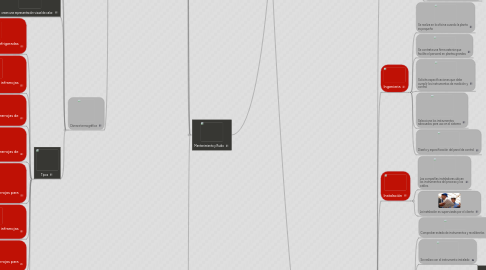
1. Mantenimiento y Ruido
1.1. Fallos en sistemas
1.1.1. Confiabilidad
1.1.1.1. Probabilidad de que un funcione en un determinado tiempo
1.1.1.2. Análisis de información operaria para mantenimientos
1.1.1.3. RCM
1.1.1.3.1. Mejorar llas funciones de los dispositivos y evitar consecuencias de sus fallas
1.1.2. Mean Time To Failure (MTTF)
1.1.2.1. Tiempo de recuperación de un sistema ante una falla
1.1.2.2. Incluye el tiempo de diagnóstico y reparación
1.1.3. Mean Time Between Failure(MTBF)
1.1.3.1. Tiempo promedio entre fallos
1.1.3.2. Probabilidad de que ocurra otra falla
1.1.4. Mantenimiento
1.1.4.1. Servicio de personas que incrementan la fiabilidad de un sistema
1.1.4.2. Preventivo,
1.1.4.3. Correctivo
1.1.4.4. Predictivo
1.1.4.5. Autónomo
1.1.5. Razón de fallas
1.1.5.1. Análisis de factores de fallos
1.1.5.2. Tomar medidas para mejorar
1.1.6. Modelos de confiabilidad
1.1.6.1. Serie
1.1.6.1.1. Fallo de un elemento produce fallo de sistema
1.1.6.1.2. Menor confiabilidad de componentes por separado
1.1.6.1.3. El funcionamiento de cada componente depende de el componente que lo antecede
1.1.6.2. Paralelo
1.1.6.2.1. El sistema funciona siempre que uno de sus componentes funcione
1.1.6.2.2. Falla cuando todos sus componentes dejan de funcionar
1.2. Filosofía de mantenimiento
1.2.1. Correctivo
1.2.1.1. Un personal que espera que se produzcan las fallas.
1.2.1.2. Una carga de trabajo irregular.
1.2.1.3. El requerimiento simultáneo en diferentes lugares.
1.2.1.4. Los repuestos se solicitan a pedido, lo que ocasiona dificultades para definir los niveles de stock
1.2.2. Preventivo
1.2.2.1. Planificar las operaciones teniendo en cuenta imperativos de producción.
1.2.2.2. Permite organizar y nivelar las cargas de trabajo con programas de visita, engrasado.
1.2.2.3. Mejora la confiabilidad y por lo tanto la disponibilidad de los equipos operando en tiempo oculto.
1.2.2.4. Optimizar el tiempo de intervención debido a una mejor preparación, por lo tanto dominar los costos de intervención y los riesgos de accidente.
1.2.3. Predictivo
1.2.3.1. Vigilancia de máquinas. Su objetivo es indicar cuándo existe un problema.
1.2.3.2. Distinguir entre condición buena y mala, y si es mala indicar cuán mala es.
1.2.3.3. La protección de máquinas. Su objetivo es evitar fallas catastróficas.
1.2.3.4. Estima cuánto tiempo más podría funcionar la máquina sin riesgo de una falla catastrófica.
1.2.4. Proactivo
1.2.4.1. Eliminar los problemas de la máquina a través de un periodo de tiempo.
1.2.4.2. Reduce el tiempo de in-movilización y una capacidad de producción extendida.
1.2.4.3. Detecta y corrige el desgaste las causas que generan el desgaste y que conducen a la falla de la maquinaria.
1.2.4.4. Establece una técnica de detección temprana, monitoreando el cambio en la tendencia de los parámetros considerados como causa de falla.
1.2.5. Mejora continua
1.2.5.1. Aplica prácticas efectivas en cada área de la organización y trasciende a lo que se entrega a los clientes.
1.2.5.2. Es la esencia de la calidad y pretende reflejar lo que las empresas en su giro necesitan hacer si desean ser más competitivas y productivas a través del tiempo
1.2.5.3. Mejoramiento incremental y mejoramiento marginal.
1.2.5.4. Insatisfacción continúa a lo que hacemos, pensar como podemos mejorar las tareas realizadas.
1.3. Instrumentos para identificación de fallas
1.3.1. Probador de tierra
1.3.1.1. dispositivos que realizan medidas de resistencia de tierra de diferentes punto
1.3.1.2. pueden ser utilizados para medir continuidad
1.3.1.3. Tipo Varilla
1.3.1.4. Tipo Gancho
1.3.2. Medidor de resistencia de aislamiento
1.3.2.1. se encargan de detectar el desgaste o fatiga en el aislamiento
1.3.2.2. Megger
1.3.2.2.1. instrumento que sirve para medir la resistencia de aislamiento, cable, bobinados, puede ser respecto a tierra o entre fases
1.3.2.2.2. se puede hallar el índice de polarización.
1.3.2.3. Aislamiento clase B, temperatura máxima 130°C.
1.3.2.4. Aislamiento clase F, Temperatura máxima 155°C.
1.3.2.5. Aislamiento clase H, temperatura máxima 180°C.
1.3.3. Multitester
1.3.3.1. muy utilizado en la industria y a nivel mundial
1.3.3.2. consta de tres variables a medir: un amperímetro, voltímetro, óhmetro
1.3.3.3. Tipos de multitester
1.3.3.3.1. Multitester digitales.
1.3.3.3.2. Multitester analógicos.
1.3.3.3.3. Multitester analógico y digitales.
1.3.3.3.4. Capacímetros.
1.3.3.3.5. Medidores de LCR.
1.3.3.3.6. Milióhmetros.
1.3.3.3.7. Watímetros o vatímetros.
1.3.4. Cámara termográfica
1.3.4.1. tipo de cámara que crea una imagen con luz infrarroja. Esta tecnología también puede llamarse mirando adelante infrarrojos (FLIR), o de imágenes térmicas.
1.3.4.2. estos dispositivos detectan la luz invisible, infrarrojos, también conocido como calor.
1.3.4.3. crean una representación visual de calor.
1.3.4.4. Tipos
1.3.4.4.1. Cámaras termográficas refrigeradas y no refrigeradas.
1.3.4.4.2. Cámaras termográficas infrarrojas tipo móvil.
1.3.4.4.3. Cámaras termográficas infrarrojas de alta tensión.
1.3.4.4.4. Cámaras termográficas infrarrojas de baja tensión.
1.3.4.4.5. Cámaras termográficas infrarrojas para usos mecánicos.
1.3.4.4.6. Cámaras termográficas infrarrojas para edificios.
1.3.4.4.7. Cámaras termográficas infrarrojas para energía eólica
1.3.4.4.8. Cámaras termográficas infrarrojas energía solar.
1.4. Ruido
1.4.1. Tipos de ruido
1.4.1.1. Ruido estacionario: Ruido cuyo nivel de presión sonora permanece constante a lo largo del tiempo.
1.4.1.2. Ruido fluctuante: Ruido cuyo nivel de presión sonora varía en función del tiempo.
1.4.1.3. Ruido intermitente: Ruido que aparece solamente en determinados instantes.
1.4.1.4. Ruido impulsivo: Ruido cuyo nivel de presión sonora aumenta
1.4.1.5. Ruido de Baja Frecuencia: Consideraremos valores de baja frecuencia todo ruido que se encuentre entre 20 y 125 Hz.
1.4.2. Fuentes de ruido
1.4.2.1. El tráfico (terrestre y aéreo)
1.4.2.2. La construcción de edificios y obras públicas
1.4.2.3. Algunas instalaciones industriales.
1.4.3. Solución
1.4.3.1. Reducir la emisión de ruidos en las fuentes,
1.4.3.2. Evitar la propagación de los ruidos mediante tratamientos acústicos de los ambientes
1.4.3.3. Proteger al personal expuesto, mediante el uso de protectores auditivos personales o mediante la utilización de cabinas.
1.4.3.4. Aislamientos acusticos
1.4.3.4.1. Barreras o pantallas.
1.4.3.4.2. Confinamiento de la fuente sonora.
1.4.3.4.3. Cabinas acústicas para el personal
1.4.3.4.4. Aumento del aislamiento de paredes existentes
1.4.3.5. Tratamientos con absorbentes
1.4.3.5.1. Revestimiento de paredes.
1.4.3.5.2. Techos con paneles suspendidos o colocación de cielorrasos fonoabsorbentes.
1.4.4. Tipos de disturbios de ruido electromagnético
1.4.4.1. Inestabilidad en dimmers y balastros
1.4.4.2. Disturbios en la iluminación tales como parpadeo
1.4.4.3. Radio recepción pobre
1.4.4.4. Inestabilidad en sistemas de control
1.4.4.5. Fluctuación en mediciones de flujo
1.4.4.6. Fallas en sistemas de cómputo
1.4.4.7. Molestas fallas de PLCs
1.4.4.8. Rebote de medidores análogos
1.4.4.9. Problemas con controles de termostatos
1.4.5. Soluciones de Ruido electromagnético
1.4.5.1. Puesta a tierra con baja impedancia
1.4.5.1.1. Esta es la técnica más común, particularmente en bajo voltaje
1.4.5.1.2. las corrientes de falla a tierra son normalmente altas pero los voltajes del sistema permanecen controlados bajo condiciones de falla.
1.4.5.1.3. Estándares
1.4.5.2. Supresión de cargas inductivas
1.4.5.2.1. se conecta un aparato de supresión de sobre tensión directamente en paralelo con la bobina del aparato de campo
1.4.5.2.2. Si el aparato inductivo tiene conectores enchufables, el aparato de supresión de sobretensión se puede instalar en el bloque terminal de la salida del relevador.
1.4.5.3. Amplificadores diferenciales
1.4.5.3.1. circuito pensado para amplificar la diferencia de dos señales.
1.4.5.3.2. presenta excelentes propiedades de aislación
1.4.5.3.3. está alimentado por dos fuentes de polaridades opuestas (V1 y V2) que en general tienen valores +V y -V respectivamente
1.4.5.4. Amplificador de instrumentación
1.4.5.4.1. uno de los amplificadores más útil, versátil y precisos en la actualidad.
1.4.5.4.2. Está formado por tres amplificadores operacionales y siete resistencias
1.4.5.5. Filtrado
1.4.5.5.1. Son circuitos caracterizados por una entrada y una salida
1.4.5.5.2. en la salida solo aparecen parte de las componentes de frecuencia de la señal de entrada
1.4.5.5.3. Tipos de filtro
1.4.6. Compatibilidad electromagnética
1.4.6.1. EMC Compatibilidad electromagnética
1.4.6.1.1. Aptitud de un aparato ó un sistema para funcionar en forma satisfactoria en su entorno electromagnético
1.4.6.1.2. Test EMC
1.4.6.2. EMI Interferencia electromagnética
1.4.6.2.1. interferencia o perturbación electromagnética es todo fenómeno electromagnético susceptible a de crear problemas de funcionamiento en un dispositivo
2. Plantas Antiguas
2.1. Modernización de plantas
2.1.1. Objetivos
2.1.1.1. Nomalización de instrumentos
2.1.1.1.1. Único proveedor
2.1.1.1.2. Instrumentos de la misma marca
2.1.1.2. Sustituir instrumentos defasados
2.1.1.2.1. Examinar del estado de instrumentos de la planta
2.1.1.3. Incorporar sistemas de control avanzado
2.1.1.3.1. Incorporación de analizadores de linea
2.1.1.3.2. Implementación de control distribuido
2.1.1.3.3. Estudiar funcionamiento de los nuesvos instrumentos
2.1.1.4. Mejorar la seguridad de operacion de la planta
2.1.2. Criterios
2.1.2.1. Minimo tiempo posible
2.1.2.1.1. Establecer tiempos
2.1.2.1.2. Establecer acuerdos con clientes
2.1.2.1.3. Poner en marcha el control
2.1.2.2. Pocas interrupciones en la fabricación
2.1.2.3. Menores costos de modernización
2.1.2.3.1. Coste entre 2% y 10% de modernización
2.1.2.3.2. Tiempos de paro mínimos
2.1.3. Planificación
2.1.3.1. Crear programas de planificación en ordenadores
2.1.3.1.1. Fechas
2.1.3.1.2. Actividades a realizar
2.1.3.1.3. Cursos de praparación
2.1.3.1.4. Simuladores de el proceso nuevo
2.1.3.2. Establecer objetivos
2.1.3.2.1. Tiempo disponible
2.1.3.2.2. Recursos humanos
2.1.3.2.3. materiales necesarios
2.1.3.3. Equipo afectado y equipo nuevo necesario
2.1.3.3.1. Instalación de equipos en paralelo a los antiguos
2.1.3.3.2. Sustirtuir entaramente equipos viejos
2.1.4. Instrumentos de campo
2.1.4.1. Transmisores
2.1.4.1.1. Electrónicos convencionales
2.1.4.1.2. Inteligentes
2.1.4.2. Válvulas de control
2.1.4.2.1. Señal de 4-20mA
2.1.4.2.2. Acople con actuadores electromecánicos
2.1.4.3. Instrumentos de panel
2.1.4.3.1. Sustitución de instrumentos de panel
2.1.4.3.2. Neumáticos de última generación
2.1.4.3.3. Electrónicos
2.1.4.3.4. Digitales
2.1.5. Modernización Total
2.1.5.1. Sustitución de toda la planta
2.1.5.2. Control distribuido
3. Plantas Nuevas
3.1. Generalidades
3.1.1. Planificación correcta
3.1.2. Formación de personal
3.1.3. Uso de simuladores de la planta
3.1.4. Entrenamiento con fábricas asociadas
3.2. Ingenieria
3.2.1. Se realiza en la oficina cuando la planta es pequeña
3.2.2. Se contrata una firma exterior que facilite el personal en plantas grandes
3.2.3. Solicita especificaciones que debe cumplir los instrumentos de medición y control
3.2.4. Selecciona los instrumentos adecuados para uso en el sistema
3.2.5. Diseño y especificación del panel de control
3.3. Instalación
3.3.1. Las compañías instaladoras ubican los instrumentos del proceso y los cables.
3.3.2. La instalación es supervisada por el cliente
3.4. Calibración
3.4.1. Comprobar estado de instrumentos y recalibrarlos
3.4.2. Se realiza con el instrumento instalado
3.4.3. Se utilizan maletas de calibración neumáticas y electrónicas
3.4.3.1. Pequeño compresor de aire sin aceite
3.4.3.2. Presión de 2Kg/cm^2
3.4.3.3. Calibra los instrumentos neumáticos de campo
3.4.3.4. Generan y reciben señales de 4-20mA y 1-5V CC
3.5. Puesta en marcha
3.5.1. Arranque de prueba en tanques y tuberis con agua por 24 horas
3.5.1.1. Permite detectar y corregir problemas
3.5.1.2. Evita perdidas en el sistema de producción
3.5.1.3. Limpia el sistema
3.5.2. Ajuste de los instrumentos de control
3.5.2.1. Ajuste de tiempos y parámetros
3.5.2.2. Método prueba y error
3.5.2.3. Definir puntos de consigna
3.5.2.4. Proporciona + integral + Derivativo
3.5.2.4.1. Método Ziegler and Nichols
3.5.2.4.2. Método de ganancia límite
3.6. Mantenimiento
3.6.1. Programas de mantenimiento
3.6.1.1. Trabajos correctivos
3.6.1.2. Trabajos preventivos
3.6.1.3. órdenes de trabajo
3.6.1.4. Mantenimiento de stock
3.6.2. Conceptos a tomar en cuenta
3.6.2.1. Fiabilidad
3.6.2.1.1. Probabilidad de que un instrumento funciones sin averías en un tiempo
3.6.2.2. Mantenibilidad
3.6.2.2.1. Probabilidad de que un fallo sea reparado antes de un tiempo
3.6.2.3. Indice de fallo
3.6.2.3.1. Relación entre el número de fallos entre el número de instrumentos en un tiempo
3.6.2.4. Tiempo medio entre fallos
3.6.2.4.1. Número de horas de funcionamiento entre el número de averías
3.6.2.5. Disponibilidad
3.6.2.5.1. Probabilidad de que un instrumento o equipo esté disponible dentro de un tiempo
3.6.3. Contratado
3.6.3.1. Trabajos de mantenimiento programados
3.6.3.2. Reparaciones de envergadura
3.6.3.3. Obras nuevas
3.6.4. Propio
3.6.4.1. Personal de la empresa
3.6.4.2. Mantenimientos correctivos