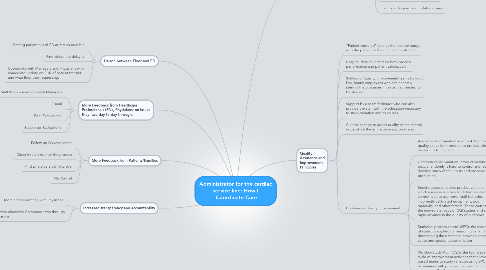
1. More Feedback from Healthcare Professionals (RNs, Physicians) on Issues they face day-to-day through:
1.1. All Staff Weekly meetings with Managers
1.2. E-mail
1.3. Peer Evaluations
1.4. Supervisor Evaluations
2. More Feedback from Patients/Families
2.1. Follow up Surveys online
2.2. Direct Interviews after the process
2.3. Find where care can improve
2.4. Mail/E-mail
3. Liaison between Floor and ED
3.1. Getting patient out of ED as fast as possible
3.2. Find where the delay is
3.3. Coordinate with Managers and Physicians with immediate update on EHR of patient transfer and what floor they requesting.
4. Increased transparency and accountability
4.1. More communication with Physicans
4.2. More electronic Communciation through liasons
5. Better/Open Communication with Mourning "huddle" meeting between Managers of and Liaison for each department in the ER:
5.1. medicine/telemetry unit
5.2. coronary care unit
5.3. thoracic intensive care unit
5.4. cardiac catheterization laboratory
5.5. echocardiogram and its laboratories.
6. Quality Assurance and Improvement Principles
6.1. “Patient centered” care as the focus of study, with the patient as the ultimate “customer”
6.2. Hospital data collected on both process performance and patient satisfaction
6.3. Staffing of Quality Improvement teams by front line, hourly employees who can honestly identify the processes in place that needed to be studied
6.4. Support by a team facilitator who can also provide the staff with the education necessary to study variation and its causes
6.5. Cultural change to adopt quality as the central value which the entire organization shares
6.6. Continuous Quality Improvement
6.6.1. Assessment of variation in output: the more quality varies from product to product, the harder it is to manage
6.6.2. Common cause variation: product variation that occurs randomly is hard to control and requires detailed study of the inputs and processes of production
6.6.3. Special cause variation: product variation for which a reason is easier to determine and control, due to user error, staff behavior, incorrectly calibrated equipment, poor materials, and other factors. These causes are the immediate focus of CQI studies and allow rapid advance in the quality of outcomes.
6.6.4. Statistical process control (SPC): the discipline of statistics applied to measuring variation and determining the difference between common cause and special cause variation
6.6.5. Plan/Do/Study/Act (PDSA): the four stage cycle of improvement activities that allows staff based teams to study variation using SPC and experiment with process changes that improve outcomes effectively as needed by the customer