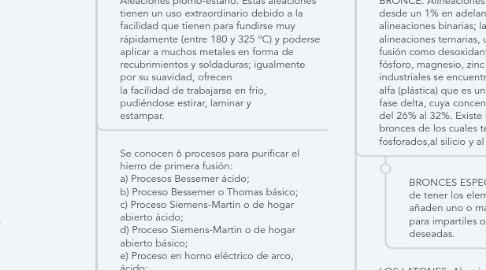
1. Metalurgia no ferrosa
1.1. propiedades y aplicaciones del aluminio, antimonio, cobre, estaño, magnesio, plomo níquel y zinc
1.1.1. ALUMINIO. Este metal es el más abundante en la corteza terrestre, tiene minerales de obtención como: la bauxita y la criolita, estas contienen impurezas que se purifica como por ejemplo la electrolisis.
1.1.1.1. Propiedades:El aluminio es un metal blanco plateado y brillante en estado de alta pureza, con mayor resistencia a la corrosión que el comercial. Es bastante dúctil y maleable. Su conductividad, a pesos iguales es casi el doble de la del cobre y el ácido sulfúrico lo ataca velozmente; el ácido clorhídrico lo disuelve rápidamente en cualquier proporción.
1.1.1.1.1. Aplicaciones:Se utiliza grandemente en las industrias de fabricación de vehículos o transportes en general tales como aviones, ferrocarriles, de automóviles, motores eléctricos y de combustión, muebles, construcciones de edificios, barras, remaches, perfiles, láminas para techar y forrar. En la Industria química y alimenticia para equipos que comprenden: cambiadores de calor, condensadores, destiladores, evaporadores, válvulas etc. En la industria de la pintura, en forma de polvo, se utiliza como pigmento para recubrimientos anticorrosivos.
1.1.2. COBRE. se encuentra en la naturaleza formando numerosos compuestos que en resumen son: minerales sulfurados y minerales oxidados.
1.1.2.1. Minerales sulfurados:La calcopirita o chalcopirita y la calcocita o chalcocita. Minerales oxidados:La cuprita, la malaquita y la azurita. Los procesos metalúrgicos que modernamente se llevan a cabo para la extracción del cobre a partir de sus minerales concentrados son: fusión, conversión y refinación.
1.1.2.1.1. Propiedades: es un metal de color rojo característico, muy maleable y dúctil en estado de alta pureza. Posee una elevada conductividad térmica y eléctrica, esta última, solo superada por la plata.
1.1.3. ESTAÑO.estaño es casiterita, SnO2, bióxido de estaño, conocido también como piedra de estaño y esta tiene mayor pureza. Contiene algunas impurezas y por lo tanto deberá ser purificado o refinado, sea por fusión o por electrólisis.
1.1.3.1. Propiedades: metal de color blanco grisáceo parecido al de la plata; es menos pesado que el plomo, pero más duro; funde a 232 °C. Es suave, dúctil y maleable, pero muy poco resistente a la tracción, o sea casi carece de tenacidad.
1.1.3.1.1. Aplicaciones: se utiliza para el recubrimiento de piezas y artículos fabricados en hierro y cobre, por ejemplo: la hoja de lata, alambres y cables de cobre para intemperie; tubos para dentífricos.Como elemento aleado, forma parte de numerosas aleaciones: soldaduras.
1.1.4. MAGNESIO. Es abundan en todo el mundo, tanto en la corteza terrestre, como en el agua de mar. Minerales obtención: Dolmita, Magnesita y Garnalita. Existen varios métodos de obtención del magnesio; uno de ellos es el ELECTROLÍTICO, a partir del cloruro de magnesio fundido, operando la electrólisis a 700 °C.
1.1.4.1. Propiedades: es un metal de color blanco plateado brillante; el más liviano de los metales usados en la ingeniería; es laminable entre 350° y 400° C, si se le calienta en el aire arriba de 650 °C. Es soluble en los ácidos minerales diluidos, exceptuando el ácido fluorhídrico.
1.1.4.1.1. Aplicaciones: se usan muchísimo en la fabricación de aviones y equipo de transporte general, equipo textil, de maniobra, moldes livianos para concreto y productos estructurales, como desoxidante y desgasificante en el vaciado de otros metales y aleaciones.
1.1.5. NÍQUEL. la mayor parte del níquel se encuentra en el magma terrestre.Los minerales de extracción del níquel más socorridos son: sulfuros y silicatos.
1.1.5.1. PROPIEDADES. es un metal blanco ligeramente pando y brillante; es duro y muy tenaz; cuando contiene una pequeña cantidad de carbono, se vuelve maleable, dejándose laminar; también es dúctil, muy resistente a la corrosión atmosférica y aleado al hierro le imparte gran resistencia a la oxidación.
1.1.5.1.1. Aplicaciones: Se emplea en la fabricación de aleaciones ferrosas y no ferrosas; aceros resistentes al calor y a la corrosión; aceros inoxidables, austeníticos y ferríticos de igual manera para partes de motores de combustión interna, por ejemplo: monoblockes de automóviles, etc.
1.1.6. PLOMO. metal se encuentra en casi todo el mundo formando compuestos. Sus principales minerales de extracción son: Galena, PbS, sulfuro de plomo, es el principal y más abundante por ultimo Cerusita.
1.1.6.1. Propiedades: es un metal de color gris azulado muy brillante recién cortado es el más pesado; muy suave y menos tenaz; se razga fácilmente con la uña estando muy puro. Su elevada plasticidad le permite ser trabajado fácilmente en frío. Se disuelve en el ácido nítrico diluido. El ácido sulfúrico concentrado y a temperatura ambiente no lo ataca; pero lo disuelve rápidamente en caliente.
1.1.6.1.1. Aplicaciones: se utiliza preferentemente para la fabricación de tuberías, drenajes y accesorios para los mismos; en forma de láminas y tiras para recubrimientos de cables telefónicos, eléctricos, subterráneos o aéreos.
1.1.7. ZINC. Este metal nunca se encuentra en estado nativo por causa de su actividad química. Sus principales minerales de obtención son: Blenda o esfalerita, ZnS, sulfuro de zinc; es el mineral mas abundante.Calamina o Smitsonita, carbonato de zinc.
1.1.7.1. Propiedades: El zinc es un metal de color blanco azulino; funde a 419 °C y hierve a 907 °C. Cristaliza en la red hexagonal compacta; es frágil o dúctil según la velocidad de enfriamiento. El zinc a temperatura ambiente por lo general es frágil; cuando se le calienta entre 100 y 150 °CJ se vuelve dúctil y maleable dejándose estirar fácilmente en láminas y alambres.
1.1.7.1.1. Aplicaciones: El principal uso del zinc está en el proceso conocido como galvanizado, particularmente a productos del hierro. En forma de lámina el zinc se utiliza para techar; forrar tanques, mesas y para fabricar tubos; asimismo se utiliza en la fabricación de baterías o pilas secas; láminas y placas para fotograbados.
2. Metalurgia no ferrosa
2.1. El hierro es el elemento más económico y el más usado en el ramo de la ingeniería y por lo tanto, el más importante en la era actual.
2.1.1. Los principales minerales de obtención son: Hematita, Fe203, sesquióxido de hierro; es el principal y el más abundante. Magnetita, Fe304, óxido ferroso-férrico, se encuentra en abundancia en los casquetes polares. Siderita, FeC03, carbonato de hierro; es poco abundante.
2.1.2. DESCRIPCIÓN Y FUNCIONAMIENTO DE UN ALIO HORNO. Un alto horno es una gran construcción cilindrica vertical entre 45 y 70M. de alto y hasta 12M. de diámetro, montada sobre una fuerte construcción a base de hormigón; el cilindro que es una chapa de placas de acero está forrado interiormente con ladrillos refractarios neutros formando un par de conos truncados.
2.1.2.1. El encendido de un alto horno consiste en cargarlo con carbón de coque y algo de piedra caliza desde el piso de crisol hasta cerca del vientre. Una vez el coque en estado incandescente (cama), es cubierto por capas de mineral en forma de pellets. Una vez disparado el aire caliente, la operación se hace continua pudiendo durar interrumpidamente entre unos tres o cinco años cuando el horno.El aire caliente que se inyecta entre 800 y 900 ° C proviene de unas estufas precalentadoras o recuperadoras de calor (4 por lo general; 2 en servicio y 2 de emergencia). Los gases capturados del alto horno, después de ser desempolvados y lavados, se mezclan con aire u oxígeno y se queman dentro del emparrillado de una estufa, hasta que los ladrillos se calienten al rojo vivo. En resumen, la operación continua de un alto horno, una vez puesto en marcha consiste en insuflar aire caliente a través de las toberas y alimentarlo por el tragante con cargas preparadas y coque.
2.1.2.1.1. Manganeso. Durante la preparación del mineral y la elaboración de los pellets, el manganeso se agrega en forma de mineral (MnOs) el cual es reducido a manganeso puro y contrarresta el efecto indeseable del azufre sobre el hierro.
2.1.2.1.2. Fósforo. Proviene de la reducción de los fosfatos que contienen casi todos los minerales del hierro; también lo contienen a veces los fundentes y el coque, aunque en pequeñas cantidades.
2.1.2.1.3. El azufre. Lo suministra el carbón de coque; también puede provenir de los minerales que al tostarse, no se eliminó totalmente; puede escorificarse parcialmente a elevadas temperaturas procurando que la escoria sea muy básica.
2.1.2.1.4. El silicio. Proviene de la reducción de los materiales silicosos que siempre acompañan a los minerales y a las cenizas del carbón de coque; esta reducción sólo tiene lugar a muy elevadas temperaturas.
2.1.3. Los productos del alto horno son: hierro fundido; escoria; gases y polvos. El hierro fundido se colecta en el crisol de donde es extraído durante cada 5 a 8 horas y puede ser conducido en forma de arroyo a un tablar de lingoteras de arena sobre el suelo donde se deja enfriar. La escoria se colecta en unas ollas puestas sobre unas vagonetas y es transportada a otros lugares para su aprovechamiento.La escoria del alto horno tiene muchos usos: como material de relleno en el concreto; en pavimentación etc. El gas de alto horno se utiliza principalmente como combustible después de separados los polvos y lavado, quemándose en las estufas precalentadoras del aire.Los polvos y humos que arrastran los gases son retenidos en unos colectores especiales mediante una precipitación electrostática.
3. Fabricación de aceros
3.1. Aceración es el resultada de la separación de las impurezas indeseables que contiene el arrabio.La eliminación de las impurezas se realiza por medio de la oxidación.Son varios los procesos que se llevan a cabo para efectuar esta oxidación.
3.1.1. Aceros para Herramientas. son aquellos que soportan las principales operaciones mecánicas así como las condiciones físicoquímicas inherentes a las cuales, una herramienta va a estar sujeta. Son 5 los principales tipos de operaciones en los cuales los aceros para herramientas son usados: corte, conformado, extrusión, laminado y troquelado.
3.1.1.1. La selección de los aceros para herramientas se lleva a cabo por los expertos en herramientas o personas idóneas en la materia. las necesidades requeridas durante su aplicación y para ello, son básicos los puntos siguientes: a) ' 'Diseño apropiado de la herramienta''; b) "Precisión al hacer la herramienta''; c) " Selección del acero para herramientas''; d) ' 'Tratamiento térmico adecuado''.
3.1.1.1.1. Los elementos especialmente aleados de los aceros para herramienta. El aluminio Se usa como desoxidante; de 1% en adelante, impide el crecimiento del grano durante el tratamiento térmico; es el principal elemento de los aceros de nitruración. El cobalto desde 0.3% aumenta la dureza de los aceros a la temperatura. El cromo desde 0.5% imparte cierta resistencia a elevada temperatura; aumenta y profundiza la dureza; incrementa la resistencia a la corrosión y a la abrasión, especialmente a los aceros de alto carbono. El manganeso desde 0.5%, se considera como elemento especial; impide la fragilidad que causa el azufre; aumenta la penetración de dureza y tiende a bajar la temperatura de endurecimiento del acero. El molibdeno desde 0.15% profundiza el endurecimiento; aumenta la resistencia al desgaste y dureza al rojo y contrarresta la tendencia de agrietamiento del acero durante el tratamiento térmico, particularmente en herramientas de diseño intrincado. El níquel desde 0.5% fortalece al acero recocido o no templado; imparte tenacidad y resistencia a la fatiga a temperaturas ordinarias y bajas; aumenta la resistencia a la corrosión y mejora las propiedades de maquinado en los aceros de corte libre. El silicio se usa como desoxidante; desde 0.6% aumenta la penetración de dureza, resistencia a la oxidación y tenacidad de los aceros, especialmente en presencia del manganeso, cromo o molibdeno. El titanio desde 0.05% vigoriza al acero y baja la tendencia de endurecimiento del mismo al aire.
4. Aleaciones a base de plomo
4.1. Aleaciones plomo-estaño. Estas aleaciones tienen un uso extraordinario debido a la facilidad que tienen para fundirse muy rápidamente (entre 180 y 325 °C) y poderse aplicar a muchos metales en forma de recubrimientos y soldaduras; igualmente por su suavidad, ofrecen la facilidad de trabajarse en frío, pudiéndose estirar, laminar y estampar.
4.2. Se conocen 6 procesos para purificar el hierro de primera fusión: a) Procesos Bessemer ácido; b) Proceso Bessemer o Thomas básico; c) Proceso Siemens-Martin o de hogar abierto ácido; d) Proceso Siemens-Martin o de hogar abierto básico; e) Proceso en horno eléctrico de arco, ácido; f) Proceso en horno eléctrico de arco, básico.
4.2.1. En cualquiera de los procesos mencionados sufren reacciones, ejemplo En el proceso ácido el carbono se elimina como COS que es un gas; el Mn y el Si forman óxidos no volátiles.
4.3. Metales para baterías ácidas. Estas aleaciones contienen entre 5 y 12% de antimonio y se vuelven más fluidas cuando contienen además hasta 0.5% de estaño y se utilizan mucho en el vaciado de las rejillas o placas de acumuladores ácidos. Se vacían entre 425 y 500 °C. Metales para baterías ácidas. Estas aleaciones contienen entre 5 y 12% de antimonio y se vuelven más fluidas cuando contienen además hasta 0.5% de estaño y se utilizan mucho en el vaciado de las rejillas o placas de acumuladores ácidos. Se vacían entre 425 y 500 °C.
4.4. Metales para caracteres de imprenta. Son aleaciones de plomoantimonio-estaño similares en composición a las usadas en los metales antifricción ya vistos con anterioridad.Los metales o tipos de metales más usados en trabajo de impresión son los siguientes: 1. Metal para monotipo; 2. Metal para linotipo; 3. Metal para estereotipo; 4. Metal para electrotipo.
4.5. Metal para monotipo. Es la aleación de plomo-antimonio-estaño usada para vaciar los tipos libres o sueltos para imprimir en máquinas tipográficas. para diversas impresiones. Los tipos más usados son: tipos para espacios blancos, tipo regular, pequeño, mediano, grande, tipo desplegado duro, etc
4.6. Metal para linotipo. Es la aleación de plomo-antimonio-estaño usada para preparar líneas enteras para imprimir en máquinas tipográficas directamente sobre papel.
4.7. Metal para estereotipo. Es la aleación de plomo-antimonio-estaño para imprimir planas enteras o fracciones, con extraordinaria nitidez, los más leves pormenores del molde, teniendo la dureza necesaria para llevar a cabo la reproducción con gran fidelidad de un sinnúmero de copias de impresión.
4.8. Metal para electrotipo. Es la aleación a base de plomo-antimonio-estaño usada en forma de placa en las cuales, se electrodeposita una ligera película de cobre en la que se realiza el electrotipo.
5. Aleaciones a base de cobre
5.1. BRONCE. Alineaciones de cobre y estaño, desde un 1% en adelante, también a otras alineaciones binarias; las mas usuales alineaciones ternarias, utilizando durante la fusión como desoxidantes: aluminio, arsénico, fósforo, magnesio, zinc etc. e los bronces industriales se encuentran dos fases: la fase alfa (plástica) que es una solución solida y la fase delta, cuya concentración de estaño va del 26% al 32%. Existe una variedad de bronces de los cuales tenemos: Bronces fosforados,al silicio y al aluminio.
5.1.1. BRONCES ESPECIALES. Aquellos aparte de tener los elementos Cu y Sn, se le añaden uno o mas elementos apropósito, para impartiles otras caracteristicas muy deseadas.
5.2. LOS LATONES. Aleaciones formada a base de cobre y zinc, estos se clasifican principalmente en dos grupos el primero a que que se puede trabajar fácilmente en frió y el segundo aquellos que poseen menor ductibilidad, caracterizándose en ser buenos materiales para trabajarse en caliente.
5.2.1. LATONES ESPECIALES. aquellos que ademas de contener zinc se agregan otros elementos para cambiar sus propiedades, entre los elementos mas usuales son el estaño, plomo, níquel.
5.3. ALEACIONES CUPRONIQUEL
5.3.1. El níquel y el cobre origina una cadena de soluciones solidas en las que las temperaturas se elevan, proporcionalmente al aumentar el contenido del níquel, a medida que aumenta el porcentaje de níquel en el cobre este va disminuyendo su color hasta alcanzar un tono rosado tuene, cuando la aleación contiene alrededor del 15-20% de níquel las aleaciones son variadas.
5.3.1.1. Algunas aleaciones: Metal mol,Aleación constatan, Metal blanco o plata alemana,
6. Aleaciones a base de aluminio
6.1. Estas aleaciones se separan en dos grupos generales que son: aleaciones de forja y aleaciones de vaciado.
6.1.1. Aleaciones de forja: se agrupan de acuerdo con el constituyente aleado principal, a su vez se clasifican aleaciones termicamente tratables y aleaciones no tratables termicamente.
6.1.1.1. Las aleaciones no tratadas termicamente se logran 5 tipos de dureza: reconocido total, medio duro, tres cuartos, totalmente duro y duro como trabajo.
6.1.2. Aleaciones para vaciado: a cada grupo de estas aleaciones se le ah designado una expresión numérica por ejemplo: aluminio-silicio(100-199) aluminio-cobre(200 a 299) etc. todas estas aleaciones puede ser vaciada en cualquier tipo de vaciado.
7. Métodos de fabricación de aleaciones
7.1. Aleaciones de alnico. Son aleaciones de aluminio - níquel - cobalto - hierro con 8 a 12% de aluminio, del 14 al 18% de níquel y 5 l 35% de cobalto con elevadores de propiedades magneticas.
7.1.1. Todos los Alnicos como imanes de tierras raras son fragile
7.2. Metales preciosos aquellos metales que se encuentran en estado libre en la naturaleza, es decir, que no se encuentran de manera combinados con otros elementos formando compuestos.
7.2.1. hay diferetes tipo de aleaciones
8. Aleaciones a base de magnesio
8.1. El magnesio es un elemento muy abundante y su principal fuente de obtención se encuentra en el agua de mar. este elemento forma aleaciones con su mayoría de los metales excepto el cromo y hierro.
8.1.1. Las aleaciones de magnesio pueden ser utilizadas en la mayoría de los procesos estirado, forjado, estampado maquinado, así mismo pueden vaciarse en arenas de moldeo.