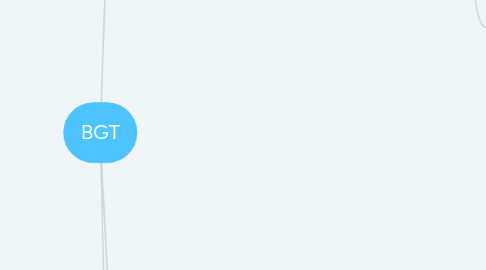
1. 検出能力の進化
1.1. 具体的な課題
1.2. 何をしないといけないか?
1.2.1. 深層学習による検査?
1.2.2. 世の中の最新技術を吸収
1.2.3. 前工程プロセスの理解
1.2.4. 前工程エンジニアからのヒアリング
1.2.5. 開発した技術のパッケージ化
1.3. 前工程を想定した課題
1.3.1. 導入台数が多い
1.3.1.1. 導入コストを下げないと
1.3.1.1.1. タイプ毎の設定を不要に、無しに
1.3.1.1.2. 学習コスト削減、効率化
1.3.1.2. エラーが発生しない検査
1.3.1.2.1. 材料バラツキ、製造工程の揺らぎを吸収する
1.3.1.2.2. ロバストな検査
1.3.1.2.3. セッティングの間違いが発生し難いシステム
1.3.2. 大量不良防止(Dコストが高い)
1.3.2.1. 不良を作らないシステム
1.3.2.1.1. 異常を検知して工程にフィードバック
1.3.2.1.2. リアルタイムでの欠陥分類(成分特定)
1.3.2.2. 早い段階で異常検出
1.3.2.2.1. 薬液塗布状態の監視
1.3.2.2.2. プロセスの監視
1.3.3. 検査対象のサイズが大きい
1.3.3.1. 分割撮像
1.3.3.1.1. 撮像時間の高速化
1.3.3.1.2. 無停止撮像
1.3.3.2. 低解像度画像(低倍率)
1.3.3.2.1. 超解像技術
1.3.4. 材料、タイプ毎のバラツキが大きい.製造工程のゆらぎ(EBR)
1.3.4.1. 自己学習技術
1.3.4.1.1. 2つのネットワークで追加学習
1.3.5. 検出対象と背景の分離
1.3.5.1. 対象のみを検出する技術
1.3.5.1.1. 分光特性を利用
1.3.5.1.2. 偏光技術
1.3.6. データが集まるか?
1.3.6.1. データを収集する仕組み
1.3.6.1.1. オンライン収集
1.3.6.1.2. データ保存サーバーが必要
1.3.6.2. 集めたデータのラベル付け作業
1.3.6.2.1. 自動化
1.3.6.2.2. 外注
2. 使いやすさの進化
2.1. 前工程を想定した課題
2.1.1. 導入台数が多い
2.1.1.1. 導入コストの削減が必要
2.1.1.1.1. オンラインソフトアップデート
2.1.1.1.2. ソフトアップデート時の整合性チェック
2.1.1.1.3. RMS機能
2.1.1.1.4. パラメータの横展開
2.1.1.1.5. 導入後の精度、確からしさ確認機能
2.1.1.1.6. 配線コスト
2.1.2. SEMI規格の通信仕様に対応
2.1.2.1. SECS通信対応
2.1.3. 画像処理に不慣れなエンジニアが対応
2.1.3.1. パラメータの自動設定
2.1.3.1.1. なにを?
2.1.3.1.2. どうやって?
2.1.3.2. ユーザーI/Fの共通化
2.1.3.3. 導入後の精度確認機能
2.1.3.4. 順番通りにやれば設定完了するシステム
2.1.4. 導入台数に対するエンジニアパワー不足
2.1.5. 設置場所がない
2.1.5.1. 小型カメラ
2.1.6. 設備からのトリガーがない
2.1.6.1. 動画トリガー技術
2.1.7. 製品情報がない
2.2. 貢献、効果
3. コストダウン
3.1. 前工程を意識した課題
3.1.1. 導入台数が多い
3.1.1.1. 機器のコストダウン
3.1.1.2. 導入のやり易さUP(使いやすさに記載)
3.1.1.3. 集中制御
3.1.1.3.1. ニーズ
3.1.1.3.2. 課題
3.1.2. 設備を借用を十分にできない
3.1.2.1. シミュレーション
3.1.2.1.1. 画像シミュレーション
3.1.2.1.2. 軸動作シミュレーション