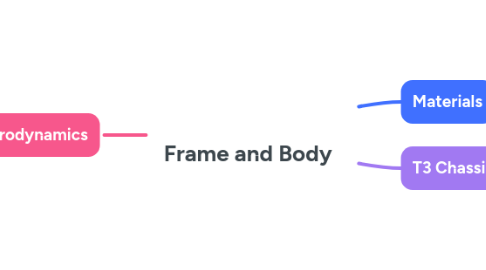
1. **Aerodynamics**
1.1. T 8.2 Restrictions
1.1.1. T 8.2.4 All restrictions must be fulfilled with the wheels pointing straight and with any suspension setup with or without a driver seated in the vehicle.
1.1.1.1. Width Restrictions
1.1.1.1.1. T 8.2.2 All aerodynamic devices lower than 500 mm from the ground and further rearward than the front axle, must not b wider than a vertical plane touching the mos outboard point of the front and rea wheel/tire. All aerodynamic devices higher than 500 mm from the ground, must not extend outboard of the most inboar point of the rear wheel/tire.
1.1.1.2. Height Restrictions
1.1.1.2.1. T8.2.1 All aerodynamic devices forward of a vertical plane through the rearmost portion of the front face of the driver head restraint support, excluding any padding, set to its most rearward position, must be lower than 500 mm from the ground. All aerodynamic devices in front of the front axle and extending further outboard than the most inboard point of the front tire/wheel must be lower than 250 mm from the ground. All aerodynamic devices in front of the front axle and extending further outboard than the most inboard point of the front tire/wheel must be lower than 250 mm from the ground.
1.1.1.3. Length Restrictions
1.1.1.3.1. T 8.2.3 All aerodynamic devices must not extend further rearward than 250 mm from the rearmost part of the rear tires. All aerodynamic devices must not extend further forward than 700 mm from the fronts of the front tires.
1.2. T 8.3 Minimum Edge Radii of Aerodynamic Devices
1.2.1. T 8.3.1 All forward facing edges of aerodynamic devices that could contact a pedestrian must have a minimum radius of 5 mm for all horizontal edges and 3 mm for vertical edges.
1.3. T 8.4 Aerodynamic Devices Stability and Strength.
1.3.1. T 8.4.1 Any aerodynamic device must be able to withstand a force of 200 distributed over a minimum surface of 225 cm2 and not deflect more than 10 mm in the load carrying direction.
1.3.2. T 8.4.2 Any aerodynamic device must be able to withstand a force of 50 N applied in any direction at any point and not deflect more than 25 mm.
1.4. T 2.2 Ground Clearance
1.4.1. T 2.2.1 The minimum static ground clearance of any portion of the vehicle, other than the tires, including a driver, must be 30 mm.
1.4.2. T 2.2.2 Sliding skirts or other aerodynamic devices that by design, fabrication or as a consequence of moving, contact the track surface are prohibited.
1.5. T 2.3 Bodywork
1.5.1. T 2.3.1 There must be no openings through the bodywork into the cockpit other than that required for the cockpit opening. Minimal openings around the front suspension and steering system components are allowed.
1.5.2. T 2.3.2 Enclosed chassis structures and structures between the chassis and the ground must have two venting holes of at least 25 mm diameter in the lowest part of the structure to prevent accumulation of liquids. Additional holes are required when multiple local lowest parts exist in the structure.
1.5.3. T 2.3.3 All edges of the bodywork that could come into contact with a pedestrian must have a minimum radius of 1 mm.
1.5.4. T 2.3.4 The bodywork in front of the front wheels must have a radius of at least 38 mm extending at least 45° relative to the forward direction, along the top, sides and bottom of all affected edges.
2. **Materials**
2.1. T3.2 WELDED MATERIALS.
2.1.1. T3.2.6 If a member of the primary structure (except for the roll hoops) is a bent tube or made from multiple tubes an additional tube must support it. This support tube must: • Have its attachment point at the position along the bend tube where it deviates farthest from a straight line connecting both ends. • Be of the same dimension as the supported tube(s). • Terminate at a node of the primary structure. • Be angled no more than 30° from the plane of the supported tube(s).
2.1.2. T3.2.7 Any welded seams shape must not be mechanically altered in any way.
2.1.3. T3.3.
2.1.3.1. T3.3.1 Alternative materials may be used for all parts of the primary structure and the TSAC with the following exceptions: • The main hoop and the main hoop bracing must be steel • The front hoop must be metal• Any welded structures of the primary structure must be steel • However, the front hoop may be an aluminum welded structure
2.1.4. T3.2.1 Table 4 shows the minimum requirements for the members of the primary structure if made from steel tubing.
2.2. T3.3 ALTERNATIVE MATERIALS.
2.2.1. T3.3.2 If any other materials than steel tubing are used in the primary structure or the TSAC, physical testing is required to show equivalency to the minimum material properties for steel in T 3.2.
2.3. T3.4 COMPOSITE STRUCTURES
2.3.1. T3.4.2 If composite materials are used in the primary structure or the TSAC the SES must include: • Material type(s) • Cloth weights • Resin type • Fiber orientation • Number of layers • Core material • Lay-up technique • 3-point-bend test and shear test data
2.3.2. T3.4.3 For any laminate in the primary structure or the TSAC, the maximum weight content of parallel fibers, relative to the weight of all fibers in the laminate, is 50 %. All fibers laid within any orientation +/-10° count as parallel in this case.
2.3.3. T3.4.4. Wherever backing plates are required, they must be fully supported by the structure they are attached to.
2.3.4. T3.4.5 Backing plates must have a continuous perimeter that is near circular or near oval. The outer perimeter profile may have some straight sections, but no concave sections. Backing plates must not have any cut-outs within their outside perimeter except for the holes for bolts.
2.4. T4 COCKPIT
2.4.1. T 4.1.2 If the side impact structure is not made of tubes, the template must pass until it is 320 mm above the lowest inside chassis point between the front and main hoop.
2.5. T3.13 FRONT BULKHEAD
2.5.1. T 3.13.2 If the front bulkhead is part of a composite structure and is modeled as an “L” shape, the EI of the front bulkhead about the vertical and lateral axes must be equivalent to a steel tube meeting the requirements for the front bulkhead. The length of the section perpendicular to the bulkhead may be a maximum of 25 mm measured from the rearmost face of the bulkhead.
2.6. T3.14 FRONT BULKHEAD SUPPORT.
2.6.1. T 3.14.2 If the front bulkhead support is part of a composite structure, it must have equivalent EI to the sum of the EI of the six baseline steel tubes that it replaces and it must not be counted towards the composite front hoop bracing structures for the structural equivalency documentation (i.e. T 3.11.4).
2.6.2. T 3.14.3 The EI of the vertical side of the front bulkhead support structure must be equivalent to at least the EI of one baseline steel tube that it replaces.
2.7. T3.16 BOLTED PRIMARY STRUCTURE.
2.7.1. T 3.16.5 When using bolted joints within the primary structure, no crushing of the laminate core material is permitted
2.8. T3.17 IMPACT ATTENUATOR
2.8.1. T 3.17.7 The attachment of the IA assembly to a monocoque structure requires an approved “Structural Equivalency Spreadsheet” per T 3.6 that shows equivalency to a minimum of eight 8 mm metric grade 8.8 bolts.
2.9. T3.7 ROLL HOOPS
2.9.1. T 3.7.4 Roll hoops attached to a composite primary structure must be mechanically attached at the top and bottom of both sides of that structure and at intermediate locations if needed to show equivalency. The lower roll hoop tubing attachment points must be within 50 m of the endpoints of the roll hoop.
2.10. T3.15 SIS
2.10.1. T 3.15.2 If the side impact structure is part of a composite structure, the following is required:
2.10.1.1. • The region that is longitudinally forward of the main hoop and aft of the front hoop and vertical from the bottom surface of the chassis to 320 mm above the lowest inside chassis point between the front and main hoop must have an EI equal to the three baseline steel tubes that it replaces, see figure 9.
2.10.1.2. • The vertical side impact structure must have an EI equivalent to two baseline steel tubes and half the horizontal floor must have an EI equivalent to one baseline steel tube.
2.10.1.3. • The vertical side impact structure must have an absorbed energy equivalent to two baseline steel tubes.
2.10.1.4. • The perimeter shear strength must be at least 7.5 kN
2.11. T3.9 FRONT HOOP
2.11.1. T 3.9.5 Fully laminating the front hoop to the monocoque is acceptable. Fully laminating means that the hoop has to be encapsulated with laminate around its whole circumference, see figure 4. Equivalence to at least four mounts compliant with T 3.16.1 must be shown in the SES. The laminate encapsulating the front hoop must overlap by at least 25mm on each side. It must have the same lay-up as the laminate that it is connecting to.
2.12. T3.9 FRONT HOOP BRACING
2.12.1. T 3.11.4 Composite front hoop bracing structures cannot be counted towards the front bulkhead support structures and vice-versa for the structural equivalency documentation.
3. **T3 Chassis**
3.1. T 3.1.1 Among other requirements, the vehicle’s structure must include: •Two roll hoops that are braced • A front bulkhead with support system and IA • Side impact structures
3.1.1. Cockpit
3.1.1.1. T 4.1 Cockpit Opening
3.1.1.1.1. T 4.1.1 The size of the cockpit opening needs to be sufficient for the template shown on the left of figure 11 to pass vertically from the cockpit opening to below the upper side impact member when held horizontally. The template may be moved fore and aft.
3.1.1.1.2. T 4.1.3 The steering wheel, seat and all padding may be removed for the template to fit. Any other parts may only be removed if they are integrated with the steering wheel.
3.1.1.2. T 4.2 Cockpit Internal Cross Section
3.1.1.2.1. T 4.2.1 The cockpit must provide a free internal cross section sufficient for the template shown on the right in figure 11 to pass from the cockpit opening to a point 100 mm rearwards of the face of the rearmost pedal in an inoperative position. The template may be moved up and down. Adjustable pedals must be in their most forward position.
3.1.1.2.2. T 4.2.2 The steering wheel and any padding that can be removed without the use of tools while the driver is seated may be removed for the template to fit.
3.1.1.2.3. T 4.2.3 The driver’s feet and legs must be completely contained within the primary structure when the driver is seated normally and the driver’s feet are touching the pedals. In side and front views, any part of the driver’s feet or legs must not extend above or outside of this structure
3.1.1.3. T 4.3 Percy (95th percentile male)
3.1.1.3.1. T 4.3.1 When seated normally and restrained by the driver’s restraint system, the helmet of a 95th percentile male and all of the team’s drivers must, see figure 12:
3.1.1.3.2. T 4.3.2 The 95th percentile male is represented by a two dimensional figure consisting of two circles of 200 mm diameter (one representing the hips and buttocks and one representing the shoulder region) and one circle of 300 mm (representing the head with helmet).
3.1.1.3.3. T 4.3.3 The two 200 mm circles are connected by a straight line measuring 490 mm. The 300 mm circle is connected by a straight line measuring 280 mm with the upper 200 mm circle.
3.1.1.3.4. T 4.3.4 The figure has to be positioned in the vehicle as follows, see figure 13:
3.1.1.4. T 4.4 Side Tubes
3.1.1.4.1. T 4.4.1 If there is any chassis member alongside the driver at the height of the neck of any of the drivers in the team, a metal tube or piece of sheet metal must be attached to the chassis to prevent the driver’s shoulders from passing under that chassis member.
3.1.1.5. T 4.5 Non-Welded Driver’s Harness Attachment
3.1.1.5.1. T 4.5.1 Any harness attachment to a monocoque must be using one 10 mm metric grade 8.8 bolt or two 8 mm metric grade 8.8 bolts (or bolts of an equivalent norm) and steel backing plates with a minimum thickness of 2 mm.
3.1.1.5.2. T 4.5.2 If the attachment of the drivers harness is not welded to a steel structure, it must be proven that the attachments for shoulder and lap belts can support a load of 13 kN and the attachment points of the anti-submarine belts can support a load of 6.5 kN.
3.1.1.5.3. T 4.5.3 If the lap belts and anti-submarine belts are attached less than 100 mm apart, these must support a total load of 19.5 kN.
3.1.1.5.4. T 4.5.4 The strength of lap belt and shoulder belt attachments must be proven by physical testing where the required load is applied to a representative attachment point with the lay-up
3.1.1.6. T 4.6 Driver’s Seat
3.1.1.6.1. T 4.6.1 The lowest point of the driver’s seat must in side view not extend below the upper face of the lowest side impact structure member or have a longitudinal tube (or tubes) that meets the material requirements for the side impact structure (T 3.2), passing underneath the lowest point of the seat.
3.1.1.6.2. T 4.6.2 Adequate heat insulation must be provided to ensure that the driver is not able to contact any parts of the vehicle with a surface temperature above 60 °C. The insulation may be external to the cockpit or incorporated with the driver’s seat or firewall. The design must address all three types of heat transfer with the following minimum requirements between the heat source and the part that the driver could contact:
3.1.1.7. T 4.7 Floor Closeout
3.1.1.7.1. T 4.7.1 All vehicles must have a floor closeout made of one or more panels, which separate the driver from the ground.
3.1.1.7.2. T 4.7.2 The closeout must extend from the front bulkhead to the firewall
3.1.1.7.3. T 4.7.3 The panels must be made of a solid, non-brittle material.
3.1.1.7.4. T 4.7.4 If multiple panels are used, gaps between panels may not exceed 3 mm.
3.1.1.8. T 4.8 Firewall
3.1.1.8.1. T 4.8.1 A firewall must separate the cockpit from all components of the fuel supply system, hydraulic fluid (except brake system and dampers), flammable liquids, the low voltage battery and any TS component, see EV 1.1.1.
3.1.1.8.2. T 4.8.2 The firewall must cover any line of sight between the parts mentioned in T 4.8.1 and any part of the tallest driver below a plane 100 mm above the bottom of the helmet.
3.1.1.8.3. T 4.8.3 The firewall must be a non-permeable surface made from a rigid, fire resistant material, see T 1.2.1, which must be rigidly mounted to the vehicle’s structure.
3.1.1.8.4. T 4.8.4 Any firewall must seal completely against the passage of fluids, especially at the sides and the floor of the cockpit.
3.1.1.8.5. T 4.8.5 Pass-throughs for wiring, cables, etc. are permitted if grommets are used to seal the pass- through.
3.1.1.8.6. T 4.8.6 Multiple panels may be used to form the firewall but must overlap at least 5mm and be sealed at the joints. Any sealing material must not be vital to the structural integrity of the firewall.
3.1.1.8.7. T 4.8.7 [EV ONLY] The tractive system firewall between driver and tractive system components must be composed of two layers:
3.1.1.8.8. T 4.8.8 [EV ONLY] Conductive parts (except for the chassis) may not protrude through the firewall or must be properly insulated on the driver’s side.
3.1.1.8.9. T 4.8.9 [EV ONLY] TS parts outside of the envelope, see EV 4.4.3, do not need a firewall.
3.1.1.9. T 4.9 Accessibility of Controls
3.1.1.9.1. T 4.9.1 All vehicle controls must be operated from inside the cockpit without any part of the driver, e.g. hands, arms or elbows, being outside the vertical planes tangent to the outermost surface of the side impact structure.
3.1.1.10. T 4.10 Driver Visibility
3.1.1.10.1. T4.10.1 The driver must have adequate visibility to the front and sides of the vehicle. Seated in a normal driving position, the driver must have a minimum field of vision of 100° to either side. The required visibility may be obtained by the driver turning their head and/or the use of mirrors.
3.1.1.10.2. T4.10.2 If mirrors are required to meet T 4.10.1, they must remain in place and be adjusted to enable the required visibility throughout all dynamic events.
3.1.1.11. T 4.11 Driver Egress
3.1.1.11.1. T4.11.1 All drivers must be able to exit to the side of the vehicle in less than 5 s with the driver in the fully seated position, hands in the driving position on the connected steering wheel (in all possible steering positions) and wearing the required driver equipment as in T 13.3. The egress time will stop when the driver has both feet on the ground.
3.1.2. I.A.
3.1.2.1. T 3.17.1 Each vehicle must be equipped with an IA.
3.1.2.2. T 3.17.2 The IA must be:
3.1.2.2.1. • Installed forward of the front bulkhead
3.1.2.2.2. • At least 100 mm high and 200 mm wide for a minimum distance of 200 mm forward of the front bulkhead.
3.1.2.2.3. • Not able to penetrate the front bulkhead in the event of an impact.
3.1.2.2.4. • Attached securely and directly to the Anti Intrusion Plate (AIP).
3.1.2.2.5. • Not part of the non-structural bodywork.
3.1.2.2.6. • Designed with a closed front section.
3.1.2.2.7. • Cannot be wider or higher than the AIP.
3.1.2.3. T 3.17.3 On all vehicles, a 1.5 mm solid steel or 4.0 mm solid aluminum AIP must be integrated into the IA.
3.1.2.3.1. • If the IA and AIP (IA assembly) are bolted to the front bulkhead, it must be the same size as the outside dimensions of the front bulkhead.
3.1.2.3.2. • If it is welded to the front bulkhead, it must extend at least to the centerline of the front bulkhead tubing in all directions.
3.1.2.3.3. • The AIP must not extend past the outside edges of the front bulkhead.
3.1.2.4. T 3.17.4 Alternative AIP designs are permissible if equivalency to T 3.17.3 is proven by physical testing as in T 3.19.2.
3.1.2.5. T 3.17.5 If the IA assembly is not integral with the primary structure, i.e. welded, a minimum of eight 8 mm metric grade 8.8 bolts must attach the IA assembly to the front bulkhead. The IA may be attached to the AIP by a minimum of four 8 mm metric grade 8.8 bolts. The bolts are considered critical fasteners and must comply with T 10.
3.1.2.6. T 3.17.6 The attachment of the IA assembly must be designed to provide an adequate load path for transverse and vertical loads in the event of off-center and off-axis impacts. Segmented foam attenuators must have the segments bonded together to prevent sliding or parallelogramming
3.1.2.7. T 3.17.8 A team may use one of the “standard” FSAE IAs, in order to avoid testing, provided that:
3.1.2.7.1. • if the front bulkhead width is larger than 400 mm and/or its height is larger than 350 mm a diagonal or X-bracing that is a front bulkhead support tube or an approved equivalent per T 3.2, must be included in the front bulkhead. Or equivalent for monocoque bulkheads
3.1.2.7.2. • must use a 1.5 mm solid steel AIP that is welded along its full perimeter to a steel bulkhead or use a 4 mm solid aluminium AIP that is bolted to any bulkhead with a minimum of eight 8 mm metric grade 8.8 bolts
3.1.2.7.3. • if the “standard” honeycomb IA is used, the IA must be of pre-crushed type
3.1.2.8. T 3.17.9 If the standard IA is used, but does not comply with the requirements of T 3.17.8 physical testing must be carried out to prove that the AIP does not permanently deflect more than 25 mm.
3.1.2.9. T 3.18.1 All teams must submit an IA data report using the Impact Attenuator Data (IAD) template provided at the competition website.
3.1.2.10. T 3.19 Impact Attenuator Test Requirements:
3.1.2.10.1. T 3.19.1 The IA assembly, when mounted on the front of a vehicle with a total mass of 300 kg and impacting a solid, non-yielding impact barrier with a velocity of impact of 7 m/s, must meet the following requirements:
3.1.2.10.2. T 3.19.2 During the IA test:
3.1.2.10.3. T 3.19.3 Teams using IAs (typically structural noses) directly attached to the front bulkhead, which shortcut the load path through the bulk of the AIP, must conduct an additional test. This test must prove that the AIP can withstand a load of 120 kN (300 kg multiplied by 40 g), where the load applicator matches the minimum IA dimensions.
3.1.2.10.4. T 3.19.4 Vehicles with aerodynamic devices and/or sensors in front of the front bulkhead must not exceed the peak deceleration of T 3.19.1 for the combination of their IA assembly and the non-crushable object(s). Any of the following three methods may be used to prove the design does not exceed 120 kN :
3.1.3. Primary structure
3.1.3.1. Front Bulkhead
3.1.3.1.1. T 3.13.1 Any alternative material used for the front bulkhead must have a perimeter shear strength equivalent to a 1.5 mm thick steel plate.
3.1.3.1.2. T 3.14.3 The EI of the vertical side of the front bulkhead support structure must be equivalent to at least the EI of one baseline steel tube that it replaces.
3.1.3.1.3. T 3.14.4 The perimeter shear strength of the monocoque laminate in the front bulkhead support structure must be at least 4 kN.
3.1.3.2. Front Bulckhead support
3.1.3.2.1. T 3.14.1 The front bulkhead must be supported back to the front hoop by a minimum of three tubes on each side; an upper member, a lower member and diagonal bracing to provide triangulation
3.1.3.2.2. T 3.14.4 The perimeter shear strength of the monocoque laminate in the front bulkhead support structure must be at least 4 kN.
3.1.3.3. Main Hoop
3.1.3.3.1. Main Hoop Bracing
3.1.3.3.2. T 3.8.1 The main hoop must be constructed of a single piece of uncut, continuous, closed section steel tubing.
3.1.3.3.3. T 3.8.2 In side view the portion of the main hoop which is above its upper attachment point to the side impact structure must be inclined less than 10° from vertical.
3.1.3.3.4. T 3.8.3 In side view any bends in the main hoop above its upper attachment point to the primary structure must be braced to a node of the main hoop bracing support structure with tubing meeting the requirements of main hoop bracing.
3.1.3.3.5. T 3.8.4 In side view any portion lower than the upper attachment point to the side impact structure must be inclined either forward or not more than 10° rearward.
3.1.3.4. Front Hoop
3.1.3.4.1. Front Hoop Bracing
3.1.3.4.2. T 3.9.1 The front hoop must be constructed of a continuous and closed section.
3.1.3.4.3. T 3.9.2 If the front hoop is made from more than one piece it must be supported by node-to-node triangulation or an equivalent construction.
3.1.3.4.4. T 3.9.3 In side view, no part of the front hoop can be inclined more than 20° from vertical.
3.1.3.4.5. T 3.9.4 If the front hoop is a welded construction made from multiple aluminum profiles, the equivalent yield strength must be considered in the as-welded condition unless the team demonstrates and shows proof that it has been properly solution heat treated and artificially aged. The team must supply sufficient documentation proving the appropriate heat treatment process was performed.
3.1.3.5. SIS
3.1.3.5.1. T 3.15.1 The side impact structure must consist of at least three steel tubes, see T 3.2, on each side of the cockpit, see figure 8.
3.1.3.6. Roll Hoop
3.1.3.6.1. Roll Hoop Bracing
3.1.3.6.2. T 3.7.1 Both roll hoops must be securely integrated to the primary structure using node-to-node triangulation or equivalent joining methods
3.1.3.6.3. T 3.7.2 The minimum radius of any bend, measured at the tube centerline, must be at least three times the tube outside diameter. Bends must be smooth and continuous with no evidence of crimping or wall failure. The minimum area moment of inertia, see T 3.2, must be maintained in all areas, including the bends of the manufactured tubes.
3.1.3.6.4. T 3.7.3 In a plane perpendicular to the longitudinal axis of the vehicle and through the lower endpoints of the roll hoop, no part of the primary structure may lie below 30 mm of the endpoints of the roll hoop.
3.1.3.6.5. T 3.7.5 Mounting plates welded to the roll hoops must be at least 2 mm thick steel or 3 mm thick aluminum, dependent of the roll hoop material.
3.1.3.6.6. T 3.7.6 Both roll hoops must have one 4.5 mm inspection hole in a non-critical straight location and its surface at this point must be unobstructed for at least 180°.
3.1.4. Bolted primary structure atattchments
3.1.4.1. T 3.16.1 If two parts of the primary structure are bolted together, each attachment point between the two parts must be able to carry a load of 30 kN in any direction.
3.1.4.2. T 3.16.2 Data obtained from the laminate perimeter shear strength test must be used to prove that adequate shear area is provided.
3.1.4.3. T 3.16.3 Each attachment point requires a minimum of two 8 mm metric grade 8.8 bolts and steel backing plates with a minimum thickness of 2 mm.
3.1.4.4. T 3.16.4 For the attachment of front hoop bracing, main hoop bracing and main hoop bracing support to the primary structure the use of one 10 mm metric grade 8.8 bolt is sufficient, if the bolt is on the centerline of the tube, see figure 10.
3.1.5. T3.6 SES
3.1.5.1. T 3.6.1 All teams must submit a Structural Equivalency Spreadsheet (SES) and Structural Equivalency 3D Model (SE3D).
3.1.5.2. T 3.6.2 The SES spreadsheet form can be downloaded from the competition website.
3.1.5.3. T 3.6.3 The SE3D must contain a three dimensional CAD model of the chassis including all members of the primary structure and all mechanical attachment details of the hoops and hoop braces in “IGES” file format not larger than 40 MB. [EV ONLY] The TSAC(s) and attachment must also be included
3.1.5.4. T 3.6.4 Vehicles must be fabricated in accordance with the materials and processes described in the SES.
3.1.5.5. T 3.6.5 Teams must bring a copy of the approved SES to technical inspection.
3.1.5.6. T3.4.1 If composite structures are used in the primary structure or the TSAC, the Flexural Rigidity (EI) of that structure must be calculated with the tools and formulas in the SES. The actual geometry and curvature of the panel may be taken into account for the main hoop bracing support, the front hoop bracing, the front bulkhead support structure, the shoulder harness bar, the TS and TSAC protective structure. For all other areas the EI must be calculated as the EI of a flat panel about its neutral axis. This panel must have the same composition as the structure used in the primary structure or the TSAC.
3.1.6. COCKPIT
3.1.6.1. T4.1 OPENING
3.1.6.1.1. T 4.1.1 The size of the cockpit opening needs to be sufficient for the template shown on the left of figure 11 to pass vertically from the cockpit opening to below the upper side impact member when held horizontally. The template may be moved fore and aft.
3.1.6.1.2. T 4.1.2 If the side impact structure is not made of tubes, the template must pass until it is 320 mm above the lowest inside chassis point between the front and main hoop.
3.1.6.1.3. T 4.1.3 The steering wheel, seat and all padding may be removed for the template to fit. Any other parts may only be removed if they are integrated with the steering wheel.
3.1.6.2. T4.2 INTERNAL CROSS SECTION
3.1.6.2.1. T 4.2.1 The cockpit must provide a free internal cross section sufficient for the template shown on the right in figure 11 to pass from the cockpit opening to a point 100 mm rearwards of the face of the rearmost pedal in an inoperative position. The template may be moved up and down. Adjustable pedals must b in their most forward position.
3.1.6.2.2. T 4.2.2 The steering wheel and any padding that can be removed without the use of tools while the driver is seated may be removed for the template to fit.
3.1.6.2.3. T 4.2.3 The driver’s feet and legs must be completely contained within the primary structure when the driver is seated normally and the driver’s feet are touching the pedals. In side and front views, any part of the driver’s feet or legs must not extend above or outside of this structure.
3.1.6.3. T4.3 PERCY
3.1.6.3.1. T 4.3.1 When seated normally and restrained by the driver’s restraint system, the helmet of a 95th percentile male and all of the team’s drivers must, see figure 12:
3.1.6.3.2. T 4.3.2 The 95th percentile male is represented by a two dimensional figure consisting of two circles of 200 mm diameter (one representing the hips and buttocks and one representing the shoulder region) and one circle of 300 mm (representing the head with helmet).
3.1.6.3.3. T 4.3.3 The two 200 mm circles are connected by a straight line measuring 490 mm. The 300 mm circle is connected by a straight line measuring 280 mm with the upper 200 mm circle.
3.1.6.3.4. T 4.3.4 The figure has to be positioned in the vehicle as follows, see figure 13: • The seat adjusted to the rearmost position • The pedals adjusted to the frontmost position • The bottom 200 mm circle placed on the seat bottom. The distance between the center of the circle and the rearmost actuation face of the pedals must be minimum 915 mm. • The middle circle positioned on the seat back • The upper 300 mm circle positioned 25 mm away from the head restraint
3.1.6.4. T4.4 SLIDE TUBES
3.1.6.4.1. T 4.4.1 If there is any chassis member alongside the driver at the height of the neck of any of the drivers in the team, a metal tube or piece of sheet metal must be attached to the chassis to prevent the driver’s shoulders from passing under that chassis member.
3.1.6.5. T4.5 NON WELDED DRIVER'S HARNESS ATTACHMENT
3.1.6.5.1. T 4.5.1 Any harness attachment to a monocoque must be using one 10 mm metric grade 8.8 bolt or two 8 mm metric grade 8.8 bolts (or bolts of an equivalent norm) and steel backing plates with a minimum thickness of 2 mm.
3.1.6.5.2. T 4.5.2 If the attachment of the drivers harness is not welded to a steel structure, it must be proven that the attachments for shoulder and lap belts can support a load of 13 kN and the attachment points of the anti-submarine belts can support a load of 6.5 kN.
3.1.6.5.3. T 4.5.3 If the lap belts and anti-submarine belts are attached less than 100 mm apart, these must support a total load of 19.5 kN.
3.1.6.5.4. T 4.5.4 The strength of lap belt and shoulder belt attachments must be proven by physical testing where the required load is applied to a representative attachment point with the lay-up and attachment brackets as in the chassis. The following requirements must be met: • Edges of the test fixture supporting the sample must be a minimum of 125 mm from the load application point. • The width of the shoulder harness test sample must not be any wider than the shoulder harness panel height used to show equivalency for the shoulder harness mounting bar. • Designs with attachments near a free edge may not support the free edge during the test. • Harness loads must be tested with the worst case for the range of the angles specified for the driver’s harness.
3.1.6.6. T4.6 DRIVER'S SEAT
3.1.6.6.1. T 4.6.1 The lowest point of the driver’s seat must in side view not extend below the upper face of the lowest side impact structure member or have a longitudinal tube (or tubes) that meets the material requirements for the side impact structure (T 3.2), passing underneath the lowest point of the seat.
3.1.6.6.2. T 4.6.2 Adequate heat insulation must be provided to ensure that the driver is not able to contact any parts of the vehicle with a surface temperature above 60 °C. The insulation may be external to the cockpit or incorporated with the driver’s seat or firewall. The design must address all three types of heat transfer with the following minimum requirements between the heat source and the part that the driver could contact:
3.1.6.6.3. T 4.2.2 The steering wheel and any padding that can be removed without the use of tools while the driver is seated may be removed for the template to fit.
3.1.6.7. T4.7 FLOOR CLOSEOUT
3.1.6.7.1. T 4.7.1 All vehicles must have a floor closeout made of one or more panels, which separate the driver from the ground.
3.1.6.7.2. T 4.7.2 The closeout must extend from the front bulkhead to the firewall
3.1.6.7.3. T 4.7.3 The panels must be made of a solid, non-brittle material.
3.1.6.7.4. T 4.7.4 If multiple panels are used, gaps between panels may not exceed 3 mm
3.1.6.8. T4.8 FIREWALL
3.1.6.8.1. T 4.8.1 A firewall must separate the cockpit from all components of the fuel supply system, hydraulic fluid (except brake system and dampers), flammable liquids, the low voltage battery and any TS component, see EV 1.1.1.
3.1.6.8.2. T 4.8.2 The firewall must cover any line of sight between the parts mentioned in T 4.8.1 and any part of the tallest driver below a plane 100 mm above the bottom of the helmet.
3.1.6.8.3. T 4.8.3 The firewall must be a non-permeable surface made from a rigid, fire resistant material, see T 1.2.1, which must be rigidly mounted to the vehicle’s structure.
3.1.6.8.4. T 4.8.4 Any firewall must seal completely against the passage of fluids, especially at the sides andthe floor of the cockpit.
3.1.6.8.5. T 4.8.5 Pass-throughs for wiring, cables, etc. are permitted if grommets are used to seal the passthrough.
3.1.6.8.6. T 4.8.6 Multiple panels may be used to form the firewall but must overlap at least 5mm and be sealedat the joints. Any sealing material must not be vital to the structural integrity of the firewall.
3.1.6.8.7. T 4.8.7 [EV ONLY] The tractive system firewall between driver and tractive system componentsmust be composed of two layers:
3.1.6.8.8. T 4.8.8 [EV ONLY] Conductive parts (except for the chassis) may not protrude through the firewallor must be properly insulated on the driver’s side. or must be properly insulated on the driver’s side.
3.1.6.8.9. T 4.8.9 [EV ONLY] TS parts outside of the envelope, see EV 4.4.3, do not need a firewall.
3.1.6.9. T4.9 ACCESSIILITY OF CONTROLS
3.1.6.9.1. T 4.9.1 All vehicle controls must be operated from inside the cockpit without any part of the driver, e.g. hands, arms or elbows, being outside the vertical planes tangent to the outermost surface of the side impact structure.
3.1.6.10. T4.10 DRIVER VISIBILITY
3.1.6.10.1. T 4.10.1 The driver must have adequate visibility to the front and sides of the vehicle. Seated in a normal driving position, the driver must have a minimum field of vision of 100° to either side. The required visibility may be obtained by the driver turning their head and/or the use of mirrors. T 4.10.2 If mirrors are required to meet T 4.10.1, they must remain in place and be adjusted to enable the required visibility throughout all dynamic events.
3.1.6.11. T4.11 DRIVER EGRESS
3.1.6.11.1. T 4.11.1 All drivers must be able to exit to the side of the vehicle in less than 5 s with the driver in the fully seated position, hands in the driving position on the connected steering wheel (in all possible steering positions) and wearing the required driver equipment as in T 13.3. The egress time will stop when the driver has both feet on the ground.