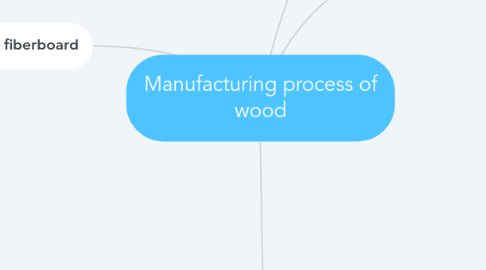
1. Particleboard and fiberboard
1.1. Processes
1.1.1. 1. Cleaning: it is placed in the debarker to clean them. The process is different because the pieces of wood used are of different sizes.
1.1.2. 2. Splinter machine: the pieces of wood are passed to turn them into small pieces, like splinters or chips.
1.1.3. 3. Warehouse: the still wet particles are kept in humid warehouses.
1.1.4. 4. Drying: it is carried out with hot air in large cylinders with forced circulation.
1.1.5. 5. Classification: it is divided into size, povo and minor residue.
1.1.6. 6. Formation of the board: all the pieces suitable for the thickness of each board are placed in the machinery.
1.1.7. 7. Comber: distributes the pieces evenly to make the shape of the board.
1.1.8. 8. Thin layer: a last thin layer of particles is placed to give the final finish to the board.
1.1.9. 9. Press: the board is pressed with a roller to compress.
1.1.10. 10. wet: wet to improve setting that thermally crimps the blanket
1.1.11. 11. Cutting and drying: The sheets are cut hot and allowed to dry in a square.
1.1.12. 12. Square and sandpaper: it is cut squarely and aligned, then it is sanded to calibrate the board.
2. Technique: It has been evolving until the Industrial era.
2.1. United States: Portland Manufacturing Company -> established a plywood plant. they used the penolic stickers.
2.2. Useful for the construction, aeronautics, naval and furniture industries.
3. First appearances: Egyptian era (1500 B.C.)
4. Wood veneer
4.1. Processes of Veneer and plywood
4.1.1. 1. Planting
4.1.2. 2. Harvest: when the trees reach maturity they are cut in a modular way and transported to the factory.
4.1.3. 3. Preparation: before entering the production line, they are wetted through asper to eliminate fungi.
4.1.4. 4. Cleaning: Once they are chosen to obtain flat or round veneer, they are prepared and cleaned with a roller that removes all the bark leaving the trunk flat.
4.1.5. 5. Cutting: they are cut to a appropriate size to use the machinery.
4.1.6. 6. Flat faces: the trunk is cut so that there are 4 flat faces so that the wood veneer can be removed from there.
4.1.7. 7. Steaming: the pieces are placed in a steam bath to soften the wood and facilitate cutting.
4.1.8. 8. Wood veneer cutting: vaporized the piece of wood is placed in the machinery to cut each veneer.
4.1.9. 9. Dry: as they come out of the cut they are transported to the dryer.
4.1.10. 10. Arrangement and cutting: technicians from the plant accommodate the veneer that comes out in mounds, then cut the corners length and width to make them the same size and shape.
4.1.11. 11. Classification: by streaks, knots, etc.
4.1.12. To make plywood: 12. The best veneers are attached through a machine by making wide sheets of wood that adhere through pressure and heat to the plank.
4.1.13. 13. Cutting and polishing: once it is adhered, it is cut and polished to make a perfect surface.