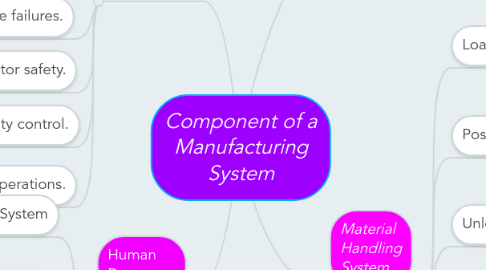
1. Computer Control System
1.1. Communicate Instructions to workers.
1.1.1. In manually operated workstations that perform different tasks on different work units,operators must receive processing or assembly instructions for the specific work unit.
1.2. Download parts programs.
1.2.1. The computer sends these instructions to computer-controlled machines.
1.3. Control material handling system.
1.3.1. This function also coordinates the activities of the material handling system with those of the workstations.
1.4. Schedule production.
1.4.1. Certain production scheduling functions may be accomplished at the site of the manufacturing system.
1.5. Diagnose failures.
1.5.1. This involve diagnosing equipment malfunctions, preparing preventive maintenance schedule & maintaining the spare parts inventory.
1.6. Monitor safety.
1.6.1. This function ensures that the system does not operate in an unsafe manner.
1.7. Maintain quality control.
1.7.1. The purpose of this control functions is to detect & reject defective work units produced by the system.
1.8. Manage operations.
1.8.1. This consists of managing the overall operations of the manufacturing system, either directly or indirectly.
2. Human Resources
2.1. Manually Operated Manufacturing System
2.1.1. Direct labor workers perform the value-added physical work on the part or product.
2.2. Automated Manufacturing System
2.2.1. Direct labor performs functions such as loading and unloading parts, changing and sharpening tools.
2.2.1.1. Computer programmers and operators
2.2.1.2. NC part programmers
2.2.1.3. Maintenance and repair personnel
3. Production Machine
3.1. Manual Operated Machine
3.1.1. Controlled / Supervised by worker
3.1.2. Machine provide the power, Worker Provide Control
3.2. Semi Operated Machines
3.2.1. Performs a portion of the work cycle under some form of program control & a worker tends to the machine for the remainder of the cylce
3.3. Fully Operated Machines
3.3.1. Operated with no human attention
4. Material Handling System
4.1. Loading
4.1.1. Moving the work units into the production machine or processing equipment form a source inside the station.
4.2. Positioning
4.2.1. Its requires the part to be in a known location & orientation relative to the workhead/tooling that performs the operation
4.2.2. Positioning in the production equipment is often accomplished by means of workholder.
4.3. Unloading
4.3.1. The work unit must be unloaded, that is, removed from the production machine and either placed in a container at the workstation or prepared for transport to the next workstation in the processing sequence.
4.4. Transporting
4.4.1. Moving parts between workstations in a multi-station system.
4.4.1.1. Fixed Routing
4.4.1.1.1. Work unit always flow through the same sequence of workstations
4.4.1.1.2. Most production lines exemplify this category
4.4.1.2. Variable Rounting
4.4.1.2.1. Work units are moved through a variety of different station sequences
4.4.1.2.2. Most job shops exemplify this category
4.5. Temporary Storage
4.5.1. Temporary storage of work units