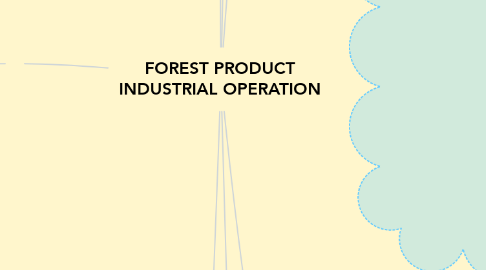
1. Linear Programming
1.1. A mathematical approach to the problem of allocating limited resources among competing activities
1.2. Mathematical technique for finding optimal solution to problems that can be expressed using linear equations and linear inequalities
1.3. known as linear optimization
1.4. Consist of...
1.4.1. A set of variables, usually denoted as xj ( j = 1,…,n,).
1.4.1.1. The variables in a linear program are a set of quantities that need to be determined in order to solve the problem
1.4.1.2. variables represent the amount of a resource
1.4.2. A linear objective function
1.4.2.1. represented by mathematical function of the variables
1.4.2.2. Two most typical forms of objective functions: Maximize f (x) or minimize f (x)
1.4.3. A set of linear constraints
1.4.3.1. Mathematical equation or inequality that represents a restriction due to a resource or technological limitation
1.5. Application of linear progeamming
1.5.1. Scheduling of personnel
1.5.2. Inventory control and production planning
1.5.3. Blending problems
1.5.4. Transportation
1.5.5. Forest management planning
1.6. Steps in LP Model Formulation
1.6.1. Define the decision variables
1.6.2. Formulate the objective function
1.6.2.1. Maximize profit
1.6.2.2. Maximize cost
1.6.2.3. Maximize overtime
1.6.3. Formulate the constraints
1.6.3.1. result of a resource or technological limitations
1.6.4. writing out the non-negativity constraint
1.6.4.1. , the variables of linear programs must always take non-negative values
1.6.5. Formulating and Solving LP Problems
1.6.5.1. Formulating the problem
1.6.5.1.1. the process of translating a real-world problem into a linear program
1.6.5.2. Solving the problem
1.6.5.2.1. a computer program can be used to solve the problem
1.6.5.3. Interpreting the solution
1.6.5.3.1. the mathematical solution is translated back to the real world
1.6.6. Reduce cost
1.6.6.1. indicates how much the coefficient on the corresponding variable
1.6.6.1.1. In the case of a minimization problem, “improved” means “reduced.”
1.6.6.1.2. In the case of a maximization problem, “improved” means “increased.”
1.6.6.2. units of the reduced cost values are the same as the units of the corresponding objective function coefficients
1.6.6.3. Since both variable values are positive, the reduced cost values are zero
1.6.7. Shadow Price
1.6.7.1. the “improvement” in the objective function if the constraint is relaxed by one unit
1.6.7.1.1. In the case of a less-than-or-equal constraint, such as a resource constraint, the dual price gives the value
1.6.7.1.2. In the case of a greater-than-or-equal constraint, such as a minimum production level constraint
1.6.7.2. non-zero when a constraint is binding
1.6.7.3. units of the objective function divided by the units of the constraint
1.6.8. Feasibility and Optimality
1.6.8.1. solution is a set of values for each variable that
1.6.8.1.1. are consistent with the constraints
1.6.8.1.2. result in the best possible value of the objective function
1.6.8.2. The problem may be unbounded
2. Lean manuacturing
2.1. what ?
2.1.1. A systematic approach for achieving the shortest possible cycle by eliminating the process waste through continuous improvement
2.1.2. manufacturing without waste
2.1.3. production of goods using less of everything compared to traditional mass production
2.2. Push versus Pull
2.2.1. The Push System
2.2.1.1. “batch-and-queue” manufacturing method
2.2.1.2. manufacturing as much product in as little time as possible
2.2.1.3. This type of production manufactures and distributes products based on market forecasts
2.2.2. The Pull System
2.2.2.1. emphasizes pulling the products through the manufacturing process
2.2.2.2. starts with the customer; that is, nothing is manufactured until the customer orders it
2.2.2.3. within the manufacturing process, the next processing centre can be thought of as an internal customer.
2.2.2.4. Parts are not passed on from one processing station
2.3. What is Waste?
2.3.1. Waste is anything that happens to a product that does not add value
2.3.2. Products being stored, inspected or delayed, products waiting in queues, and defective products do not add value
2.3.3. Seven types of waste
2.3.3.1. over production
2.3.3.1.1. Producing more/sooner than the Internal or External customer needs
2.3.3.2. movement
2.3.3.2.1. Excessive movement of people, information or materials.
2.3.3.3. inventory
2.3.3.3.1. Excessive storage and delay of information or products.
2.3.3.4. poor processing
2.3.3.4.1. Using the wrong set of tools, procedures or systems.
2.3.3.5. waiting
2.3.3.5.1. Long periods of inactivity for people, information, machinery or materials
2.3.3.6. defect
2.3.3.6.1. Frequent errors in paper work, product quality problems
2.3.3.7. motion
2.3.3.7.1. people or equipment moving or walking more than is required to perform the processing.
2.4. 5 principles of lean
2.4.1. Specify value
2.4.1.1. Specify value from the standpoint of the end customer
2.4.2. Identify the value stream
2.4.2.1. steps in the value stream for each product family, eliminating whenever possible those step dont create value
2.4.3. Create flow
2.4.3.1. value-creating steps occur in tight sequence so the product will flow smoothly
2.4.4. Let the customer pull product through the value stream
2.4.4.1. Make only what the customer has ordered
2.4.5. Seek perfection
2.4.5.1. value streams are identified, wasted steps are removed, and flow and pull are introduced
2.5. Lean Tools
2.5.1. poka yoke
2.5.1.1. “Mistake proofing”
2.5.1.2. techniques/device to prevent defects
2.5.1.3. drive defects out of products and process
2.5.1.4. human error which ultimately can improve quality and reliability
2.5.1.4.1. Wrong part used in the process
2.5.1.4.2. Measurement error
2.5.1.5. Three types of poka-yoke for detecting and preventing errors
2.5.1.5.1. The contact method identifies product defects by testing the product's characteristic
2.5.1.5.2. The fixed-value or constant number method alerts the operator if a certain number of movements are not made
2.5.1.5.3. The motion-step or sequence method determines whether the prescribed steps of the process have been followed
2.5.2. 5s visual workplace
2.5.2.1. Sort
2.5.2.1.1. Organized-keeping what is necessary and throw unused product
2.5.2.2. Set in order
2.5.2.2.1. Orderliness-arrange and label the item
2.5.2.3. Shine
2.5.2.3.1. Cleanliness-make sure everything is clean and clear
2.5.2.4. Standardized
2.5.2.4.1. Standardized cleanup-state the exist first item
2.5.2.5. Sustain
2.5.2.5.1. Sustain the discipline-make the discipline habit
2.5.3. Just in time
2.5.3.1. only what is needed, when it is needed, and in the amount needed
2.5.3.2. produce just in time
2.5.3.3. lead to huge improvements in quality and efficiency
3. Management of quality
3.1. Quality Definition
3.1.1. the ability of a product or service to consistently meet or exceed customer requirements or expectations
3.1.2. Different customers will have different expectations
3.1.3. what the customers want, then translating this information into technical specifications
3.1.4. Understanding dimensions that customers use to judge the quality of a product or service
3.2. Dimensions of Product Quality
3.2.1. Performance– main characteristics of the product
3.2.2. Aesthetics– appearance, feel, smell, taste
3.2.3. Special features– extra characteristics
3.2.4. Conformance– how well the product conforms to design specifications
3.2.5. Reliability– consistency of performance
3.2.6. Durability– the useful life of the product
3.2.7. Perceived quality– indirect evaluation of quality
3.2.8. Service-ability– handling of complaints or repairs
3.3. Dimensions of Service Quality
3.3.1. Convenience– the availability and accessibility of the service
3.3.2. Reliability– ability to perform a service dependably, consistently, and accurately
3.3.3. Responsiveness– willingness to help customers in unusual situations and to deal with problems
3.3.4. Time– the speed with which the service is delivered
3.3.5. Assurance– knowledge exhibited by personnel and their ability to convey trust and confidence
3.3.6. Courtesy– the way customers are treated by employees
3.3.7. Tangibles– the physical appearance of facilities, equipment, personnel, and communication materials
3.3.8. Consistency– the ability to provide the same level of good quality repeatedly
3.4. Benefits of Having Good Quality
3.4.1. Competitive Advantage
3.4.2. Raise Company’s Reputation
3.4.3. Rationalize Premium Prices
3.4.4. Decrease Liability Costs
3.4.5. Increase Productivity
3.4.6. Increase Customer Loyalty
3.4.7. Increase Customer Satisfaction
3.5. Consequences of Poor Quality
3.5.1. loss of business and existing market share
3.5.2. legal liability
3.5.3. lack of productivity
3.5.4. increased costs
3.6. Quality Product and Service?
3.6.1. Effective organizations need systems to ensure their products or services achieve the highest level of quality
3.6.2. A variety of standards, program, and award provide guidance into how to establish and implement a quality management system and effective organization
3.7. What Standards, Programs and Awards Exist
3.7.1. Quality Standards
3.7.1.1. ISO 9000
3.7.2. Awards
3.7.2.1. Malcolm Baldridge National Quality Award, Japan’s Deming Prize
3.7.3. Programs
3.7.3.1. Total quality management
3.8. Basic quality Tools
3.8.1. Pareto analysis
3.8.2. Flowcharts
3.8.3. Check sheets
3.8.4. Histograms
3.8.5. Scatter diagrams
3.8.6. Control charts
3.8.7. Fishbone diagram
4. 1. Production and Operations Management
4.1. production and operation management
4.1.1. Production can be seen on things like factories, machines, equipment and assembly lines.
4.1.1.1. “Production” refers as the step-by-step taken of material to form another thing
4.1.1.2. "Management" is a process involve the manage activity
4.1.1.2.1. Planning
4.1.1.2.2. Organizing
4.1.1.2.3. Motivating
4.1.1.2.4. Controlling
4.1.2. Production concept and idea literally been applied in manufacturing process and also service provided
4.1.2.1. Product manufacturing
4.1.2.2. Hotel management
4.1.2.3. Restaurant management
4.1.2.4. Education sector
4.2. good producer and service producer
4.2.1. manufacturing organizations produce physical, tangible goods that can be stored in inventory before they are needed.
4.2.2. service organizations produce intangible products that cannot be produced ahead of time.
4.3. production system
4.3.1. Input + Resources > Process(Production/transformation) > Output
4.4. elements of production system
4.4.1. Input
4.4.2. Output
4.4.3. Production process
4.4.4. Resources
4.5. why production and operation management is important
4.5.1. Reduce cost product and service with efficient
4.5.2. Can increase revenue through increases customer satisfaction in producing quality goods and services
4.5.3. reduce the amount of investment (capital employed) necessary to produce the goods and service by being effective and innovative in the use of resources
5. 2. Plant location
5.1. One of the major strategy decisions that must be made by organization especially for manufacturer is where to locate its first factory
5.1.1. Location options for any organizations
5.1.1.1. Corporations choose from expanding an existing facility
5.1.1.2. Shutting down one location and moving to another
5.1.1.3. Adding new locations while retaining existing facilities
5.1.1.4. Options of doing nothing and maintaining the status quo
5.2. Why ?
5.2.1. shift of location to some other place known as relocation
5.2.2. expanding the market and diminishing resources
5.2.3. companies will expand their markets
5.3. Location factors
5.3.1. broad array of factors that can influence revenue, costs, or both, and profits
5.3.2. operational location factors
5.3.2.1. Market related factor
5.3.2.1.1. Locations of demand
5.3.2.1.2. Location of competitors
5.3.2.2. Tangible cost factors
5.3.2.2.1. Transportation
5.3.2.2.2. Raw material availability and costs
5.3.2.2.3. Labor availability and costs
5.3.2.2.4. Site and construction costs
5.3.2.2.5. Taxes
5.3.2.3. Intangible factors
5.3.2.3.1. Stability of political environment
5.3.2.3.2. Zoning and legal consideration
5.3.2.3.3. Quality of life
5.4. Location evaluation methods
5.4.1. decision where to locate
5.4.2. three techniques to help a location decision
5.4.2.1. The transportation model method
5.4.2.1.1. minimize the cost of transportation
5.4.2.1.2. production of sources supplies
5.4.2.1.3. demand sources or destination
5.4.2.1.4. minimize transportation cost
5.4.2.2. Linear programming method
5.4.2.3. Geographic information system (GIS)
5.4.2.3.1. determining the location of a facility which will reduce transportation costs (travel time).
5.4.2.3.2. using GIS software
5.4.3. Factor-rating method
5.4.3.1. involves qualitative and quantitative inputs
5.4.3.2. evaluates alternatives based on comparison after establishing
5.4.3.3. Steps involved in the method
5.4.3.3.1. Develop a list of locational factors
5.4.3.3.2. Assign weight to each factors from 0 – 1.0
5.4.3.3.3. Assigned a subjective score (usually between 0 to 100) for each factor
5.4.3.3.4. Multiply score by weight
5.4.3.3.5. Recommend the location with the highest point score
5.4.4. The center-of-gravity technique
5.4.4.1. a quantitative method for locating a facility
5.4.4.2. indicates the ideal location in the grid-map
5.4.4.3. involves the use of a visual map and a coordinate system
5.4.4.4. three locations, 1, 2, and 3, each at a set of coordinates (xi, yi)
5.4.4.5. value Wi is the annual weight/quantity/volume
5.4.4.6. to determine a central location for a new facility
5.4.4.7. coordinates for the location of the new facility are computed using formulas
6. 3. Plant layout
6.1. When and why ?
6.1.1. When the company first starts its business
6.1.2. ensure a smooth flow of work
6.2. Types of facility layout
6.2.1. Fixed position
6.2.1.1. materials or major components remain in a fixed position
6.2.1.2. used when product is very bulky, heavy or fragile
6.2.1.3. used in large construction projects
6.2.2. Process
6.2.2.1. equipment and workstations are arranged according to the type of process they perform
6.2.2.2. Machines are grouped into departments
6.2.2.3. most movement of products from workstation to workstation
6.2.2.4. Advantages
6.2.2.4.1. better utilized and fewer machines are required
6.2.2.4.2. Flexibility of equipment and personnel is possible
6.2.2.4.3. Lower investment
6.2.2.5. Disadvantages
6.2.2.5.1. lot of inventory
6.2.2.5.2. expensive and consume much time
6.2.3. Product
6.2.3.1. to achieve a smooth and rapid flow
6.2.3.2. Geared to production line which manufacture only one product
6.2.3.3. Equipment and manual workstations are arranged to mirror the required flow
6.2.3.4. Advantages
6.2.3.4.1. Reduced material handling activities
6.2.3.4.2. Work In Process almost eliminated
6.2.3.4.3. Minimum manufacturing time
6.2.3.4.4. Simplification of the production planning and control systems
6.2.3.4.5. Tasks simplification
6.2.3.5. Disadvantages
6.2.3.5.1. No flexibility in the production process
6.2.3.5.2. Low flexibility in the manufacturing times
6.2.3.5.3. High capital investment
6.2.3.5.4. workstation is critical to the process
6.2.3.5.5. Monotonous work
7. 4. Forecasting
7.1. Introduction
7.1.1. the process of predicting the future of supplier, manufacturer or retailer
7.1.2. used sales forecast from marketing department for operations planning
7.1.3. forecast machine breakdown
7.1.4. – forecast on product group or families
7.2. The Time Horizon
7.2.1. Short term
7.2.1.1. Day-to-day planning
7.2.2. Intermediate term
7.2.2.1. Measured in weeks or months
7.2.3. Long-term
7.2.3.1. Firm’s manufacturing strategies
7.3. Forecasting Techniques
7.3.1. Qualitative approaches
7.3.1.1. subjective opinions from one or more experts
7.3.1.2. Hierarchical method
7.3.1.2.1. salesmen are required to estimate expected sales in their respective territories and sections
7.3.1.2.2. sales manager of a region could take all individual forecast to produce aggregate regional forecast
7.3.1.2.3. Advantages
7.3.1.2.4. Disadvantages
7.3.1.3. Expert opinion
7.3.1.3.1. Develop a forecast from the results of interview
7.3.1.3.2. Advantages
7.3.1.3.3. Disadvantages
7.3.1.4. Delphi method
7.3.1.4.1. consist of an effort to arrive at a consensus about expected level of demand
7.3.1.4.2. The results are compiled and a summary of the result is returned to the expert
7.3.1.4.3. The process is repeated
7.3.1.4.4. Response received and analyzed by independent body
7.3.1.4.5. Advantages
7.3.1.4.6. Limitations
7.3.1.5. Surveys
7.3.1.5.1. known as opinion surveys
7.3.1.5.2. signal future trends and shifting preference patterns
7.3.1.5.3. effective in forecasting market share, product redesign, product repackaging, setting prices
7.3.1.5.4. Advantages
7.3.1.5.5. Limitations
7.3.2. Quantitative approaches
7.3.2.1. Rely on data and analytical techniques
7.3.2.2. Moving averages
7.3.2.2.1. known as rolling average, moving mean, or running average
7.3.2.2.2. Analyze a series of averages of different subset of numbers from a larger set of data
7.3.2.2.3. commonly used with time series data to smooth out short term fluctuation
7.3.2.2.4. highlight longer-term trends or cycles
7.3.2.2.5. Simple Moving Average (SMA)
7.3.2.3. Weighted moving averages (WMA)
7.3.2.3.1. the ability to give more importance to what happened recently
7.3.2.4. Exponential smoothing
7.3.2.4.1. provides an exponentially weighted moving average of all previously observed values
7.3.2.5. Linear regression
7.3.2.5.1. Estimating the linear trend in a time series
7.3.2.5.2. The estimated regression equation describing a straight-line relationship between an independent variable