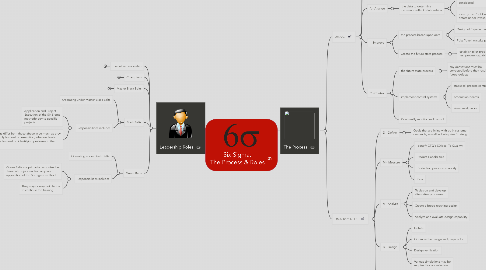
1. Leadership Roles
1.1. Executive Leadership
1.1.1. C level executives
1.1.2. Responsibilities include:
1.1.2.1. Establishing a clear vision under Six Sigma practices
1.1.2.2. Providing other Six Sigma members with support and tools to innovate
1.2. Champions
1.2.1. Upper level management
1.2.2. Responsibilities include:
1.2.2.1. Practical implementation of the Six Sigma goal (as set by Executive Leadership) across the business
1.2.2.2. Acting as mentors to Black Belt Six Sigma members
1.3. Master Black Belts
1.3.1. Management
1.3.1.1. Tapped by Champions
1.3.2. Responsibilities include:
1.3.2.1. Assistance to Champions
1.3.2.2. Guiding and mentoring Black and Green belt members
1.3.2.3. Statistical tasks ensuring Quality
1.3.2.4. Ensuring practical application of the Six Sigma method across different functions and departments
1.4. Black Belts
1.4.1. Operating under Master Black Belts
1.4.2. Responsibilities include:
1.4.2.1. Application and Project Execution of the Six Sigma methodology to specific projects
1.4.2.2. Black Belts differ from those above in so much as they are primarily focused on execution, whereas levels higher are focused on identifying problems in the process
1.5. Green Belts
1.5.1. Operating under Black Belts
1.5.2. Responsibilities include:
1.5.2.1. Green Belts are primarily recognized as those who's job function requires application of the Six Sigma method.
1.5.2.2. They may or may not decide to continue the training
2. The Process
2.1. DMAIC
2.1.1. D- Define
2.1.1.1. The Problem
2.1.1.2. The customer's voice
2.1.1.3. The project goals
2.1.2. M- Measure
2.1.2.1. Key aspects of the current process
2.1.2.1.1. Collect data
2.1.3. A - Analyze
2.1.3.1. the data to determine cause-and-effect relationships
2.1.3.1.1. ensure all factors have been considered
2.1.3.1.2. identify the Root Cause of the defect under investigation
2.1.4. I - Improve
2.1.4.1. the process based upon data
2.1.4.1.1. Design of Experiements
2.1.4.1.2. Poka Yoke | mistake proofing
2.1.4.2. Create the future state process
2.1.4.2.1. establish pilot programs to test process capability
2.1.5. C - Control
2.1.5.1. the future state process
2.1.5.1.1. any derivations must be corrected before they result in future defects
2.1.5.2. implement control systems
2.1.5.2.1. statistical process control
2.1.5.2.2. production boards
2.1.5.2.3. visual workplaces
2.1.5.3. Continually monitor and control
2.2. DMADV of DFFS
2.2.1. D - Define
2.2.1.1. Goals that are inline with both customer demands, as well as Enterprise Strategy
2.2.2. M - Measure
2.2.2.1. Identify CTQ's (Critical To Quality)
2.2.2.2. Product Capabilities
2.2.2.3. Production process capability
2.2.2.4. Risks
2.2.3. A - Analyze
2.2.3.1. To design and develop alternative processes
2.2.3.2. Create a broad reaching design
2.2.3.3. Analyze and evaluate design capability
2.2.4. D - Design
2.2.4.1. Details
2.2.4.2. Optimize the design and prepare for..
2.2.4.3. Design verification
2.2.4.4. Various simulations may be required for optimization
2.2.5. V - Verify
2.2.5.1. The design
2.2.5.2. Establish Pilot and test verification programs
2.2.5.3. Implement the new process and deliver it to it's new owner.