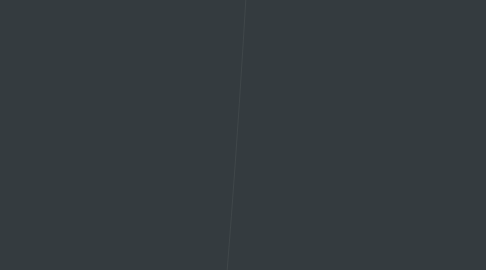
1. Camara termografica
1.1. es un tipo de cámara que crea una imagen con luz infrarroja. Esta tecnología también puede llamarse mirando adelante infrarrojos (FLIR), o de imágenes térmicas.
1.2. estos dispositivos detectan la luz invisible, infrarrojos, también conocido como calor.
1.3. Tipos
1.3.1. Cámaras termográficas refrigeradas y no refrigeradas.
1.3.2. Cámaras termográficas infrarrojas tipo móvil.
1.3.3. Cámaras termográficas infrarrojas de alta tensión.
1.3.4. Cámaras termográficas infrarrojas de baja tensión.
1.3.5. Cámaras termográficas infrarrojas para usos mecánicos.
1.3.6. Cámaras termográficas infrarrojas para edificios.
1.3.7. Cámaras termográficas infrarrojas para energía eólica
1.3.8. Cámaras termográficas infrarrojas energía solar.
2. Plantas Antiguas
2.1. Modernizacion
2.1.1. Crecimiento global de la empresa
2.1.1.1. Aumentar Productividad
2.1.1.2. Rebajar costes de productos fabricados
2.1.1.3. Flexiblidad en la fabricacion
2.1.1.4. Mejorar seguridad de la Planta
2.1.2. Cambios en la Planta
2.1.2.1. Paneles de control Modernos
2.1.2.2. Cambios en la caracteristicas del Proceso
2.1.2.3. Mejorar velocidad de trasmision y control de variables
2.1.3. Sustitucion y modificacion de los procesos industriales
2.1.4. Periodo determinado , planta actualmente funcionando
2.1.4.1. Realizar la transformacion en el minimo tiempo posible
2.1.4.2. Alteraciones en la fabriacion minimas
2.1.4.3. Gastar el minimo dinero posible
2.1.5. Proyecto de modernizacion
2.1.5.1. Objetivos referentes a la instrumentacion de la planta
2.1.5.1.1. Reducir numeros de proveedores y modelos
2.1.5.1.2. Sustitucion de instrumentos defasados
2.1.5.1.3. Incorporacion de sistemas de control avanzado
2.1.5.1.4. Mejora de la seguridad de operacion de la planta.
2.1.5.2. Restricciones
2.1.5.2.1. Normalizacion de los instrumentos
2.1.5.2.2. Estado actual de los instrumentos de la planta.
2.1.5.2.3. Cambio o modificacion del Cv de las valvulas de control
2.1.5.2.4. Incorporacion de analizadores en linea
2.1.5.2.5. La valoracion del paso del control clasico al control distribuido
2.2. Planificacion
2.2.1. Formas de realizarla
2.2.1.1. Por Nudos o uniones de datos o mas actividades
2.2.1.2. Por CPM o por centencias
2.2.2. Elementos de la Planificacion
2.2.2.1. Objetivos de la modernizacion.
2.2.2.1.1. limites de costo y de tiempo
2.2.2.1.2. asiganar recursos tecnicos
2.2.2.1.3. asignar recursos humanos y materiales necesarios
2.2.2.2. Equipo afectado por la modernizacion y el nuevo equipo necesario
2.2.2.3. Disponibilidad
2.2.2.3.1. Definir numero de personal , calificaciones y periodos de tiempo
2.2.2.4. Beneficios y recursos de modernizacion
2.2.2.4.1. Cursos de Preparacion al personal y disponer de equipos reales o simuladores para practicar.
2.2.2.5. Sistemas de Control
2.2.2.5.1. Fijar los instrumentos que deben sutituirse o modificarse
2.2.2.5.2. En la mayoria de los casos sale mas barato utilizar instrumentos nuevos que reparar los antiguos
2.2.3. Instrumentos de campo
2.2.3.1. Transmisores neumaticos de la planta
2.2.3.1.1. Sustituirlos por otros:
2.2.3.2. Consideraciones de la sustitucion de los transmisores neumaticos
2.2.3.2.1. Los transmisores electronicos convencionales en caso de averias se reparan en el taller de instrumentacion.
2.2.3.2.2. Los transmisores inteligentes presentan una mayor facilidad de mantenimiento y pueden calibrarse directamente en campo.
2.2.4. Valvulas de Control
2.2.4.1. Si se pasa a control electronico: sustituir los actuadores neumaticos originales montados en las valvulas de control por actuadores con posicionador electroneumatico
2.2.4.2. En el caso del control digital: se sustituira el servomotor por otro con actuador digital
2.2.4.3. Si la instalacion es muy antigua: sustituir enteramente la valvula de control
2.2.5. Sustitucion Instrumentos de Campo
2.2.5.1. Sustitucion de los instrumentos de panel por otros neumaticos, electronicos o digitales.
2.2.5.1.1. Controladores neumaticos de ultima generacion.
2.2.5.1.2. Instrumentos electronicos de panel
2.2.5.1.3. Instrumentos digitales
2.2.6. Modernizacion Total
2.2.6.1. Sustitusion masiva de toda la instrumentacion de la planta adoptando el control distribuido
2.2.6.2. Problemas de mala Instalacion
2.2.6.2.1. medidor de caudal magnetico instalado en posicion horizontal
2.2.6.2.2. medicion de nivel del tanque; dara mala lectura si el fluido varia su densidad
2.2.6.2.3. medicion de nivel en un tanque con espuma en su superficie y utilizando aparato de ultrasonido
3. Nuevas Plantas
3.1. Generalidades
3.1.1. Costes
3.1.1.1. el coste aproximado de los instrumentos y de su instalacion alcanza una cifra de 2-3 % del valor total de inversion si la planta tiene pocos instrumentos de medida
3.1.1.2. Si la planta esta bien automatizada tiene un 5-10 %
3.1.2. Ventajas
3.1.2.1. no exciste un limite de tiempo para llevrla a cabo la instalacion
3.1.2.2. La planta puede proyectarse en todas las fases de la ingenieria
3.1.2.2.1. peticion de ofertas
3.1.2.2.2. compra de material e instrumentos
3.1.2.2.3. intalacion y puesta en marcaha
3.1.3. Formacion del Personal
3.1.3.1. Cursos de formacion en control de procesos enfocados a operadores de proceso.
3.1.3.2. Uso de simuladores de la planta
3.1.3.3. Entrenamiento en fabricas asociadas
3.1.4. Fases del proyecto
3.1.4.1. la ingenieria
3.1.4.2. la isntalacion
3.1.4.3. la calibracion
3.1.4.4. la puesta en marcha
3.1.4.5. el mantenimiento
3.2. Ingenieria
3.2.1. Tamaño
3.2.1.1. si la planta es pequeña
3.2.1.1.1. se raliza en la propia oficina del usuario con personal eventual utilizable durante un tiempo determinado
3.2.1.2. si la planta es grande
3.2.1.2.1. es contratada a una firma exterior que destina el personal necesario y un tiempo suficiente para realizar el proyecto
3.2.2. Especificaciones
3.2.2.1. instrumentos de medicion
3.2.2.2. isntrumentos de control
3.2.2.3. valvulas
3.2.2.4. Listas de proveedores
3.2.2.4.1. Al menos 5 proveedores
3.2.2.4.2. instrumentos suministrados por el mismo fabricante
3.2.3. Diagramas de Flujo
3.2.3.1. permiten el examen critico del sistema do control del proceso y el estudio de todos los detalles
3.2.4. Pedido
3.2.4.1. instrumentos de campo
3.2.4.2. isntrumentos de panel
3.2.4.3. Analizadores
3.2.4.4. valvulas de control
3.2.4.5. elementos finales de control
3.2.4.6. paneles y consolas
3.2.4.7. intalacion y construccion
3.2.4.8. Puesta en marcha y mantenimiento posterior
3.2.5. Paneles
3.2.5.1. especificaciones
3.2.5.1.1. dimensiones
3.2.5.1.2. cortes a realizar en el panel
3.2.5.1.3. tipo de panel
3.2.5.1.4. Cableado interior entre todos los instrumentos
3.3. Instalacion
3.3.1. tipos de instalacion
3.3.1.1. la compañia seleccionada instala los instrumentos en el proceso
3.3.1.2. lugar de instalacion de los cables o tubos
3.3.1.2.1. galerias subterraneas
3.3.1.2.2. zanjas adecuadamente señaladas
3.4. Calibracion
3.4.1. la calibracion se raliza siempre que es posible con el instrumento ya instalado, y despues se comprueba cada lazo de control para detectar posibles problemas
3.4.2. Maletas de calibracion
3.4.2.1. neumaticas
3.4.2.1.1. pequeño componente de aire sin aceite , apto para alimentar dos o tres instruments
3.4.2.1.2. permite caibrar instrumentos neumaticos de campo o panel.
3.4.2.2. electronicas
3.4.2.2.1. Son suministrados por los fabricantes de los aparatos y destinadas a sus propios instrumentos
3.5. Puesta en marcha
3.5.1. Arranque
3.5.1.1. un primer arranque de la fabrica alimentando los tanques y tuberias con agua y trabajando durante un tiempo de 24 horas a una semana
3.5.2. Limpieza
3.5.2.1. se limpian tuberias de objetos como restos de varillas de soldar, trapos, madera, etc.
3.5.3. Ajuste de isntrumentos
3.5.3.1. fijacion de los valores de las acciones proporcional+integral+derivada de los instrumentos
3.5.3.2. en cuanto al control distribuido este seraliza llamando al lazo correspondiente tecleando el valor de cada accion.
3.5.3.3. Criterios de Ajustes
3.5.3.3.1. Lazo de control
3.6. Mantenimiento
3.6.1. Programas de mantenimiento
3.6.1.1. Mantenimiento de Stock minimo
3.6.1.2. Ordenes de trabajo
3.6.1.3. Trabajos correctivos
3.6.1.4. Trabajos Preventivos
3.6.2. Gestion del Mantenimiento
3.6.2.1. Fiabilidad
3.6.2.1.1. Probabilidad que un instrumento fucione sin averias en un tiempo
3.6.2.2. Mantenibilidad
3.6.2.2.1. Probabilidad que un fallo sea reparado antes de un tiempo desde que se detecto la falla.
3.6.2.3. Indice de fallo
3.6.2.3.1. Relacion entre el numero de fallos que se dan en un tiempo entre el numero de instrumentos que estaba funcionando correctamente antes del fallo.
3.6.2.4. Tiempo medio entre fallos
3.6.2.4.1. Numero total de horas trabajadas por los instrumentos entre el numero de averias que se han presentado en dicho tiempo
3.6.2.5. Disponibilidad
3.6.2.5.1. Probabilidad de que un instrumento o equipo este disponible dentro de un intervalo de tiempo determinado
3.6.3. Contratado
3.6.3.1. mantenimiento programado
3.6.3.2. reparaciones de envergaduras
3.6.3.3. obras nuevas
3.6.4. Propio
4. Mantenimiento Y Ruido
4.1. Fallos en Sistema
4.1.1. Confiabilidad
4.1.1.1. Probabildiad de que un dispositivo realice adecuadamente su funcion.
4.1.1.2. Analisis de informacion operatica para mantenimientos
4.1.1.3. RCM (mantenimiento centrado en la Confiabildiad)
4.1.1.3.1. Maneja mas eficiente las consecuencias de las falllas.
4.1.2. MTTF (Mean Time to Failure
4.1.2.1. Tiempo Promedio de recuperacion del sistema antes una falla
4.1.3. MTBF (Mean Time Between Failure
4.1.3.1. Indica el intervalo de tiempo mas probable entre su arranque y la aparicion de un falllo
4.1.3.2. Cuando el valor sea mayor, la confiabilidad sera mayor.
4.1.4. Mantenimiento
4.1.4.1. Elementos
4.1.4.1.1. Conjunto de personas que ofrecen y prestan servicio de conservacion de equipos
4.1.4.2. Tipos
4.1.4.2.1. Preventivo
4.1.4.2.2. Predictivo
4.1.4.2.3. Correctivo
4.1.4.2.4. Autonomo
4.1.4.2.5. TPM(mantenimiento productivo total)
4.1.5. Razon de fallo
4.1.5.1. informes de fallas
4.1.5.2. Medidas a tomar para mejorar
4.1.6. Modelos de Confiabilidad
4.1.6.1. Serie
4.1.6.1.1. el falllo de un elemento conlleva al fallo total del sistema
4.1.6.1.2. menos confiable
4.1.6.1.3. cada item depende del componente que lo antecede
4.1.6.2. Paralelo
4.1.6.2.1. El sistema funciona siempre que funcione al menos uno de sus componentes
4.1.6.2.2. falla cuando se presenta en todos sus elementos
4.2. Filosofia de Mantenimiento
4.2.1. Correctivo
4.2.1.1. Personal espera a que se ocurra la fallla
4.2.1.2. Una carga de trabajo irregular
4.2.1.3. Requrimiento simultaneo en diferentes lugares
4.2.1.4. Dificultades para medir el Stock
4.2.2. Preventivo
4.2.2.1. Planificar las operaciones teniendo en cuenta imperativos de producción.
4.2.2.2. Permite organizar y nivelar las cargas de trabajo con programas de visita, engrasado.
4.2.2.3. Mejora la confiabilidad y por lo tanto la disponibilidad de los equipos operando en tiempo oculto.
4.2.2.4. Optimizar el tiempo de intervención debido a una mejor preparación, por lo tanto dominar los costos de intervención y los riesgos de accidente.
4.2.3. Predictivo
4.2.3.1. Vigilancia de máquinas
4.2.3.2. Distinguir entre condición buena y mala, y si es mala indicar cuán mala es.
4.2.3.3. Proteccion de la maquina
4.2.3.4. Estima cuánto tiempo más podría funcionar la máquina sin riesgo de una falla catastrófica.
4.2.4. Proactivo
4.2.4.1. Eliminar los problemas de la máquina a través de un periodo de tiempo.
4.2.4.2. Reduce el tiempo de in-movilización y una capacidad de producción extendida.
4.2.4.3. Detecta y corrige el desgaste las causas que generan el desgaste y que conducen a la falla de la maquinaria.
4.2.4.4. Establece una técnica de detección temprana, monitoreando el cambio en la tendencia de los parámetros considerados como causa de falla.
4.2.5. Mejora continua
4.2.5.1. Aplica prácticas efectivas en cada área de la organización y trasciende a lo que se entrega a los clientes.
4.2.5.2. Es la esencia de la calidad y pretende reflejar lo que las empresas en su giro necesitan hacer si desean ser más competitivas y productivas a través del tiempo.
4.2.5.3. Mejoramiento incremental y mejoramiento marginal.
4.2.5.4. Insatisfacción continúa a lo que hacemos, pensar como podemos mejorar las tareas realizadas.
4.3. Instrumentos para Identificacion de fallas
4.3.1. Probador de tierra
4.3.1.1. Tipos
4.3.1.1.1. Tipo Varillla
4.3.1.1.2. Tipo gancho
4.3.1.2. Realiza medidas de resistencia de tierra pueden medir continuidad o enlace.
4.3.2. Medidor de resistencia de aislamiento
4.3.2.1. se encarga de detectar el desgaste o fatiga en el aislamiento
4.3.2.2. Megger
4.3.2.2.1. Mide resistencia de aislamiento,cable,bobinados,puede ser respecto a tierra o entre fases, con el megeer se puede hallar el índice de polarización
4.3.2.3. Tipos de medidores
4.3.2.3.1. Aislamiento clase B, temperatura máxima 130°C.
4.3.2.3.2. Aislamiento clase F, Temperatura máxima 155°C.
4.3.2.3.3. Aislamiento clase H, temperatura máxima 180°C.
4.3.3. Multitester
4.3.3.1. es muy utilizado en la industria y a nivel mundial
4.3.3.2. el más común consta de tres variables a medir: un amperímetro, voltímetro, óhmetro.
4.3.3.3. Tipos de Multitester:
4.3.3.3.1. Multitester digitales.
4.3.3.3.2. Multitester analógicos.
4.3.3.3.3. Multitester analógico y digitales.
4.3.3.3.4. Capacímetros.
4.3.3.3.5. Medidores de LCR.
4.3.3.3.6. Milióhmetros.
4.3.3.3.7. Watímetros o vatímetros.
4.4. Ruido
4.4.1. Tipos de ruido
4.4.1.1. Ruido estacionario: Ruido cuyo nivel de presión sonora permanece constante a lo largo del tiempo.
4.4.1.2. Ruido fluctuante: Ruido cuyo nivel de presión sonora varía en función del tiempo.
4.4.1.3. Ruido intermitente: Ruido que aparece solamente en determinados instantes.
4.4.1.4. Ruido impulsivo: Ruido cuyo nivel de presión sonora aumenta.
4.4.1.5. Ruido de Baja Frecuencia: Consideraremos valores de baja frecuencia todo ruido que se encuentre entre 20 y 125 Hz.
4.4.2. Fuentes de Ruido
4.4.2.1. El tráfico (terrestre y aéreo)
4.4.2.2. La construcción de edificios y obras públicas
4.4.2.3. Algunas instalaciones industriales.
4.4.3. Solucion
4.4.3.1. Aislamientos acústicos:
4.4.3.1.1. Barreras o pantallas.
4.4.3.1.2. Confinamiento de la fuente sonora.
4.4.3.1.3. Cabinas acústicas para el personal.
4.4.3.1.4. Aumento del aislamiento de paredes existentes
4.4.3.2. Tratamientos con absorbentes:
4.4.3.2.1. Revestimiento de paredes.
4.4.3.2.2. Techos con paneles suspendidos o colocación de cielorrasos fonoabsorbentes.
4.4.3.3. Proteger al personal expuesto, mediante el uso de protectores auditivos personales o mediante la utilización de cabinas.
4.4.4. Disturbios ocacionados por el ruido electromagnetico
4.4.4.1. Inestabilidad en dimmers y balastros
4.4.4.2. Disturbios en la iluminación tales como parpadeo
4.4.4.3. Radio recepción pobre
4.4.4.4. Inestabilidad en sistemas de control
4.4.4.5. Lazos Fluctuación en mediciones de flujo
4.4.4.6. Fallas en sistemas de cómputo
4.4.4.7. Molestas fallas de PLCs
4.4.5. Soluciones para el ruido electromagnetico
4.4.5.1. Puesta a tierra con baja impedancia
4.4.5.1.1. Esta es la técnica más común, particularmente en bajo voltaje.
4.4.5.1.2. La desventaja de este arreglo es que las corrientes de falla a tierra son normalmente altas pero los voltajes del sistema permanecen controlados bajo condiciones de falla.
4.4.5.1.3. Metodos para cefectuar una conexion a tierra.
4.4.5.2. Supresión de cargas inductivas
4.4.5.2.1. Los aparatos de carga inductivos (aparatos con una bobina) engendran voltajes transitorios cuando se energiza con un contacto de relevador.
4.4.5.3. Amplificadores diferenciales
4.4.5.3.1. El amplificador diferencial (AD) es un circuito pensado para amplificar la diferencia de dos señales.
4.4.5.3.2. Este circuito es la configuración óptima para las etapas de ganancia de los circuitos integrados lineales, en ese caso los dispositivos que lo constituyen son especialmente apareados durante el proceso de fabricación.
4.4.5.4. Amplificador de Instrumentación (AI)
4.4.5.4.1. El amplificador de instrumentación es uno de los amplificadores más útil, versátil y precisos en la actualidad.
4.4.5.4.2. Está formado por tres amplificadores operacionales y siete resistencias
4.4.5.5. Filtrado
4.4.5.5.1. Son circuitos caracterizados por una entrada y una salida de forma que en la salida solo aparecen parte de las componentes de frecuencia de la señal de entrada.
4.4.5.5.2. Tipos de Filtros
4.4.6. Compatibilidad electromagnetica
4.4.6.1. EMI (Interferencia Electromagnética)
4.4.6.1.1. La interferencia o perturbación electromagnética es todo fenómeno electromagnético susceptible a de crear problemas de funcionamiento en un dispositivo, aparato ó sistema ó bien afectar en forma desfavorable la materia viva o inerte.
4.4.6.2. EMC (Compatibilidad Electromagnética)
4.4.6.2.1. Aptitud de un aparato ó un sistema para funcionar en forma satisfactoria en su entorno electromagnético
4.4.6.2.2. Test EMC