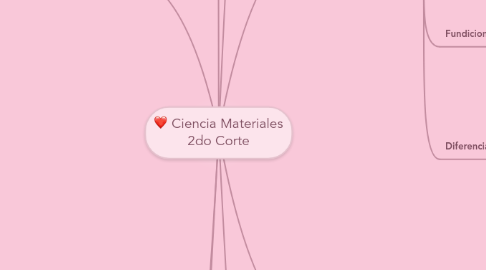
1. Clase 2
1.1. Ensayos de Materiales
1.1.1. Rigurosidad
1.1.1.1. a) Ensayos científicos: De gran precisión, fidelidad y sensibilidad. Tratan de extraer valores de ciertas magnitudes físicas. Ej: densidad. b) Ensayos tecnológicos: Se utilizan para comprobar si las propiedades de un determinado material son adecuadas para una cierta utilidad. Son rápidos y simples. Se persigue con el ensayo obtener información del material con respecto a las cargas normales del trabajo
1.1.2. Naturaleza
1.1.2.1. Ensayos químicos: Para conocer la composición química (cualitativa y cuantitativa) así como su comportamiento ante agentes químicos. Ensayos físicos: Se trata de determinar propiedades físicas (densidad, conductividad eléctrica, …) Ensayos metalográficos: Consiste en analizar la estructura interna del material al microscopio. Ensayos mecánicos: Determina la resistencia y elasticidad material cuando se somete a diferentes esfuerzos (tracción, compresión, flexión,...)
1.1.3. Utilidad
1.1.3.1. Ensayos destructivos: Los materiales sometidos a ensayo sufren rotura o daño en su estructura. Ensayos no destructivos: No se daña la estructura ni sufre deformación, aunque se analizan los defectos que puedan ocasionarse
1.1.4. Ensayos mecanicos
1.1.4.1. Traccion
1.1.4.2. Flexion
1.1.4.3. Dureza
1.1.4.4. Fluencia
1.1.4.5. Fatiga
1.1.4.6. Impacto
1.1.5. Metodos
1.1.5.1. Brinell
1.1.5.2. Vickers
1.1.5.3. Rockwell
1.2. Fractura
1.2.1. Se define fractura como la separación de un sólido bajo un estado de esfuerzos en dos o más trozos.
1.2.1.1. Tipos
1.2.1.1.1. a) Fractura muy dúctil en la cual la probeta se estricciona hasta Ilegar a un punto. (b) Fractura moderadamente dúctil después de cierta estricción. (c) Fractura frágil sin ninguna deformación plástica
1.2.2. Factores de rotura
1.2.2.1. Temperatura: Actualmente se realizan ensayos en diferentes temperaturas. Comportamiento en frío: A medida que se enfríe el periodo plástico va desapareciendo, se convierte de material dúctil a frágil. El límite elástico se aproxima a la tensión de rotura. Comportamiento en caliente. Aumenta el periodo plástico, disminuye la tensión de rotura. Velocidad: Al aumentar la velocidad disminuimos el periodo plástico. No cambia la Tensión de Rotura. Estructura Cristalina: Grano grande y abierto. El material rompe antes, NO hay periodo plástico. Grano pequeño y cerrado. Hay periodo plástico, el material rompe más tarde.
2. Clase 3
2.1. Ensayos Destructivos
2.1.1. Ensayos destructivos: 1. Ensayo en uniformidad en la soldadura. 1.1. Ensayo de rotura sobre piezas con entallas. 1.2. Ensayo de plegado libre. 1.3. Ensayo de plegado guiado. 2. Ensayo de tracción. 2.1. Alargamiento y elongación. 2.2. Dureza. 2.3. Valores de impacto. 3. Ensayo de chispa. 4. Ensayo de rotura. 5. Ensayo de compresión. 6. Ensayo de corte o de cortadura.
2.1.2. Ensayos destructivos: 7. Ensayo de plegado. 8. Ensayo de doblez. 9. Ensayo de flexión al choque en pieza entallada. 10. Ensayo de embutición 11. Ensayo de doblado de uno a otro lado. 12. Ensayo de fatiga. 13. Ensayo de dureza. 13.1. Ensayo de dureza según brinell. 13.2. Ensayo de dureza según vickers. 13.3. Ensayo de dureza según rockell.
2.2. Ensayos No Destructivos
2.2.1. ENSAYOS MAGNETICOS. Se utiliza el magnetoscopio. Se hace circular una corriente y se crea un campo magnetico en la pieza a probar. No existe defecto si las líneas del campo magnético discurren paralelas, uniformes y equidistantes. Si existe defecto las líneas del campo magnético se desviaran, y donde este el defecto se verán mas líneas del campo.
2.2.2. ENSAYOS POR LIQUIDOS PENETRANTES. Se emplea para detectar discontinuidades abiertas en la superficie de los materiales no porosos. El liquido se aplica sobre la superficie del material y penetra sobre la discontinuidad o defecto.
2.2.3. ENSAYOS DE RAYOS X. Los rayos X son vibraciones electromagnéticas invisibles que se propagan a la velocidad de la luz, pero con una longitud de onda muy corta
2.3. Conductores
2.3.1. Metalicos
2.4. No conductores
2.4.1. Ceramicos
2.5. Semi-conductores
3. Clase 4
3.1. Los metales
3.1.1. Aleacion
3.1.1.1. Las propiedades de las aleaciones dependen de su composición y del tamaño, forma y distribución de sus fases o micro constituyentes. La adición de un componente aunque sea en muy pequeñas proporciones, incluso menos de 1% pueden modificar intensamente las propiedades de dicha aleación. Las propiedades físicas y químicas son, en general, similares a la de los metales, sin embargo las propiedades mecánicas tales como dureza, ductilidad, tenacidad etc. pueden ser muy diferentes a las que pueden tener los componentes de forma aislada.
3.1.1.1.1. Las aleaciones no tienen una temperatura de fusión única, dependiendo de la concentración, cada metal puro funde a una temperatura, coexistiendo simultáneamente la fase líquida y fase sólida. Hay ciertas concentraciones específicas de cada aleación para las cuales la temperatura de fusión se unifica. Esa concentración y la aleación obtenida reciben el nombre de eutéctica, y presenta un punto de fusión más bajo que los puntos de fusión de los componentes
3.1.1.2. Aleacion ferrosa
3.1.1.2.1. tienen como elemento mayoritario el Fe y en general, son aleaciones fuertes, maleables, de bajo costo y relativamente fáciles de obtener. La mayor producción de estas son los aceros, aleaciones Fe – C, a los que cambiando el porcentaje de estos elementos y agregando algunos otros, se les pueden dar propiedades específicas, dependiendo de la industria a la que se van a aplicar
3.1.1.3. Aleacion No ferrosa
3.1.1.3.1. Los materiales No Ferrosos no contienen hierro. Estos incluyen el aluminio, cobre, cromo, níquel, magnesio, zinc, plomo y otros elementos metálicos.
3.1.2. DIAGRAMA FE-C
3.1.2.1. Se representan las transformaciones que sufren los aceros al carbono con la temperatura, admitiendo que el calentamiento (o enfriamiento) de la mezcla se realiza muy lentamente, de tal forma que el proceso de mezcla se realiza completamente.
3.1.2.1.1. Líquidus: temperatura a la cual el líquido empieza a solidificarse bajo condiciones de equilibrio. Sólidus: temperatura durante la solidificación de una aleación a la cual la última parte de la fase liquida se solidifica. Austenización: Calentamiento de un acero dentro de un rango de temperatura de la austenita para que su composición se convierta en austenita. La temperatura de la austenización varia dependiendo de la composición del acero Eutectoide: Acero con un 0,8% C. Hipoeutectoide: Acero con menos de 0,8% C. Hipereutectoide: Acero con un 0,8% C a un 1,76% C
3.1.2.2. Clasificacion
3.1.2.2.1. Aceros de bajo contenido de carbono (aceros estructurales) 0.003-0.8% de C, hipoeutectoide (ferrita+perlita) Aceros de alto contenido de carbono (aceros de herramientas) 0.8-1.76% de C, hipereutectoide (perlita+cementita) Fundición de hierro 1.76-6.65% de C: 1.76-4.26% de C hipoeutectica 4.26-6.65% de C hipereutectica
3.1.2.3. Fases
3.1.2.3.1. Fase Austenítica (0 hasta 2,1% C)
3.1.2.3.2. Fase Ferrita alfa α (0 hasta 0,022%C)
3.1.2.3.3. Fase Ferrita delta δ (0 hasta 0,09%C)
3.1.2.3.4. Fase Cementita (0,022% a 6,67%C)
3.1.2.3.5. Fase Martensita
3.1.2.3.6. Fase Ledeburita
3.1.2.3.7. Fase Perlita
3.1.2.3.8. Fase Grafito
3.1.3. Acero
3.1.3.1. Acero Eutectoide
3.1.3.2. Acero Hipoeutectoide
3.1.3.3. Acero hipereutectoide
4. Clase 5
4.1. Horno alto
4.1.1. Un alto horno es una instalación industrial en la que la mena contenida en el mineral de hierro es transformada en arrabio, también llamado hierro bruto. Estas instalaciones reciben este nombre por su gran altura que suele estar en torno a los 30 metros. El horno es alimentado con una mezcla de mineral de hierro, carbón de coque y fundente, generalmente piedra caliza
4.2. El convertidor LD
4.2.1. Es una vasija de grandes dimensiones que se construye externamente en acero e internamente de material refractario. Al Convertidor llega el arrabio (60-80%) producido en el Horno Alto – > 1320 ºC- junto con la chatarra (20-40%) y una vez cargados, se les añade los fundentes y prerreducidos necesarios para conseguir la composición del acero a fabricar.
4.3. Colada convencional
4.3.1. Es uno de los procesos más antiguos que se conocen para trabajar los metales. El proceso consiste en dar forma a un objeto al verter el material líquido en una cavidad formada en un bloque de arena aglomerada u otro material que se llama molde y dejar que se solidifique el líquido
4.4. Colada continua
4.4.1. Cuando se requiere un material de sección constante y en grandes cantidades se puede utilizar el método de la colada continua. En este método el contenido de la cuchara se vierte en un crisol que mediante una válvula va suministrando una cantidad constante de arrabio sobre un molde con la forma requerida. Por gravedad el material fundido pasa por el molde.
4.5. Elementos de aleacion
4.5.1. Aluminio Boro Cobalto Plomo Estaño Manganeso Molibdeno Niquel cromo Silicio Tungsteno Vanadio Zinc titanio
4.6. Tratamientos de acero
4.6.1. Superficiales
4.6.1.1. Cromado: recubrimiento embellecedor superficial para proteger de la oxidación. Galvanizado: recubrimiento superficial con zinc que se da al acero. Niquelado: similar al cromado pero con níquel. Pavonado: tratamiento superficial que se da a piezas pequeñas de acero, como la tortillería, consiste en aplicar una capa superficial de óxido, con el que se cubren las piezas y se evita su corrosión. Pintura: recubrimiento protector, usado en estructuras, automóviles, barcos.
4.6.2. Termicos
4.6.2.1. Temple
4.6.2.2. Recocido
4.6.2.3. Revenido
4.6.2.4. Normalizado
4.6.3. Termoquimicos
4.6.3.1. Cementación con carbono: se suelen emplear sólidos como el carbón o líquidos como cianuro sódico, o gases como mezclas de monóxido de carbono y metano. Nitruración con nitrógeno: se alcanzan temperaturas alrededor de los 500ºC y en el seno de una atmósfera de amoniaco (NH3), los átomos de nitrógeno se asocian con elementos constituyentes de la aleación como el cromo constituyéndose compuestos extraordinariamente duros.
4.6.3.2. Cianuración: en este tratamiento se alcanzan temperaturas del orden de 850ºC y los elementos que se difunden son: cianuro sódico, cloro y carbonato sódico. Sulfinización: se eleva a temperatura hasta 600ºC y se somete a la pieza a tratar a un baño de sales ricas en azufre, combinándose este elemento superficialmente con la pieza a tratar obteniéndose una extraordinaria dureza superficial.
5. Clase 1
5.1. DEFORMACION
5.1.1. Un cuerpo que cambia de tamaño y forma atravez de un esfuerzo interno
5.1.2. TIPOS
5.1.2.1. Deformacion Elastica.
5.1.2.1.1. Es aquella en la que el cuerpo recupera su forma original al retirar la fuerza que le provoca la deformación
5.1.2.1.2. Es aquella en el que el cuerpo recupera su forma original al retirar la fuerza que le provoca a la deformación.
5.1.2.2. Deformacion Plastica
5.1.2.2.1. Es aquella en la que el cuerpo no recupera su forma original al retirar la fuerza que le provoca la deformación. En los metales la deformación plástica ocurre mediante la formación y el movimiento de dislocaciones.
5.1.2.2.2. Es aquella en el que el cuerpo no recupera su forma original al retirar la fuerza que la provoca la deformación.
5.2. MECANISMOS DE ENDURECIMIENTO
5.2.1. Endurecimiento por disminución del tamaño de grano
5.2.1.1. Los bordes de grano actúan como barreras al movimiento de las dislocaciones. -Al pasar de un grano a otro las dislocaciones deben cambiar de dirección. - Los bordes de grano son desordenes de átomos, existiendo discontinuidades en los planos de deslizamiento.
5.2.2. Endurecimiento por solución solida
5.2.2.1. El endurecimiento por solución solida se debe a la interacción entre los átomos de soluto y las dislocaciones. Es el fenómeno por medio del cual un metal dúctil se vuelve más duro y resiste a medida que se deforma plásticamente. La efectividad del soluto depende de la diferencia de tamaño con respecto al solvente, y del porcentaje agregado. Si el átomo de soluto es más grande que el del solvente, se inducen campos de compresión, mientras que si es más pequeño, son de tracción.
5.2.3. Endurecimiento por deformación en frio
5.2.3.1. Es el fenómeno por el cual un metal dúctil se vuelve más duro y resistente a medida que es deformado plásticamente. Se llama trabajo en frio debido a que la deformación se da a una temperatura por debajo de la fusión del metal
5.2.3.1.1. Trefilado
5.2.3.1.2. Laminacion
5.2.3.1.3. Embutido
5.2.3.1.4. Extrusion
5.2.4. Endurecimiento por precipitación o envejecimiento.
5.2.4.1. -Las dislocaciones se desplazan por el material con mayor o menor facilidad atendiendo al trabajo necesario realizar para romper y crear enlaces. - Si dentro de un material se introducen partículas rígidas, por las cuales no pueden moverse las dislocaciones, estas se atascarán (anclado de dislocaciones) al llegar a dichas partículas. -La velocidad a la que se produce la precipitación varía con la temperatura. A temperaturas bajas, se requiere tiempos más largos para completar la precipitación debido a que la velocidad de difusión es muy lenta
5.3. MECANISMOS DE RESTAURACION
5.3.1. Recido
5.3.2. Recuperacion
5.3.3. Recristalizacion
5.4. LA PLASTICIDAD
5.4.1. Es la propiedad mecánica de un material de deformarse permanentemente e irreversiblemente cuando se encuentra sometido a tensiones por encima de su rango elástico, es decir, por encima de su límite elástico.
5.5. MECANISMOS DE ENDURECIMIENTO
5.5.1. Endurecimiento por disminución del tamaño de grano
5.5.2. Endurecimiento por solución solida
6. Clase 6
6.1. Aceros
6.1.1. Nomenclatura
6.1.1.1. ASTM International es una de las organizaciones internacionales de desarrollo de normas más grandes del mundo. En ASTM se reúnen productores, usuarios y consumidores, entre otros, de todo el mundo, para crear normas de consenso voluntarias. AISI American Iron and Steel Institute (Instituto americano del hierro y el acero), SAE Society of Automotive Engineers (SociedadNorteamericana de Ingenieros Automotores). AWS (American Welding Society) ASME (American Society of Mechanical Engineers), ANSI (American National Standards Institute) ACI (Alloy Casting Institute)
6.1.1.1.1. ASTM
6.1.1.1.2. AISI
6.1.1.1.3. SAE
6.1.2. Aceros al carbono
6.1.2.1. Más del 90% de todos los aceros son aceros al carbono. Estos aceros contienen diversas cantidades de carbono y menos del 1,65% de manganeso, el 0,60% de silicio y el 0,60% de cobre
6.1.3. Aceros aleados
6.1.3.1. Estos aceros contienen un proporción determinada de vanadio, molibdeno y otros elementos, además de cantidades mayores de manganeso, silicio y cobre que los aceros al carbono normales
6.2. Fundiciones
6.2.1. Tratamientos termicos
6.2.1.1. Recociodo Revenido Temple Normalizado
6.2.1.2. Fundicion gris
6.2.2. Fundicion Blanca
6.2.2.1. Maleables
6.3. Diferencias entre aceros y fundiciones
6.3.1. Los aceros tienen un porcentaje menor de carbono (<1,76% C) que las fundiciones (>1,76% C). - Los aceros son más caros que las fundiciones. - Las fundiciones son más duras que los aceros. - Los aceros son más tenaces que las fundiciones, es decir, soportan mejor los golpes.
7. Clase 7
7.1. Materiales no ferrosos
7.1.1. Tratamientos Termicos
7.1.1.1. Homogenizacion Solubilidad Recocido
7.1.2. Cobre Bronce Aluminio Cromo Zinc Estaño Plomo Cobalto Titanio Magnesio
8. Clase 8
8.1. Procesos de conformado
8.1.1. Trabajo en frio
8.1.1.1. Ventajas
8.1.1.1.1. Mejor precisión, menores tolerancias, mejores acabados superficiales, posibilidades de obtener propiedades de dirección deseadas en el producto final y mayor dureza de las partes
8.1.1.2. Desventajas
8.1.1.2.1. Ya que requiere mayores fuerzas porque los metales aumentan su resistencia debido al endurecimiento por deformación, produciendo que el esfuerzo requerido para continuar la deformación se incremente y contrarreste el incremento de la resistencia la reducción de la ductilidad y el aumento de la resistencia a la tensión limitan la cantidad de operaciones de formado que se puedan realizar a las partes
8.1.2. Trabajo en caliente
8.1.2.1. Ventajas
8.1.2.1.1. La porosidad en el metal es considerablemente eliminada. La mayoría de los lingotes fundidos contienen muchas pequeñas sopladuras. Estas son prensadas y a la vez eliminadas por la alta presión de trabajo. Las impurezas en forma de inclusiones son destrozadas y distribuidas a través del metal. Los granos gruesos o prismáticos son refinados. Dado que este trabajo está en el rango recristalino, seria mantenido hasta que el límite inferior es alcanzado para que proporcione una estructura de grano fino.
8.1.3. Acero es la denominación que comúnmente a una aleación de hierro con una cantidad de carbono variable entre el 0,03% y el 1,76% en peso de su composición, dependiendo del grado.
8.1.4. Trabajo en lamina
8.1.4.1. Cizallado Troquelado Doblado Embutido Trefilado
8.1.5. Trabajo en Bloque
8.1.5.1. Fundicion Laminado Forjado