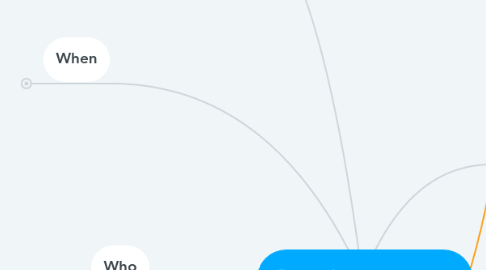
1. Tools
1.1. Lean
1.1.1. Value Stream mapping
1.1.1.1. Process mapping
1.1.1.2. assign data
1.1.1.2.1. Processing time
1.1.1.2.2. waiting time
1.1.1.2.3. Cost resources
1.1.1.2.4. Risk
1.1.1.2.5. Systems
1.1.2. Fishbone
1.1.3. 5 Whys
2. When
2.1. @ Fixed times, KPIs Review
2.1.1. After every Q-report
2.1.2. Annual Client survey
2.1.3. Annual staff survey
2.2. When ideas come fwd
2.2.1. When one proposes an idea either goes to the backlog or -if really good- is prioritized and acted upon
2.3. When a problem appears
2.4. Audit findings
3. How (Analysis)
3.1. Plan
3.1.1. Generic: Problem selection and benefit analysis
3.1.2. Define the problem to be solved, including customer impact and potential benefits
3.1.3. Generic: Translation of the problem into a measurable form, and measurement of the current situation
3.2. Do
3.2.1. List causes, identify key process variables that cause issues, prioritize
3.2.2. Id influences input vs outputs
3.2.3. Design change
3.2.4. Benchmark the change
3.2.5. Implement change
3.2.6. Comms and training
3.3. Check
3.3.1. Monitor metrics & benchmark
3.3.2. Audit process/Change
3.4. Act
3.4.1. adjust if necessary
3.4.2. Implement ongoing measures and actions to sustain improvement
3.5. Share knowledge & replicate
4. Project management
5. Who
5.1. Process owner
5.1.1. Risk
5.1.2. Compliance
5.2. Project Portfolio Mgr
5.3. Business Analysts
5.4. CI Ambassadors
6. Infrastructure
6.1. The platform to store and prioritize change ideas should be MS Teams/Sharepoint which can be customized and is available. Also a simple solution.
6.2. Events of 1-2 days to see the whole process through; incl. implementation.
7. Why
7.1. improving existing services (Focused on debt transactions)
7.1.1. Improve efficiency
7.1.2. Improve service delivery
7.1.3. Improve control