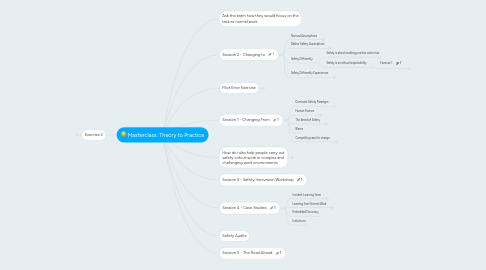
1. Safety Audits
2. Ask the team how they would focus on the task as normal work
3. How do rules help people carry out safety critical work in complex and challenging work environments
3.1. Golden Rules
3.1.1. These may have value if they are constructed in the right context and culture
4. Exercise 2
4.1. Safety Audits
4.1.1. Allow them to carry out the work and capture stories and discussion as qualitative data
4.1.1.1. Structure the audits around actual the business needs (risk and legislative)
4.1.1.2. Provide a mechanism that is accessible and usable for employees
4.1.2. Conduct a collaborative workshop
4.1.2.1. Analyse the findings and get the group to determine findings
4.1.3. Look to adapt work methods into a renewed method
4.1.4. Share learnings to other parts of the orgranisation
4.1.5. Should be able to identify with the variation between procedure and work as performed
4.2. Incident Investigation
4.2.1. The language around investigation needs to change
4.2.1.1. I have used the "8-Step" engineering risk method (it removes the ambiguity/subjective responses from the process)
4.2.2. Look at what gets investigated and gets to decide
4.2.3. Look at make up of the team
4.2.4. Need a facilitator process as opposed to lead invstigator
4.2.5. Broaden the scope of work reviewed relating to the event being examined
4.2.6. Broaden the application of the findings so they are not limited to just matching work processes.
4.3. Just Culture Process
4.3.1. Design a process for anonymous test of whether an act is appropriate or inappropriate
4.3.2. Allow the members to self regulate as to where the line is.
4.3.3. Could be used to recognise and reward people for initiatives
4.3.4. Anonymity is a key to this process
4.3.5. Process informs organisational decision making, rather than binding it.
4.4. Indicators and Performance Measures
4.4.1. Independent reviews
4.4.1.1. Focus on high consequence risk
4.4.2. Empowerment
4.4.2.1. End user confidence
4.4.3. Vibe
4.4.4. Solutions that have been implemented
4.4.5. Safe People
4.4.6. Quality of communication and language being used
5. Pilot Error Exercise
5.1. Group Solutions
6. Session 1 - Changing From
6.1. Dominant Safety Paradigm
6.1.1. People are the problem
6.1.1.1. Heinrich Accident Pyramid
6.1.1.1.1. Heinrich data has never been verified
6.1.1.1.2. Incidents filled out by supervisors
6.1.1.1.3. 88% attributed to human error is not evidence based
6.1.1.2. Systems would be fine if not for erratic and unreliable people
6.1.1.3. People do not do what they are supposed to do
6.1.2. Bureaucracy of Safety
6.1.2.1. Safety is about looking good
6.1.2.2. Doing things for bureaucratic reasons
6.1.2.3. Safety is about the papaerwork
6.1.2.4. Safety is about the system, not the people
6.1.3. Traditional Safety
6.1.3.1. The system is safe
6.1.3.2. Accidents happen because of unsafe acts/rare deviations from plan
6.1.3.3. Variability is a threat
6.1.3.4. People are a liability
6.1.3.5. Procedural compliance is mandatory
6.1.3.6. How can we change people?
6.1.4. What if there were no traffic rules
6.1.4.1. Self organisation comes in to play
6.1.4.2. Pedestrians will loose out
6.1.4.3. traffic will not flow as well
6.1.4.4. High level of anxiety initially
6.1.4.5. A collective social contract will emerge
6.1.4.6. Current State
6.1.4.6.1. Where does safety come from?
6.1.4.7. Hans Monderman -
6.1.4.7.1. Planted Flowers to change the characteristic of the road
6.1.4.7.2. Took away the rules
6.1.4.7.3. How can you try something not supported by evidence?
6.1.5. Safety Traditionally
6.1.5.1. People are a problem to control
6.1.5.2. Safety is about preventing negative outcomes
6.1.5.3. Safety is about a bureaucratic accountability up
6.1.5.4. People are the recipients of trouble
6.2. Human Factors
6.2.1. Alphonse Chapanis - B17
6.2.2. People understand the gap in the standards
6.3. The Brand of Safety
6.3.1. People finish the design
6.3.2. Apple
6.3.2.1. User friendly
6.3.2.2. Cool
6.3.2.3. Innovative
6.3.3. Safety
6.3.3.1. Accident
6.3.3.2. Procedures
6.3.3.3. Rules
6.3.3.4. harm
6.3.3.5. Risk
6.3.3.6. Fault
6.4. Blame
6.5. Compelling case for change
6.5.1. Whats frustrating you with the current ways
6.5.1.1. Safety is culturally driven
6.5.1.2. Bureacracy constraining innovation
6.5.1.3. Driven by numbers, facts and figured
6.5.1.4. Too beuracratic
6.5.1.5. Based on assumptions that are not valid
6.5.1.6. Ignores what it is to be human
6.5.1.7. Push philosophy rather than pull - Safety from the centre
6.5.1.8. Loss of time
6.5.1.9. Disengagement
6.5.1.10. Focus on failure
6.5.1.11. Disempowerment
6.5.1.12. Compliance for its own sake
6.5.1.13. Limiting ability to communicate organisation to organisation
6.5.1.14. 3 Streams
6.5.1.14.1. Rules
6.5.1.14.2. Negativity
6.5.1.14.3. Engagement
6.5.2. Herbert Heinrich - Accident Triangle
6.5.2.1. Not proactice
6.5.2.2. Dupont Accident Pyramid
7. Session 2 - Changing to
7.1. Revised Assumptions
7.1.1. 1 - Safety is the presence of a capability to create positive outcomes
7.1.2. 2 - People are the solution
7.1.2.1. Creates accountability at the workplace
7.1.2.2. Trust helps safety
7.1.2.3. People finish the design
7.1.3. 3 - Looking Inward to define safety direction
7.1.3.1. We do not need leaders that take charger, we need leaders that care
7.1.3.2. Leaders need to be of service to their people
7.2. Dekker Safety Assumptions
7.2.1. People are a solution to Harnass
7.2.2. 1 - Safety is the absence of negatives
7.2.3. 2 - People are a problem that needs to be controlled
7.2.4. 3 - Safety is a bureaucratic accountability
7.3. Safety Differently
7.3.1. Safety is about enabling positive outcomes
7.3.2. Safety is an ethical responsibility
7.3.2.1. Exercise 1
7.3.2.1.1. What do we need to manage safety differently
7.4. Safety Differently Experiences
7.4.1. Seeking to change the language of safety
7.4.2. Safety has plateaued and seek to do things differently
7.4.3. Looking for ways to be solution focused within risk framework
8. Session 3 - Safety Innovation Workshop
9. Session 4 - Case Studies
9.1. Incident Learning Team
9.1.1. Collaborative Inquiry
9.1.2. Apache Eyes
9.1.3. Start from the beginning and work towards the end
9.1.4. Allow soaking time
9.1.5. Invite ideas for how things can be improved
9.2. Learning from Normal Work
9.2.1. Collective Improvements
9.2.1.1. When Work is Difficult
9.2.1.1.1. What works well
9.2.1.1.2. Speaking up
9.2.1.1.3. Solutions
9.2.1.2. Collaborative Analysis
9.2.2. Appreciative Investigations
9.2.2.1. Site Improvement Teams