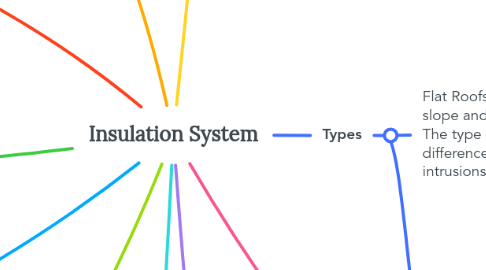
1. Vapour Barrier (VB)
1.1. Purpose of VB
1.1.1. VB's purpose is to prevent water vapour from reaching the inside of the building where it can condense and cause mold and rot
1.2. Water Vapour
1.2.1. Water Vapour is water in it's gas state and is invisible.
1.2.2. As water vapour passes through a wall, veiling or other barrier and meets a surface that has temperature below the dew point then becomes condensation.
1.2.2.1. Water vapour constantly diffuses through building materials from the warm interior of a house towards the cold dry exterior
1.3. What is VB?
1.3.1. Vapour Barrier is a sheet used to prevent condensation from forming in building assemblies
1.4. Classes
1.4.1. 2. (0.1-1.0 perm) Unfaced EPS or XPS, #30 Asphalt coated paper, Bitumen sandwiched kraft paper.
1.4.2. 1. (0.1 perm or less) Sheet metal, Polyethylene sheet, Rubber membrane.
1.4.3. 3. (>1perm<10 perm) Gypsum board, Fibreglass insulation, cellulose insulation, board lumberm concrete block, #15 asphalt coated paper, House wrape ( I.E. Tyvek)
1.4.4. Note that Polythylene sheets & bitumen coated kraft paper are not acceptable materials by RCABC Roofstar Guarentee
1.4.5. North America is divided into 8 climate areas. Marine, Cold, Very cold, Subarctic, Mixed dry, Hot dry, Mixed humid, Hot humid
1.4.5.1. Marine cold, Very cold, and Subarctic recommended to have class I or II Vapour Retarder
2. Types
2.1. Flat Roofs Function with very little slope and the insulation is crucial. The type of insulation makes a big difference to saving energy, water intrusions and roof degradation.
2.1.1. Perlite
2.1.1.1. R Value or 2.75 per inch
2.1.1.2. Heat INSENSITIVE and flame resistant
2.1.1.3. Not widely used
2.1.1.4. Made from volcanic glass
2.1.2. Yellow Death (Fiberglass)
2.1.2.1. R Value of 3.1-3.4 per inch
2.1.2.2. Flame RESISTANT
2.1.2.3. Non toxic but may cause skin irritation
2.1.2.4. Not typically used anymore
2.1.3. ISO (polyisocyanurate)
2.1.3.1. R Value of 5.75 per inch
2.1.3.2. Heat INSENSITIVE
2.1.3.3. Most commonly glass facer
2.1.4. XPS (extruded polyststyrene)
2.1.4.1. R Value 4.75-5 per inch
2.1.4.2. Type 4 required on protected membrane assemblies
2.1.4.3. Heat SENSITIVE and will melt if exposed to hot asphalt or primers/adhesives
2.1.5. Mineral wool
2.1.5.1. R value of 3.5 per inch
2.1.5.2. Heat INSENSITIVE
2.1.5.3. with the appropriate facer may be torched to the insulation
2.1.6. Phenolic
2.1.6.1. R Value of 6.7-7.5 per inch
2.1.6.2. Heat INSENSITIVE flame resistant
2.1.6.3. Causes corrosion of metal if moisture is introduced to the system
2.1.6.4. because of the corrosive properties it isn't widely used
2.1.7. EPS (Expanded polystyrene)
2.1.7.1. R Value of 3.75-4.25 per Inch
2.1.7.2. Often used for tapered insulation
2.1.7.3. Heat SENSITIVE
2.1.7.4. Often referred to as "Popcorn"
2.1.8. CT Board ( concrete top board)
2.1.8.1. Uses type 4 XPS with concrete on top
2.1.8.2. Used for protected membrane assembly (P.M.A)
2.1.9. Vermiculite (Asbestos)
2.1.9.1. BC's Leading cause of workplace related deaths.
2.1.9.2. Anything built or installed prior the 1990's should be tested for Asbestos
2.1.9.3. DO NOT DISTURB ASBESTOS!
2.1.10. Fibreboard (Donna Conna)
2.1.10.1. R Value of 2 per inch
2.1.10.2. VERY FLAMMABLE and will potentially smolder for hours before igniting
2.2. Desirable properties
2.2.1. Resistance
2.2.1.1. Fire (R Value)
2.2.1.2. Thermal conductivity
2.2.1.3. Cell deterioration
2.2.1.4. Impact
2.2.1.5. Moisture
2.2.2. Capability
2.2.2.1. Attatchment
2.2.2.2. Asphalt
2.2.2.3. Roof componants
3. Wind Uplift
3.1. Zone 1: Field (F) – The interior of the roof bound by the edge and the corners
3.2. Zone 2: Edge (E) – Defined as 10% of the building width or 40% of the building height, whichever is less. In no case will perimeter zones be less than 7’ (2m)
3.3. Zone 3: Corner (C) – Part of the perimeter but not less than 7’x7’. The corner area is defined by the edge in both directions at the corners
4. FASTENING INSULATION
4.1. Can be loose laid in certain ballasted systems Fastened with screws and plates with a minimum 1” nail head Adhered with hot asphalt Adhered with foam adhesive
4.1.1. LOOSE LAID
4.1.1.1. Protected Membrane Assembly (PMA) require only type 4 extruded polystyrene insulation – XPS Ballast for PMA is typically minimum 1200lbs per square Ballasted EPDM typically also have loose laid insulation installed under the membrane Field, perimeter and corner calculations not applicable to these systems Increased insulation thickness for PMA systems or increased wind loads will require more ballast.
4.1.2. SCREWS AND PLATES
4.1.2.1. Minimum fastening requirement: Field – 8 per 4x8 sheet Perimeter – 12 per 4x8 sheet Corner – 15 per 4x8 sheet
4.1.2.2. Most roofing manufacturers require their screws and plates
4.1.3. MECHANICALLY FASTENING TO STEEL DECK
4.1.3.1. Fasteners must be installed on the high points of the deck
4.1.3.2. Fasteners must penetrate the deck by 3/4” minimum.
4.1.3.3. Cantilevering of insulation boards over flutes should be avoided if installing only one layer of insulation
4.1.4. ASPHALT ADHERED
4.1.4.1. When installing insulation with hot asphalt the insulation must not be more than 4’ in any direction (max 4’x4’) When adhering coverboard to heat sensitive insulation the cover board shall be mopped then laid onto the heat sensitive insulation. This is commonly referred to as “mop and flop”. The first layer of coverboard will then have all seams covered by joint tape made of either #15 organic felt, or fiberglass. The second layer will be installed by mopping the substrate then installing the cover board.
4.1.5. FOAM ADHESIVE
4.1.5.1. Ribbons should be 12” wide at point of installation
4.1.5.1.1. Maximum 12” spacing for the field Most assemblies require minimum 6” spacing
4.1.5.1.2. Most membrane manufacturers require the use of their own foam adhesive to be used.
4.1.5.2. Time before installing insulation varies by manufacturer Some foam adhesive installation require weights on the boards, check manufacturers instructions
5. Requirenments
5.1. RCABC requires a minimum 2” of heat insensitive insulation OVER heat sensitive insulation. Or historically, 2 layers of heat insensitive overlay board.
5.2. Nailing strips required on roofs 1/12 or greater Maximum insulation thickness of 2” for nailing
6. Cover board
6.1. Cover Boards are materials, formed into boards and placed on top of insulation to evenly disperse weight, and protect from mechanical damages as well as protect heat sensitive insulation from hot asphalt or torches.
6.1.1. Gypsum Board
6.1.1.1. Used to support insulation or membrane over steel deck flutes Can be used as a final overlay board to create a suitable substrate May cause blister formation of asphalt over glass-faced gypsum board. Manufacturers recommend priming prior to application.
6.1.2. Asphaltic core board
6.1.2.1. Asphaltic core sandwiched between glass fiber reinforcement. Designed for use with hot applied asphalt membranes and torch on systems.
7. Heat
7.1. Heat moves three ways. Conduction, Radiation, and Convection.
7.1.1. Conduction
7.1.1.1. This is the transfer of heat through physical contact, think of a stove top.
7.1.2. Radiation
7.1.2.1. Occurs independently of solids, gasses, and liquids, such as when the sunlight heats a roof or heat rises out from a building at night. Think of a Microwave.
7.1.3. Convection
7.1.3.1. This Occurs within gasses and liquids as a result of heat conduction within the gas or liquid and the movement of these substances. Think of an Oven.