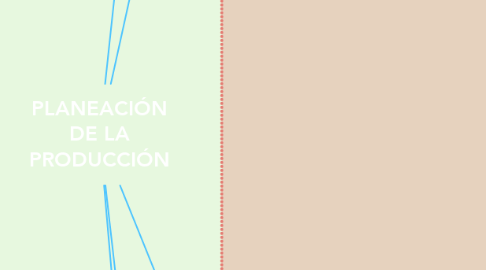
1. PLANEACIÓN DE REQUERIMIENTO DE MATERIALES
1.1. GESTIÓN DE STOCKS
1.2. CONTROL
1.2.1. CANTIDAD A PEDIR O FABRICAR
1.2.2. PUNTO DE PEDIDO
1.2.3. EL STOK DE SEGURIDAD O PROTECCIÓN
1.2.4. PLAZO DE APROVISIONAMIENTO
1.3. NO CONTROLABLES
1.3.1. DEMANDAS
1.3.2. NECESIDADES DE SALIDA DE ALMANCEN
1.3.3. FORMAS DE FINANCIACIÓN
1.3.4. CADUCIDAD DE LOS ARTÍCULOS
1.3.5. ESPACIO DEL ALMACÉN
1.4. MODELO WILSON
1.4.1. DETERMIA EL TAMAÑO DE LOTE A COMPRAR O FABRICAR
1.4.1.1. Q: CANTIDAD ECONÓMICA A PEDIR
1.4.1.2. T: PERIODO TOTAL AL QUE REFERIMOS LA GESTIÓN
1.4.1.3. N: NÚMERO DE PEDIDOS DURANTE T.
1.4.1.4. C: CONSUMO EN UNIDAD DE TIEMPO T.
1.4.1.5. S: COSTO DE PEDIDO POR PEDIDO
1.4.1.6. I: COSTO DE MANTENIMIENTO POR UNIDAD DE ARTÍCULO EN UNIDAD DE TIEMPO
1.5. TIEMPO DE TRABAJO
2. PLANIFICACIÓN PRODUCCIÓN POR UNIDAD
2.1. DISEÑA PARA PRODUCIR
2.2. MAQUINARIA, DISTRIBUCIÓN
2.2.1. BASADO EN UN SOLO PRODUCTO
2.3. ALTOS NIVELES DE PRODUCCIÓN
2.4. OPERACIONES EN LINEA
2.5. VENTAJAS
2.5.1. Altos niveles de eficiencia
2.5.2. No es necesaria tanta destreza
2.6. DESVENTAJAS
2.6.1. Difícil adaptación para fabricar otros productos
2.6.2. Exige cuidado para mantener balanceada la linea de producción
3. PLANIFICACIÓN PRODUCCIÓN INTERMITENTE
3.1. POR TALLERES
3.2. PRODUCCIÓN POR LOTES A INTERVALOS INTERMITENTES
3.3. MAQUINAS SIMILARES
3.4. VENTAJAS
3.4.1. Trabajo con variedad de Productos
3.5. DESVENTAJAS
3.5.1. Bajo Nivel de eficiencia
3.5.2. Gran trabajo de planificación y control
4. PLANIFICACIÓN GLOBAL
4.1. Planificación a Nivel de Fábrica
4.1.1. Obtención de los productos que la empresa desea producir
4.2. Planificación de Procesos
4.2.1. Distintas operaciones que configuran cada uno de los procesos
4.3. Planificación de Operaciones
4.3.1. Se estudia cada puesto de trabajo y las operaciones establecidas en la fase anterior