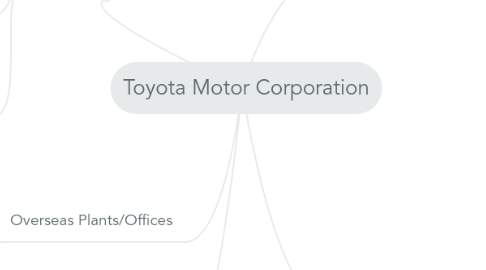
1. Overseas Plants/Offices
1.1. Altona Plant (Australia)
1.1.1. Produces cars for the Australian market - saves on transport costs
1.1.2. Also Australia's biggest vehicle export company
1.2. Each regional/national office uses its own marketing strategies - has different promotions, discounts, etc in response to differing economic situations
1.3. Overseas Global Production Centres (GPCs) established in Thailand,US and UK
2. Products/Marketing Strategy
2.1. Prices of the same product can differ in different regions due to economic situation - A Toyota Land Cruiser can cost up to 20,000 euros more in France than in USA
2.2. Sells different products in different regions due to differences in tastes and cultures
3. Toyota as a TNC
3.1. Impacts
3.1.1. Highly popular firm in Kentucky, US - 70000 people applied for only 3000 jobs because of the high wages (double the average pay), generous pension plan and the safe working environment
3.1.2. Toyota's precision in work led to employees suffering ill health as a result of long hours doing repetitive work. To solve this, they operated on a rotational job basis so workers learn to do different jobs and also become more skilled.
3.1.3. Insistence on using Japanese components in their products squeezes out local firms. Car manufacturers have like Ford have complained that Toyota makes use of the UK as a place to manufacture and sell cars with most profits returning to Japan.
3.1.3.1. British manufacturers unable to adapt to Toyota's flexible production methods and develop similar technology --> unable to compete
4. Production System
4.1. Kaizen (Continuous Improvement)
4.1.1. Workers seek continual improvement despite standardised work guidelines - based on theory that problems are most apparent to those who are involved in the process
4.2. Just In Time Manufacturing
4.2.1. Strives for absolute elimination of waste, overburden and unevenness in all areas.
4.2.2. A term coined by Toyota
4.2.3. Entire production process regulated by the laws of supply and demand.
4.2.4. Activity in the system only occurs in response to customer orders
4.2.5. When sales increase, more resources are allocated to avoid overburdening the workers
4.3. Jidoka (Automation with a human touch)
4.3.1. Encourages workers to identify opportunities for making improvements and work with management to improve the production system.
4.3.2. Design equipment that will stop and call for attention once abnormalities are observed, halting production - improves product quality
4.4. Suppliers
4.4.1. Each process is the customer for the preceding process and the supermarket for the next process.
4.4.2. Suppliers usually make use of JIT manufacturing processes as well.
4.4.3. 2012 Tohoku earthquake - many of Toyota's single suppliers were affected, causing supply bottlenecks for Toyota. The company aims to increase the number of suppliers and also engage in consolidation to gives suppliers economies of scale.
4.4.4. Sources most parts from suppliers - separated into different tiers depending on production stage.