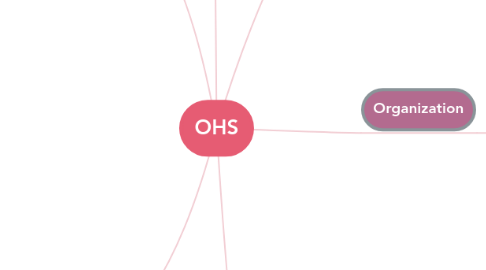
1. Safety
1.1. Concepts
1.1.1. Avoid hazardous conditions and at-risk behaviors.
1.2. Personal Protection
1.2.1. Wear protective coveralls or a mask if doing a job where liquids, fumes or dust that can cause dermatitis.
1.2.2. If chemicals can contaminate the whole body, full body protection is required.
1.2.3. Personal Protective Equipment should be suitable for specific working environment in order to protect from hazards.
2. Health
2.1. Hazard Control
2.1.1. Confinement
2.1.1.1. To avoid contact with hazardous substance s by mechanizing and automating the working procedures.
2.1.2. Isolation
2.1.2.1. To reduce the number of employees contacting the hazardous substances by isolating the working procedures.
2.2. Hazard Identification
2.2.1. Physical
2.2.1.1. Persistent hearing of intense noise without wearing suitable ear protection may lead to deafness.
2.2.1.2. Expose to ionizing radiation such as operating X-ray machines and using radioactive substances may develop acute inflammation of dermatitis or skin ulceration.
2.2.2. Chemical
2.2.2.1. Laboratory accidentally contacts with strong acid and alkali will burn skin.
2.2.3. Biological
2.2.3.1. Health care workers technicians maybe infected with influence, AIDS by contacting patients
2.2.4. Ergonomic
2.2.4.1. Repetitive motion in an inappropriate posture
2.2.4.2. Incorrect posture when operating computers
2.2.5. Psychological
2.2.5.1. Excessive pressure can cause psychological and physical hazard such as heart diseases.
3. Society
3.1. Education
3.1.1. Publishing OHS research for discovery of latest information and evidence.
3.1.2. Establishing the safety culture and mindset at community level.
3.2. Government
3.2.1. Inform, and assist employers and workers in promoting the knowledge of safety and awareness in workplace.
3.2.2. Encourage and support more organization to invest in safety management and systems
3.2.3. Providing the consultancy services to companies on welfare practices
4. Humans
4.1. Human Errors
4.1.1. One of the main causes of occupational accidents is human error. Therefore OHS management is the key strategy to enhance the safety and health of workers in order to reduce incidents and improve productivity.
4.2. Factors leading to Human Failures
4.2.1. Errors
4.2.1.1. Technical Errors
4.2.1.1.1. Slips of action
4.2.1.1.2. Lapses of memory
4.2.1.2. Mistakes
4.2.2. Violations
4.3. Reducing Human Errors
4.3.1. Well Communication
4.3.1.1. Good personal communication skills allow employees to work effectively in groups.
4.3.2. Skilled competent workers
4.3.2.1. Workers could enhance their knowledge, skills and strengthen their safety attitude by practicing training programs.
4.3.3. Establish routines
4.3.3.1. Using standardized instructions or pre-job briefs can help to reduce errors.
5. History of OHS
5.1. 1800's, in United Kingdom
5.1.1. Poor working condition in factories. But it was the major source of income for British.
5.1.2. The HM Factory Inspectorate formed. Resolution the guidance of safety among factories
5.1.3. One of the remarkable labor movement occurred in 1837. Priestly v Fowler. Which introduced the responsibility of employer in to the common law.
5.1.4. The Royal Commission founded to monitor industrial accidents and harsh working conditions in the mining industry.
5.2. Early 1900's
5.2.1. In America, National Labor Relations Act published during WWII. National Labor Relations Act published during WWII. Regulated labour's right and avoids law dissension.
5.2.2. The famous tort OHS law case Wilsons and Clyde Coal Ltd v English arose. Introduced the duty of employers to ensure a safe working environment.
5.2.3. Australia started to introduce and established OHS laws to workers and factories, for example Workers''Compensation Commission.
5.3. 1970's-1990's, in Hong Kong
5.3.1. As the British had developed their colony in Hong Kong, the economy and manufacturing industry started to boom.
5.3.2. To promote industrial safety, the Occupational Safety and Health Council established.
5.3.3. The Council improved the safety and health standard and awareness through launching research and dissemination information to the community.
6. Organization
6.1. Employer
6.1.1. Provides OHS training and information to enhance staff's safety awareness.
6.1.2. Balance interests and risks when making decisions.
6.1.3. Provides safety and healthy working environment.
6.1.4. Regulate the maximum number of working hours.
6.2. Employee
6.2.1. Ensure protective clothing is cleaned and inspected regularly.
6.2.2. Keep your workplace clean, including machinery and tools.
6.2.3. Wash gloves immediately after use. Otherwise, the contaminant may gradually degrade or permeate the gloves.