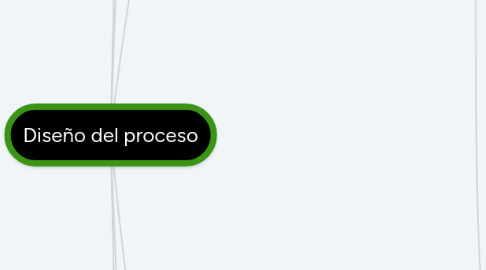
1. Orientacion de la distribucion
1.1. Las dos orientaciones básicas de la distribución son la producción en masa y el trabajo en el taller. La producción en masa está orientada al producto y sigue una trayectoria fija a través de la planta. La línea de ensamble ilustra mejor la orientación a la producción en masa. Ésta es preferible a la orientación al trabajo en el taller, porque el costo unitario es menor, pero no todos los productos siguen una trayectoria fija.
1.1.1. Tecnicas
1.1.1.1. 1. La tecnología de grupo trata de clasificar las partes en grupos con secuencias de proceso similares. Después, el equipo se coloca en línea recta o como celda de manufactura siguiendo una ruta fija. La planta podría tener una línea de lámina metálica, línea de plásticos, línea de barras, línea de fundición, etcétera. El objetivo es reducir el tránsito, los retrocesos y la distancia de viaje.
1.1.1.2. 2. Una celda de manufactura es un grupo de máquinas que se dedican a fabricar una parte complicada. Uno o dos operadores pueden manejar de seis a 10 máquinas. Éstas permanecen preparadas en forma indefinida para hacer dicha parte. Algunas de ellas tal vez no se utilicen por completo, pero el tiempo perdido se compensa con la menor cantidad de inventario que se requiere, menos manejo de materiales y el tiempo de recorrido inferior (el tiempo que una parte pasa en el proceso de producción).
2. Fabricacion
2.1. Se conoce como establecer ruta a la secuencia de etapas que se requiere para producir (manufacturar) una parte única. La parte se mete a la ruta de la primera máquina a la segunda y así sucesivamente, hasta que está terminada para unirse con otras partes. El formato que se emplea para describir el establecimiento de la ruta se conoce como hoja de ruta.
2.1.1. Hojas de ruta
2.1.1.1. Se requiere una hoja de ruta para cada parte individual del producto que se fabrica (para las partes que se manufacturan). Si el producto terminado que se va a hacer tiene 30 partes diferentes, de las que 10 se compran fuera de la compañía (compras) y 20 se elaboran en ésta, entonces se necesitan 20 hojas de ruta. La hoja de ruta enlista las operaciones que se necesitan para fabricar cada parte en la secuencia apropiada. Debe su nombre a la forma en que se usa
2.1.2. Numero de maquinas necesario
2.1.2.1. La pregunta de cuántas máquinas deben comprarse sólo puede responderse si se conoce lo siguiente: 1. ¿Cuántas unidades terminadas se necesitan por día? 2. ¿Qué máquina procesa qué partes? 3. ¿Cuál es el tiempo estándar para cada operación?
3. Tabla de cargas de trabajo en las celdas
3.1. Para entender mejor el concepto de celda de manufactura se necesita definir el concepto de tecnología de grupo. La tecnología de grupo aprovecha las ventajas de la similitud de las partes o las características en un grupo de partes o familia de éstas, de modo que pueden procesarse como grupo. La tecnología de grupo requiere que los dibujos técnicos incluyan cierto esquema de códigos que especifique el tipo y los parámetros del procesamiento que son necesarios. El tipo de proceso que especifica el código, puede ser, por ejemplo, una operación de perforación
3.1.1. 1. Reducen el tiempo de arranque en forma significativa. 2. Eliminan todo almacenamiento entre operaciones.
3.1.2. 3. Eliminan la mayoría de tiempo de movimiento entre operaciones. 4. Terminan con los retrasos por esperar a la máquina siguiente. 5. Reducen los costos.
3.1.3. 6. Disminuyen el inventario (disminuciones de trabajos en proceso). 7. Reducen el tiempo de manufacturas en proceso.
4. Analisis del proceso de ensamble y empaque
4.1. Una vez que todas las partes han sido producidas por los departamentos de manufactura o recibidas de los proveedores y están listas para ensamblarse, se necesitan nuevas herramientas analíticas.
4.1.1. Grafica de ensamble
4.1.1.1. Muestra la secuencia de operaciones para juntar las partes del producto. El diseñador de la distribución hará el diagrama del proceso de ensamble con el uso del dibujo de desglose y la lista de partes. La secuencia de ensamble tiene varias alternativas. Para decidir cuál es la mejor, se requieren los estándares de tiempo. Este proceso se conoce como balanceo de la línea de ensamble.
4.1.2. Tiempo para cada tarea
4.1.2.1. Las tareas deben ser tan pequeñas como sea posible, de modo que el diseñador de instalaciones tenga la flexibilidad de dar una a varios ensambladores diferentes. Las técnicas para establecer los estándares de tiempo usados en el diseño de la línea de ensamble provienen ya sea de un sistema de estándares de tiempo predeterminados o de datos estándar.
4.1.3. Tasa de produccion y velocidad del transportador
4.1.3.1. La velocidad del transportador depende del número y las unidades que se necesitan por minuto, el tamaño de la unidad, el espacio entre unidades y, a veces, el espacio para engancharlas. La velocidad del transportador se registra en pies por minuto. Por tanto, el tamaño de la parte más el espacio entre ellas (medidos en pies), multiplicado por el número de partes que se necesitan en un minuto, es igual a los pies por minuto.
4.2. Subensamble, soldadura, pintura del ensamble final y empaque son operaciones incluidas en esta área de la planta.
5. Elaborar un formato de balanceo de la linea de ensamble
5.1. Los propósitos de la técnica de balanceo de la línea de ensamble son los siguientes: 1. Igualar la carga de trabajo de los ensambladores. 2. Identificar la operación que constituya el cuello de botella. 3. Establecer la velocidad de la línea de ensamble. 4. Determinar el número de estaciones de manufactura. 5. Calcular el costo de la mano de obra de ensamblado y empaque. 6. Establecer la carga de trabajo porcentual de cada operador. 7. Auxiliar en la distribución de la planta. 8. Reducir el costo de producción.
5.1.1. Los subensambles que podrían retirarse de la línea deben ser los siguientes:
5.1.1.1. 1. Los que tienen carga deficiente. Entre más pequeño es el porcentaje cargado, más deseable es subensamblar.
5.1.1.2. 2. Partes pequeñas que se guardan y almacenan con facilidad.
5.1.1.3. 3. Elementos que se mueven sin dificultad. El costo de transporte e inventario se elevaría, pero debido a la mejor utilización de la mano de obra, el costo total debe descender.