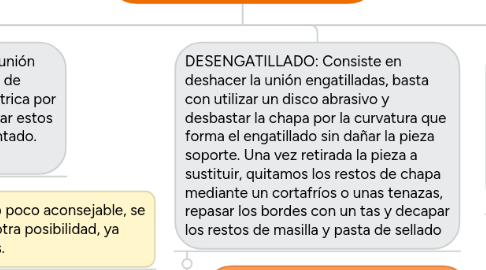
1. CORTADO: Se realiza con mucha frecuencia en el taller de carrocería, el primer paso antes de realizar la operacion es trazar una linea de referencia.
1.1. Cizallado: operacion de cortar chapa mediante un procedimiento basado en el desplazamiento de dos cuchillas que pivotan en un punto rozando una con otra
1.1.1. Accionadas mecanicas o manualmente
1.2. Cizalla accionada mecánicamente: la mas utilizada en el taller, denominada cizalla universal. Se acciona a través de una palanca manipulada por el operario, la chapa a cortar se coloca entre las dos cuchillas coincidiendo la linea de corte con las cuchillas. Para cortar grandes láminas pueden ser hidráulicas o eléctricas. INCONVENIENTE: pueden producir deformaciones.
1.3. Cizalla accionada manualmente: para realizar cortes en chapas ensambladas sobre el propio vehículo o en chapas de pequeñas dimensiones. También se le denominan tijeras de carrozero. Pudiendo ser:
1.3.1. Para cortar en linea recta, a izquierda o a derecha
1.3.2. Para cortar en círculo, a izquierda o derecha
1.4. Cizalladora manual neumática: accionada de forma neumática por un pulsador que manipula el operario, facilita el trabajo disminuyendo los esfuerzos físicos.
1.4.1. Otra herramienta que funciona de manera similar es la Roedora, que permite el cortado de chapa hasta 1,5 mm de espesor. puede realizar cortes rectos o circulares
1.5. PRECAUCIONES EN EL PROCESO DE CIZALLADO:
1.5.1. Realizar siempre el trazado de la línea de corte
1.5.2. Utilizar la cizalla adecuada
1.5.3. Coger la cizalla de forma adecuada
1.5.4. Utilizar guantes
1.5.5. Respetar las instrucciones de uso
2. DESPUNTADO: El método de unión más utilizado en la fabricacion de carrocería es la soldadura eléctrica por punto, a la operación de separar estos puntos se le denomina despuntado. Pudiendo ser:
2.1. Cincelado: Procedimiento poco aconsejable, se utilizará cuando no haya otra posibilidad, ya que suele dañar las piezas.
2.2. Fresado: Utilización de una fresa circular compuesta por un cabezal giratorio provisto de dientes como la hoja de sierra. Incorpora un dispositivo para regular la profundidad del fresado y así no dañar las piezas. Antes de comenzar a fresar es conveniente marcar con un granete el centro del punto a fresar
2.3. Taladrado: Procedimiento similar al del fresado, sólo que se taladra unicamente el punto de soldadura. Se realiza con una broca de acero rápido con un ángulo de 140º en la punta para realizar un taladrado casi plano y no dañar la pieza. Actialmente se utiliza la despuntadora, que incorpora un dispositivo para regular la profundidad del taladrado en funcion de la pieza a sustituir.
2.4. PROCESO PARA REALIZAR UN DESPUNTADO CON LA DESPUNTADORA
2.4.1. 1. Descrubrir la línea de puntos de la soldadura
2.4.2. 2. Decapar la zona con una radial con disco de alambre
2.4.3. 3. Marcar el centro del punto de soldadura
2.4.4. 4. Regular la profundidad del corte
2.5. PRECAUCIONES DEL PROCESO DE DESPUNTADO
2.5.1. Utilizar guantes y gafas de proteccion
2.5.2. Respetar las instrucciones de seguridad en el uso de las herramientas
3. DESENGATILLADO: Consiste en deshacer la unión engatilladas, basta con utilizar un disco abrasivo y desbastar la chapa por la curvatura que forma el engatillado sin dañar la pieza soporte. Una vez retirada la pieza a sustituir, quitamos los restos de chapa mediante un cortafríos o unas tenazas, repasar los bordes con un tas y decapar los restos de masilla y pasta de sellado
3.1. PRECAUCIONES DEL PROCESO DE DESENGATILLADO
3.1.1. Utilizar guantes y gafas de protección
3.1.2. Respetar las instrucciones de seguridad en el uso de las herramientas
4. CINCELADO: Objetivo, desprender o separar el material utilizando el cortafríos, consta de cabeza, cuerpo y filo.
4.1. Cabeza: es la parte que se golpea
4.2. Cuerpo: parte por donde se agarra el cincel
4.3. Filo: encargado de cortar
4.4. Para cortar con el cincel se puede utilizar un martillo manual o neumático
4.5. PRECAUCIONES DEL PROCESO DE CINCELADO
4.5.1. Realizar siempre el trazado de la línea de corte
4.5.2. Utilizar guantes
4.5.3. Utilizar gafas de proteccion
4.5.4. Respetar instrucciones de seguridad
4.5.5. Utilizar auriculares protectores si se emplea el martillo neumático
4.5.6. Observar siempre el filo del cincel y nunca la cabeza
5. ASERRADO: Procedimiento más utilizado en la reparación de carroceria, debido a su facil manejo, versatilidad, escaso calor producido por la friccion y que deja los bordes sin deformaciones. Se realiza mediante una hoja de sierra con dentado de diferentes formas geométricas.
5.1. En funcion del grosor y dureza de la pieza dependerá el tipo de hoja que escojamos
5.2. El aserrado puede ser con sierra manual, sierra neumática o sierra eléctrica
5.3. Para realizar cortes en línea recta, existe otro tipo de sierras circulares, neumáticas o eléctricas que sustituyen la hora de sierra por un disco dentado
5.4. PRECAUCIONES DEL PROCESO DE ASERRADO
5.4.1. Realizar el trazado de la línea de corte
5.4.2. Utilizar guantes, gafas de proteccion y casco
5.4.3. Respetar las instrucciones de seguridad en el uso de las herramientas
6. SEPARACION DE SOLDADURA CONTINUA: Consiste en emplear un disco abrasivo mediante una radial neumática o eléctrica. El corte del cordón se ha de realizar sin dañar la pieza soporte, a veces es díficil de conseguir.
6.1. Actualmente se ha diseñado otra herramienta denomidad Láser Cutter LC 04 para separar estas uniones y las realizadas por cordón continuo con el Láser, como:
6.1.1. En el techo
6.1.2. Huecos de las puertas
6.1.3. Marco parabrisas
6.1.4. etc.
6.2. PROCESO DE UTILIZACION DE LA DESPUNTADORA
6.2.1. 1. Comprobar el espesor de la pieza que se va a eliminar
6.2.2. 2. Seleccionar el soporte distanciador para ese espesor
6.2.3. 3. Seleccionar la muela de corte correcta
6.2.4. 4. Realizar el montaje de estos elementos
6.2.5. 5. Ajustar la pantalla protectora
6.2.6. 6. Aplicar el aceite de corte sobre la chapa a debastar
6.2.7. 7. Proceder a la separación de la unión
6.3. PRECAUCIONES DEL PROCESO DE SEPARACIÓN DE SOLDADURA CONTINUA
6.3.1. Utilizar guantes, gafas de proteccion y protector auditivo
6.3.2. Respetar las instrucciones de seguridad en el uso de herramientas
7. EXTRACCION DE REMACHES ESTAMPADOS: Sistema de unión fría, se utiliza solo en el proceso de fabricación de carrocería, en las reparaciones hay que proceder a la extraccion de estos remaches y sustituirlo por remaches ciegos de calidad en función de las piezas a unir
7.1. MATERIAL A UTILIZAR PARA LA EXTRACCION
7.1.1. 1. Fuente de alimentacion y control
7.1.2. 2. Pinzas de soldar vástago extractor. Funciona bajo atmósfera controlada de argón
7.1.3. 3. Extractor de remache estampado que a su vez puede servir de remachadora
7.1.4. 4. Pinzas de masa
7.2. PROCESO DE ELIMINACION DE REMACHES ESTAMPADOS
7.2.1. 1. Verificar que están todas las conexiones del cableado
7.2.2. 2. Regular los distintos parámetros de la máquina
7.2.3. 3. Conectar las dos pinzas de masa para que los vástagos se suelden siempre entre las dos pinzas
7.2.4. 4. Eliminar la pintura y dejar la cabeza de los remaches brillantes
7.2.5. 5. Introducir el vástago extractor en la pinza
7.2.6. 6. Soldar el vástago en la cabeza del remache
7.2.7. 7. El vástago debe quedar perpendicular a la cabeza del remache
7.2.8. 8. Introduccir el vástago en el extractor, mantenerlo perpendicularmente y presionar el gatillo para extraerlo, saldrá unido al vástago
7.2.9. 9. Una vez extraídos todos los remaches proceder a reponer la pieza nueva utilizando remaches ciegos
8. CORTE POR PLASMA: Constituido por un flujo obtenido mediante la casi completa ionización de un gas, neutro que se encuentra a temperaturas muy elevadas, pudiendo llegar hasta los 3000ºC. Contiene proporciones casi iguales de electrones y de iones positivos y conduce de forma excelente la electricidad.
8.1. Produccion de un plasma
8.1.1. Mediante fuertes decargas eléctricas, calentado los elementos que rodean al gas neutro
8.1.2. Calentado simplemente el gas a una temperatura aproximada a los 7000ºC
8.1.3. Aprovechando la ionización producida por rayos muy energéticos
8.2. En el sector del automóvil se utiliza el de descargas eléctricas y calentamiento de los elementos, que consiste en hacer pasar un arco eléctrico que crea una corriente intensa de aire caliente hasta 30.000ºC que funde y quita el metal sobre un área muy reducida
8.3. Elementos de un equipo de plasma
8.3.1. Transformador eléctrico con sistema de refrigeración
8.3.2. Circuito neumático cuya presion se puede regular a través de un manómetro irregulador
8.3.3. Una antorcha y correspondientes mangueras eléctricas y neúmaticas:
8.3.3.1. Cabezal
8.3.3.2. Electrodo
8.3.3.3. Difusor
8.3.3.4. Tobera
8.3.3.5. Portatobera
8.3.3.6. Interruptor de funcionamiento
8.3.4. Elementos de protección (fusibles) para prevenir sobrecargas y cortocircuitos
8.3.4.1. Proteccion contra el sobrecalentamiento en el transformador
8.3.4.2. Proteccion contra el sobrecalentamiento por falta de presión en el circuito neumático
8.3.4.3. Proteccion contra tensiones peligrosas en el cuerpo de la antorcha
8.4. Funcionamiento de la máquina:
8.4.1. el transformador eléctrico produce la tensión necesaria para establecer un arco eléctrico entre electrodo y la tobera que están separados por el difusor, por donde se hace pasar el aire comprimido produciendose una temperatura muy elevada que provoca que el aire se ionice y se transforme en un aglomerado de iones positivos, átomos neutros y electrones libres convirtiendose en conductor eléctrico
8.5. Proceso para el corte por plasma
8.5.1. 1. Reglaje del tiempo de prefujo
8.5.2. 2. Reglaje del tiempo de posflujo
8.6. SEGURIDAD DURANTE EL PROCESO DEL CORTE POR PLASMA
8.6.1. Utilizar gafas y guantes
8.6.2. Comprobar que la toma de tierra está conectada
8.6.3. No utilizar lentes de contacto
8.6.4. Realizarlo en zonas ventiladas
8.6.5. Respetar las instrucciones de seguridad en el uso de las herramientas
9. SUSTITUCIONES PARCIALES: Aquellas operaciones en las que no se cambian las piezas completas, sólo se pueden efectuar si el fabricante del vehículo lo contempla en sus manuales de reparación, donde se detalla los elementos y procesos que hay que realizar.
9.1. Interpretación de las líneas de corte
9.1.1. La calidad de la reparación va depender en gran medida de la correcta ejecucción del trabajado, respetando líneas de corte propuestas por el fabricante del vehículo
9.1.1.1. Algunos fabricante de vehículos tienen diseñadas
9.1.2. Algunos fabricantes de vehículos tienen diseñadas unas plantillas para posicionar la línea de corte en la carrocería
9.2. Proceso operativo genérico de las susticiones parciales
9.2.1. 1. Analizar las deformaciones que afectan a la zona a reparar y decidir si la sustitución será completa o parcial
9.2.2. 2. Comprobar el manual del fabricante
9.2.3. 3. Comprobar el despiece del recambio para saber si existe la pieza que desea cambiar o hay que adquirir la pieza completa
9.2.4. 4. Detener el proceso del fabricante
9.2.5. 5. Desmontar las piezas anexas
9.2.6. 6. Preparar los medios de proteccion personal
9.2.7. 7. Proteger las zonas cercanas a la reparación
9.2.8. 8. Decapar las zonas afectadas de las piezas, utilizando un disco de fribra de nylon o una lijadora de anclaje
9.2.9. 9. Ver y analizar donde se tienen que realizar las líneas de corte y marcarlas
9.2.10. 10. Realizar el corte de la seccion de la pieza por la linea trazada y despuntar los puntos de soldadura
9.2.11. 11. Extraer totalemente la seccion de pieza a cambiar
9.2.12. 12. Cortar la pieza de recambio un poco mas larga que la seccion montada, para que quede solapada
9.2.13. 13. Extraer la pieza de recambio y realizar su corte, acoplar nuevamente la pieza preparada y verficiar su perfecto anclaje
9.2.14. 14. Preparar la pieza en función del sistema de soldadura que se deba realizar en función del sistema que establezca el fabricante
9.2.15. 15. Acoplar la pieza sujetandolo con los útiles apropiados, ajustar, puntear y soldar, pulir los puntos de soldadura y aplicar los productos de proteccion