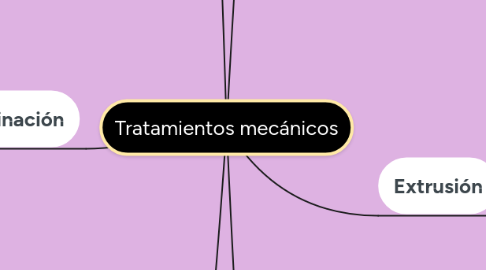
1. Corte
1.1. El corte de metal tiene como objetivo obtener una pieza con la forma, las dimensiones y los acabados necesarios para su función. Las piezas obtenidas tras estos procesos se emplean en sectores como la construcción, la siderurgia, la industria eléctrica, la del automóvil o en las telecomunicaciones.
1.1.1. Los procesos de mecanizado más tradicionales son: aserrado, torneado, fresado y taladrado. Las piezas deseadas se generan con el desprendimiento de metal en forma de virutas.
1.1.2. Son conceptos básicos en estos procesos el metal sobrante (sobre espesor), la profundidad de corte, la velocidad de avance, la velocidad de corte y el ángulo de corte.
1.1.3. La clasificación de la viruta puede hacerse según su tipo, calificándose como viruta discontinua, continua o continua con protuberancias; según su clase, por lo que puede ser plástica, cortada o de arranque. Y, según su forma, de agujas, desmenuzadas, helicoidaes, hélices, etc.
1.1.3.1. Tipos de corte:Troquelado
1.1.3.2. Se realiza con troqueles en máquinas denominadas prensas. Es necesario definir la forma de la pieza final, sus dimensiones, las características del material y si es posible extraer con facilidad la pieza de la matriz. Este proceso es utilizado para elaborar desde monedas a señales para carreteras.
1.1.3.3. Oxicorte:
1.1.3.4. En este caso el corte se realiza por la combustión de un gas (propano, hidrógeno, acetileno, etc.) junto a oxígeno, para dar lugar a una reacción química. El corte se produce por la combustión del propio metal, que es quemado a medida que se avanza con el soplete sobre su superficie. Es muy utilizado para el corte de chapas, barras de acero al carbono de baja aleación, para el corte manual de acero de gran espesor y de otros metales férricos.
1.1.3.5. Corte por plasma:
1.1.3.6. Se basa en la acción de un chorro de gas calentado por un arco eléctrico de corriente continua. El chorro de gas-plasma es lanzado contra el metal, para fundir una zona determinada de la pieza de trabajo. A la vez, el chorro elimina el material derretido.
2. Laminación
2.1. Proceso industrial por medio del cual se reduce el espesor de una lámina de metal con la aplicación de presión mediante el uso de distintos procesos, como la laminación de anillos o el laminado de perfiles. Por tanto, este proceso se aplica sobre materiales con un buen nivel de maleabilidad. La máquina que realiza este proceso se le conoce como laminador.
2.2. El laminado puede ser en frío o en caliente. El laminado en caliente es el que se realiza con una temperatura bastante mayor a la de la recristalización que tiene el metal. La forma actual del laminado en caliente deriva del proceso patentado por el británico Henry Cort en 1783, que es popularmente conocido como «el padre de la laminación» debido al gran impacto de dicho proceso en la industria metalúrgica.
2.2.1. Laminado en caliente Laminado en frió Laminado de perfiles
2.2.1.1. Ventajas: Con las operaciones en caliente se logran cambios significativos en la forma del material. Las operaciones en frió incrementan la resistencia del metal, y en ninguno de los casos anteriores se genera desperdicio de material. Desventajas: El lamina requiere una elevada inversión de capital y al realizarse en caliente sin ningún otro tipo de tratamiento suele haber un grado de oxidación.
2.2.1.1.1. Aplicaciones: Barras, varillas, marcos estructurales, laminas, placas, etc.
3. Embutido
3.1. La embutición es un proceso tecnológico que consiste en la obtención de piezas huecas con forma de recipiente a partir de chapas metálicas. Este proceso permite obtener piezas de formas muy diversas.
3.2. En la embutición de una pieza se parte de una porción de chapa que descansa sobre la matriz, mientras el pisador la mantiene sobre esta y el punzón ejerce la presión necesaria para conformar la pieza provocando la fluencia del material a través de la cavidad abierta en la matriz. La pieza va a conformarse en función de la forma de la abertura de la matriz y la forma del punzón, mientras que el pisador va a evitar el pandeo del material.
3.2.1. Fases del proceso: 1.Se coloca una silueta circular con espesor to y diámetro D sobre la superficie de la matriz que tiene una abertura con el diámetro d2. Normalmente, en la arista de la abertura de la matriz está aplicado un radio rd.
3.2.2. 2.El pisador pisa la chapa y se inserta el punzón con el diámetro d1 en la dirección del eje. El extremo del punzón tiene el radio rp. Este mismo radio queda como el radio del fondo del vaso embutido.
3.2.3. 3.Conforme el punzón se introduce en la matriz, se embute la parte central de la silueta progresivamente mientras el perímetro de la silueta se desliza sobre la superficie de la matriz y se traslada hacia el interior de la misma.
3.2.4. 4.Al encoger la circunferencia de la silueta se generan esfuerzos de compresión en la dirección circunferencial de la chapa, los cuales pueden provocar el pandeo y producir arrugas. Para evitar este fenómeno se sujeta la silueta con el pisador.
3.2.5. 5.En el momento de que se embute la chapa, se comprime en la dirección circunferencial y se dobla recibiendo la tensión en la dirección radial simultáneamente en la boca de la abertura de la matriz. De igual manera la parte que tiene contacto con la cabeza del punzón recibe la tensión, sobre todo las zonas de los radios de matriz y punzón son la que recibe la mayor tensión del doblado. La zona cilíndrica entre rd y rp, la cual corresponde a la pared lateral del recipiente se estira verticalmente.
3.2.6. 6.Así la silueta avanza gradualmente a través de la abertura de la matriz recibiendo diversas fuerzas y deformándose. Si el material resiste los esfuerzos que se generan durante este proceso, la pieza se conformará plásticamente y alcanzando su forma final.
4. Forja
4.1. Proceso de fabricación que utiliza la deformación plástica en caliente por la aplicación de fuerzas de compresión. La deformación se puede realizar de dos formas diferentes: por presión, de forma continua utilizando prensas, o por impacto, de modo intermitente utilizando martillos pilones.
4.1.1. Los principales tipos de forja que existen son:
4.1.2. Forja libre
4.1.3. Forja con estampa
4.1.4. Recalcado
4.1.5. Forjado isotérmico
4.1.6. Aplicaciones: bielas, cigüeña les, ejes, rejas, barandillas, cabezas de tornillos y pernos, remaches, clavos, etc.
4.1.6.1. Efectos que produce la forja en caliente: Orientación de la fibra: las propiedades mecánicas del producto variarán, si el esfuerzo se aplica en la dirección de la fibra. Afinamiento del grano: esto se produce a temperaturas superiores a la de recristalización pero inferiores a la de equicohesión y la forja se realiza con martillos pilones, de modo intermitente. Eliminación de cavidades, poros, sopladuras, debido a las enormes presiones a las que el material es sometido en la operación, este es compactado y desaparecen las cavidades, poros, sopladuras, etc.
4.1.6.1.1. Este proceso puede aplicarse a: Metales puros: aluminio, cobre, titanio y zinc. Aleaciones: acero, de aluminio, de cobre, de magnesio y bronces
5. Extrusión
5.1. Es un proceso utilizado para crear objetos con sección transversal definida y fija. El material se empuja o se extrae a través de un troquel de una sección transversal deseada. Las piezas finales se forman con una terminación superficial excelente.
5.2. En cierta medida, se puede hacer la analogía divulgativa de un material sólido que sale por la boquilla de una jeringilla o matriz que se va moviendo. Se podría decir que es una especie de inyección de un material.
5.3. La extrusión puede ser continua (produciendo teóricamente de forma indefinida materiales largos) o semicontinua (produciendo muchas partes). El proceso de extrusión puede hacerse con el material caliente o frío.
5.3.1. Los materiales extruidos comúnmente incluyen metales, como los polímeros, cerámicas, hormigón y productos que se usan para la construcción.
5.3.1.1. Extrusión en frío
5.3.1.1.1. Ventajas:
5.3.1.1.2. Una reducción del 25 a 30 % de la fuerza de fricción, permite la extrusión de largas barras.
5.3.1.1.3. Hay una menor tendencia para la extrusión de que el material se resquebrajarse o quebrarse porque no hay calor formado por la fricción.
5.3.1.1.4. El recubrimiento del contenedor durará más debido al menor uso.
5.3.1.1.5. La barra es usada más uniformemente tal que los defectos de la extrusión y las zonas periféricas ásperas o granulares son menos probables.
5.3.1.1.6. Desventajas:
5.3.1.1.7. Las impurezas y defectos en la superficie de la barra afectan la superficie de la extrusión. Antes de ser usada, la barra debe ser limpiada o pulida con un cepillo de alambres.
5.3.1.1.8. Este proceso no es versátil como la extrusión directa porque el área de la sección transversal es limitada por el máximo tamaño del tallo.
5.3.1.2. Extrusión tibia
5.3.1.3. Extrusión directa
5.3.1.4. Extrusión hidrostática
5.3.1.5. Extrusión indirecta
6. Doblado
6.1. En el doblado, el metal se somete a esfuerzos tanto en tensión como de compresión con valores inferiores a la resistencia límite del material, sin un cambio apreciable del espesor. Tal como en una prensa dobladora, el doblado simple implica un doblez recto a lo largo de la lámina de metal.
6.2. Para diseñar una sección rectangular a doblar, uno debe determinar cuánto metal se debe dejar para el doblez, pues las fibras exteriores se alargan y las interiores se cortan. Durante la operación, el eje neutro de la sección se mueve hacia el lado de la compresión, lo cual arroja más fibras en tensión. Todo el espesor disminuye ligeramente, el ancho aumenta en el lado de la compresión y se acorta en el otro.
6.2.1. Prensa dobladora
6.2.2. Se usan para doblar, formar, rebordear, repujar, desbarbar y punzonar lámina metálica de bajo calibre. Tales prensas pueden tener espacio para lámina de 6 m de ancho y 16 mm de espesor.
6.2.3. La capacidad de presión requerida de una prensa dobladora para un material dado, se determina por la longitud de la pieza, el espesor del metal y el radio del doblez. El radio mínimo interior de doblez se limita usualmente a un valor igual al espesor del material.