incomodidad, algún pequeño cambio de escasa trascendencia, o un pequeño coste adicional.
6. Selección del Modelo de Mantenimiento
6.1. Si el equipo resulta ser Crítico, el modelo de mantenimiento será alguno de los tres que corresponden a Mantenimiento Programado. Si el equipo es Importante, tendremos que estudiar todavía un poco más las consecuencias de una avería. Si el equipo, por último, es Prescindible, ya sabemos que el modelo que le corresponderá será el Modelo Correctivo.
6.1.1. Modelo Programado
6.1.1.1. Condicional
6.1.1.2. Alta Disponibilidad
6.1.1.3. Sistematico
6.1.2. Modelo predecible
6.1.2.1. Correctivo
6.1.2.2. +Consideraciones
7. Plan de Mantenimiento
7.1. El Plan de Mantenimiento es un documento que contiene el conjunto de tareas de mantenimiento programado que debemos realizar en una planta para asegurar los niveles de disponibilidad que se hayan establecido.
7.1.1. Plan de Mantenimiento basado en RCM
7.1.1.1. Reliability Centered Maintenance, Mantenimiento Basado en Fiabilidad. Es una técnica más dentro de las posibles para poder elaborar un Plan de Mantenimiento
7.1.1.1.1. Mejora en la comprensión del funcionamiento de los equipos.
7.1.1.1.2. Estudio de las posibilidades de fallo de un equipo y el desarrollo de los mecanismos que tratan de evitarlas, ya sean producidas por causas intrínsecas al propio equipo o por actos personales.
7.1.1.1.3. Elaboración de planes que permiten garantizar la operación de los equipos dentro de los parámetros marcados.
8. Objetivos
8.1. Maximizan de la vida de la máquina.
8.2. Evitar, reducir, y en su caso, reparar, las fallas sobre los bienes precitados.
8.3. Disminuir la gravedad de las fallas que no se lleguen a evitar.
8.4. Evitar detenciones inútiles o para de maquinas.
8.5. Evitar accidentes.
8.6. Evitar incidentes y aumentar la seguridad para las personas.
8.7. Conservar los bienes productivos en condiciones seguras y preestablecidas de operación.
8.8. Balancear el costo de mantenimiento con el correspondiente al lucro cesante.
8.9. Alcanzar o prolongar la vida útil de los bienes.
9. Tipos de Mantenimiento
9.1. — Mantenimiento correctivo: Es el conjunto de tareas destinadas a corregir los defectos que se van presentando en los distintos equipos y que son comunicados al departamento de mantenimiento por los usuarios de los mismos.
9.2. — Mantenimiento preventivo: Es el mantenimiento que tiene por misión mantener un nivel de servicio determinado en los equipos, programando las correcciones de sus puntos vulnerables en el momento más oportuno.
9.3. — Mantenimiento cero horas: Es el conjunto de tareas cuyo objetivo es revisar los equipos a intervalos programados bien antes de que aparezca ningún fallo. Dicha revisión consiste en dejar el equipo a cero horas de funcionamiento, es decir, como si el equipo fuera nuevo.
9.4. — Mantenimiento en uso: es el mantenimiento básico de un equipo realizado por los usuarios del mismo. Consiste en una serie de tareas elementales (tomas de datos, inspecciones visuales, limpieza, lubricación, reapriete de tornillos) para las que no es necesario una gran formación, sino tan solo un entrenamiento breve.
10. ¿Cuál es el mantenimiento que debo aplicar a cada uno de los equipos que componen una planta concreta?
10.1. Un modelo de mantenimiento es una mezcla de los anteriores tipos de mantenimiento en unas proporciones determinadas, y que responde adecuadamente a las necesidades de un equipo concreto.
10.1.1. Modelo Correctivo: . Es aplicable, como veremos, a equipos con el más bajo nivel de criticidad, cuyas averías no suponen ningún problema, ni económico ni técnico.
10.1.1.1. • Inspecciones visuales. • Lubricación. • Reparación de averías.
10.1.2. Modelo Condicional: Este modelo de mantenimiento es válido en aquellos equipos de poco uso, o equipos que a pesar de ser importantes en el sistema productivo su probabilidad de fallo es baja
10.1.2.1. • Inspecciones visuales. • Lubricación. •Mantenimiento Condicional. • Reparación de averías.
10.1.3. Modelo Sistemático: Este modelo incluye un conjunto de tareas que realizaremos sin importarnos cuál es la condición del equipo; realizaremos, además, algunas mediciones y pruebas para decidir si realizamos otras tareas de mayor envergadura; y, por ultimo, resolveremos las averías que surjan. Es un modelo de gran aplicación en equipos de disponibilidad media, de cierta importancia en el sistema productivo y cuyas averías causan algunos trastornos.
10.1.3.1. • Inspecciones visuales. • Lubricación. •Mantenimiento Preventivo Sistemático. •Mantenimiento Condicional. • Reparación de averías
10.1.4. Modelo de alta Disponibilidad: Se aplica en aquellos equipos que bajo ningún concepto pueden sufrir una avería o un mal funcionamiento. En esta revisión se sustituyen, en general, todas aquellas piezas sometidas a desgaste o con probabilidad de fallo a lo largo del año (piezas con una vida inferior a dos años). Estas revisiones se preparan con gran antelación, y no tiene por qué ser exactamente iguales año tras año.
10.1.4.1. • Inspecciones visuales. • Lubricación. • Reparación de averías. • Mantenimiento Condicional. • Mantenimiento Sistemático. • Puesta a cero periódica, en fecha determinada (Parada).
10.1.5. Otras Consideraciones: En primer lugar, algunos equipos están sometidos a normativas legales que regulan su mantenimiento, obligando a que se realicen en ellos determinadas actividades con una periodicidad establecida. En segundo lugar, algunas de las actividades de mantenimiento no podemos realizarlas con el equipo habitual de mantenimiento (sea propio o contratado) pues se requieren de conocimientos y/o medios específicos que solo están en manos del fabricante, distribuidor o de un especialista en el equipo.
11. No existe una estructura óptima para un tipo dado de organización. Lo que resulta adecuado para una es posible que lo sea para otra. Las organizaciones pequeñas normalmente están estructuradas funcionalmente (centralizadas), mientras que las de tamaño mediano se inclinan por estructuras divisionales (descentralizadas) y las grandes generalmente optan por unidades estratégicas de negocio o por estructuras matriciales.
11.1. Según la norma COVENIN ISO 3049
11.1.1. Mantenimiento de Área:
11.1.1.1. Subdivide a Sistema Productivo en varias partes geográficas y a cada una de ellas se asignan cuadrillas de personal para ejecutar las acciones de mantenimiento. Su objetivo es aumentar la eficiencia operativa, ya que estas pequeñas organizaciones se sitúan en las proximidades de los sistemas a los cuales sirven. Se caracteriza por: mayor y mejor control de personal por área, personal especializado en el área de trabajo, aumento de costos por especialización funcional, mayor fuerza laboral, programación y prevenciones más ajustadas a la realidad, sistemas de información más complejos y recomendables para el Sistema Productivo suficientemente grandes en distribución geográfica, diversidad de procesos y de personal.
11.1.2. Mantenimiento Centralizado:
11.1.2.1. Es la concentración de los recursos de mantenimiento en una localización central. Se caracteriza por: Transferencia de personal de un lugar a otro donde exista necesidad de mantenimiento, personal con conocimiento del Sistema Productivo a mantener, bajo nivel de especialización en general comparado con el de área, reducción de costos por la poca especialización funcional; en emergencia se adecentar con todo el personal y se recomienda para Sistemas Productivos medianos a pequeños y con poca diversidad de procesos.
11.1.3. Mantenimiento Área Central:
11.1.3.1. Se aplica e macro Sistemas Productivos, los cuales tienen organizaciones en situaciones geográficas alejadas, cantidades elevadas de personal y diversidad de procesos. En este tipo de entes organizacionales cada área tiene su organización de mantenimiento, pero todas manejadas bajo una administración central. Independientemente del tipo de estructura de organización de mantenimiento requerida, se deben tener en cuenta como principios fundamentales el factor costo implicado, tipo de persona necesario y diversidad de procesos
11.2. Niveles Jerárquicos de una Organización de Mantenimiento:
11.2.1. Nivel 1: Dirección y Gerencia
11.2.2. Nivel 2: Supervisión y Apoyo.
11.2.3. Nivel 2.1: Supervisión y Control de ejecución de acciones de mantenimiento
11.2.4. Nivel 2.2: Apoyo logístico a la función de mantenimiento: Planificación, Diseño, Programación, Almacén, Automatización entre otros.
11.2.5. Nivel 2.3: Mantenimiento de Taller
11.2.6. Nivel 3: Supervisión y Ejecución de acciones de mantenimiento para cada área específica.
11.2.7. Nivel 4: Ejecución propiamente dicha de acciones de mantenimiento