Balanceo de Línea
por Daniela Fuentes Rdz
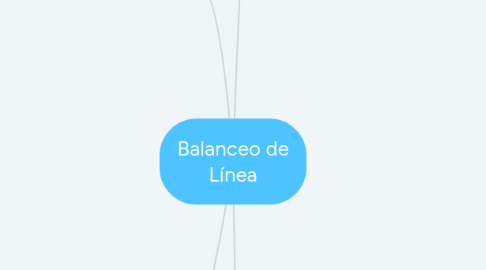
1. Método de Kibridge & Wester
1.1. Este método se enmarca dentro de Planeación y control de la producció, cuyo problema fundamental responde a: · División del trabajo en operaciones o tareas · Asignación de las tareas a estaciones u operarios · Cumplir con las restricciones del proceso.
1.2. Está conformado por 3 objetivos los cuales son: *Determinar el número de operarios * Minimizar ocio * Distribuir de forma equitativa las cargas de trabajo
1.3. Estrategia basada en la tarea: - Se mira las tareas que se pueden asignar por sus relaciones de precedencia. - Se asigna la más prioritaria a la estación que más temprana o una nueva
1.4. Estrategia basada en la estación: - Se mira las tareas que se pueden asignar por sus relaciones de precedencia - Por orden de prioridad se mira a la primera que pueda entrar en la estación - Si ninguna puede entrar en la estación actual, se crea una nueva estación
2. 1.- Conceptos generales de balanceo de lineas
2.1. concepto
2.2. El balanceo de línea es una de las herramientas más importantes para el control de la producción, dado que de una línea de fabricación equilibrada depende la optimización de variables tales como los son los inventarios de producto en proceso, los tiempos de fabricación y las entregas parciales de producción.
2.3. objetivo
2.4. Igualar los tiempos de trabajo en todas las estaciones del proceso.
2.5. Condiciones
2.6. * Cantidad: El volumen o cantidad de la producción debe ser suficiente para cubrir la preparación de una línea. * Continuidad: Deben tomarse medidas de gestión que permitan asegurar un aprovisionamiento continuo de materiales, insumos, piezas y sub-ensambles.
3. 2. Descripción y aplicación de métodos para el balanceo de líneas de producción
3.1. Método de peso posicional
3.2. concepto
3.3. Consiste en intentar que todas las estaciones de trabajo tengan aproximadamente la misma carga de trabajo con el objetivo de minimizar los tiempos inactivos.
3.4. Pasos para el proceso de balanceo
3.5. 1.- Descomposición de las tareas:
3.6. 2.- Determinación de la capacidad de la línea y cálculo del tiempo de ciclo:
3.6.1. Tc(minutos/unidad)= 60 (Minutos/Hora) / Q (Unidades/Hora)