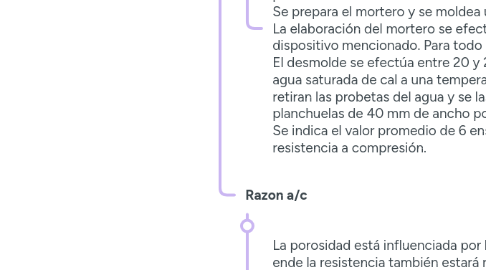
1. Fabricacion del Cemento
1.1. 4 etapas
1.1.1. Proceso Mecanico: Obtencion de la harina cruda
1.1.1.1. Ensayos
1.1.1.1.1. Estandar de cal
1.1.1.1.2. Modulo de silicio
1.1.1.1.3. Modulo Fundente
1.1.2. Produccion del clinker
1.1.2.1. Torre de precalenteamiento (Ciclones)
1.1.2.2. Muestras
1.1.2.3. Horno rotatorio
1.1.2.4. Enfriamiento rapido (parrillas)
1.1.2.5. Acopio
1.1.3. 2do Proceso mecanico
1.1.3.1. Incorporacion de YESO
1.1.3.1.1. El yeso se le agrega al clínker para modificar el fraguado del cemento y poder asi trabajar el hormigón. El retraso se produce por la reacción química entre el aluminato tricálcico y el regulador, ya que este sin éste fraguaría rápidamente. Por lo tanto, la cantidad de regulador a agregar es función de la cantidad de aluminato tricálcico presente en el clinker.
1.1.3.2. Molienda
1.1.4. Despacho
2. Requerimientos para cementos de uso general
2.1. Fisicos
2.1.1. Finura
2.1.1.1. Es una propiedad del cemento que esta relacionada con el tamaño de las partículas y su importancia radica en que la hidratación comienza sobre las superficies de las partículas, determinando la tasa de hidratación. Influye sobre la velocidad de hidratación, las propiedades reológicas y el desarrollo de la resistencia del cemento.
2.1.1.1.1. La finura favorece el proceso de hidratación, es importante la finura dado que de esta depende la velocidad de hidratación. El material resultante de la molienda está constituido por partículas de 1 y 80 micrones. La mayoría de partículas están por debajo de 50 micrones, siendo estas las que reaccionan con el agua. El ensayo evalúa el tamaño del grano mayor a 75 micrones y superficie específica. La velocidad de hidratación depende del tamaño del grano y de esta la resistencia, el fraguado, etc.
2.1.2. Constancia de volumen
2.1.2.1. se mide mediante el ensayo de expansión en autoclave, esta no puede ser mayor al 1%
2.1.2.1.1. Expansión en autoclave (detecta óxidos expansivos= oxido de calcio y oxido de magnesio libre) (max)
2.1.3. Tiempo de fraguado inicial (min)
2.1.3.1. Es una propiedad que permite conocer cómo se comportará el futuro el hormigon para saber los tiempos disponibles que tenemos para su manejo. En la práctica se necesita un tiempo de fraguado inicial mínimo para poder trabajar el hormigón (trasportado, colocado, compactado). Si fragua muy rápido no nos da tiempo de trabajar el hormigón.
2.1.3.1.1. Penetracion mediante aparato de Vicat
2.1.4. Contraccion por secado (max)
2.1.4.1. Contracción macroscópicamente perceptible en la pasta de cemento endurecida. Cambios de humedad generan cambios de volumen en la pasta de cemento endurecida perceptibles.
2.1.5. Requerimiento de agua (max)
2.1.5.1. Tiene por objetivo evaluar la demanda de agua requerida para alcanzar un cierto grado de fluidez en la pasta
2.2. Quimicos
2.2.1. Perdida por calcinacion
2.2.2. Residuo insoluble
2.2.3. HAY VARIOS MAS
3. Cales
3.1. Material calcinado capaz de reaccionar con el agua, constituido en mayor proporción por óxidos de Ca o Mg y con cantidades moderadas de compuestos silíceos y aluminosos. Según la naturaleza y cantidad de los productos formados durante la cocción, la cal podrá endurecer al aire o al agua.
3.1.1. Hidraulicas
3.1.1.1. Se obtienen a partir de rocas calcáreas que presentan impurezas arcillosas (mayor al 5%). Se trituran las rocas hasta tamaños menores de 1 cm y luego, se calcinan y se obtiene OCa, silicatos y aluminatos de calcio. El OCa libre es hidratado obteniéndose la cal hidráulica hidratada. Este hidratado debe ser supervisado para que no se hidraten los silicatos y aluminatos ya que si lo hacen, la cal pierde el poder cementante. Es decir, debe ser apagada en planta ya que si se le agrega agua de más o durante un tiempo mayor hidratamos el silicato y no ganamos resistencia.
3.1.2. Aereas
3.1.2.1. se obtienen a partir de rocas calizas puras o con alto grado de pureza. Se agrupan en cálcicas o magnésicas. Su utilización en obra como ligante requiere su previa conversión en hidróxido mediante el agregado de agua (apagado) siendo el producto final la cal aérea hidratada. Cuando las cales cálcicas presentan MgO como impureza se produce, durante la calcinación, el sobrecalentamiento del mismo lo que hace que se hidrate de forma diferida una vez que la cal ha sido utilizada (dentro del revoque). Se produce una expansión porque los productos del MgO son de mayor volumen que los originales y generan tensiones de tracción que provocan reventones y fisuras.
3.1.2.1.1. Aplicaciones:
3.1.2.1.2. Propiedades
3.1.2.1.3. Apagado
4. Hidratacion del cemento
4.1. C3A
4.1.1. aluminato tricálcico (C3A)
4.1.1.1. Si hidratamos el C₃A se forma un compuesto que endurece muy rápido, por eso que se agrega yeso a la mezcla. Al hidratar el C₃A+ yeso (sulfato de calcio dihidratado) se forma etringita (sulfoaluminato de calcio hidratado) elemento que cristaliza en forma de agujas prismáticas, la cual provoca un importante aumento de volumen, PERO como cuando se forma, la pasta aun está en estado de fluido viscoso (estado plastico) entonces al no haber endurecido, la expansión de este componente de hidratación no genera daño. Es estable cuando hay altas concentraciones de sulfatos (Yeso en exceso). En el cemento no se puede poner una cantidad excesiva de yeso porque estaría afectando la hidratación de otros productos y la resistencia, por lo tanto si este posee mucho aluminato que no puede transformarse en etringita (por falta de yeso para combinarse), al cabo de un tiempo ese aluminato reacciona con la etringita +agua que se formo y se va a transformar en monosulfoaluminato de calcio hidratado, cristaliza como platos hexagonales (rosetas) el problema radica en que cuando la estructura esté en servicio, en contacto con suelos o agua que tienen sulfatos estos van a provocar que nuevamente se forme etringita (secundaria) en el hormigón ya rígido y este material expansivo va a generar fisuras. Primer pico por la formación de etringita ocurre a los 10 a 15 min. 2do pico depende de la cantidad de iones de CaSO4 en la disolución que determina la transformación de etringita a monosulfoaluminato. (entre las 12 a 36 horas)
4.1.1.1.1. Resumiendo:
4.2. C4AF
4.2.1. Ferroaluminato tetracálcico (C4AF)
4.2.1.1. La hidratación del C₄AF es similar a la del C₃A aunque son mas lentas, liberan menor calor de hidratación y no provoca problemas de expansión.
4.3. C2S
4.3.1. Silicato Dicalcico (C2S)
4.3.1.1. posee un mecanismo de reacción similar al C3S pero su desarrollo es más lento. El C2S se disuelve y precipita los primeros hidratos con una relación C/S baja, luego aparecen el periodo durmiente, la aceleración y finalmente el estado estacionario. Los productos de hidratación del β-C2S son de mayor orden y peso molecular que los de C3S.
4.4. C3S
4.4.1. Silicato tricalcico (C3S)
4.4.1.1. En forma general se puede expresar que: Silicato de calcio + agua ----------------- C-S-H + CH + calor desde el punto de vista físico, se da la perdida de plasticidad, el fraguado y el endurecimiento. Hidratación silicato tricálcico: Cuando se mezcla el C3S con agua se produce un periodo de rápida evolución del calor debido a la disolución de una pequeña proporción de C3S (15 minutos). Para explicar la desaceleración de la reacción existen varias teorías, una de ellas es la formación de una capa de CSH(m)metaestable (C/S=1), sobre la superficie de grano del C3S o la de una doble capa de iones. Luego, se produce un periodo relativamente inactivo, denominado periodo durmiente (2-4 hs), durante el cual el C3S está continuamente en disolución y el agua tiende a saturarse de iones de calcio y oxhidrilos. Cuando La disolución se sobresatura de Ca(OH)2, los compuestos se precipitan y se produce un cambio de CSH a una forma más permeable y la reacción se acelera por un proceso de cristalización autocatalítica, dando lugar al inicio del fraguado(aceleración). El C3S continúa su rápida hidratación alcanzando la máxima velocidad de liberación de calor al final de este periodo de aceleración. En esta etapa se produce el fraguado que se manifiesta por medio de la rigidización del sistema y comienza el endurecimiento donde los productos de hidratación crecen en el espacio libre de la pasta generando calor. Este período finaliza cuando los hidratos depositados en la superficie de los granos de C3S reducen la difusión de SiO4 4+ y determinan una desaceleración de la reacción de hidratación; periodo durante el cual la tasa de liberación de calor es decreciente. El último estado es el estacionario, donde la curva de liberación de calor se hace asintótica en el tiempo. Es un proceso controlado por la difusión de especies químicas o por la tortuosidad de los caminos que debe atravesar el agua para alcanzar al C3S sin reaccionar. 5 etapas Disolución 15 min Durmiente 2 a 4 hs Aceleración Desaceleración Estacionario Etapa 1. Rápida evolución del calor asociada con el proceso de disolución. Etapa 2. Continúa la disolución en forma lenta. Etapa 3. La concentración de iones calcio e hidroxilo alcanza un valor crítico. Comienza la cristalización de CH y CSH. Comienza el endurecimiento. Etapa 4. El CSH cubre los granos de C3S anhidro formando una barrera a través de la cual el agua debe pasar para alcanzar el C35 (desaceleración de la reacción). Etapa 5. Se alcanza el 100% de la hidratación.
5. Tipos de cementos puros
5.1. Uso general
5.1.1. CPN Cemento portland normal
5.1.1.1. Uso para cualquier obra. Gran calor de hidratación (recomendable en climas fríos). Precaución con obras en agua o terrenos agresivos o de gran espesor. Componentes: Clinker + Sulfato de Calcio: 90‐100% Escoria: 0‐10%
5.1.2. CPF Cemento portland con filler calcareo
5.1.2.1. Mayor cohesión, mejor trabajabilidad, menor exudación, mejor bombeabilidad y mejor resistencia en edad temprana. Precaución con las bajas temperaturas o aditivos reductores de agua que pueden producir retrasos en el fraguado. Componentes: Clinker + Sulfato de Calcio: 80‐99% Filler Calcáreo: 1‐20%
5.1.3. CPEG Cemento portland con escoria
5.1.3.1. menor calor de hidratación, mayor resistencia a largo plazo,mayor resistencia en medios agresivos, obras subterráneas precaución con hormigón pretensado con alambres adherentes, hormigón a bajas temperaturas o aditivos reductores de agua que pueden producir retrasos en el fraguado
5.1.4. CPC Cemento portland compuesto
5.1.4.1. 2 o mas adiciones minerales
5.1.5. CPP Cemento portland puzolánico
5.1.5.1. Menor calor de hidratación, desarrollo de resistencia a largo plazo, resistencia en lugares agresivos con agregados potencialmente reactivos, obras hidráulicas ya que resiste los sulfatos. Precaución con obras en lugares fríos Componentes: Clinker + Sulfato de Calcio: 50‐85% Puzolana: 15‐50%
5.1.6. CAH Cemento de alto horno
5.1.6.1. Bajo calor de hidratación, importante evolución de resistencia a largo plazo, resistencia a medios agresivos. Usar en obras con ambientes agresivos por salinidad o sulfatos, hormigón armado. Precaución con bajas temperaturas y hormigón expuesto al contacto de altas concentraciones de ion Mg. Componentes: Clinker + Sulfato de Calcio: 25‐65% Escoria: 35‐75%
5.1.7. Cemento de Albañileria
5.1.7.1. El cemento de albañilería se obtiene a partir de una intensa molienda del Clinker portland, rocas calcáreas de alta pureza, pequeñas cantidades de yeso y aditivos. Es un producto destinado exclusivamente a trabajos de albañilería. Su excelente perfomance permite obtener, entre otras ventajas, mezclas de gran trabajabilidad y alto rendimiento. Las características de este ligante están especificadas en la norma IRAM 1685 y sus requisitos se basan fundamentalmente en el desempeño de las mezclas en estado fresco y su resistencia en el estado endurecido. Tiene mucha menos resistencia pero más trabajable. Se usan para mampostería, contrapisos etc. Si tengo que hacer un revoque fino no es recomendable utilizar este material. Debido a que su resistencia mecánica es significativamente menor que la del cemento Portland se le da otros usos en la construcción donde no se exija compromiso estructural.
5.2. Uso Especial
5.2.1. ARI Alta resistencia inicial
5.2.1.1. Tiene un elevado porcentaje de C3S y se usan para desencofrar a muy corta edad para la prefabricación y el pretensado o cuando el hormigonado en clima frío demora las reacciones de hidratación. Estos cementos alcanzan o superan a los 7 días la resistencia que posee un cemento normal a los 28 días. Son más costosos que los cementos normales.
5.2.2. ARS Altamente resistente a sulfatos MRS moderada resistencia a sulfatos
5.2.2.1. Estos cementos de propiedades especiales son sumamente útiles cuando se desea hormigonar en suelos agresivos o bien en aguas marítimas o de otra índole que posean alta concentración de sulfatos. El ataque por sulfatos se produce sobre los productos de hidratación del AC3 (aluminato tricálcico) formando nuevamente la ettringita que es de naturaleza expansiva. Estas expansiones, dentro de la matriz, provocan la aparición de fisuras. Estas agresiones se evitan utilizando este tipo de cementos que dependiendo del grado de concentración de sulfatos: si existe una alta concentración de los mismo se utiliza un ARS (altamente resistente a los sulfatos) que posee bajo contenido de AC3 (4%); si la concentración de sulfatos es menor se utiliza un MRS (moderadamente resistente a los sulfatos) que posee un porcentaje algo mayor de AC3 (8%).
5.2.3. B Blanco
5.2.3.1. Es el producto de pulverización del clínker blanco, obtenido a partir de materias primas con bajo contenido de hierro en su composición: arcillas libres de hierro (caolinita), y rocas calizas sin impurezas. Presenta alto contenido de C3A y bajo C4AF. Puede colorearse con distintos óxidos. Se utiliza para hormigones arquitectónicos y para la fabricación de revestimientos.
5.2.4. RRAA Resistente a la reaccion Alcali Agregado
5.2.4.1. Son requeridos cuando el hormigón se elabore con agregados potencialmente reactivos frente a los álcalis. La expansión se evalúa usando probetas preparadas con este cemento.
6. ADICIONES MINERALES
6.1. Sustancias naturales o industriales silíceas o silicoaluminosas capaces de reaccionar con hidróxido de calcio presente en el cemento para formar Silicatos de Calcio Hidratado. Se pueden incorporar durante la fabricación del cemento o del Hº.
6.1.1. Activas
6.1.1.1. reaccionan en condiciones normales y generan más SCH y SCH secundario.
6.1.1.1.1. Puzolanicas: puzolanas, ceniza volcánica.
6.1.1.1.2. Autopuzolanicas: ceniza volante, escoria de alto horno.
6.1.2. Inertes
6.1.2.1. no generan SCH secundario.
6.1.2.1.1. Efecto filler: dispersa las partículas de cemento, favorece su hidratación y la resistencia a corta edad. Actúa como centro de nucleación para el desarrollo de productos hidratados como el CH. El filler incrementa la velocidad de hidratación del Clinker.
6.2. Efectos sobre las propiedades del hormigon
6.2.1. Reducen la exudación Retrasan el fraguado Puede incrementar la demanda de agua Mejora la resistencia a larga edad Mejora la calidad de los productos de hidratación Reduce la permeabilidad Mejora la durabilidad de la pasta Reduce el calor de hidratación Aporta economía
6.3. REVISAR DEL LIBRO
7. Hormigon Fresco
7.1. Trabajabilidad
7.1.1. La trabajabilidad es una propiedad tecnología del hormigón fresco. Se define como la facilidad de colocar y terminar perfectamente al hormigón en un determinado elemento estructural, en una posición definida y con los medios disponibles en obra, alcanzando la máxima compacidad sin perdida de la homogeneidad obtenida en el mezclado (segregación). Otra definición bastante usada respecto al termino trabajabilidad (Glanville, Collins y Matthews) es la siguiente: Energía necesaria para alcanzar en el hormigón su máximo grado de compactación sin segregación.
7.1.1.1. Los métodos de ensayo desarrollados tienden a valorar una de las siguientes tres (3) características más importantes que hacen a la trabajabilidad: Compactibilidad: facilidad con la que el hormigón puede ser compactada y el aire removido de su masa. Movilidad: facilidad con la que el hormigón puede fluir dentro de los encofrados y entre las armaduras Estabilidad: habilidad de mantener su homogeneidad sin segregarse durante su transporte, colocación y compactación.
7.1.1.1.1. Ensayos que evaluan la consistencia o fluidez:
7.1.1.2. Ensayo de penetración de la Bola Kelly
7.1.1.2.1. Es una prueba de penetración sencilla, fácilmente de aplicar en obra. Consiste en determinar la profundidad que un hemisferio de metal de 13,6 kg. se hundirá en el hormigón bajo su peso propio. El espesor de la capa de material a ensayar debe ser mayor de 3 veces el tamaño máximo del agregado grueso o al menos 20 cm, y la menor dimensión lateral de 46 cm. La caída de la semi‐esfera es conveniente realizarla de manera guiada para evitar que se incline y roce el eje con el marco y modifique el resultado. La penetración resulta aproximadamente igual a la mitad del asentamiento. En el caso de aplicar este método a hormigones livianos el peso de la semi‐esfera es de 9,0 kg. Este ensayo puede realizarse en una bandeja o carretilla; también, en encofrados antes de cualquier manipuleo.
7.1.2. Terminacion
7.1.2.1. La terminación de un hormigón es la facilidad con la que se puede alisar la superficie del mismo. Ésta se la evalúa pasando una cuchara de albañil tratando de alisar la superficie de la mezcla. Si tras tres o cuatro pasadas la mezcla queda alisada, se dice que la misma posee una terminación “buena”.
7.1.3. % óptimo de arena
7.1.3.1. Se le llama contenido óptimo de arena (o agregado fino) a aquel que sea ligeramente mayor al necesario para ocupar junto con la pasta los espacios dejados por el agregado grueso. Se lo calcula con el método de los pastones de prueba que, resumiendo, consiste en lo siguiente: a) Elección del asentamiento. b) Elección de la razón agua/cemento adecuada para dar cumplimiento a las exigencias de resistencia y durabilidad. c) Preparación de uno o más pastones de prueba con la razón agua/cemento elegida en b) con el objeto de determinar las proporciones entre los agregados fino y grueso, y las cantidades de cada uno de los materiales componentes, para obtener una mezcla trabajable, de la consistencia (asentamiento) necesaria, con la mínima cantidad posible de pasta. El contenido óptimo de arena varía dependiendo del tipo de agregado que sea, la granulometría de los mismos, la razón agua/cemento (necesaria para satisfacer simultáneamente los requerimientos de resistencia y durabilidad) y del asentamiento necesario en función del tipo de estructura y métodos de compactación.
7.1.3.1.1. Cuando calculamos el % de arena de un hormigón lo debemos hacer en volumen ya que lo que se busca es que el contenido de arena que se busca es aquel que ocupe el volumen de vacíos que dejan los agregados gruesos. Se trata de un problema volumétrico.
7.2. Cambios de Volumen
7.2.1. los cambios de volumen que pueden ocurrir en el hormigón en estado fresco, es decir durante el lapso de tiempo que va desde su colocación hasta su fraguado final. Los cambios de volumen en este estado pueden ser:
7.2.1.1. Contraccion Quimica
7.2.1.1.1. Cambio de volumen absoluto que sufre la fase sólida (partículas de cemento) y fase líquida (agua) como consecuencia de la hidratación, sin tener en cuenta el volumen de vacíos capilares. Es visible macroscópicamente solo hasta el inicio del fraguado, después se compensa macroscópicamente mediante la formación de poros capilares. Se mide o estima con el volumen de cemento hidratado y la densidad de los productos de hidratación.
7.2.1.2. Contraccion Autogena
7.2.1.2.1. Cambio de volumen relativo que sufre la pasta, sin aporte externo de agua, como consecuencia de la hidratación, incluyendo el volumen de vacíos capilares. Es macroscópicamente visible hasta el final del fraguado. Aumenta con la disminución de la a/c y con el aumento de la cantidad de pasta. Es muy importante en hormigones con a/c menores que 0,42. Se puede medir con el volumen de cemento hidratado, densidad de los productos de hidratación y volumen de capilares.
7.2.1.3. Contraccion Plastica
7.2.1.3.1. Se produce como consecuencia de la evaporación de agua presente en la red capilar formada en los primeros minutos después de la colocación y compactación del hormigón. Cuando la velocidad de evaporación es mayor que la de exudación, se generan tensiones capilares en la masa que producen la contracción de la misma. Dependiendo de la magnitud de la contracción, se pueden inducir tensiones de tracción en la masa que produzcan fisuras en el Hº.
7.2.1.4. Asentamiento Plastico
7.2.1.4.1. Son los cambio de volumen que sufre el Hº en sus primeros minutos antes del inicio del fraguado como consecuencia de la sedimentación de sus partículas sólidas. Se pone de manifiesto cuando se tienen: altos contenidos de pasa; altos asentamiento; escasa retención de aire; agregados mal graduados; compactación deficiente; grandes espesores de Hº o elevada exudación. Las restricciones internas debido a armaduras o externas debido a encofrados pueden generar fisuras. En general éstas se orientan según la posición de las armaduras. Puede reducir el recubrimiento de las armaduras horizontales superiores.
7.2.1.5. Expansion (hinchazón)
7.2.1.5.1. Se produce en presencia de agua externa y se manifiesta después del fraguado final, ocurre debido a la combinación del crecimiento de los cristales, absorción de agua y presión osmótica. Cuando se elimina la fuente de agua externa, las contracciones autógenas y de secado revierten el cambio de volumen. La magnitud de la expansión no es muy grande, sólo cerca de 50 millonésimos en las edades tempranas.
7.3. Segregacion
7.3.1. La segregación es la separación de las fases solidas del hormigón fresco de modo que la mezcla deja de ser razonablemente homogénea. Existen dos fenómenos diferenciados de segregación según cual sea la fracción predominante que se separa: la segregación de los agregados gruesos respecto del mortero y la segregación de la pasta respecto del conjunto de agregados. Además, aparecen dos tipos de segregación, según sea el origen de la misma: la Segregación Interna, debida al propio hormigón (por dosificación inadecuada) y la Segregación Externa,originada en causas independientes al hormigón en sí mismo (por ejemplo causada por efectos de transporte, colocación o compactación de la mezcla).
7.4. Exudacion
7.4.1. La segregación del agua en la cual parte del agua de la mezcla tiende a ascender hacia la superficie del hormigón recientemente colocado recibe el nombre de exudación.
7.4.1.1. Tipo particular de segregación por la que el agua tiende a ascender a la superficie debido a la sedimentación de los demás componentes (más pesados) o cuando las partículas sólidas no pueden retener el agua durante la consolidación. Este proceso continúa hasta que se produce el equilibrio entre las fuerzas de atracción electrostáticas del agua adsorbida y las fuerzas gravitatorias que actúan sobre las partículas dispersas
7.4.1.1.1. Exceso de exudación
7.4.1.1.2. Defecto de exudación:
7.4.1.2. Factores que la afectan:
7.4.1.2.1. Finura y composición del cemento (AC3 y álcalis); Fracción fina del agregado (Pasa tamiz N°50); Contenido de cemento y a/c; Contenido de aire y Contenido de puzolana.
7.5. Temperatura
7.6. Madurez
8. Aditivos
9. Los aditivos son sustancias generalmente líquidas, que se agregan al hormigón en pequeñas dosis con el fin de producir ciertos cambios en las características y propiedades del hormigón fresco y también del hormigón endurecido, de modo que facilite la ejecución de la estructura, permita mejorar sus características mecánicas o aumentar en forma pronunciada su durabilidad frente al medio ambiente de su lugar de emplazamiento, o a las condiciones que impone su funcionamiento.
9.1. Modificadores de Fraguado
9.1.1. Retardadores de Fraguado
9.1.1.1. Aceleran o retardan el tiempo de fraguado. Recomendados para casos en los que se necesite mantener al hormigón en estado trabajable y en condiciones de ser vibrado o revirado durante un tiempo mayor que el normal. Un ejemplo puede ser cuando la obra esté muy lejos de la hormigonera entonces se necesite retardar el tiempo de fraguado.
9.2. Fluidificantes o Superfluidificantes
9.2.1. Modifican la fluidez, de manera que aprovechando la fluidez que provee el aditivo se puede reducir el agua manteniendo la trabajabilidad, lo que aumentaría la resistencia. También se puede utilizar para reducir el contenido de cemento (reduciendo la cantidad de agua, manteniendo la resistencia y trabajabilidad). Dependiendo del caso de hormigón que poseamos podemos darle diferentes tipos de uso, ya sea para mejorar su trabajabilidad, su resistencia, o hacer un hormigón más económico reduciendo la cantidad de cemento de la mezcla.
9.2.1.1. Podemos utilizar un aditivo plastificante o reductor de agua para aumentar la fluidez de la mezcla sin realizar ningún otro cambio en la dosificación dando así una mejor trabajabilidad. Reduciendo la cantidad de agua en la mezcla, con el aditivo plastificante, manteniendo la fluidez, reducimos así la relación a/c por lo que aumenta la resistencia. Si mantenemos la fluidez de la mezcla y a su vez mantenemos la resistencia, como con el aditivo plastificante reducimos la cantidad de agua necesaria de la mezcla, podemos reducir la cantidad de cemento obteniendo así un hormigón mas económico.
9.3. Incorporadores de aire
9.3.1. Incorporan micro burbujas de aire mejorando la durabilidad del hormigón. Recomendados para estructuras que requieran gran resistencia a la acción de los agentes atmosféricos, a los efectos de la congelación y deshielo, al ataque de líquidos agresivos.
9.3.1.1. permiten reducir el contenido de agua del hormigón hasta en un 12 % sin afectar la consistencia del hormigón o incrementar el asentamiento hasta en 10cm manteniendo constante el contenido de agua.
9.3.1.1.1. La incorporación de aire se logra de forma controlada mediante el agregado de aditivos tesoactivos durante el mezclado del hormigón fresco. Las burbujas de aire incorporado actua como partículas finas sin friccion, que aumentan la trabajabilidad del hormigón fresco. Consecuentemente, se reduce la cantidad de agua de mezclado necesaria para obtener la consistencia de diseño. Al actuar como partículas finas, también puede reducir el porcentaje de arena en el hormigón. A si mismo, las mezclas resultan mas cohesivas, disminuye la exudación y la segregación, y requieren menos energía para moverlas y compactarlas. Cuando se deben resistir acciones de congelación y dehielo, el volumen de aire que se requiere incorporar en la mezcla fresca es el necesario para lograr el factor de espaciamiento de las burbujas en el hormigón endurecido luego de su compactación.
9.4. Aceleradores de Resistencia
9.4.1. Aceleran la ganancia de resistencia una vez que el fraguado ha comenzado utilizado en obras que requieran adquirir la resistencia en un menor tiempo que el habitual como puede ser en bacheos de pavimentos por ejemplo.
10. Hormigon Endurecido
10.1. Resistencia
10.1.1. La resistencia es una de las propiedades fundamentales del hormigón: lo define, se usa como parámetro de diseño, se emplea como factor de calidad, para la aceptación o rechazo. Está asociado con la mayoría de las propiedades principales, como lo son la durabilidad, impermeabilidad, dureza, rigidez.
10.1.1.1. Ensayo para determinar la Resistencia a compresión de un cemento
10.1.1.1.1. El mortero para el ensayo debe estar constituido por: 1 parte de cemento, 3 partes de arena normal secada a estufa hasta peso constante y 1/2 parte de agua potable (relación agua/cemento = 0,5), medidas en peso. A este mortero se lo denomina mortero normal. Para realizar el ensayo de compresión es necesario: una mezcladora de dos velocidades accionada eléctricamente; moldes de acero de tres compartimentos, que permiten preparar tres probetas prismáticas de 4 x 4 x 18 cm. Se prepara el mortero y se moldea un juego de 3 probetas para cada edad de ensayo (2, 7 y 28 días). La elaboración del mortero se efectúa con la mezcladora, las probetas deben ser compactadas con el dispositivo mencionado. Para todo ello, existe una metodología y técnica normalizada. El desmolde se efectúa entre 20 y 24 horas después de confeccionadas las probetas y se sumergen en agua saturada de cal a una temperatura de 20°C, hasta la edad de ensayo. A la edad de ensayo, se retiran las probetas del agua y se las ensaya con el dispositivo de compresión el cual consiste en dos planchuelas de 40 mm de ancho por 10 mm de espesor y soporte guía. Se indica el valor promedio de 6 ensayos de compresión, que determinan a los 7 y 28 días, la resistencia a compresión.
10.1.1.2. Razon a/c
10.1.1.2.1. La porosidad está influenciada por las proporciones relativas de a/c, por ende la resistencia también estará relacionada con esta. A medida que se utiliza mayor cantidad de agua crece el volumen de poros capilares y el material es menos resistente. La porosidad también es variable con el desarrollo de la hidratación y existe una función que vincula la resistencia con el tiempo y depende de l a cantidad y tipo de componentes del cemento, de las condiciones de humedad y T existentes durante el proceso de hidratación.
11. Hormigonado en Clima Caluroso
11.1. cualquier combinación de alta temperatura ambiente, baja humedad relativa y velocidad de viento, que tienda a perjudicar la calidad del Hº fresco o endurecido. Se acelera la tasa de perdida de humedad y la velocidad de hidratación del cemento.
11.1.1. Temperatura de colocacion del Hormigon Fresco
11.1.1.1. La temperatura del hormigón fresco inmediatamente después de su colocacion y compactacion, debe ser igual o menor que 30°C. Esta temperatura no evita la formación de fisuras por contracción térmica.
11.1.2. Condiciones Perjudiciales en Climas Calurosos:
11.1.2.1. Alta Temperatura Ambiente
11.1.2.2. Alta temperatura del Hormigon
11.1.2.3. Baja Humedad Relativa
11.1.2.4. Alta Velocidad del Viento
11.1.2.5. Radiacion Solar
11.1.3. Efectos del clima Caluroso sobre el Hormigón
11.1.3.1. Incremento en los requerimientos de agua
11.1.3.1.1. Reducción de la resistencia como resultado del alto requerimiento de agua y del incremento en el nivel de temperatura
11.1.3.2. Perdida acelerada del Asentamiento (correspondiente tendencia a añadir agua en el lugar de la obra)
11.1.3.3. Incremento en la velocidad de Fraguado
11.1.3.4. Aumento de la fisuracion por Contraccion plastica
11.1.3.4.1. Contraccion Plastica:
11.1.4. Precauciones:
11.1.4.1. Mantener la temp del hormigón baja a través del enfriamiento de los agregados y del agua de mezcla
11.1.4.2. Levantar los parabrisas temporarios para reducir la velocidad del viento sobre la superficie del hormigón
11.1.4.3. Levantar sombrillas o media sombra temporarias para reducir la temp sobre la superficie del hormigón
11.1.4.4. Adicionar fibras plásticas a la mezcla de hormigón para ayudar a disminuir la formación de fisuras plásticas
11.1.4.5. Aplicar una membrana química de curado antes de que seque la superficie del hormigón, como recurso para reducir la velocidad de evaporación
11.1.4.6. Humedecer los agregados que estén secos y sean absorbentes
11.1.4.7. Humedecer la subrasante y los encofrados antes de la colocacion del hormigon.
11.1.4.8. Rociar la losa inmediatamente después de la colocación y antes del acabado, tomando cuidado para prevenirla acumilacion de agua que reduce la calidad de la pasta de cemento en la superficie de la losa
11.1.4.9. Disminuir los tiempos de transporte, colocacion y terminacion
12. Hormigonado en clima Frio
12.1. Se considera clima frio cuando la temperatura media diaria ambiente es menor a 5ºC y la temperatura ambiental es igual o menor que 10ºC durante medio día de cualquier periodo de 24hs.
12.1.1. La mezcla de Hº y su temperatura se deben adaptar a los procedimientos constructivos y las condiciones del clima. Cuando la temperatura del Hº es de -10ºC o menor, no se produce reacciones de hidratación y por lo tanto no hay ganancia de resistencia, por lo tanto, debe ser protegido el Hº hasta alcanzar un mínimo de resistencia.
12.2. Efectos de la congelacion sobre el Hormigon a Temprana Edad
12.2.1. Antes del Fraguado
12.2.1.1. Si la congelación se produce inmediatamente después que el hormigón se ha terminado de colocar, dicho proceso de fraguado quedara suspendido mientras duren las bajas temperaturas. La expansión del agua durante este congelamiento temprano originara durante el deshielo vacíos que, si no son eliminados provocan una significativa reducción en el desarrollo de la resistencia. Este problema se puede solucionar con una revibracion.
12.2.2. Despues del Fraguado
12.2.2.1. Cuando la congelación se produce luego que el hormigón ha fraguado, pero no ha ganado aun suficiente resistencia (menor a 3,5MPa segun ACI y 7 MPa segun CIRSOC), alrededor de las 10 hs, la expansión asociada a la formación del hielo causa un daño y una perdida irrecuperable de la resistencia. En caso de que la congelación se produzca cuando el hormigón ha alcanzado suficiente resistencia (mayores a las antes mencionadas), puede soportar la congelación sin mayor daño. Es por eso que debe protegerse el hormigon durante las primeras edades.
12.2.3. Medidas para Minimizar el efecto de las temperaturas bajas:
12.2.3.1. Incorporar aire intencionalmente.
12.2.3.1.1. 5%
12.2.3.2. Acelerar el tiempo de fraguado y endurecimiento mediante aditivos.
12.2.3.2.1. Aditivos aceleradores de fraguado
12.2.3.3. Usar cementos de fraguado más rápido (ARI)
12.2.3.4. Calentar el agua de mezclado
12.2.3.5. Quitar el hielo de las armaduras.
12.2.4. Verificacion y precaciones antes del hormigonado:
12.2.4.1. Medios necesarios para proteger el hormigon
12.2.4.2. Materiales libres de hielo o escarcha
12.2.4.3. Encofrados, Armaduras libres de nieve, hielo o escarcha
12.2.4.4. El hormigon no debe ponerse en contacto con suelos congelados
12.2.4.5. La temperatura de la superficie de contacto debe ser mayor a los 2 grados
12.2.5. Medidas para hormigonar:
12.2.5.1. Recintos
12.2.5.1.1. Son calefaccionados y permiten el hormigonado en climas frios
12.2.5.2. Agregados
12.2.5.2.1. Se utilizan en orden de llegada y con una temperatura de 65 y menor a 80 grados
12.2.5.3. Agua de mezclado
12.2.5.3.1. Temp Max de 80 grados
12.2.5.4. "En ningun caso la temperatura del hormigon fresco debera ser mayor a 30 grados"
12.2.5.4.1. La temperatura del Hº después de su colocación y compactación debe ser igual o menor a 30ºC. Con ella no se evita la formación de fisuras por contracción térmica, contraccion plastica.
13. Reaccion Alcali Silice (RAS)
13.1. Se produce entre los agregados con sílice reactiva y los álcalis presentes en el hormigón. El producto de la reacción es un gel expansivo que conduce a la fisuración del Hº.
13.1.1. El gel que rellena las fisuras presenta distintos colores ámbar, caramelo, marrón y blanco cuando se carbonata. Este gel genera tensiones internas de traccion que fisuran el Hormigon.
13.1.1.1. Es común visualizar fisuras en la superficie que parten desde un punto y se orientan a 120º
13.1.1.1.1. El plazo de aparicion de la RAS puede ir desde unos meses a decenas de años
13.2. Condiciones para que se produzca:
13.2.1. AGREGADOS CON SILICE REACTIVA METAESTABLE
13.2.1.1. hay minerales potencialmente reactivos (opalo,calcedonia, cristobalita, tridimita, vidrio volcánico [1-2% reacción rápida], cuarzo microcristalino tensionado o deformado [reacciones lentas]).
13.2.2. ALCALIS
13.2.2.1. concentración mínima de iones alcalinos (Na+, K+, Ca+ y OH-) en la solución de poros. provienen de un aporte interno (cemento, agregados (feldespatos aportan álcalis), aditivos químicos, adiciones minerales) o externos (sales descongelantes, agua de mar, aguas alcalinas de desagües industriales).
13.2.3. PRESENCIA DE HUMEDAD:
13.2.3.1. para que la reacción de inicie y progrese en el hormigón, es necesario un elevado contenido de humedad interna, 80-85%, ya que el gel de la RAS necesita presencia de agua para inducir la expansión. -Los geles deshidratados (por el secado parcial) se hidratan y vuelven a expandir cuando el hormigón vuelve a estar en contacto con humedad. -Los geles parcialmente deshidratados y carbonatados no se rehidratan. Por ejemplo en pavimentos (por no evaporarse el agua), hormigones masivos (por su humedad interna) el aumento de humedad interna, conduce al deterioro por RAS. El tratamiento superficial o películas aislantes o repelentes de agua, pueden limitar o reducir eficazmente el ingreso de humedad.
13.2.4. TEMPERATURA
13.2.4.1. el aumento de To provoca un aumento de la velocidad de expansión por RAS
13.2.5. transcurso del tiempo para que se alcancen las condiciones óptimas para el inicio de la reacción
13.3. Mecanismo de Expansion:
13.3.1. Durante el mezclado del Hormigon, los alcalis del cemento se disuelven en el agua de mezclado. Parte del CH formado en la hidratacion de los silicatos se solubiliza y satura de liquido los poros. Ese liquido ataca las particulas de los agregados reactivos y como consecuencia se produce un gel viscoso. A medida que el gel absorbe agua aumenta su volumen y al estar encerrado rodeada de la pasta de cemento endurecida, genera una presion interna de traccion la cual excede holgadamente la resistencia a la traccion del hormigon produciendo su ruptura en forma de fisuras.
13.3.1.1. Dependiendo del grado de desorden en la estructura del agregado y de su porosidad y tamaño de la partícula, los geles de álcali – silicato de composición química variable, son formados en la presencia de iones de hidroxilo y de metal alcalino. La forma de ataque en el concreto incluye el rompimiento de la estructura de sílice del agregado por los iones de hidroxilo, seguida la adsorción de los iones de metal alcalino en la superficie de los productos de la reacción. Cuando los geles de silicato alcalino se ponen en contacto con el agua por medio de osmosis (difusión entre dos líquidos o gases capaces de mezclarse). La presión hidráulica desarrollada puede conducir a la expansión y agrietamiento de las partículas del agregado afectado. La solubilidad de los geles de silicato alcalino en el agua, es la responsable de su movilidad desde el interior del agregado hasta las microgrietas, tanto adentro del agregado como en el concreto. La continua disponibilidad de agua provoca un agrandamiento de las microgrietas, que alcanzan el exterior → Agrietamiento de mapeo. El desarrollo depende de la cantidad, tamaño y tipo de agregado reactivo presente y de la composición química del gel formado. Cuando un material reactivo se encuentra presente en forma finamente dividida, puede haber evidencias considerables de reacción pero las expansiones a un grado significativo no ocurren.
13.4. Tipos de Deterioro:
13.4.1. Microfisuracion, fisuracion y agrietamiento del Hormigon
13.4.2. Cambios dimensionales
13.4.3. Exudacion y Manchado (color caramelo, marron)
13.5. EVALUACION DE LA REACTIVIDAD DE LOS AGREGADOS
13.5.1. En estructuras en servicio con más de 10-15 años de antigüedad, como mínimo 3 estructuras. Se debe tener en cuenta:
13.5.1.1. El agregado debe provenir del mismo yacimiento, poseer el mismo tipo y cantidad de mineral reactivo.
13.5.1.2. El cemento debe poseer el mismo contenido de álcalis.
13.5.1.3. Las condiciones de exposición deben ser similares.
13.5.2. Análisis petrográfico del agregado, si resulta potencialmente reactivo continúan las evaluaciones.
13.5.3. Ensayo de barras de mortero, si manifiesta reacción.
13.5.4. Ensayo de prismas de Hº, si manifiesta reacción.
13.6. MEDIDAS PARA DISMINUIR LOS EFECTOS DELETEREOS DEL RAS
13.6.1. Reemplazo total o parcial del agregado por otro no reactivo.
13.6.2. Limitar el contenido de álcalis en el Hº
13.6.3. Incorporar AMA o inhibidores de la RAS
13.6.4. Usar aditivos químicos: sales de litio. El tipo y cantidad depende del tipo de cemento y agregado reactivo.
13.6.5. Reducir la permeabilidad del Hº. (menor a/c)
14. Ataque por Sulfatos
14.1. fenómeno muy complejo que involucra:
14.1.1. el movimiento de iones sulfato a través de los poros del hormigón, mediante distintos mecanismos de transporte;
14.1.2. reacciones químicas de los sulfatos del medio exterior con los aluminatos de calcio y el CH de la pasta de cemento hidratada
14.1.3. formación de compuestos expansivos que producen fisuras por presiones de cristalización de la sal en los poros de ambas fases del hormigón, aumento de volumen de los elementos estructurales y pérdida progresiva de masa y resistencia del hormigón. A su vez, la formación de fisuras incrementa las vías de acceso a la masa del hormigón y acelera la agresión de los sulfatos provenientes del medio exterior.
14.1.4. El ataque de sulfatos puede ser interno o externo.
14.1.4.1. La agresion por sulfatos se da en la superficie exterior de contacto entre la estructura y el medio ambiente (ATAQUE EXTERNO) pero la accion mas perjudicial es la que se produce en el interior de su masa (ATAQUE INTERNO)
14.1.4.1.1. la evidencia de un ataque por sulfatos se debería verificar mediante análisis químicos y petrográficos.
14.2. ATAQUE EXTERNO DE SULFATO
14.2.1. cuando las aguas o suelos con sulfatos en solución se ponen en contacto con las estructuras de hormigón y las sales provocan mecanismos de degradación de la pasta de cemento y de los agregados. (presencia de yeso, o sulfatos alcalinos) Todos los mecanismos de ataques externos por sulfatos requieren de la presencia de agua y están vinculados con la existencia del hidróxido de calcio y de las fases portadoras de aluminatos en la pasta hidratada.
14.2.1.1. FORMACION DE ETTRINGITA
14.2.1.1.1. Durante el mezclado del hormigón, el yeso del cemento se combina con los aluminatos formando monosulfoaluminato y tri sulfoaluminato o etringita. En los primeros momentos, cuando la concentración de sulfatos en la solución elevada predomina la formación de etringita que, por sus 32 moléculas de agua de cristalización, posee mayor volumen que las sustancias que la originaron. Este aumento de volumen dentro de una masa plástica no provoca efectos perjudiciales. A medida que avanza la hidratación de los aluminatos desciende la concentración de sulfatos en la solución y la etringita se descompone en monosulfoaluminato. En estas condiciones se completa el fraguado y gran parte del endurecimiento de la pasta de cemento. Si posteriormente ingresan sulfatos desde el exterior, se vuelve a incrementar su contenido en la solución de poros y el monosulfoaluminato retorna a la condición de equilibrio químico como etringita, fijado moléculas de agua que había cedido y aumentando su volumen. Esta expansión en una masa rígida supera la resistencia a tracción de la pasta y provoca la formación de fisuras sobre la superficie del hormigón.
14.2.1.2. FORMACION DE YESO
14.2.1.2.1. La formación de yeso se produce por intercambio iónico: los SO4 provenientes del medio exterior reemplazan a los (OH) del hidróxido de calcio. Se produce en soluciones concentradas de sulfatos(SO4>1000 mg/l) Según Mehta, la cristalización del yeso comienza cuando se agota la disponibilidad de aluminatos para formar etringita. Este proceso va acompañado de aumento de volumen, pérdida de resistencia y rigidez de la pasta y formación de fisuras. Los cristales de yeso se encuentran generalmente localizados en los poros y en la interfase pasta-agregado, la cristalización preferencial del yeso en la zona de transición no sólo debe atribuirse a la disponibilidad de CH sino también a su mayor porosidad. Los productos resultantes del ataque por formación de yeso y la magnitud de deterioro difieren según sea el catión del sulfato. Cuando el catión es magnesio, la degradación se agrava pues continua con la desestabilización de los silicatos y su transformación en una masa no cohesiva.
14.2.1.3. FORMACION DE BRUCITA
14.2.1.3.1. El ataque por sulfato de magnesio depende de la concentración de este agente agresivo en el medio.
14.2.1.4. FORMACION DE THAUMASITA (CO2)
14.2.1.4.1. La agresión por sulfato de magnesio puede tener otra particularidad cuando el hormigón contiene agregados calcáreos(calizas o dolomitas) o está expuesto a un medio exterior rico en anhídrido carbónico (CO2)
14.2.1.4.2. Resumiendo:
14.2.1.5. CRISTALIZACION DE SALES
14.2.1.5.1. Cuando el agua en contacto con la estructura contiene sales solubles en solución, la misma ingresa en el sistema de poros y asciende por succión capilar. La posterior evaporación del agua origina la cristalización de la sal dentro de los poros del hormigón.
14.2.2. MEDIDAS PREVENTIVAS
14.2.2.1. La reducción del ingreso de agua por succión capilar y/o permeabilidad constituye el medio más efectivo para reducir la velocidad de agresión por sulfatos. El ataque de sulfatos solo ocurrirá cuando el agua transporte los SO4 2- en solución dentro del hormigón por uno u otro de estos mecanismos.
14.2.2.1.1. Los hormigones con baja a/c, elevado contenido de cemento, bien compactados y apropiadamente curados tienen baja permeabilidad y una buena resistencia a los sulfatos independientemente del tipo de cemento usado. Por otro lado, los hormigones porosos y permeables son muy vulnerables al ataque por sulfatos cuando contienen compuestos inestables en su interior que pueden causar la degradación.
14.3. ATAQUE INTERNO DE SULFATO
14.3.1. Se produce sin aporte externo de sulfatos y por formación de la llamada etringita diferida (FED) en el hormigón endurecido y a partir de sus propios componentes (del hormigón). Siempre que exista aporte externo de agua
14.3.1.1. Los casos identificados se deben a tres fuentes que liberan lentamente los sulfatos:
14.3.1.1.1. Agregados naturales contaminados con yeso y cementos de contracción compensada
14.3.1.1.2. Cementos que contienen una elevada concentración de SO3 por el uso de combustibles alternativos
14.3.1.1.3. Hormigones curados a vapor a alta temperatura(elementos premoldeados)
14.3.2. Los agregados contaminados con sulfatos, especialmente yeso, conducen a una expansión diferida por la reacción entre los iones sulfatos disueltos de los agregados con la fase de AFm de la pasta de cemento endurecida.
14.3.2.1. Esta expansión provoca fisuración uniforme de la zona afectada y en este caso particular no se encuentra etringita en la interfase pasta-agregado.
14.4. DAÑO POR ATAQUE DE SULFATOS
14.4.1. Micro y macrofisuracion Perdida de masa
14.4.1.1. Disminucion de la resistencia
14.4.1.2. Disminucion de la rigidez
14.4.1.3. Aumento de la permeabilidad
14.4.2. Disminucion de la vida util
15. Corrosión de las Armaduras
15.1. La corrosión es la degradación que experimentan los materiales por la acción de los medios que los rodean.
15.1.1. La corrosión es un proceso inevitable y lo que se pretende es controlar la velocidad de corrosión (tiempo compatible con la vida útil).
15.2. TIPOS DE CORROSION
15.2.1. Segun la Morfologia:
15.2.1.1. Corrosion Localizada
15.2.1.1.1. el ataque se localiza en sectores puntuales (pitting)
15.2.1.2. Corrosion Uniforme
15.2.1.2.1. el ataque se extiende en forma homogénea sobre toda la superficie la penetración media e igual en todos los puntos.
15.2.2. Segun el Medio ionico:
15.2.2.1. Corrosion Quimica
15.2.2.1.1. el metal reacciona con un medio no iónico, no se generan corrientes eléctricas.
15.2.2.2. Corrosion Electroquimica
15.2.2.2.1. el metal reacciona con un medio iónico, se generan corrientes eléctricas debido al flujo de iones a través de un electrolito
15.3. Pasividad de las Armaduras
15.3.1. En el hormigón armado se crea un sistema acero-hormigón donde este último cumple una doble función. El recubrimiento de la armadura constituye una barrera física que separa la barra del medio ambiente exterior y por otra parte, el líquido contenido en sus poros que forma una capa de óxidos protectores, sobre la barra de acero, firmemente adherida y duradera, que evita la corrosión del metal (el acero se pasiva desde el punto de vista electroquímico). Esta solución acuosa está constituido principalmente por iones (OH-), los cuales provee una elevada alcalinidad(pH⋍12,5) La película pasiva impide la disolución del hierro e imposibilita la corrosión de las armaduras, incluso cuando se cumplen algunas condiciones necesarias para la corrosión (presencia de humedad y oxígeno) alcanzando de esta forma uno de los requisitos fundamentales de la viabilidad del hormigón armado como material estructural para la construcción. El acero se mantiene en estado pasivo mientras no se alteren las condiciones que provocaron la formación de la capa protectora. Pero esta situación no es permanente. Las estructuras expuestas al medio ambiente experimentan algunos procesos que, en su momento, van a provocar la pérdida de protección del acero. Los procesos más importantes son:
15.3.1.1. Despasivacion de la armadura:
15.3.1.1.1. Disminucion de alcalinidad (pH<9)
15.3.1.1.2. Presencia de cloruros (Cl > umbral critico)
15.3.2. Una vez que se despasiva la armadura, en presencia de Agua y Oxigeno comenzara el proceso de corrosion de la misma.
15.4. Proceso de Corrosion:
15.4.1. El modelo teorico que esquematiza el proceso de corrosion de las armaduras incluye dos periodos bien diferenciados:
15.4.1.1. Periodo de propagacion
15.4.1.1.1. Tiempo en el cual la armadura se corroe hasta llegar a un deterioro inaceptable para la seguridad, funcionalidad, estetica de la estructura. Elevadas temperaturas aceleran el proceso.
15.4.1.2. Periodo de iniciacion:
15.4.1.2.1. Tiempo que tarda en despasivarse la armadura
15.5. Daños que produce la corrosion:
15.5.1. Sobre la armadura:
15.5.1.1. Disminucion de la seccion y por lo tanto de la resistencia o capacidad portante
15.5.1.2. Disminucion de la ductilidad, mayor riesgo de fractura fragil
15.5.2. Sobre el Hormigon
15.5.2.1. Disminuye hasta desaparecer la adherencia entre el acero y el hormigon
15.5.2.2. Reduccion de la capacidad portante de la estructura
15.5.2.3. Generacion de tensiones que fisuran el hormingon
15.5.2.3.1. Debido a los productos de la corrosion (herrumbre) los cuales ocupan mayor volumen que la armadura sana y que superan la tension de traccion del hormigon.
15.6. Proteccion contra la corrosion:
15.6.1. ● Elaborar Hormigones de baja permeabilidad.
15.6.2. ● Emplear espesores de recubrimiento compatible con el medio de exposición (cumplir con el espesor mínimo).
15.6.3. ● Utilizar adiciones minerales activas.
15.6.4. ● Proteger al hormigón mediante recubrimientos que impidan el ingreso de agua y Oxigeno (pinturas, lacas)
15.6.5. ● Controlar la fisuración del Hormigón
15.6.6. ● Utilizar aditivos Inhibidores de la corrosión. Los migratorios, ingresan a través de la estructura del hormigón, buscando metales ferrosos y de adhieren a las superficiales, cubriéndolas con delgadas capas protectoras
15.6.7. ● Limitar la relación Agua /Cemento Máxima y el contenido de cemento mínimo.
16. Congelacion y Deshielo
16.1. El daño por congelamiento en el hormigón puede ser por agrietamiento y descascaramiento, causado por la expansión progresiva de la matriz de la pasta de cemento a causa de ciclos repetidos de congelamiento y deshielo;
16.1.1. La congelación y deshielo reiterados sobre el hormigón genera en el mismo un deterioro que comienza en la superficie expuesta y puede alcanzar varios centímetros de profundidad. Este deterioro está íntimamente relacionado con la estructura de poros capilares de la pasta, con la composición y características de los agregados y con el grado de saturación del hormigón en el momento que se produce el ataque. Este fenómeno se manifiesta por un debilitamiento de la superficie expuesta provocado por las sucesivas expansiones, con un efecto acumulativo que conduce al agrietamiento y descascaramiento y rotura en forma de escamas. El daño se produce cuando la tensión provocada por la dilatación que ocurre en el hormigón debido a esta acción física, supera su resistencia a la tracción. La resistencia a la congelación del hormigón cae abruptamente a partir de un grado de saturación del 85%
16.1.1.1. MECANISMO DE DETERIORO
16.1.1.1.1. Cuando una pasta de cemento saturada se congela, el agua de los capilares grandes solidifica, pero el agua de los poros de gel continua en estado líquido sobreenfriando. Se crea entonces un desequilibrio termodinámico entre el hielo con baja energía libre y el agua sobreenfriada que posee un alto contenido de energía. Este desequilibrio provoca la migración del agua de gel hacia los vacíos mayores donde el agua puede congelarse, provocando presiones y expansión de la pasta.
16.1.1.1.2. En una pasta cuyos capilares y poros de gel están llenos de agua, o próximos a esa condición al descender la temperatura por debajo de 0°C comienzan a formarse cristales de hielo en los capilares mayores. El aumento de volumen del hielo hace que la suma de agua solidificada más la que permanece aún en estado líquido exceda el volumen de la cavidad original, produciendo presiones hidráulicas dentro de la misma que hacen que el capilar se dilate o el agua fluya hacia otras cavidades que actúan como válvulas de alivio de presiones.
16.1.1.2. Congelación en partículas de los agregados
16.1.1.2.1. Las partículas de los agregados gruesos con alta absorción porosidad relativa, causada principalmente por los poros de mediano tamaño, son los que se saturan más fácilmente y contribuyen al deterioro del hormigón por reventones individuales. Habitualmente los grandes poros de los agregados no se llenan completamente de agua. En el hormigón, la falta de durabilidad por causa del agregado se presenta como reventones puntuales alrededor de la partícula. Por su parte, los agregados no resistentes a la congelación absorberán agua que luego es expelida del mismo durante aquella. Debido a las presiones que se desarrollan, se provocan roturas de la partícula y de la matriz. Cuando la partícula está cerca de la superficie, puede producirse un reventón en el hormigón.
16.1.2. MECANISMOS DE PREVENCION
16.1.2.1. Para que el hormigón se comporte satisfactoriamente en un medio ambiente con ciclos de temperaturas de congelación y deshielo, se requiere un mínimo contenido de aire incorporado en la pasta de cemento. Esa cantidad, referida a una mezcla de mortero u hormigón dependerá del tamaño máximo del agregado y del tipo de exposición.
16.1.2.2. Reducir permeabilidad (Reduciendo a/c)
16.1.2.3. Incorporar Aire (AII)
16.1.2.3.1. actuaran como camaras disipadoras de tension, es decir, cuando el agua se congele podra migrar hacia los espacios de las burbujas evitando que produzcan tensiones en el hormigon.
16.1.3. La resistencia a la congelacion y deshielo dependera de:
16.1.3.1. Permeabilidad
16.1.3.2. Grado de saturacion de la pasta
16.1.3.3. Velocidad de congelacion
16.1.3.4. Factor de esparcimiento
16.1.3.5. Naturaleza y tamaño del agregado
16.1.4. EVALUACION DE RESISTNECIA DEL HORMIGON FRENTE A LA CONGELACION Y DESHIELO
16.1.4.1. Mediante la observacion del comportamiento en estructuras de servicio
16.1.4.2. Mediante ensayo en laboratorio (IRAM 1666)
16.1.4.2.1. Se elaboran tres prismas de hormigon se llevan a camaras de humedad y se les mide el Ed (Modulo de elasticidad dinamico)
16.1.4.2.2. Se los somete a ciclos de congelacion y deshielo saturando la probeta previamente y midiendo el Ed cada 30 ciclos para evaluar el comportamiento interno del material.
16.1.4.2.3. Se continua el estudio hasta alcanzar minimamente los 300 ciclos o una dismunicion del Ed del 60%
17. Ataque Marino
17.1. el agua de mar es uno de los medios naturales mas agresivos. En el mar, el deterioro de las estructuras se produce por la convergencia de procesos físicos y químicos: de la acción física de erosión de las olas, los ciclos de mojado y secado, la cristalización de sales, la congelación y deshielo, la corrosión de armaduras, la reacción álcali agregado, etc.
17.1.1. El agua de mar contiene aproximadamente 3,5g/l de sales constituidas por:
17.1.1.1. Cloruros
17.1.1.1.1. produce corrosión de las armaduras por la penetración en el hormigón y su posterior combinación con los aluminatos (la presencia de estos últimos reduce la cantidad de cloruros libres provocando la corrosión). Inversamente, parte de los aluminatos no están disponibles para formar etringita. Por esas razones, en los hormigos sometidos a ambiente marino no se aconseja utilizar cementos con muy bajo aluminato tricálcico y se prefieren los cementos denominados modernamente resistentes a los sulfatos. Los cloruros se combinan con el agua y el AC3 y forman una sal de Friedel que resulta expansiva
17.1.1.2. Sulfatos
17.1.1.2.1. forman etringita como se ha descripto anteriormente (ataques por sulfatos) que es expansiva.
17.1.1.3. Sodio
17.1.1.3.1. la presencia de iones sodio puede dar lugar a RAS. También en combinación con los sulfatos pueden forman etringita.
17.1.1.4. CO2 anihidrido carbonico
17.1.1.4.1. disuelto en agua se combina con el hidróxido de calcio, esta reacción precipita y tampona los poros. Pero también puede dar lugar a la formación de la thaumasita.
17.1.2. Cuando se construyen estructuras de hormigón en áreas costeras reclamadas al mar, si las fundaciones se encuentran por debajo del nivel del agua salobre, la succión capilar y la evaporación pueden provocar supersaturación y cristalización en el hormigón por encima del nivel del terreno, lo cual provocaría tanto un ataque químico sobre el hormigón (sulfato) como la agravación de la corrosión del acero (cloruros).
17.2. Pueden identificarse 3 zonas:
17.2.1. -Zona atmosférica:
17.2.1.1. ataque químico, está sujeta principalmente a la corrosión de armaduras
17.2.2. Zona de mareas:
17.2.2.1. se produce el mayor deterioro debido a la variación de marea, la estructura se encuentra expuesta a ataques físicos (abrasión, congelamiento y deshielo) y químicos (a corrosión de armadura por el aumento en la concentración de cloruros por ciclos de mojado y secado).
17.2.3. Zona sumergida:
17.2.3.1. predomina el ataque químico, ataque por sulfatos, magnesio, CO2. No hay oxigeno.
17.3. ATAQUE QUIMICO
18. Accion del Fuego
18.1. En términos comparativos con otros materiales de uso estructural, el hormigón presenta un buen comportamiento frente al fuego debido a su baja conductividad térmica y a que es un material incombustible.
18.1.1. El hormigón no es combustible y no desprende humos tóxicos cuando se los somete a altas temperaturas.
18.1.2. El fuego introduce altos gradientes de temperatura y como resultado de ello, las capas superficiales tienden a separarse y saltar del cuerpo interior más frio. En caso de que la velocidad de calentamiento sea alta y la permeabilidad de la pasta baja, el hormigón se puede dañar en forma de descascaramiento superficial.
18.2. Factores que controlan la respuesta del hormigón frente al fuego.
18.2.1. ➢ Composición del concreto: Tanto la pasta como el agregado constan de componentes que se descomponen con el calor.
18.2.1.1. o En la pasta:
18.2.1.1.1. La temperatura del hormigón no se incrementa hasta que toda el agua evaporada haya sido removida, pero si hay mucha cantidad de agua puede ser un problema ya que, si la permeabilidad es baja y hay una alta velocidad de calentamiento, la presión producida por el vapor del interior produce descascaramiento del Hormigón.
18.2.1.2. o Los Agregados:
18.2.1.2.1. Pueden ser susceptibles de expansiones de ruptura que conducen a reventones. Por ejemplo, el cuarzo a 573°C cambia de cuarzo alfa a beta, produciendo un cambio en su estructura y a su vez una expansión que genera fuertes tensiones en el hormigón
18.2.1.2.2. los agregados porosos, dependiendo de la velocidad de calentamiento, tamaño del agregado, de la permeabilidad y del estado de humedad, pueden ser susceptibles a expansiones de ruptura que conducen a botaduras (falla del agregado en la que una parte de la pieza de agregado permanece en el hormigón y la otra sale con la hojuela de mortero).
18.2.2. ➢ Permeabilidad Del Hormigón
18.2.2.1. Tamaño del elemento y velocidad e incremento del enfriamiento, tiempo de exposición y temperatura máxima: Son importantes porque rigen el desarrollo de presiones internas de los productos gaseoso de descomposición (la pasta y los agregados tienen productos que al calentarse se descomponen)
18.3. Después de estar en contacto con el fuego, el hormigón queda con una resistencia residual que es menor a la resistencia original del hormigón
19. Ataque acido
19.1. En general, el cemento pórtland no tiene una buena resistencia a los ácidos; no obstante, puede tolerar algunos ácidos débiles, particularmente si la exposición es ocasional.
19.1.1. Un hormigón denso con una baja relación w/c proporciona algún grado de protección contra el ataque por ácidos. Ciertos materiales puzolánicos, y los vapores de sílice en particular, aumentan la resistencia del hormigón a los ácidos (Sellevold y Nilson 1987). Sin embargo, en todos los casos el tiempo de exposición a los ácidos se debería minimizar tanto como sea posible y se debería evitar la inmersión
19.1.1.1. Independientemente de su composición, ningún hormigón de cemento hidráulico puede soportar durante mucho tiempo un agua fuertemente ácida (pH menor o igual que 3). En estos casos se debería utilizar un sistema de barrera protectora o tratamiento adecuado.
20. Definiciones
20.1. Hinchamiento o Expansion por Humedecimiento
20.1.1. Es el aumento de volumen que sufre el hormigon en estado endurecido debido a la absorcion de agua.
20.2. Relajacion
20.2.1. La relajación es la disminución en el nivel de esfuerzos para deformaciones constantes.
20.2.1.1. Factores que influyen:
20.2.1.1.1. tipo y contenido de agregados
20.2.1.1.2. tipo de cemento
20.2.1.1.3. incorporación de aditivos
20.3. Extensibilidad
20.4. Modulo de elasticidad estatico
20.5. Fluencia lenta o Creep
20.5.1. La fluencia lenta es el aumento de deformaciones del hormigón endurecido para un nivel de esfuerzos constantes.
20.5.1.1. Se pueden distinguir deformaciones reversibles y otras no recuperables.
20.5.2. Causas principales:
20.5.2.1. fluido viscoso de la pasta de cemento
20.5.2.2. cierre de vacíos internos
20.5.2.3. fluir cristalino de los agregados
20.5.2.4. fluir del agua coloidal adsorbida en el CSH hacia los vacíos internos
20.5.3. Fluencia basica
20.5.3.1. representa las deformaciones que se producirían en el hormigón aún si se encontrara aislado del medio ambiente (sin intercambio de humedad).
20.5.4. Fluencia por secado
20.5.4.1. La fluencia aumenta si la aplicación de las cargas se superpone con un proceso de secado (contracción), y esto se debe al micro agrietamiento adicional en la zona de transición debido a la contracción por secado.
20.5.5. Factores que afectan la fluencia
20.5.5.1. -Relación a/c
20.5.5.2. -Humedad ambiente
20.5.5.3. -Edad de aplicación de la carga
20.5.5.4. -Tensión aplicada
20.5.5.5. -Tipo de agregado
20.5.6. Para disminuir los efectos del creep: se debe cargar la estructura a la mayor edad posible, ejecutarla con hormigón compacto de alta resistencia (baja a/c), conservarlo todo lo posible en medio húmedo.
20.6. Contraccion por secado
20.6.1. Es la reduccion que sufre el hormigon debido a la perdida del agua contenida en sus poros capilares.
20.7. Durabilidad
20.8. Comportamiento termico
20.9. Asentamiento plastico
20.9.1. Es el asentamiento que sufre el hormigon en estado plastico o previo a su fraguado debido a la accion de su propio peso y la exudacion. Si existe alguna restriccion que impida este asentamiento como puede ser una armadura se pueden generar fisuras en la superficie.
20.10. Extensibilidad
20.10.1. La capacidad maxima del hormigón de deformarse sin agrietarse antes de fallar bajo carga
20.11. Interface pasta agregado
20.11.1. La región de transición entre la pasta de cemento y los agregados gruesos y finos en el hormigón.
20.11.1.1. Las interfaces consisten en una zona a través de la cual se desarrolla la interacción entre la matriz y los agregados. Conceptualmente están formadas por una capa de agregado y otra de matriz, ambas con propiedades distintas al resto del agregado y de la matriz. Aquí se produce un “efecto pared” entre la pasta y los agregados que cambia la razón a/c ya que el llenado de los espacios vacíos durante la hidratación será menor en la zona de contacto con los agregados que en el interior de la pasta y, en consecuencia, variará la porosidad con respecto a la del interior de la matriz. Esto explica por qué la interfase es una zona rica en algunos compuestos, como CH, justificando el hecho que se desarrollen cristales mas grandes gracias al mayor espacio disponible. Estas zonas de transición constituyen el vínculo más débil del compuesto, el lugar por donde se inician y desarrollan las fisuras y la vía preferencial de ingreso de sustancias agresivas. Los productos de mayor cristalinidad y de menor aporte resistente (CH) se concentran en las interfases, se orientan y constituyen planos preferenciales de clivaje. El ingreso de sustancias agresivas puede causar exudación, contracción por secado y reacción deletéreo. Cuanto mayor tamaño máximo, mayor interface, por lo tanto mayor deformabilidad y menor resistencia. La adherencia es menor en la interface sometida a tracción directa que otra expuestas a esfuerzos constantes. Las adiciones reducen el espesor de la interface. (Las fases están vinculadas a través de zonas de transición (interfases) que poseen características diferentes a las de la matriz y los agregados. Las interfaces tienen mayor porosidad y productos de hidratación con menor aporte resistente a los que existen en el seno de la pasta de cemento.)
20.12. Porosidad capilar
20.12.1. Los poros pequeños y conectados en el hormigón que permiten el paso de agua y otros líquidos.
20.13. Contraccion por secado
20.13.1. La contracción que experimenta el hormigón debido a la pérdida de humedad durante el curado y el secado.
20.14. Salto termico
20.14.1. La diferencia de temperatura repentina que experimenta el hormigón.
20.15. Ettringita secundaria (Ettringita diferida FED)
20.15.1. Un compuesto que se forma durante la reacción entre la ettringita y el sulfato en el hormigón.
20.16. Modulo de elasticidad diferido o sostenido
20.16.1. La capacidad del hormigón de recuperar su forma original después de una deformación bajo carga sostenida a largo plazo.
21. Durabilidad
21.1. La durabilidad del hormigón se define como su capacidad para resistir a la acción del tiempo, los ataques químicos, la abrasión o cualquier otro proceso de deterioro, durante el ciclo de vida para el cual fue proyectado, requiriendo un mantenimiento mínimo. Un hormigón durable retendrá su forma original, su calidad y su servicio, cuando se exponga al medio ambiente. Ningún material es intrínsecamente durable, ya que como resultado de las interacciones ambientales, la microestructura y consecuentemente las propiedades de los materiales cambian con el tiempo.
22. Produccion
23. Dosificacion Metodo ACI (Tablas)
23.1. Se deben conocer las siguientes características de los materiales que se disponen para elaborar el pastón: 1. Cemento = ‐Tipo y peso específico 2. Agregado fino = ‐Módulo de finura (Mf) ‐Peso específico saturado y superficie seca (Pef). 3. Agregado grueso = ‐Tamaño máximo (T Max) ‐Peso específico saturado y superficie seca (Peg). ‐Peso de la unidad de volumen del agregado seco y compacto (P.U.V. scg). ‐Forma
23.1.1. En cuanto a los datos propios de la estructura son los mismos mencionados en el método de los pastones de prueba, es decir y resumiendo: 1. Resistencia característica o Resistencia media y coeficiente de variación (δ) o tipo de control. 2. Tipo y ubicación de la obra (por problemas de durabilidad). 3. Tipo de estructura y equipos de compactación a los efectos de la elección del Asentamiento.
23.1.1.1. EJEMPLO
23.1.1.1.1. Se desea realizar un Hormigón H25 para una estructura de hormigón armado a ejecutarse en un ambiente frio con posibilidad de congelación y deshielo sin uso de sales descongelantes. Cuál debe ser la resistencia de diseño del hormigón si la planta ejecutora trabaja con un grado de control 1, y el S es de 3.5 mpa. Exposición C1 – Hormigón armado: Razón a/c máxima: 0,45 (con aire intencionalmente incorporado) Resistencia característica mínima: 30 Mpa Las dos circunstancias que definen las dos posibles resistencias características en una dosificación son: La resistencia que nos otorga el calculista debido a su cálculo estructural y la resistencia debido a la durabilidad por exposición de la obra. Adoptaría de las dos posibles resistencias, la mayor lo cual cubra de seguridad a la menor. En este caso es la resistencia debido a la durabilidad (de 30 Mpa) que cubre la otorgada por el calculista (de 25 Mpa) a) Modo de Control 1: f'cr = f'c + 1,34 sn f'cr = 30 Mpa +1,34 x 3,5 Mpa f'cr = 34,69 Mpa f'cr = f'c + 2,33 sn – 3,5 f'cr = 30 Mpa + 2,33 x 3,5 Mpa – 3,5 f'cr = 34,65 Mpa Adopto como resistencia de diseño 34,69 Mpa
24. Control de Calidad
25. Hidratación de los silicatos
25.1. Constituyen entre 70 - 75% del cemento, siendo los principales determinantes del endurecimiento y resistencia. Ambos silicatos (C3S y C2S) al hidratarse generan silicato de calcio hidratado e hidróxido de calcio. El primero es el más importante producto de la hidratación y el qué es el principal artífice de la resistencia. La diferencia en la hidratación de ambos silicatos está en la velocidad, hidróxido de calcio liberado y calor de hidratación. La hidratación del C₃S genera mas CH, es mas rápida y libera mas calor que la de los C₂S.
25.1.1. S-C-H Silicato de calcio hidratado
25.1.1.1. Ocupa entre el 50 - 60% del volumen de sólidos, tiene una estructura cristalina bien desarrollada. Se presenta en forma de fibras delgadas y tiene gran superficie específica. Su estructura puede cambiar con la temperatura de formación, razón a/c, etc. Es determinante de la estabilidad volumétrica, resistencia y durabilidad pero también puede producir contracción por secado y fluencia lenta.
25.1.2. C-H Hidroxido de calcio
25.1.2.1. Ocupa 20 - 25% del volumen de sólidos. No contribuye demasiado con la resistencia. Es atacable por ácidos y tiene un rol importante en presencia de adiciones minerales activas.