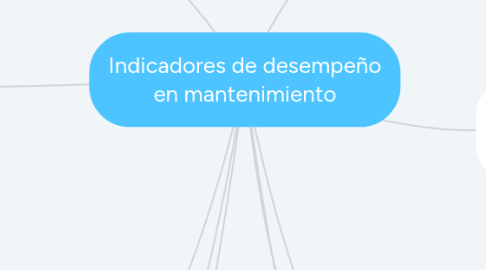
1. MTTR (Mid Time To Repair, tiempo medio de reparación)
1.1. Nos permite conocer la importancia de las averías que se producen en un equipo considerando el tiempo medio hasta su solución.
2. Número de Órdenes de trabajo generadas en un periodo determinado
2.1. Es discutible si el número de órdenes de trabajo es un indicador muy confiable de la carga de trabajo en un período, ya que se pueden combinar 100 órdenes de trabajo de una hora en una orden de trabajo con un concepto más amplio. Sin embargo, dada la sencillez de obtención de estos datos, suele ser un indicador muy utilizado. Cuanto más representativa sea la información proporcionada por este indicador, mayor será la O.T media producida por la planta. Por lo tanto, es fácil producir menos de 100 O.T. El mantenimiento mensual de la efectividad de este indicador es menor que el que una fábrica produce 1000 O.T.
3. Número de Órdenes de trabajo de Emergencia (prioridad máxima)
3.1. Una referencia muy importante para el estado de la fábrica es el número de O.T de emergencia generadas en un período de tiempo determinado. Si hay poco o nada, nos aseguraremos de que el estado de la fábrica sea confiable. Por otro lado, si se generan muchos pedidos de máxima prioridad, se puede considerar que el estado de la fábrica no es bueno. Como siempre, es igualmente importante observar la evolución de este indicador en comparación con períodos anteriores.
4. Proporción de coste de la Mano de Obra de Mantenimiento
4.1. Es el cociente de dividir el nº total de horas empleadas en mantenimiento entre el coste total de la mano de obra
5. Rotación del Almacén
5.1. Es el cociente de dividir el valor de los repuestos consumidos totales y el valor del material que se mantiene en stock(valor del inventario de repuestos)
5.1.1. Hay una variación interesante de este índice, cuando se pretende determinar si el stock de repuestos y consumibles está bien elegido. Si es así, la mayor parte del material que consume mantenimiento lo toma del almacén, y solo una pequeña parte de lo comprado es de uso inmediato
6. Disponibilidad total
6.1. Sin duda, es el indicador más importante en mantenimiento y, por supuesto, el indicador que tiene más probabilidades de ser "controlado". Si el cálculo es correcto, es simple: es el cociente de la cantidad de horas que un equipo puede producir dividido por la cantidad total de horas en un período.
6.1.1. Los equipos no están dispuestos en línea, es interesante definir una serie de equipos importantes, porque lo cierto es que calcular la disponibilidad de absolutamente todos los equipos será largo y laborioso y no nos proporcionará información valiosa. Entre el total de equipos de la fábrica, debemos seleccionar aquellos que tengan cierta entidad o importancia en el sistema de producción.
7. MTBF (Mid Time Between Failure, tiempo medio entre fallos)
7.1. Nos permite conocer la frecuencia con que suceden las avería.
8. Índice de cumplimiento de la planificación
8.1. Aunque el uso de este indicador es muy lógico, pocas fábricas lo implementan
9. Índice de Mantenimiento Programado
9.1. Es la suma de todos los medios auxiliares que ha sido necesario alquilar o contratar: grúas, carretillas elevadoras, alquiler de herramientas especiales, etc.
9.1.1. Con todos los índices referentes a costes puede prepararse una Tabla de Costes, como la que se muestra en la figura adjunta. En ella pueden visualizarse con rapidez todos gastos de mantenimiento de la planta, divididos en conceptos y en secciones. Presentarlos de esta manera facilitará su lectura y la toma de decisiones consecuente