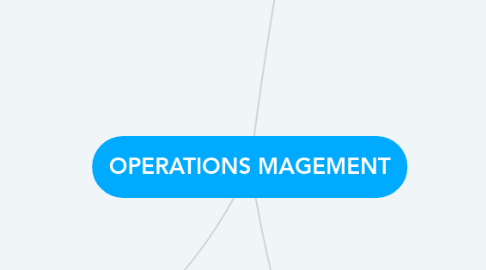
1. PROJECT PLANNING PROBABILISTIC AND HEURISTIC METHODS
1.1. AGGREGATE PLANNING OPTIMIZATION AND DISAGGREGATION OF A MPS
1.1.1. Planning is one of the most important activities in a company because it is a function of the management that systemize the available resources, such as the manpower, raw material, machinery and the equipment used for a product manufacturing.
1.2. NETWORKS WITH PROBABILISTIC TIMING AND PROJECT SHORTENING
1.2.1. In a project, you need to do a detailed planning; otherwise, you have the risk of affecting the work due to the cost increases produced by unnecessary delays and the lack of coordination.
1.3. DEFINITION OF HEURISTIC METHODS AND LIMITATIONS OF JOBS SEQUENCING
1.3.1. Heuristics are a problem-solving method that uses shortcuts to produce good-enough solutions given a limited time frame or deadline. Heuristics are a flexibility technique for quick decisions, particularly when working with complex data.
1.4. STOCHASTIC MODELS FOR JOBS SEQUENCING
1.4.1. Stochastic modeling is a form of financial model that is used to help make investment decisions. This type of modeling forecasts the probability of various outcomes under different conditions, using random variables.
1.5. LINE BALANCING
1.5.1. Line balancing is a production strategy that involves balancing operator and machine time to match the production rate to the Takt time.
2. INVENTORY MODDEL
2.1. IMPORTANCE AND RELEVANT COSTS ON INVENTORY CONTROL
2.1.1. Inventory carrying costs are the costs related to storing and maintaining its inventory over a certain period of time. Inventory costs are described as a percentage of the inventory value
2.2. SIZE OF THE ECONOMIC QUANTITY
2.2.1. Inventory model is a mathematical model that helps business in determining the optimum level of inventories.
2.3. INVENTORY MODEL
2.3.1. Inventory model is a mathematical model that helps business in determining the optimum level of inventories.
2.4. MRP
2.4.1. Material Requirements Planning (MRP) is a system for calculating the materials and components needed to manufacture a product.
2.5. BASIC CONCEPTS OF THE CRP, MPS AND MRP
2.5.1. CRP
2.5.1.1. Capacity Resource Planning (CRP) is a management tool, as it serves to make short, mid and long - term decisions on the objectives
2.5.2. MPS
2.5.2.1. Master Production Schedule (MPS) refers to the major plan that is used to assess the production of finalized items. MPS displays the varying amounts that firms need to produce for each period of business in terms of final articles.
2.5.3. MRP
2.5.3.1. Material Requirements Planning (MRP) is a planning and control system for inventory, production, and scheduling. MRP converts the master schedule of production into a detailed schedule, so that you can purchase raw materials and components.
3. INVENTORY CONTROL SYSTEMS AND AGGREGATE PLANNING
3.1. JIT
3.1.1. The just-in-time (JIT) inventory system is a management strategy that aligns raw-material orders from suppliers directly with production schedules.
3.2. OPT
3.2.1. The OPT (Optimized Production Technology) system calculates the near-optimum schedule and sequence of operations for all a manufacturing company’s work centers, taking into account priorities and capacities.
3.3. PRODUCTION CONTROL SYSTEM
3.3.1. Production control system is the system performs planning and management activities to make the effective use of human resources, raw materials, and facilities based on the order information received from customers.
3.4. PROJECT MANAGEMENT
3.4.1. Project management involves the planning and organization of a company's resources to move a specific task, event, or duty towards completion.
3.5. AGGREGATE PLANNING ELEMENTS: GRAPHICS AND CHARTS
3.5.1. Aggregate planning involves projecting market demand and evaluating production capacity to ensure that a firm is sufficiently equipped to meet demands for a given period.