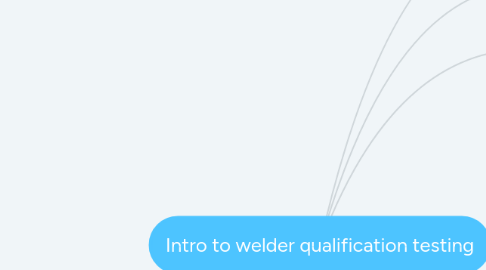
1. General Code Requirements
1.1. Know them!!!
1.1.1. Don't listen to what you hear on t he job unless you see it in the code
1.1.2. Rules Change between codes. Be aware of the differences
1.1.3. Project Specifications may apply
1.2. Have the code
1.2.1. Before testing for review
1.2.1.1. Refresh yourself on the requirements
1.2.1.1.1. Make a Traveler/Checksheet
1.2.1.1.2. Don't get production/procedure/Performance requirements confused
1.2.1.1.3. Are additional Requirements required?
1.2.2. During Testing For Reference
1.2.2.1. Test Instructions for Welder and Test Supervisor
1.2.2.2. Review with welder
1.2.3. After Testing for record
1.2.3.1. If I review a record certifying compliance with a code, I should have the code!
1.3. Scope and responsibilities
1.3.1. Companies need to know where they fall
1.3.2. There is more to code compliant welding than Performance
1.3.2.1. 5 or so pages in D1.1 Paragraphs. Rest Tables/Figures.
1.3.3. Some codes require MFG to witness tests.
1.3.3.1. ASME IX Requires
1.3.3.1.1. B31.3 allows exceptions
1.3.4. Company is always responsible for their welding
1.3.5. A company that doesn't test a welder....Hmmmm
1.4. Default for Most US Codes
1.4.1. MFG or Contractor tests own welders
1.4.2. WPS Required
1.4.3. Essential variables must be addressed
1.4.3.1. Procedure Variables do not affect Performance Qualification
1.4.4. Some or all may be subcontracted
1.4.5. Company Maintains responsibility
1.4.6. Testing May be many methods
1.4.7. Some require welder vision test
1.4.7.1. D17.1 Requires
1.4.7.2. D1.5 Suggests
1.4.8. Some require training (248)
1.4.8.1. Navsea 248
1.4.8.2. AWS SENSE Program (Not Prior to Testing Though)
1.4.9. May allow acceptance of other testing.
1.4.10. Many more pages for compliance than just testing!!
1.4.11. Do not require a CWI. Other Options exist
2. What is a good welder?
2.1. Code rules for tests may not be sufficient
2.1.1. Companies may add requirements
2.2. Production conditions vs test
2.2.1. Making a 3G test 42" off floor ...HARD?
2.3. Is time a factor?
2.3.1. Weld V Grinding
2.3.2. Every pass Cooling to touch ??? Hmmm
2.4. Should there be a "knowledge" factor.
2.4.1. Not required by codes
2.4.2. "Cetfied Welder" implies knowledge
2.4.3. Knowledge is required for AWS SENSE welder
2.4.4. Break machine down and have setup (NOCTI)
2.5. Varies by project/Industry
2.5.1. Good welder in coal mine may not be a good welder on a bridge
2.5.2. SS Pipe Welder maynot have a cluse about Carbon with SMAW
2.6. Test may "qualify" for many welds but does not verify ability.
2.6.1. If accepting previous qualifications, give a wiorkmanship test
2.6.2. Place a workmanship sample in a position similar to production conditions
3. Building your own "Program"
3.1. Have a written system
3.2. AWS B5.4
3.2.1. Great Starting Point.
3.2.2. Calibration Req.
3.2.3. Qualifications of Inspectors
3.2.4. May add requirements
3.2.4.1. Time Limits
3.2.4.1.1. Required by Code?
3.2.4.1.2. Cost per test?
3.2.4.1.3. Excessive Grinding/Cooling
3.2.4.2. Tighter WPS requirements
3.2.4.2.1. Welder may be better at welding with other settings.
3.2.4.2.2. Welder may have no idea how to set equipment but WPS gets them "through" the test.
3.2.4.2.3. Could force difficult parameters to show skill.
3.2.4.3. Looser WPS variables
3.2.4.3.1. Welder makes decision
3.2.4.3.2. Must comply with WPS requirments for code
3.2.4.3.3. may cause undue confusion
3.2.4.4. modify test location/restrictions
3.2.4.4.1. Fixed location
3.2.4.4.2. Resticion objects
3.2.4.5. additional hold points.
3.2.4.5.1. Before closing root on Pipe
3.2.4.5.2. Each layer
3.2.4.6. additional tests
3.2.4.6.1. sides and face/root
3.2.4.6.2. Dest and NDE
3.2.4.6.3. bead width/height variation
3.2.4.6.4. Company INspector VT
3.2.4.6.5. Written Knowledge?
3.3. Can be better than AWS ATF welders
3.3.1. Code only tests may be "easy"
3.3.2. Addede requirements may be attractive to some
3.3.3. Added Requirements may be a negative for some.
3.3.4. Develop a written description of "levels" for a test.
3.4. Reviewed by Local Industry
3.4.1. Thier perception may be "code wrong" but valuable
3.4.2. Find out what they require and build around. Company Specific "test plans"
3.4.2.1. Great for Students
3.4.2.2. Great for potential employee screening
3.5. Personnell
3.5.1. Who must supervise?
3.5.2. Who has final certification authority.
3.5.3. What do they need to know.
3.5.4. Is a "certification" needed
4. Process
4.1. Know what the specific code requires
4.1.1. Never test anyone without having the code
4.1.2. Have the code available onhand
4.1.3. Exceptions allowed/requested by customer-Document!
4.1.4. If additional restrictions allowed/requested. Document
4.1.5. Refresh your knowledge
4.2. Verify the requested qualifications and review with the customer
4.2.1. More to it than welder testing for production
4.2.1.1. Codes require more than WPQ
4.2.1.2. What does the company quality system say
4.2.1.3. What do customers require/expect
4.2.2. Certified Welder Article
4.2.3. Show code paragraph regarding responsibility
4.2.3.1. Manufacturers/Contractors always responsible for t hier welding.
4.2.3.2. If a company has no interest other than "get them certified" be cautious
4.3. Document review of requirements
4.3.1. Welder Test Plan/WPQTI
4.3.2. Document additions/exceptions and obtain sig
4.3.3. Who is required to sign the "Bottom Line"
4.4. Review reqts with welder
4.4.1. Safety
4.4.2. WPS Review
4.4.3. Acceptance Criteria
4.4.4. Equipment Operation
4.4.5. Hold Points
4.4.6. Position Secured
4.4.7. Test Assembly ID
4.4.8. Filler Metal locations
4.4.9. Using your "opinion"
4.4.10. Grinding
4.4.11. Others in booth
4.4.12. welding outside WPS ranges
4.5. Fitup and Tack
4.5.1. Tack Locations
4.5.1.1. May interfere with bends
4.5.1.2. locations not adjacent to bends for pipes
4.5.1.3. bridge tacks anywhere
4.5.2. May be any process if not in joint
4.5.3. Backing Strip Standoff
4.5.3.1. Clamps/Fixtures
4.5.3.2. Hot Tack
4.5.4. No Visible misalignment
4.5.4.1. Unless required to make sure skills exist
4.5.5. If tacks in Joint, length location
4.5.5.1. keep em short if not done in position
4.5.5.2. for pipe, allow option of 2 but welder responsible for distortion
4.6. Mark test Assy
4.6.1. Unique # (database)
4.6.2. At destructive test locations preferred
4.6.3. TOP on pipes
4.6.4. no names/ss #
4.7. Locate in position
4.7.1. What variation does code allow?
4.7.1.1. +/- 5 degrees? Is it written?
4.7.1.2. Eyeball should be good enough
4.7.2. Allowed to move location but not position.
4.7.2.1. May be restricted for higher "level" tests.
4.7.3. No removal for grinding by welder
4.7.4. If noticed removed from position-Fail
4.8. weld root pass
4.8.1. Start and Stop Required?
4.8.2. Hold Point
4.8.2.1. Make sure welder knows
4.8.2.1.1. Acceptance Criteria
4.8.2.1.2. Gromdimg restrictions
4.8.2.2. May not be required by code but
4.8.2.2.1. Good way to verify abilities quickly
4.8.2.2.2. Help assure no time wasted.
4.8.2.3. Before grinding (if allowed)
4.8.3. Welder may correct anything BEFORE requesting inspection
4.8.4. No "coaching"
4.8.5. Observation of skills may require "opinion"
4.9. inspect and document
4.9.1. WPQTI/Traveler
4.9.2. Some codes have acceptance criteria some do not
4.9.3. OQE
4.9.3.1. Photos of Root Optional
4.9.3.2. Video optional
4.9.3.2.1. ASME Code Case?
4.9.3.3. Completion of WPQR implies root acceptable per code.
4.9.4. May not be possible with pipe until specimens cut or RT
4.10. fill and cap
4.10.1. Follows WPS
4.10.2. Listen/look for excessive grinding.
4.10.3. Observe position
4.10.4. No coaching
4.10.5. Make sure welder knows requirements
4.11. inspect final layer
4.11.1. Know acceptance criteria Code
4.11.2. Know Acceptance criteria Customer
4.11.3. Does the code require inspection before grinding?
4.12. Remove from position
4.12.1. Verify ID number in readable condition
4.13. verify documentation matches test#
4.14. Perform Testing
4.14.1. Mark Specimens before removing
4.14.2. KNow Locations for removal
4.14.3. Know Dimensions
4.14.4. Mark Face and Root if applicable
4.14.5. Thermal Cutting Requirements?
4.14.5.1. Some codes require grinding if thermally cut
4.14.6. Keep Drop identified until tests are done.
4.14.7. Know Bend radius required for base/weld metal
4.14.8. If IP is visible on specimens, review code!
4.14.9. Maintain Specimens until documentation completed.
4.14.10. I keep failed specimens but check the code/quality system
5. Specific Code requirements
5.1. AWS D1.1 Module
5.1.1. Who can test welders
5.1.1.1. D1.1 Clause 4.2.2
5.1.2. Who is reponsible for welder qualification
5.1.2.1. D1.1 Clause 4.2.2
5.1.2.2. Can Be subcontracted but responsibility stays the same
5.1.3. What Weld Tests are "required"
5.1.3.1. Depends on Ranges for production
5.1.3.2. See Clause 4.17 for figures
5.1.3.2.1. Rolling Dirction Optional
5.1.4. What are the qualified ranges
5.1.4.1. Listed in Clause 4, Part C
5.1.4.1.1. Weld Type-4.17
5.1.4.1.2. Positions-4.15.1
5.1.4.1.3. Thickness and Diameter-4-15.2
5.1.5. What tests/inspections must be done
5.1.5.1. Visual- 4.16.1-Item 1
5.1.5.1.1. Refers to 4.9.1 (Procedure)
5.1.5.2. Destructive Tests Groove Welds-4.16.1 Item 2
5.1.5.2.1. Notic this is default. NOT RT
5.1.5.2.2. See 4.9.3.1 WPS requirements
5.1.5.2.3. Number and Type Required-Table 4.11
5.1.5.2.4. Specimen locations shown in figures for weld joints
5.1.5.2.5. Dimensions for specimens shown in figures
5.1.5.3. Radiography- 4.16.1.1
5.1.5.3.1. Optional Not Required
5.1.5.3.2. Not allowed for GMAW-S
5.1.5.3.3. Prduction RT allowed for OPERATOR ONLY
5.1.6. WPS Required
5.1.6.1. Welder Does not QUALIFY TO a WPS
5.1.6.2. Welder Qualifies Using a WPS
5.1.6.3. A welder may not be qualified to use a production WPS within its full range
5.1.7. What if the test fails
5.1.8. Who signs the "bottom line"
5.2. ASME Sec IX Module (Under Development)
5.2.1. Who can test welders
5.2.1.1. Manufacturer or Contractor ONLY
5.2.2. Who is reponsible for welder qualification
5.2.2.1. Manufacturer Contaractor
5.2.3. What Weld Tests are "required"
5.2.3.1. Depends on Ranges for production
5.2.3.2. Each Process has own table
5.2.3.2.1. Rolling Dirction Optional
5.2.3.2.2. No Specific Test Assempbly Required for Grooves.
5.2.4. What are the qualified ranges
5.2.4.1. Each Table for process refers to a QW-4XX vaeriable in Article 4
5.2.4.1.1. Weld Type-4.17
5.2.4.1.2. Positions-4.15.1
5.2.4.1.3. Thickness and Diameter-4-15.2
5.2.5. What tests/inspections must be done
5.2.5.1. Visual- Very Liberal
5.2.5.2. Destructive Tests or RT
5.2.5.2.1. Notic this is default. NOT RT
5.2.5.2.2. See 4.9.3.1 WPS requirements
5.2.5.2.3. Number and Type Required-Table 4.11
5.2.5.2.4. Specimen locations shown in figures for weld joints
5.2.5.2.5. Dimensions for specimens shown in figures
5.2.5.3. Radiography- 4.16.1.1
5.2.5.3.1. Optional Not Required
5.2.5.3.2. Not allowed for GMAW-S
5.2.5.3.3. Prduction RT allowed for OPERATOR ONLY
5.2.6. What if the test fails
5.2.7. Who signs the "bottom line"