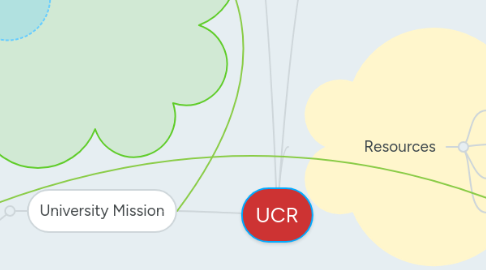
1. Occupational Safety
1.1. incident investigations
1.1.1. root cause anaylsis
1.1.2. lessons learned
1.2. communication
1.3. stretches
1.4. SOPs
1.4.1. work practices
1.5. evaluations
1.5.1. ergo
1.6. Permits
1.7. database
1.7.1. inventory of confined space
1.8. Hazard Assessments
1.8.1. by EH&S
1.8.2. by departments
1.9. audits
1.10. Equipment
1.10.1. relocate access
1.10.2. ventilation
1.10.3. retrofit (clean in place)
1.10.4. camera surveillance
1.10.5. purchasing better equipment
1.10.6. design changes
1.10.7. mechanical device
1.10.8. material handling
1.10.9. placement (better)
1.10.10. engineering controls & devices
2. COE
2.1. Goals
2.1.1. Serve/Assist
2.1.1.1. Provide services systemwide that individual locations cannot provide
2.1.1.2. Deliver the best software to UC in EH&S and Risk
2.1.1.3. Load/Remove online courses from LMS
2.1.1.4. Visit other campuses to implement our model. Expanding Cal/OSHA variance for low flow hoods.
2.1.1.5. Assist locations with using LMS as needed
2.1.1.6. Test online courses to load in LMS
2.1.1.7. Support regulatory compliance @ all UC campuses
2.1.1.8. Inform campuses of the need for engineering solutions to safety problems, and provide Occupational Safety _____
2.1.2. Solve/Invent
2.1.2.1. Improve safety in academic research laboratories
2.1.2.2. Make UC operated high-containment labs as safe as possible
2.1.2.3. Investigate a new intervention to reduce injuries
2.1.2.4. Develop a systemwide energy isolation program & mobile app used by facilities and researchers alike
2.1.3. Participate
2.1.3.1. Reach as many people (in need of support) as possible
2.1.3.2. Participate in STEW meetings
2.1.3.3. Develop local relationship between EH&S and Theater Arts department. Improve knowledge of Fall Protection.
2.1.4. Analyze
2.1.4.1. Provide data to researchers
2.1.4.2. Understand systemwide metric reports needs
2.2. Barriers
2.2.1. Staffing/Resources
2.2.1.1. Acquiring more funds to hire assistant
2.2.1.2. Constraints of UC data/ID management
2.2.2. Awareness
2.2.2.1. Visiting campuses that don't understand what a safety & risk center does
2.2.2.2. Not marketing / branding my COE
2.2.3. Expectations
2.2.3.1. I was asked to focus on providing services (not focus on research)
2.2.3.2. No UC standard
2.2.3.3. Challenges: 1) Direction, 2) Scheduling
2.2.4. Resistance
2.2.4.1. Resistance from EH&S Directors
2.2.4.2. Complains about lack of usefulness that COE provides
2.2.4.3. Politics getting in the way of making logical decisions
2.2.4.4. Difficult to engage
2.2.5. Delay
2.2.5.1. Being in a holding pattern (stalled efforts)
2.2.5.2. Not making enough progress - not enough time
2.2.6. Failures
2.2.6.1. Got kicked out of the Dean of Engineering's research lab because I asked him safety questions about his lab he couldn't answer
2.2.6.2. Copying another campus code & trying to extend it to all UC
2.2.6.3. RFP an contracting with a vendor
2.3. Successes
2.3.1. Leadership
2.3.1.1. Publishing an influential paper on lab safety
2.3.1.2. Initial "Chair" & start up of O.S. workgroup
2.3.2. Positive Feedback
2.3.2.1. Audit findings :)
2.3.2.2. A lot of interest from outside organizations
2.3.2.3. Positive feedback on COE service received by a location
2.3.3. Plan
2.3.3.1. Having a plan & updating it as we learned more
2.3.4. Communication
2.3.4.1. Communication to EH&S Leadership Council
2.3.4.2. Meeting and interacting with many people
2.3.4.3. Research on lab accidents and the ability to talk about it
2.3.4.4. Developing a lab ventilation assessment process. Support from UCOP. Opportunity to share.
2.3.4.5. BSL3 Lab Safety training for Directors
2.3.4.6. Meet a need that challenges ___ ____ do ____ by themselves.
2.3.5. Identify
2.3.5.1. 1st to research a new topic in safety
2.3.6. Solve
2.3.6.1. Visited & provided safety engineering support to all campuses & 3 hospitals
2.3.6.2. Loading/unloading testing of online courses in LMS
2.3.6.3. Providing assistance/guidance with LMS
2.3.6.4. Participated in RFPs and hiring committees
2.3.6.5. Identified severe high hazard research processes that were not understood by local EH&S & implemented controls
2.3.6.6. Moving into Agile
3. Culture
3.1. Service Excellence
3.2. Teamwork
3.3. Continuous Improvement
3.3.1. Gemba
3.4. Psychological Safety*
3.5. Shingo Model
3.6. Visual Management
3.7. Organizational Excellence
3.7.1. Tools
3.7.1.1. Lean
3.7.1.2. Six Sigma
3.7.2. Books
3.7.2.1. Toyota Way
3.7.2.2. Smarter Faster Better
3.7.2.3. Lean Thinking
4. University Mission
4.1. Values
4.1.1. Integrity
4.1.2. People
4.1.2.1. Black Belt
4.1.2.2. Faculty
4.1.2.3. Staff
4.1.2.4. Students
4.1.3. Process
4.1.4. Resources
4.1.4.1. Future State
4.1.5. Client
5. Resources
5.1. Gap
5.2. Activity Based Costing
5.3. Balanced Scorecard
5.4. BAS Client Satisfaction Survey
6. Service Level Agreement
6.1. BAS Departments
6.1.1. Auxiliary
6.1.2. R'Shared Services
6.1.3. Business Financial Services
6.1.4. Enterprise Risk Management
6.1.5. Human Resources
6.2. Organizational Units
6.2.1. VC BAS
6.2.2. VC P&B
6.2.3. VC RED
6.2.4. VC SA
6.2.5. VC UA