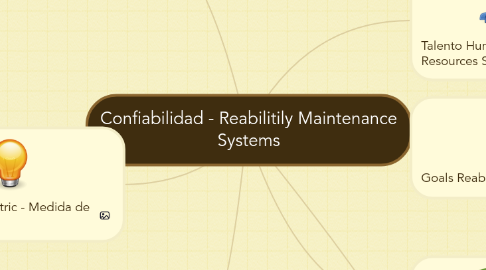
1. Time Cycle Scale Calculated
1.1. Calculated Cycle Indicators
1.1.1. One Day = 24 hr/year
1.1.2. Week = 168 hr/year
1.1.3. 4 week = 672 hr/year
1.2. Priority Importance EPT - SPT
1.2.1. 8760 Operations Hours / 365 Days of Year
1.2.2. One Day = 24 Hr/Operations
1.2.3. One Week = 168 Hr/Operations
1.2.4. One Moon = 720 Hr/Operations
1.2.5. Example Trimestre = 2.160 Hr/Operations
1.3. Planing Operations
1.3.1. Target and Benchmarking. Plianing by Scale * Time Scheduled Cycle Operations Between Total Operations Calendar
2. Performance Metric - Medida de Rendimiento
2.1. Key Performance Indicator
2.1.1. Scheduled Hours = Conditions Programming Scheduled Hours Operations
2.1.2. shutdown = Mean Time Between Shutdowns = Total Operations Hours (+ Hours by Productions) between Total Shutdowns by Cycle
3. Other Performance Calculated - Scheduled Maintenance = Scheduled Hours between Total Maintenance Shutdown Hours ( assimilate shutdown and scheduled hours)
4. Other Performance Calculated - Failure Maintenance = Human Hours Maintenance and Mean Time To Repair between shutdown by Cycle ( Example 8760 Operations Hours, 720 Month Hours, 168 Week Hours / 365 Days of Year / )
5. Talento Humano - Human Resources Specialitily
5.1. EERM - Expert Executive Reabilitily Maintenance
5.2. EGQM - Expert Group Quality Maintenance
5.3. ESOPM - Expert Support Operations Process Maintenance
6. Goals Reabilitily Maintenance Systems
6.1. highest Availiability = Mean Time Between Shutdowns / Mean Time Between Shutdowns + Mean Time To Repair (Example Mechanical, Electrical, Lubrications and Instrumentations)
6.2. Maintainability = Reference Applications by highest only changes Mean Time to Repair (Example Mechanical, Electrical, Lubrications and Instrumentations)
6.3. Asset Utilization = Operations Hours between Total Calendar Hours
7. Conditions by Cycle
7.1. Status Electrical Maintenance
7.2. Status Mechanical Maintenance
7.2.1. Physical Availiability = Operations Hours + Stand-by Hours between Operations Hours + Stand-by Hours + Hours shutdown
7.2.2. Availiability Mechanical = Operations Hours + Stand-by Hours between Operations Hours + Stand-by Hours + Hours imperfections mechanical
7.3. Status Lubrications Maintenance
7.4. Status Instrumentations Maintenance
7.4.1. Availiability Mechanical = Operations Hours + Stand-by Hours between Operations Hours + Stand-by Hours + Hours imperfections Instrumentations