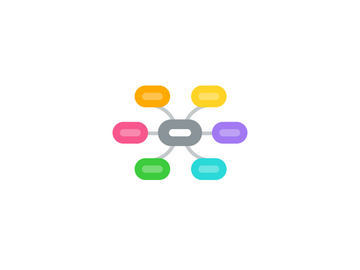
1. Wire Rope Classification
1.1. Number of strands
1.1.1. 6x7 - 6 strands with 7 wires in each strand;
1.1.2. 6x19 - 6 strands with 9-26 wires in each strand;
1.1.3. 6x37 - 6 strands with 27-49 wires in each strand
1.1.4. E.g. 6x19 Seal, Fibre Core OR 6x19 S FC
1.1.5. E.g. 33mm 6x25 S RLL OR Lang lay rope
1.2. Construction/stranding principle
1.2.1. Seal
1.2.2. Warrington
1.2.3. Filler
1.2.4. Filler Seale
1.3. Types of cores
1.3.1. Fibre Core (FC)
1.3.1.1. used for ski lifts
1.3.1.2. natural or synthetic
1.3.1.3. compress with wear; provide strands less support
1.3.2. Independent Wire Rope (IWRC)
1.3.2.1. good for counterweight rope
1.3.2.2. consists of a small wire rope used as a core for a larger wire rope
1.3.2.3. NOT used as a haul rope
1.3.3. Solid Core
1.3.3.1. a solid plastic rod, around which the strands are laid.
1.3.3.2. Heat is ised in th eprocess so that the straands imbed themselves in the plastic
1.3.3.3. compress LESS than FC
1.3.4. minimal stretch and diameter reduction
1.3.5. more difficult to splice; do not act as a lubricant reservoir
2. Ski lift application
2.1. Surface lifts 9platters and T-bars) haul ropes: 6x7
2.2. Chairlift haul ropes: 6x19
2.3. Detachable lift haul rope: 6x35
2.4. Counterweight ropes: 6x36, 6x41 (Warrington Seale)
3. Critical Properties
3.1. Size (Diametr)
3.1.1. Surface/small chairlifts: 7.5-32 mm
3.1.2. chairlifts/gondolas: 22-40 mm
3.1.3. large gondolas, tramways/funiculars: 42-55mm
4. Vocabulary
4.1. tensile strenth - растяжимость
4.2. amrasion - истирание
4.3. galvanized rope - оцинкованная, гальвализированная
4.4. wear - износ
5. Grade and Related Rope Properties
5.1. tensile strength (растяжимость)
5.1.1. flexibility provided by wires in a wire rope OR ability to withstand longitudinal stress.
5.1.1.1. Safety factor 4.5
5.2. fatigue resistance
5.2.1. the wire rope's ability to resist bending fatigue and vibration
5.2.2. usually concentrated at grip locations and at points along the splice
5.3. abrasion (истирание) resistance
5.3.1. rope's ability to resist both external and internal abrasion
5.3.2. strong rope core reduce the amount of internal a.
5.4. crushing strenght
5.4.1. important for counterwieght ropes
5.4.2. rope's ability to withstand forces that distort its cross-section and reduce its life
5.5. corrosion resistance
5.5.1. ability to resist corrosion
5.5.2. oxidation (окисление), rusting (ржавление)
5.6. Plow steel
5.6.1. the high tensile steel wire
5.6.2. grades
5.6.2.1. Improved Plow Steel (IPS)
5.6.2.2. Extra Improved Plow Steel (EIPS)
5.6.2.3. Double Extra Improved Plow Steel (EEIPS)
6. Processes
6.1. Prestressing
6.1.1. involves subjecting the rope to some degree of load or stress at the manufactuaring plant
6.1.2. reduces or eliminates construction stretch
6.1.2.1. C.s. - the stretch that results from the normal wearing-in process that happens once the rope has been put into service. This occurs as the Strands seat/compress in on the core
6.1.3. reduces a rope's lifespan
6.1.4. Optional part of manufacturing process
6.2. lubrication
6.2.1. it reduces internal friction
6.2.2. it can rpotect wires from corrosion
6.2.3. if no lubrication, bending fatigue increases
6.2.4. part of manufacturing process and field lubrication
6.3. Glavanizing (гальванизация)
6.3.1. used in Europe
6.3.2. protects steel wires from corrosion
6.3.3. needs smaller amounts of lubrication than bright ropes
6.3.4. Bright rope - non-galvanized
6.3.4.1. have brownish colour
6.3.5. Galvanized VS bright ropes
6.3.5.1. reduced maintenance
6.3.5.2. improved drive friction (need less lube)
6.3.5.3. improved appearance (limited rope discolouration or disc. of sheaves, carriers, towers in wet climates)
6.4. Compacted Ropes
6.4.1. Provide increased strength and longer rope life
6.5. Preforming
6.5.1. the wires and strands are lshaped intor their helical (спиралевидную) form
6.5.1.1. withoout this process, a broken wire can protrude (торчать) from the rope and unravel (расплетатться)
6.5.2. Done as part of manufacturing process
6.5.3. Standard for all ropes
7. Main wear factors
7.1. reduced rope diameter
7.2. broken wires
8. The direction and Type of Lay
8.1. Lay lenght
8.1.1. the distance a strand takes to make one full circle around the ropes axis
8.1.2. increased lay length (when rope wears out, it stretches)
8.1.3. variations in lay lenght
8.2. Lay directions
8.2.1. Regular Lay
8.2.1.1. wires VS strands=opposite direction
8.2.2. Lang lay
8.2.2.1. Same direction=wires in the strand=strands
8.2.2.2. longer exposed crown wires = spreads the load over a larger area
8.2.2.3. coefficient friction?
8.2.2.3.1. you want it high; overwise, it slips