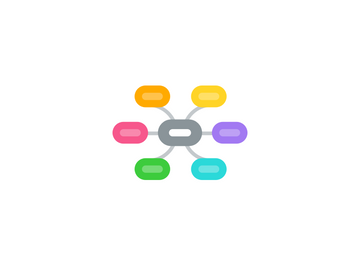
1. CLR
1.1. MAIN PAGE
1.1.1. PAGE SPECIFIC INFORMATION
1.1.1.1. IS SYNC INFORMATION IDENTIFIED ON MAIN PAGE
1.1.1.2. IS THE LATEST TSO NUMBER IDENTIFIED ON THE MAIN PAGE
1.1.1.3. IS THE BIT RATE IDENTIFIED ON THE MAIN PAGE
1.1.1.4. IS A DETAILED SOURCE OF TIMING IDENTIFIED ON THE MAIN PAGE OR REFERENCE TO TIMING LAYOUT; I.E. EQUIPMENT TYPE, SIGNAL TYPE, STRATUM REFERENCE, PHYSICAL CONNECTIONS
1.1.1.5. IS THE CCO IDENTIFIED ON THE MAIN PAGE WITH VALID CONTACT INFORMATION OR REFERENCE
1.1.1.6. IS THE FULL CCSD LISTED ON THE MAIN PAGE
1.1.1.7. IS THE LATEST TSP NUMBER ON THE MAIN PAGE
1.1.1.8. IS SYNC INFORMATION IDENTIFIED ON MAIN PAGE
1.1.2. RESPONSIBILITY SPECIFIC INFORMATION
1.1.2.1. IF NOT SERVICING TCF OVER CIRCUIT OR TRUNK AND IT MAKES A PHYSICAL APPERANCE IN FACILITY ARE ALL APPLICABLE AND NECESSARY ITEMS OF SERVICE DEPICTED ON MAIN PAGE
1.1.2.2. IF NOT SERVICING TCF OVER CIRCUIT OR TRUNK AND IT MAKES NO PHYSICAL APPERANCE IN FACILITY ARE ALL APPLICABLE AND NECESSARY ITEMS OF SERVICE DEPICTED ON MAIN PAGE
1.1.2.3. IF SERVICING TCF OVER CIRCUIT OR TRUNK AND IT MAKES NO PHYSICAL APPERANCE IN FACILITY ARE ALL APPLICABLE AND NECESSARY ITEMS OF SERVICE DEPICTED ON MAIN PAGE
1.1.2.4. IF SERVICING TCF OVER CIRCUIT OR TRUNK AND IT MAKES A PHYSICAL APPERANCE IN FACILITY ARE ALL IN-HOUSE ITEMS DEPICTED ON MAIN PAGE AS WELL AS ALL EXTERNAL APPLICABLE AND NECESSARY ITEMS
1.1.3. LOCATION SPECIFIC INFORMATION
1.1.3.1. IS EACH APPLICABLE EQUIPMENT ITEM LABELED IN THE MAIN PAGE WITHIN A ROOM NUMBER OR NAME
1.1.3.2. IS EACH APPLICABLE EQUIPMENT ITEM LABELED IN THE MAIN PAGE WITHIN A COUNTRY IF NECCESSARY OR APPLICABLE
1.1.3.3. IS EACH APPLICABLE EQUIPMENT ITEM LABELED IN THE MAIN PAGE WITH SHELF NUMBER OR IF MULTIPLE OF LIKE EQUIPMENT WHICH NUMBER IN SERIES
1.1.3.4. IS EACH APPLICABLE EQUIPMENT ITEM LABELED IN THE MAIN PAGE WITHIN A SITE
1.1.3.5. IF CIRCUIT IS WITHIN FACILITY ARE ALL APPLICABLE ITEMS DEPICTIED IN DIAGRAM
1.1.3.6. IS EACH APPLICABLE EQUIPMENT ITEM LABELED IN THE MAIN PAGE WITH RACK NUMBER
1.1.3.7. IS EACH APPLICABLE EQUIPMENT ITEM LABELED IN THE MAIN PAGE WITHIN A BUILDING NUMBER OR NAME
1.1.4. EQUIPMENT SPECIFIC INFORMATION
1.1.4.1. IS EACH APPLICABLE EQUIPMENT ITEM'S OUTPUT/INPUT PORT DEPICTED IN THE MAIN PAGE
1.1.4.2. IS EACH APPLICABLE EQUIPMENT ITEM LABELED IN THE MAIN PAGE WITH EQUIPMENT TYPE; MANUFACTURER, MODEL, ETC
1.1.4.3. IS EACH EQUIPMENT ITEM LABELED IN THE MAIN PAGE WITH EQUIPMENT NOMENCLAUTRE; DISA ID, LOCAL ID, ETC.
1.1.5. CONNECTION SPECIFIC INFORMATION
1.1.5.1. IS EACH ELECTRICAL INTERFACE IDENTIFIED WITH APPLICABLE STANDARD; IF NON-STANDARD IS IT IDENTIFIED WITH A REFERENCE
1.1.5.2. IS EACH PHYSICAL MEDUIM IDENTIFED IN ACCORDANCE WITH THE CURRENT COLOR LABELING REFERENCE
1.1.5.3. IS EACH PHYSICAL INTERFACE IDENTIFIED WITH APPLICABLE STANDARD, PINOUT, OR ROUTING; IF NON-STANDARD IS IT IDENTIFIED WITH A REFERENCE
1.1.6. FORMATING SPECIFIC INFORMATION
1.1.6.1. ARE ALL APPLICABLE FACILITES/ROOMS/SITES IDENTIFIED BY A CLEAR FORM OF SEPERATION
1.1.6.2. ARE ALL DEMARKS IDENTIFIED IN MAIN CLR BY CURRENT VERSION'S FORMATTING TECHNIQUE
1.1.6.3. IF A CLOUD OR OTHER GENERAL ROUTING FORMAT IS USED TO DEPICT IN HOUSE ROUTING IS IT REFERENCED TO A DETAILED DIAGRAM
1.1.6.4. ARE ALL APPLICABLE TRANSMISSION LINES LABLED WITH SIGNAL DIRECTIONS
1.1.6.5. IS THE CURRENT VERSION TEMPLATE BEING USED
1.2. Policy Requirement Documentation
1.2.1. CLRs for digital circuits must include timing and sync information (e.g., synchronous, asynchronous or isochronous), data rate, electrical and mechanical interface type (i.e., RS-232, RS-449, MIL-STD-188-114A, etc.), signal type (i.e., NRZ, Bipolar/AMI, B8ZS, etc.), protocol (i.e., Bisync, HDLC, SDLC, etc.), and source of timing.
1.2.2. CLRs for analog circuits must include audio signal levels, type signaling, and signaling frequency for each transmission level point (TLP).
1.2.3. In-facility circuit layout records (CLRs) must be completed for all trunks and circuits that have a physical patch panel appearance in the TCF/PTF, and for all trunks and circuits for which the TCF/PTF is the servicing TCF/PTF. The CLR must depict "infacility" equipment and cross-connect information. The reverse side of DD Form 1441 may be used to satisfy this requirement. Other methods, including automated, may also be used. TCF/PTFs with numerous circuits of the same configuration (e.g., DSN IST's) may use one CLR that depicts the common configuration as long as specific cross-connect, conditioning equipment, and other pertinent information is maintained for each individual circuit.
2. FACIT
2.1. Front Page
2.1.1. Is the correct category identified
2.1.2. Is the current rate identified
2.1.3. If HIT/SI is it identified
2.1.4. Is the current Purpose/Use identified
2.1.5. Is the current TSP identified
2.1.6. Is the correct circuit identifier declared
2.1.7. Is the mission impact identified in the mission statement section
2.1.8. Is the current service availability identified
2.2. Other Tabs
2.2.1. Affected Circuits
2.2.1.1. If circuit has lower level circuits are they identified in this section
2.2.2. Affected By Circuits
2.2.2.1. Is circuit rides higher level trunk is it identified
2.2.3. Equipment
2.2.4. Circuit Actions
2.2.4.1. Is the current TSO# identified
2.2.4.2. Is the status of the action current
2.2.5. Interested Parties
2.2.5.1. Are any applicable interested parties identified
2.2.6. QC
2.2.6.1. No longer used. CAD replaces
2.2.7. Path
2.2.7.1. Is the current CCO identified
2.2.8. Diagrams
2.2.8.1. Is there a updated diagram in accordance with CLR checklist and attached as a link
2.2.9. Reportable
2.2.9.1. If circuit is designated to be reported to a facility/organization are they identified
2.2.9.1.1. MOC
2.2.9.1.2. CFP
2.2.10. Alternate Designator
2.2.10.1. If circuit is identified by other name by any other organization is it entered into fields
2.2.10.1.1. TRUNK ID
2.2.10.1.2. ALLA
2.2.10.1.3. MDA circuit number
2.2.10.1.4. Mission Id
2.2.10.1.5. Phone number
3. PHYSICAL
3.1. Has all equipment been properly labeled?
3.1.1. Equipment
3.1.1.1. Promina Cards
3.1.1.1.1. Circuit Identification
3.1.1.1.2. Node Identification
3.1.1.2. Software
3.1.1.2.1. Broadmore
3.1.1.2.2. CTC
3.1.1.3. ALL EQUIPMENT CHASSIS
3.1.1.3.1. POC NAME
3.1.1.3.2. POC ORGANIZATION
3.1.1.3.3. POC PHONE NUMBER
3.1.1.3.4. POC EMAIL ADDRESS
3.1.2. Patch Panel
3.1.2.1. Types
3.1.2.1.1. Circuit Identification
3.1.2.2. Policy Requirement Documentation
3.1.2.2.1. Labels all patch bays, test boards, or other circuit access points normally used by technical control personnel. As a minimum, labeling must include the last four characters of the circuit Command Communications Service Designator (CCSD) and the NCS TSP restoration priority. If a NCS TSP is not assigned, then the letters "NA" (none assigned) must be entered with the CCSD to indicate that the circuit has no assigned restoration priority.
3.1.3. Cable
3.1.3.1. Font Size
3.1.3.1.1. 6
3.1.3.2. Label Size
3.1.3.3. Required Information
3.1.3.3.1. CCSD
3.1.3.3.2. From Location
3.1.3.3.3. From Equipment
3.1.3.3.4. From Equipment Specifics
3.1.4. Rack
3.1.4.1. Rack Identification
3.1.4.1.1. Rack Identification Number in Series
3.1.4.2. Layout
3.1.4.2.1. Center Top
3.1.4.3. Format
3.1.4.3.1. LABEL SIZE
3.1.4.3.2. FONT SIZE
3.1.4.3.3. LABEL COLOR
3.1.5. NOTES
3.1.5.1. Labeling Devices
3.1.5.1.1. Brother PT-2400/2410
3.1.5.1.2. Dymo
3.1.5.1.3. ID Expert
3.1.5.2. Colors Thoughts
3.1.5.2.1. BACKGROUND COLOR
3.1.5.2.2. TEXT
3.2. Has all equipment been properly installed?
3.2.1. Cable
3.2.1.1. DONT
3.2.1.1.1. Lay cable across racks
3.2.1.1.2. Use longer cable than required, thereby making it neccessary to wrap cable in trough
3.2.1.1.3. Use zipties
3.2.1.2. DO
3.2.1.2.1. Tie cable to one side of rack
3.2.1.2.2. Use exacting measurements from and to equipment
3.2.1.2.3. Use pre-existing main cable One Trunk out of rack
3.2.2. Equipment
3.2.2.1. DO
3.2.2.1.1. Ground Properly
3.2.2.1.2. Leave space between adjoining equipment
3.2.2.1.3. Allow for air circulation
3.2.2.1.4. Label with POC contact information
3.2.2.2. DONT
4. MISCELLANEOUS
4.1. If applicable has the CLR been sent to all persons?
4.2. If applicable have the CSIRS records been updated?
4.2.1. Description
4.2.1.1. The CSIR is a collection of records associated with the installation of a communications and information system in a facility, building or location. The CSIR is comprised of three parts; (1) an administrative record, (2) drawing record, and (3) maintenance record. These records provide both a historical record of communications system and equipment installation and a living document that reflects how the system/equipment is modified over time. It is used for planning, programming, and supporting communications systems/equipment operations, maintenance, integration, and Engineering and Installation (EI) efforts. The record documents the locations and physical configuration of communications systems/ equipment in a facility, building or location.
4.2.2. Policy Requirement Documentation
4.2.2.1. AFI 33-101
4.2.2.1.1. Develop and maintain CSIR drawing records in the CIPS Visualization Component (CVC) or installation supported systems or facilities
4.2.2.2. MPTO 00-33A-1001
4.2.2.2.1. They are required for all AF-owned fixed communications and information systems regardless of who maintains or operates the systems.
4.2.3. Unsure
4.2.3.1. Was any equipment removed or installed?
4.2.3.1.1. Yes
4.2.3.1.2. No
4.3. If applicable has the network diagram been updated?
4.3.1. Optical Cloud
4.3.2. Node Site Coordinator
4.4. If applicable have historical records been updates?
4.4.1. Unsure
4.4.1.1. Was any equipment or equipment items that would be inventoried in IMDS installed?
4.4.1.1.1. Yes
4.4.1.1.2. No
4.4.1.1.3. Unsure
4.4.1.1.4. Policy Requirement Documentation
4.4.2. Description
4.4.2.1. Work center facility, systems installation, and equipment records are historical documentation that constitute a permanent record of significant maintenance actions or significant changes to the facility or system. Historical records must remain with each equipment or system throughout its life cycle. They are designed to provide technicians and item managers with an accurate portrayal of significant actions, modifications, issues, and overhauls.
4.4.3. Policy Requirement Documentation
4.4.3.1. Historical records, AFTO Form 95, Significant Historical Data, Integrated Maintenance Data System (IMDS) history files or other records, are required on all Mission Capable (MICAP) reportable equipment, command supported equipment, and other equipment as designated by the Item Manager/System Manager/Program Manager (IM/SM/PM).
4.5. Has the circuit configuration been properly documented?
4.6. Has the user letter been sent to all applicable persons and is there proof of it properly stored on the shared drive?
4.6.1. Policy Requirement Documentation
4.6.1.1. Sends DII user notification letters to each user upon activation of a new circuit, and annually thereafter. An updated letter should also be sent any time information contained in the letter affects the users ability to contact appropriate personnel (i.e., phone number, point of contact, etc.).
5. CIRCUIT HISTORY FOLDER
5.1. Policy Requirement Documentation
5.1.1. Each history file must contain a copy of:
5.1.1.1. In-effect, exception, and delayed service reports applicable to the latest TSO.
5.1.1.2. Status Acquisition Message (SAM).
5.1.1.3. Copies of quality control waiver requests and approvals.
5.1.1.4. The initial test and acceptance data (DD Form 1697 or 1697-1)
5.1.1.5. Copies of the latest TSO that reflects the current end-to-end configuration, control office assignment, etc.
5.1.1.6. Copies of any appropriate documentation (i.e., QC results, letters, etc.) resulting from action(s) taken to resolve degradations when a trunk or circuit fails management threshold for two consecutive months or more. Documentation must be kept on file for 1 year.
5.1.2. Automation
5.1.2.1. The ADP system must provide for adequate backup capability so that computer failure will not prevent the maintenance of required records or the retrieval of information
5.1.2.2. If ADP systems are used to maintain TCF/PTF records, all personnel must also be trained to use the paper forms required by this chapter. A 90-day supply of paper forms must be maintained and accessible to personnel on duty. Contingency procedures must be developed to include instructions on how and when to revert to manual recordkeeping.
5.1.2.3. The ADP system must be redundant with a second computer immediately available to replace a failed unit
5.1.2.4. The backup process should be an automated procedure, or should at least prompt the operator to perform the required actions
5.1.3. Each TCF/PTF must establish and maintain permanent history files for
5.1.3.1. all trunks and circuits for which the TCF/PTF is the CCO/CMO or servicing TCF/PTF
5.1.3.2. all trunks and circuits that have physical patching capabilities within the TCF/PTF
5.1.3.3. all links that terminate at their facility
5.1.4. Circuit history files are not required for through facility trunks and circuits that do not have physical patch appearances, unless the TCF/PTF is the CCO/CMO or servicing TCF/PTF.