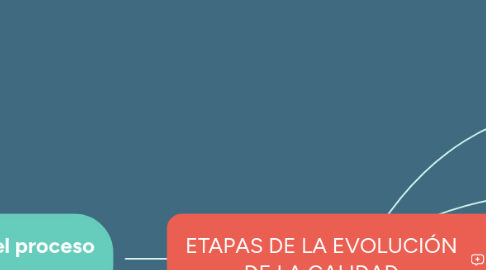
1. Antes de la inspección
1.1. Al comienzo no había procesos de manufactura ni garantías, así que se protegían al momento de realizar la inspección y con un estrecho contacto con el productor
1.2. Los productos eran únicos y hechos para satisfacer las necesidades del cliente
1.3. No habían competencias entre productores
1.4. Ventaja
1.4.1. Era mas sencillo llegar a la calidad de conformancia y satisfacer al cliente
1.5. Desventaja
1.5.1. - Cuando surgió el mercado, vino la separación entre el productor y el usuario
2. Etapa de inspección
2.1. Los primeros procesos organizados se enfocaron, al principio, en proyectos de construcción, los cuales requerían gran cantidad de hombres y trabajos especializados.
2.2. La Revolución Industrial hizo posible una enorme expansión de los procesos de manufactura y de los bienes de consumo
2.3. Los problemas de calidad que se resolvieron fueron técnicos sobre todo y los que aparecieron fueron administrativos y humanos.
2.4. La etapa de inspección se desarrolló durante el auge industrial.
2.4.1. La etapa de inspección, según Bounds et al. (1994), se caracterizó por la detección y solución de los problemas generados por la falta de uniformidad del producto.
2.4.2. Buscar que un producto reúna los atributos de calidad que desea el cliente ha sido una realidad desde la época artesanal.
2.4.3. Con el advenimiento de la era industrial apareció la producción masiva, y con ella la imposibilidad del contacto directo entre el fabricante y el usuario.
2.4.4. A principios del siglo XX, la inspección por estándares se refinó aún más y fue clave en la línea de ensamble de Henry Ford y en el sistema administrativo propuesto por Frederick W.
2.4.5. Taylor. Radford (1922) vincula formalmente la inspección al control de calidad, y por primera vez la calidad es considerada una responsabilidad independiente de la administración.
2.4.6. Durante toda la década de 1920 se limitó a contar y detectar la mala calidad.
3. Etapa del control estadístico de la calidad
3.1. En 1931 Walter A. Shewhart, de Bell Telephone Laboratories, dio un fundamento científico a la calidad mediante la publicación del libro Economic Control of Quality of Manufactured Product. En este texto se dieron a conocer las cartas de control y el estudio de la calidad a través de variables, las cuales es necesario estudiar
3.2. Entre 1943 y 1945, un total de 810 organizaciones enviaron representantes al curso sobre control estadístico de calidad, impartido por la Office of Production Research and Development. Las personas que prepararon este curso fueron el doctor W. Edwards Deming (discípulo de Shewhart) y los profesores Eugene L. Grant y Holbrook Working (Duncan, 1989).
3.3. El conocimiento y las metodologías sobre la calidad que se habían logrado desarrollar en Estados Unidos hasta esas fechas empezaron a trasladarse a Japón, un país derrotado y devastado por la Segunda Guerra Mundial.
4. Control estadístico del proceso (década de 1930)
4.1. Estadístico se entendía la calidad como un problema de variación que puede ser controlado y prevenido mediante la eliminación a tiempo.
4.2. La etapa se desarrolló durante la inspección dejó de ser masiva.
4.2.1. La etapa de inspección según Walter Shewhart (1891-1967) se caracteriza por los principales personajes de esta época, entendía la calidad como un problema de variación que se podía controlar y prevenir.
4.2.2. Busca que una producción pudiese cumplir con la tolerancia de especificación de su diseño, sin tener que esperar a que el producto estuviera terminado para corregir las fallas y lograr este objetivo, Shewhart ideó las gráficas de control.
5. Etapa del aseguramiento de la calidad (década de 1950)
5.1. En la etapa de aseguramiento de la calidad se reconoce que la calidad no sólo depende de los procesos de manufactura, sino que requiere servicios de soporte, por lo cual se deben coordinar esfuerzos entre las áreas de producción y diseño de producto, ingeniería de proceso, abastecimiento, laboratorio, etcétera.
5.2. A principios de la década de 1950, Joseph M. Juran (1989) impulsó el concepto del aseguramiento de calidad, el cual se fundamenta en que el proceso de manufactura requiere servicios de soporte de calidad; por ello, se debían “coordinar esfuerzos entre las áreas de producción y diseño del producto, ingeniería de proceso, abastecimiento y laboratorio, entre otras”.
5.3. Para Juran, la calidad consiste en “adecuar las características de un producto al uso que le dará el consumidor”.
5.4. La competitividad de la industria japonesa fue ganando terreno hasta convertirse en líder en varias ramas industriales, como se señala a continuación:
5.4.1. En 1970, los países occidentales participaron en el mercado mundial declinó y hubo necesidad de cerrar plantas en occidente debido a la competencia de Japón. El diagnóstico de occidente fue que tal pérdida de competitividad se debía al bajo costo de la mano de obra en Japón (Goldratt y Fox, 1992).
5.4.2. En 1975, los países occidentales perdieron el liderazgo en aparatos electrodomésticos. Además de la mano de obra barata, se añadieron nuevos elementos para explicar esto: el dumping y el plagio (Goldratt y Fox, 1992).
5.4.3. Es a finales de la década de 1970 cuando la competencia de los productos japoneses empieza a provocar alarma en la industria orgullo de Estados Unidos: la automotriz. En 1980, se prenden los “focos de alarma” en este país por la competencia de los productos orientales e inician la investigación de cómo éstos lograron conquistar los mercados internacionales.
5.4.4. En mayo de 1980, la cadena de televisión estadounidense NBC transmitió un programa titulado “Si Japón puede, ¿por qué nosotros no?”, que explicaba a los estadounidenses las ventajas del control de calidad japonés. Es a raíz de este documental que el doctor Deming se hizo conocido en los medios empresariales de Estados Unidos.
5.4.5. En febrero de 1981, un total de 30 ejecutivos de Ford se reunieron con E. Deming, convencidos de que sus problemas se localizaban en alguna parte específica del proceso.
5.4.6. A mediados de la década de 1980, Japón asume el liderazgo en electrónica, en la producción de microchips (Goldratt y Fox, 1992). Es decir que, desde 1950, se venían haciendo las tres actividades fundamentales por la calidad: innovación, control y mejora.
5.4.7. En Estados Unidos apareció un movimiento muy importante por la calidad, conocido como Zero Defects, que se enfocaba en elevar las expectativas de la administración, así como en motivar y concientizar a los trabajadores por la calidad de “promover un constante y consciente deseo de hacer el trabajo bien a la primera vez” (Halpin, 1966).