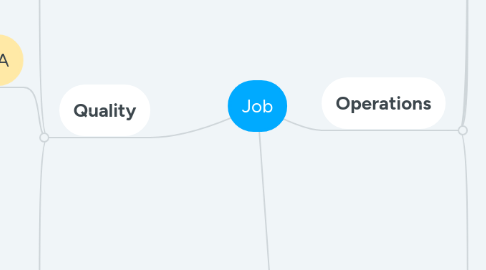
1. Quality
1.1. Environmental Health
1.1.1. Unannounced Audit
1.2. STS / SALSA
1.2.1. Annual Announced Audit
1.2.2. Cleaning Records
1.2.2.1. Daily records
1.2.3. Glass & Plastic Records
1.2.3.1. Daily Records
1.2.4. Maintenance Records
1.2.4.1. Monthly records
1.2.5. Supplier Approval Records
1.2.5.1. Product Specifications
1.2.5.1.1. Raw Materials
1.2.5.1.2. Packagaging
1.2.5.1.3. Finished Product
1.2.5.2. Annual review
1.2.6. Lab Results
1.2.6.1. Environmental Swabbing
1.2.6.2. End Product testing
1.2.6.3. Water Testing
1.2.6.4. Drain testing
1.3. Customer Visits and Queries
1.3.1. Announced Audits
1.3.2. Allergen Assessments
1.3.3. Supplier Forms
2. Improvements / Achievements
2.1. 2019
2.1.1. Creation of 40+ SOPs
2.1.2. Encouraging use of EFACs
2.1.3. saving £5000 per year by changing waste contract supplier
2.1.4. saving £10000 per year by reducing staffing hours whilst increasing output
2.1.5. SALSA implemented within 30 days of starting
2.1.6. Internal Layout of Production area completely changed within 30 days of starting, leading to more efficient workflow
2.1.7. Despatch area moved to increase efficiency
2.2. 2020
2.2.1. Managed the changeover of the factory to a COVID safe factory, Implemented social distancing and maintained workflows
2.2.2. Working alongside one other staff member March to May before unfurloughing, working excessive hours for the company (All produciton, despatch and admin)
2.2.3. trained Paul to become autonomous in general duties of operations
2.2.4. Successful passing of STS/SALSA
2.3. 2021
3. Operations
3.1. Production
3.1.1. Maintenance
3.1.2. Management of 3 Staff
3.1.2.1. Appraisals
3.1.2.2. Training & Development
3.1.2.3. H&S
3.1.3. Scheduling of all Coffee
3.1.4. Quality Control
3.1.4.1. Ensuring adherence to SOPs
3.1.4.2. GRN procedures
3.1.4.3. Management of 1 direct / 2 indirect
3.1.4.4. Managing internal quality checking
3.1.4.4.1. Ensuring cupping scheduled
3.1.4.4.2. Ensuring roast degree measurement
3.1.4.4.3. Staffing: Roasters / QC
3.1.4.4.4. Container Checks
3.2. Warehousing / Despatch
3.2.1. Management of 2 staff
3.2.1.1. Appraisals
3.2.1.2. Training & Development
3.2.1.3. H&S
3.2.2. Warehousing
3.2.2.1. Ensuring adherence to SOPs
3.2.2.2. GRN procedures
3.2.3. Despatch
3.2.3.1. Selecting suitable couriers
3.3. Purchasing/Reordering
3.3.1. Purchasing of all Ancillaries
3.3.2. Purchasing of all Machines
3.3.3. Logistics Of Arrival
3.3.4. Management of 1 staff
3.4. Site Services and Maintenance
3.4.1. Fire
3.4.1.1. weekly alarm testing
3.4.1.2. Ensuring training upkeep
3.4.1.2.1. Fire warden training
3.4.1.2.2. Induction training
3.4.1.3. Monthly Extinguisher checks
3.4.1.4. On-Site contact
3.4.1.5. Annual Audit
3.4.2. Health and Safety
3.4.2.1. Manual Handling
3.4.2.2. Induction Training
3.4.2.3. PPE
3.4.2.4. On Site Contact
3.4.2.5. Forklift Training
3.4.2.6. Risk Assessments
3.4.3. Plumbing (Gas & Water)
3.4.3.1. On-Site contact
3.4.4. Electrician
3.4.4.1. On-Site contact
3.4.5. Builders
3.4.5.1. On-Site contact
3.4.6. Air Compressor
3.4.6.1. On-Site contact
3.4.6.2. Servicing
3.4.7. Security System
3.4.7.1. Alarm Board
3.4.7.1.1. Servicing
3.4.7.2. Dialer
3.4.7.2.1. On-site contact
3.4.7.3. CCTV
3.4.8. Gardens
3.4.8.1. Arranging upkeep
3.4.9. Waste Management
3.4.9.1. On Site Contact